由于電子產(chǎn)品的小型化、高性能化、多功能化和信號傳輸高頻(速)化的迅速發(fā)展,推動了PCB必須快速地從傳統(tǒng)的PCB工業(yè)走向以高密度化、精細化為特點的高精密pcb產(chǎn)品。IC封裝基板是具有更高密度化的pcb電路板。IC封裝基板的首要問題是與所要封裝元(組)件的CTE(熱膨脹系數(shù))匹配兼容問題,其次才是高密度化問題。從本質(zhì)上來說,PCB是為元組件提供互連和機械物理支撐的高精密pcb。在今天的電子封裝市場上,除了陶瓷基板封裝外,還包括有機基板(FR)的封裝、晶圓級封裝(WLP,Wafer Level Package)、直接芯片安裝(DDA,Direct Die Attach)。很顯然,常規(guī)的PCB是不具備這些高級封裝(低CTE場合)能力的,因此,PCB工業(yè)必須發(fā)展能夠進行這些高級封裝基板材料的技術(shù)和產(chǎn)品。
陶瓷材料作為新型封裝材料的使用,具有優(yōu)良的機械性能,在電熱性能上面的表現(xiàn)更為耀眼。因為陶瓷電路板具有高散熱、高絕緣、低膨脹系數(shù)、耐腐蝕等優(yōu)點,被廣泛應用在航空航天、汽車電子、智慧照明、生物醫(yī)療、5G互聯(lián)等等。不同的陶瓷材料在某一性能方面的表現(xiàn)也尤為突出。比如氮化硅/碳化硅的耐磨、耐沖擊性能;氮化鋁材料的高性價使其廣泛用于VCSEL封裝熱沉;金剛石的導熱率更是能夠達到1000~2000W/m.k。那么這些陶瓷材料是如何被制作成PCB電路板的呢?
陶瓷電路板的制作過程是一整套復雜的加工工藝。首先需要做的就是將陶瓷粉體加工成特定形狀尺寸的載體基板。以氮化鋁陶瓷基板為例,選用高純度且為微粉的氮化鋁粉末,一般而言氧質(zhì)量含量在1.2%以下,碳質(zhì)量含量為0.04%以下,F(xiàn)e含量為30ppm以下,Si含量為60ppm以下,最大粒徑控制在20μm以下的氮化鋁粉末。利用混合裝置(球磨機、棒磨機或砂磨機等)將煅燒助劑(大多使用稀土金屬化合物、堿土金屬化合物、過渡金屬化合物等。例如可選用氧化釔或氧化鋁等)與合格的氮化鋁粉末混合,在混合后得到的原料粉中添加粘合劑后,通過片材成型(流延成型,注塑成型等)工藝得到成型體,進一步將其脫脂,再將脫脂后的成型片材進行煅燒得到氮化鋁基板的煅燒體。
拿到陶瓷基板后,要想實現(xiàn)陶瓷基板上下面電路的導通,需要在基板上打孔。因為陶瓷材料高硬度高脆性、容易碎裂,傳統(tǒng)的機械鉆銑機不能滿足微加工要求,激光打孔則不受影響,是最適合陶瓷打孔加工的設(shè)備。激光打孔是現(xiàn)代制造領(lǐng)域的關(guān)鍵技術(shù)之一,不同于手動鉆孔加工、電火花穿孔加工、電子束打孔加工,激光打孔是一個高精細,高效率,高質(zhì)量的打孔設(shè)備,它能做到一些常規(guī)方法無法實現(xiàn)的工藝。斯利通采用脈沖激光器和光纖激光器,激光束通過光學系統(tǒng)聚焦在激光軸垂直放置的的工作臺面上,發(fā)出高能量密度(一般為10*5-10*9w/cm2)的激光束使材料熔化、氣化,一股與光速同軸氣流由激光切割頭噴出,將熔化的材料由切口的底部吹出而逐步形成通孔。由于電子器件和半導體元器件具有尺寸小、密度高等特點,故對激光打孔的精度和速度有較高要求,根據(jù)元器件應用的不同,微孔直徑范圍為0.05mm-0.2mm。陶瓷精密加工的激光器,一般激光焦斑的直徑小于0.05mm。根據(jù)陶瓷板材厚度尺寸不同,對于直徑小于0.15mm的通孔,一般可通過控制離焦量來實現(xiàn)不同孔徑的通孔打孔。
打孔完成后就是對陶瓷基板電路制作的過程。目前市場上能夠批量生產(chǎn)的覆銅工藝主要有LTCC(低溫共燒陶瓷)、HTCC(高溫共燒陶瓷)、DBC(直接覆銅工藝)、AMB(活性釬焊工藝)、DPC(直接鍍銅工藝)。相比于其他覆銅工藝,DPC采用半導體微加工技術(shù),能夠使金屬化線路更加精細,因此非常適合對精準度要求較高的微電子器件封裝。首先需要用磁控濺射技術(shù)在陶瓷基板表面沉積一層金屬層(Ti/Cu)。磁控濺射是物理氣相沉積(Physical Vapor Deposition,PVD)的一種,過程中使用磁鐵將電子捕獲在帶負電的靶材上,這樣它們就不會自由地轟擊基材,防止要鍍膜的物體過熱或損壞,具有更快的薄膜沉積速率。磁控濺射系統(tǒng)通常配置為直列式,基板在某種類型的傳送帶上通過目標材料行進從而得到沉積。對于較小的應用通常設(shè)置為圓形。常規(guī)使用這幾種方法來誘導高能狀態(tài),包括直流 (DC)、交流 (AC) 和射頻 (RF) 磁控濺射源。與更傳統(tǒng)加熱溫度的熱蒸發(fā)相比,濺射發(fā)生在等離子體的第四自然狀態(tài)環(huán)境中,具有更高的溫度和動能,可以在原子水平上進行更純凈和更精確的薄膜沉積。
由于電路載板在使用中需要過受一定的電壓和電流,磁控濺射的銅層厚度并不能達到要求,因此需要在后面的工序中將銅層增厚。首先根據(jù)客戶的設(shè)計圖紙,通過圖形轉(zhuǎn)移工藝將需要的圖形制作出來。在高密度電路制造工藝中,圖形轉(zhuǎn)移是關(guān)鍵控制點,也是技術(shù)難點,其質(zhì)量的優(yōu)劣直接影響電路的合格率,生產(chǎn)過程中若控制失靈,極容易滲鍍、顯影不良或抗蝕干膜剝離等質(zhì)量問題。所以在制作過程中,必須要達到以下幾點:1.干膜盡可能平整且厚度均勻。要求干膜應具有很好的柔韌性、良好的塑性、流動性與粘結(jié)性以確保達到無間隙貼膜。2.曝光要適度。這樣才能達到線條清晰平直,保證圖形電鍍的合格率及其基板的電性能和其它工藝要求。3.顯影要充分。顯影是與下道工序直接相連的重要工序,其質(zhì)量的好與壞是整個圖形轉(zhuǎn)移成功與否的重要標志。4.車間潔凈度及溫濕度控制。由于線路板是較為精密的元器件,而PCB無塵車間制造中難免會出現(xiàn)四處飄散的灰塵,因此需要打造潔凈度標準較高的環(huán)境,以確保不會因為這些灰塵而產(chǎn)生開路、短路、阻焊雜物等問題。
接下來的步驟就是電鍍環(huán)節(jié)。圖形制作完成后,需要通過電流電鍍將銅厚加工到客戶指定厚度,電鍍原理是鍍液中的金屬離子在外電場的作用下,經(jīng)電極反應還原成金屬原子,并在陰極上進行金屬沉積的過程。因此,這是一個包括液相傳質(zhì)、電化學反應和電結(jié)晶等步驟的金屬電沉積過程。斯利通采用垂直連續(xù)電鍍線,通過改良的電鍍添加劑,在深鍍能力上實現(xiàn)10:1的厚徑比,填孔率、板面均勻性、銅面平整性能均可以達到品質(zhì)要求。電鍍完成后通過藥水將線路圖形刻蝕出來。不同的藥水刻蝕因子、側(cè)蝕量也不同,斯利通擁有改良的藥水配方,蝕刻線路的精度可以控制在10um以內(nèi),滿足電子芯片封裝的高精度要求。電路載板完成還需要邦定金線或者貼片,根據(jù)不同的要求需要在銅面上進行沉銀或者沉金。銀面公平已簡單快速,表面平整成本低,即使暴露在熱、濕的環(huán)境中,銀面仍然能夠保持良好的可焊性,適合無鉛焊接、SMT,以及非常精細的線路。沉金工藝的優(yōu)點是色澤穩(wěn)定,光亮度很好,鍍層平整可焊性好,并且耐磨,邦定金線的強度很高。
最后交給客戶手上還需要分板和切割,將不需要的工作邊去除掉。外型加工主要有激光和水刀切割兩種工藝。激光切割的原理和激光打孔類似,由于激光光斑小、能量密度高、切割速度快,能夠獲得較好的切割質(zhì)量,這里就不贅述。水刀切割的原理是用高壓泵把密封的水加壓,通過高級硬質(zhì)合金、藍寶石、金剛石等做成的噴嘴極細的噴頭噴出切割材料。水刀切割是一種冷態(tài)切割,切割時不產(chǎn)生熱效應,不會改變材料的物理化學性質(zhì),切割面整齊平滑,不會再切割過程中使被切割物體有任何損傷,因此現(xiàn)在在工業(yè)切割技術(shù)方面得到越來越廣泛的應用。水刀切割的加工精度可控制在0.1mm~0.25mm之間,當然這與機器精度、切割工件大小及厚度也有一定的關(guān)系。
做好的電路板經(jīng)過專業(yè)設(shè)備和人員檢測后,再經(jīng)過精美的包裝,最后就可以放心的交給客戶使用了。斯利通秉持“用心服務客戶,創(chuàng)造放心品牌”的價值理念,在陶瓷PCB領(lǐng)域不斷創(chuàng)新突破,為客戶創(chuàng)造價值。
審核編輯:湯梓紅
-
pcb
+關(guān)注
關(guān)注
4369文章
23496瀏覽量
409955 -
電路板
+關(guān)注
關(guān)注
140文章
5138瀏覽量
102745 -
陶瓷基板
+關(guān)注
關(guān)注
5文章
246瀏覽量
11851
發(fā)布評論請先 登錄
微電機軸心的研磨生產(chǎn)工藝及調(diào)試技術(shù)
貼片電容生產(chǎn)工藝流程有哪些?
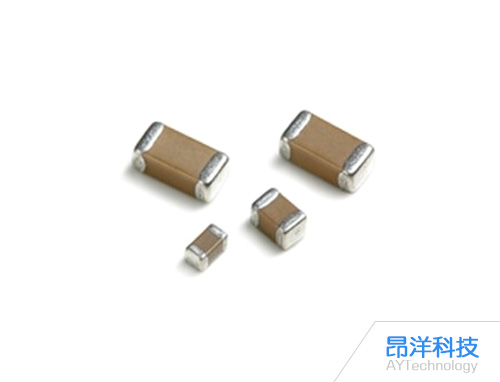
電子產(chǎn)品生產(chǎn)中的電路板布線設(shè)計
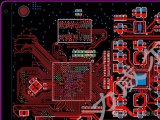
一文帶你全面了解陶瓷電路板厚膜工藝
焊接工藝如何左右PCB電路板的命運
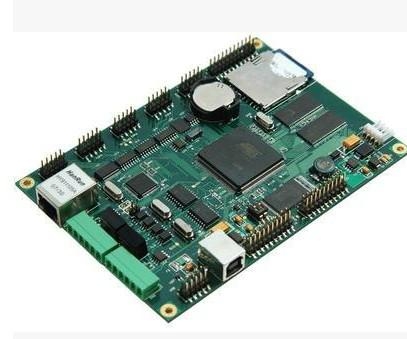
aoc跳線的生產(chǎn)工藝
【「大話芯片制造」閱讀體驗】+ 芯片制造過程和生產(chǎn)工藝
陶瓷電路板在制冷行業(yè)的應用
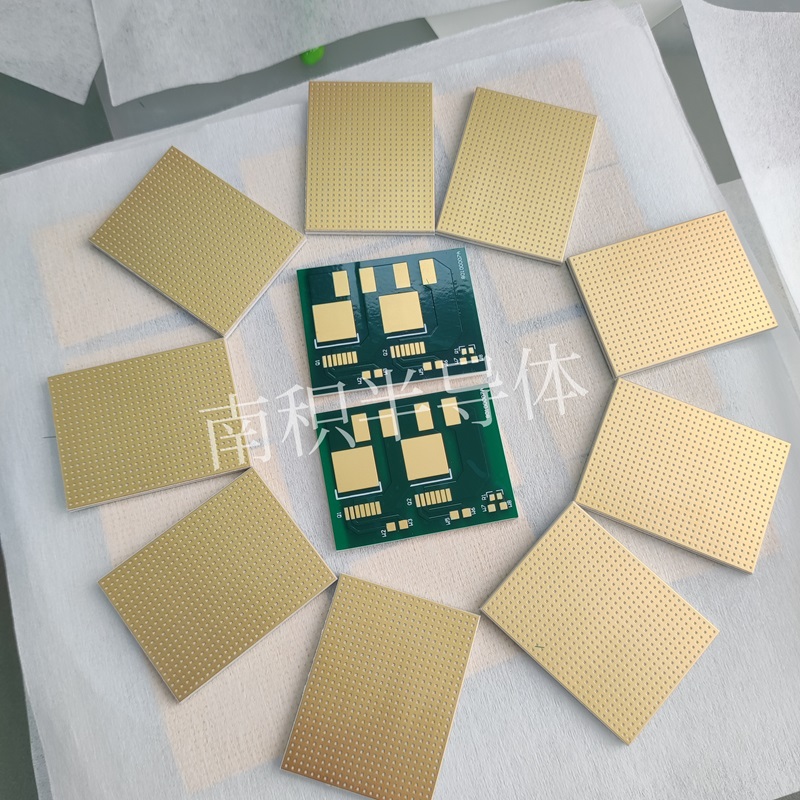
HDI盲埋孔電路板OSP工藝優(yōu)缺點
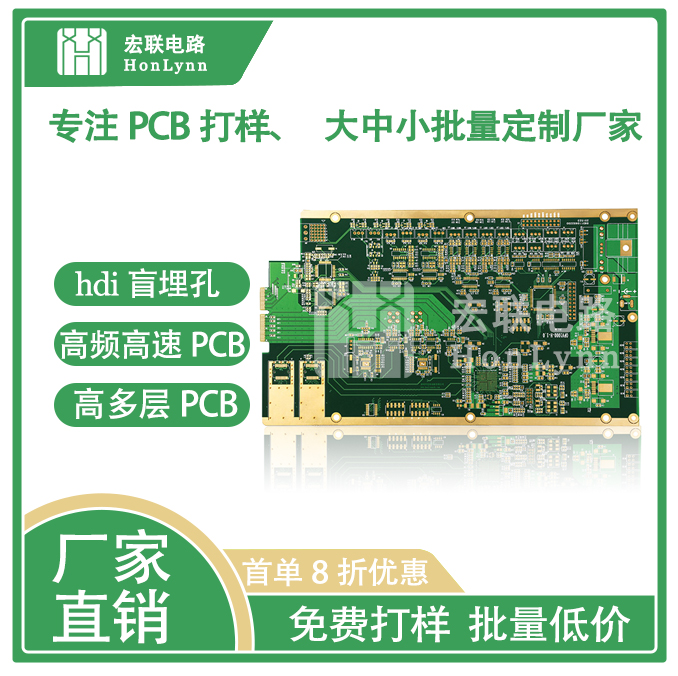
hdi盲埋孔線路板生產(chǎn)工藝流程
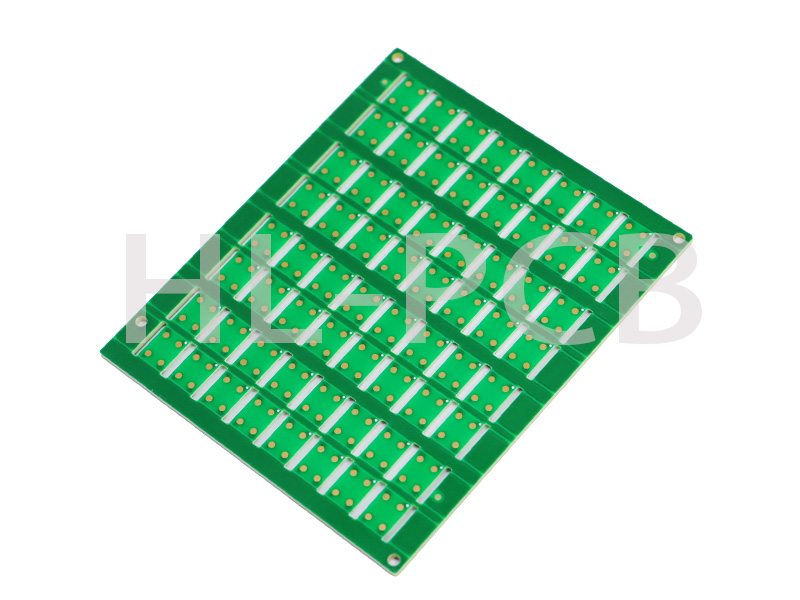
評論