摘要
0201、01005微型片式元件立碑是SMT焊接過程常見的工藝缺陷,特別是隨著電子產(chǎn)品的微型化,立碑問題越來越突出,本文系統(tǒng)介紹了片式元件立碑的機(jī)理及主要影響因素,提出了通過設(shè)計、工藝、設(shè)備、管理的優(yōu)化來系統(tǒng)解決立碑缺陷的主要措施。
前沿
電子產(chǎn)品的發(fā)展趨勢是功能越來越多、重量越來越輕、價格越來越低、密度越來越高,對元器件的要求則是越來越微型化,這不僅表現(xiàn)在諸如BGA、CSP、QFP等封裝形式的有源器件的尺寸減小、引腳間距變小,電容和電阻之類的分立元件的尺寸也在相應(yīng)減小,電子產(chǎn)品發(fā)展趨勢及對器件和PCB帶來的新挑戰(zhàn)。
由于智能手機(jī)等移動終端類產(chǎn)品的多功能化、高密度化發(fā)展趨勢,使得手機(jī)內(nèi)部的元器件貼裝密度迅速增加,微型片式元件的使用量在加大。目前智能手機(jī)上MLCC、Chip-R、片式電感器的用量激增。
隨著這些0402(1mm*0.5mm)、0201(0.6mm*0.3mm)甚至01005(0.4mm*0.2mm)微型封裝元件使用的迅速增加,以及布局密度的不斷提高,組裝難度不斷加大,使得微型片式元件組裝所面臨的加工缺陷成為電子組裝中的主要挑戰(zhàn),而微型片式元件最常見的缺陷之一便是立碑。
圖 元件微型化趨勢
立碑工藝缺陷的機(jī)理分析
立碑在電子制造行業(yè)內(nèi)被稱為"墓碑(tombstoning)、吊橋(drawbridging)、石柱(stonehenging)和曼哈頓(Manhattan)"現(xiàn)象,都是用來描述如圖3所示的片式元件焊接工藝缺陷的形象說法,此類缺陷的典型特點(diǎn)就是元件的一端在回流焊過程中翹起一定角度。
在早期的SMT焊接過程中,立碑現(xiàn)象是與氣相回流焊、紅外回流焊工藝強(qiáng)相關(guān)的工藝缺陷。在氣相回流焊接中,立碑的主要原因是由于元件升溫過快,升溫時沒有一個均熱的過程再達(dá)到焊膏融化,導(dǎo)致熱容量有差異的元件兩端的焊膏不是同時熔化的,所以器件兩端的潤濕力不平衡導(dǎo)致立碑現(xiàn)象發(fā)生。
對紅外回流焊接來說,焊盤、焊膏、焊端顏色的差異都會導(dǎo)致吸收熱量的不同,從而引起兩端焊膏不同時融化造成的器件兩端潤濕力不平衡則引起立碑。
隨著片式元件焊端質(zhì)量的提高、熱風(fēng)回流焊的廣泛使用以及對回流曲線的優(yōu)化研究,立碑現(xiàn)象逐漸減少,已經(jīng)不是SMT組裝過程中的一個重要問題了。
但是,近年隨著電子元件微型化,特別是移動終端類產(chǎn)品中0402、0201、01005封裝器件的大量使用,立碑缺陷又成為SMT工藝的一個主要缺陷,對產(chǎn)品的加工質(zhì)量、直通率、返修成本都產(chǎn)生了很大的影響。
從機(jī)理上來分析,立碑缺陷產(chǎn)生的本質(zhì)原因是器件兩端的潤濕力不平衡,當(dāng)一端的潤濕力產(chǎn)生的轉(zhuǎn)動力矩超過了另一端潤濕力及器件重力聯(lián)合作用的力矩時,在轉(zhuǎn)動力矩的作用下把元件一端提升起來了,元件的受力過程如圖4所示。
圖 立碑現(xiàn)象的力學(xué)分析
圖a為元件貼片后、回流焊前的器件受力狀態(tài),圖4b為回流焊接中立碑時器件的受力狀態(tài),貼片后、回流焊接前器件受元件兩端的粘結(jié)力、支持力F1、F2及重力的作用,焊接過程立碑發(fā)生時器件在拉起端的粘結(jié)力T2、器件重力T3及融化端的潤濕力T4、T5綜合作用下產(chǎn)生翻轉(zhuǎn),此時T4對焊端支撐點(diǎn)產(chǎn)生的力矩大于T2+T3+T5對焊端支撐點(diǎn)產(chǎn)生的力矩之和,即:
M(T4)>M(T2)+M(T3)+M(T5) (1)
由圖可知,元器件越小,重量越輕,就越容易產(chǎn)生立碑現(xiàn)象。
圖中各個參數(shù)的意義:
T1、T2 元件焊端的粘結(jié)力
F1、F2 元件焊端受到的支持力M
(T2) 元件焊端的粘結(jié)力T2產(chǎn)生的力矩
T3 元件的重力
M(T3) 元件的重力T3產(chǎn)生的力矩
T4 元件端部的潤濕力
M(T4) 元件端部的潤濕力T4產(chǎn)生的力矩
T5 元件焊端底部的潤濕力
M(T5) 元件焊端底部的潤濕力
T5產(chǎn)生的力矩
影響片式元件立碑的因素
焊盤設(shè)計對立碑缺陷形成的影響
元件的焊盤尺寸越大,熔融焊料的表面積越大,對焊端產(chǎn)生的潤濕力也越大,對立碑產(chǎn)生的影響也越顯著。IPC標(biāo)準(zhǔn)對焊盤尺寸的設(shè)計有推薦的建議,但是同一類型的器件各個廠家的尺寸存在差異。
如圖所示,對立碑現(xiàn)象影響最大的兩個焊盤尺寸是W與S,W大于S時端部潤濕力產(chǎn)生的力矩比W小于S時產(chǎn)生力矩小,立碑發(fā)生的機(jī)率就小。因此在設(shè)計階段要關(guān)注焊盤的尺寸,綜合器件的尺寸得到合理的焊盤設(shè)計,從而有效減少立碑的發(fā)生。
圖 影響立碑的焊盤尺寸
焊膏印刷對立碑缺陷形成的影響
當(dāng)焊膏印刷出現(xiàn)偏差,焊膏沒有準(zhǔn)確地印刷在焊盤上,如圖6所示,上部焊盤的錫膏印刷出現(xiàn)了偏位,貼片后器件端子沒有與焊膏良好接觸,在回流爐中進(jìn)行回流焊接時,焊膏就不會向元件焊端爬錫,器件的兩端一邊有潤濕力而另一端沒有潤濕力,就會出現(xiàn)嚴(yán)重的力矩不平衡,沒有與焊膏接觸的一端被拉起來而出現(xiàn)立碑。
圖所示是比較嚴(yán)重的印刷不良,有時是由于印刷效果不好,導(dǎo)致焊盤兩端的焊膏量差異比較大,這時在回流焊接時兩端的潤濕力也會有較大的差異,當(dāng)差異達(dá)到一定程度就會導(dǎo)致立碑的發(fā)生。
圖 焊膏印刷偏位導(dǎo)致元件立碑
貼片精度對立碑缺陷形成的影響
如果貼片機(jī)的貼片精度差,貼裝過程中元件端相對于焊盤有較大的偏位,元件兩端與錫膏接觸面積不同,焊膏融化時元件兩端的潤濕力不平衡,導(dǎo)致立碑發(fā)生。
更為嚴(yán)重時元件貼放偏位較大,元件一端與錫膏未接觸上,回流焊接時,元件兩端潤濕力嚴(yán)重不平衡,導(dǎo)致立碑出現(xiàn)。因此對于微型片式元件,貼片精度必須保證,特別是隨著0201、01005器件的大量使用,越小的器件對各類誤差越敏感。
圖 元件貼放偏位對立碑缺陷的影響
回流溫度曲線對立碑缺陷形成的影響
回流焊接溫度曲線對立碑的產(chǎn)生也有較大的影響,如果溫度曲線設(shè)置不當(dāng),比如升溫速率過快、預(yù)熱時間過短等,這就會在回流時造成器件兩端存在較大的溫差,嚴(yán)重時器件一端的焊膏已經(jīng)融化了,而另一端還沒有融化,這時由于兩端潤濕力的不平衡會導(dǎo)致器件立碑。
圖所示就是因?yàn)閮啥撕父嗟臏囟扔休^大差異,焊料沒有同時融化而出現(xiàn)潤濕力不平衡引起的立碑的示意圖。
圖 回流溫度曲線設(shè)置不合理導(dǎo)致立碑
材料可焊性對立碑缺陷形成的影響
器件焊端的可焊性不一致,比如一端可焊性好,一端可焊性差,當(dāng)回流焊接時,融化的焊料對可焊性差的焊端的潤濕力就會小于可焊性好的焊端,這樣兩端就會出現(xiàn)較大的力不平衡,導(dǎo)致立碑發(fā)生。
如果PCB焊盤的一端可焊性差,而另一端可焊性良好,當(dāng)回流焊接時,對于可焊性差的一端,融化的焊料就會被器件焊端吸走,這樣可焊性差的一端的焊盤對器件的潤濕力就很小,而可焊性良好的一端焊盤對器件的潤濕力就會較大,此時依然會由于潤濕力的不平衡而出現(xiàn)立碑。圖9所示為片式元件焊端存在可焊性差異,造成的立碑缺陷。
立碑工藝缺陷的解決措施
立碑缺陷是一種可以防止的工藝缺陷,分析它的形成機(jī)理,總結(jié)根本原因和影響因素,通過工藝設(shè)計、質(zhì)量控制、工藝調(diào)制、設(shè)備改進(jìn)可以減少立碑的發(fā)生,提高組裝過程的直通率、降低缺陷率、減少返修,從而提高電子產(chǎn)品的質(zhì)量與可靠性。
當(dāng)我們對立碑缺陷的機(jī)理有了充分的認(rèn)識后,可以梳理出造成立碑的主要原因圖所示:
圖 造成片式元件立碑缺陷的主要影響因素
對應(yīng)機(jī)理分析和主要原因,我們就可以整理出防止立碑發(fā)生的常見措施:
提高DFM設(shè)計水平,特別是焊盤設(shè)計要合理:焊盤超出片式元件端子的延伸部分要適當(dāng),不能過大;焊盤的寬度要合適,超出器件寬度的焊盤,在回流融化時會使器件飄移,出現(xiàn)立碑的機(jī)率會增大;
保證錫膏印刷位置精度要求和兩端焊膏量的一致;
保證元件貼放位置精度要求;
回流曲線設(shè)置合理:適當(dāng)?shù)纳郎厮俾逝c預(yù)熱時間,避免過快的升溫速率和較短的預(yù)熱時間;
保證材料的良好可焊性:元件焊端和PCB焊盤以及焊膏都要具有良好的可焊性。
誤差控制:包括器件焊端的尺寸誤差、PCB焊盤的尺寸誤差,越小的器件對誤差越敏感。
總結(jié)
隨著040、0201、01005等微型片式元件在電子產(chǎn)品中的廣泛應(yīng)用,立碑缺陷的分析與解決成為困擾SMT工程師的一個主要問題。
本文從微型片式元件立碑缺陷形成的機(jī)理分析入手,通過對影響立碑的各種因素的分析,提出了解決立碑缺陷的各種措施,對于解決SMT組裝過程中片式元件的立碑這種工藝缺陷的有一定的指導(dǎo)意義。
作者介紹
王文利 博士、博士后、教授,西安電子科技大學(xué)電子可靠性(深圳)研究中心主任,雅時國際商訊顧問。
審核編輯:湯梓紅
-
元器件
+關(guān)注
關(guān)注
113文章
4833瀏覽量
95021 -
封裝
+關(guān)注
關(guān)注
128文章
8651瀏覽量
145378 -
smt
+關(guān)注
關(guān)注
43文章
3037瀏覽量
71930 -
BGA
+關(guān)注
關(guān)注
5文章
571瀏覽量
48561
原文標(biāo)題:如何解決0201、01005微型片式元件的立碑缺陷?
文章出處:【微信號:actSMTC,微信公眾號:actSMTC】歡迎添加關(guān)注!文章轉(zhuǎn)載請注明出處。
發(fā)布評論請先 登錄
幾種SMT焊接缺陷及其解決措施
片式元件新寵——超微型超高精度微波MLCC
SMT焊接常見缺陷原因及對策分析
0201元件裝配良率和元件方向之間的關(guān)系
SMT焊接常見缺陷原因和對策分析
請問如何防止SMT回流過程中的立碑和開放缺陷?
SMT線“立碑”的出現(xiàn)和在線修復(fù)
PCB Layout時如何避免立碑缺陷呢?
回流焊接后元件直立產(chǎn)生的原因及處理方法
回流焊元件立碑形成原因以及預(yù)防措施
片式元器件立碑現(xiàn)象該如何有效解決
怎樣避免SMT造成的立碑失效
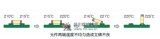
PCB上的立碑不良缺陷

pcb立碑什么意思 如何防止pcb立碑現(xiàn)象發(fā)生
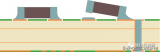
評論