以下文章來源于不懂聊封裝 ,作者大名叫懂懂
一.前言
IC載板(封裝基板)具備高密度、高精度、高性能、小型化和輕薄化等一系列優良特性,成為現代電子產品中不可或缺的關鍵組件。IC載板的結構如下圖所示,在中間芯板的兩面多次壓合增層制成,其作用是為芯片提供電氣連接和機械支撐。一個完整的芯片系統通常由裸芯片(即晶圓片)和封裝體組成,而封裝體包括封裝基板、固封材料和引線等部分。封裝基板作為核心部分,連接裸芯片與外部電路,確保電信號的傳輸與散熱效果。同時,IC載板還具備抗高溫、高頻性能,能夠支撐未來更多電子器件的高速運算與數據處理需求。
有機IC載板的起源可以追溯到集成電路(IC)封裝技術的發展早期。隨著半導體行業的快速進步,芯片的集成度和性能需求不斷提高,傳統的封裝技術如陶瓷和金屬基板逐漸無法滿足更高密度、低成本和輕量化的要求。
20世紀70年代,電子設備的需求開始呈現小型化、低成本和高性能的發展趨勢,推動了有機封裝材料的應用。在這個階段,陶瓷和金屬基板,它們雖然具備良好的熱導率和機械強度,但加工成本高且材料本身較重,不利于小型化和大規模生產,而有機材料(如環氧樹脂)具備重量輕、易于加工和低成本的優勢,成為一個理想的替代選擇。有機IC載板最初是從印刷電路板(PCB)技術中發展而來,借鑒了PCB中常用的有機材料,如FR-4和聚酰亞胺(PI)等。
有機IC載板在20世紀90年代開始廣泛應用,這是因為隨著消費電子和計算機產業的蓬勃發展,對集成電路封裝的需求從低端產品擴展到高性能計算和通信領域。有機基板的優點不僅體現在材料成本上,還在于其適應性強、可以實現更復雜的多層結構,適用于各種先進封裝技術如BGA(球柵陣列封裝)和CSP(芯片尺寸封裝)。
與常規PCB板相比,有機IC載板的線寬和線距更為精細,板子的尺寸也更小,這使得它能夠滿足主流芯片的嚴苛要求。在線寬/線距達到50μm/50μm時,常規PCB已經屬于高端產品,而在封裝基板制造領域,30μm/30μm以內的線寬/線距已屬于常規標準。這種更精密的設計滿足了現代高性能芯片對于體積小、信號傳輸效率高的需求。
隨著技術朝著高密度和高精度方向發展,封裝基板在PCB市場中的占比逐步提升。根據Prismark的數據顯示,2000年封裝基板在PCB市場中的占比為8.43%,到2020年這一比例已增長至15.68%。預計到2026年,封裝基板在PCB市場的占比將進一步上升至21.11%。這一增長趨勢反映出封裝基板在現代電子產品中的重要性,特別是在高性能計算、5G通信、物聯網和其他先進應用領域,封裝基板已成為核心基礎材料。
二.材料選擇
1. 芯板材料—BT樹脂
“BT”樹脂是由日本三菱瓦斯化學公司開發的一種具有特殊性能的樹脂材料,其名稱來源于該公司推出的化學商品名。BT樹脂由雙馬來酰亞胺(Bismaleimide,簡稱BMI)和氰酸酯(Cyanate Ester,簡稱CE)樹脂通過合成反應制備而成,具有優異的熱穩定性、機械強度和電氣性能[1]。這種材料的開發始于1972年,當時三菱瓦斯化學公司就著手研究如何將BT樹脂應用于電子封裝領域。到1977年,BT板首次成功應用于芯片封裝,標志著其作為高性能封裝材料的潛力得到了初步驗證。
在隨后的幾十年中,三菱瓦斯化學公司持續優化和改進BT樹脂的性能,特別是針對電子封裝和高頻應用的需求。通過對基礎BT樹脂的不斷改性,該公司開發出了多種不同類型的BT樹脂材料,以滿足電子產品性能日益復雜的需求。到20世紀90年代末,三菱瓦斯化學已推出十幾種不同品類的BT樹脂產品,覆蓋多個應用領域。
在日本、美國、歐洲等地區,BT樹脂在高性能、高頻電路用PCB的制造中得到了越來越廣泛的應用。尤其是在過去兩三年里,它已經成為全球范圍內迅速崛起的高密度互連(HDI)技術中積層多層板(Build-Up Multilayer, BUM)和封裝用基板的重要材料之一。BT樹脂憑借其出色的電氣性能、低損耗和高穩定性,特別適用于需要精密互連和高頻傳輸的應用場景,推動了這些先進封裝技術的發展,并成為電子行業中不可或缺的基礎材料。
2. 增層材料—BT樹脂
ABF膠膜(Ajinomoto Build-up Film)的起源可以追溯到20世紀90年代,由日本味之素公司開發,最初是為了應對半導體封裝技術日益復雜的需求而誕生的。隨著芯片集成度的提高,傳統的PCB材料難以滿足高密度互連(HDI)和微型化封裝的要求。為解決這一問題,味之素利用其在化工領域的優勢,開發出了一種專門用于IC載板制造的增層膠膜材料——ABF膠膜。
ABF材料的開發標志著半導體封裝材料的一次重要技術突破。它不僅滿足了更精細、更密集的電路互連需求,還具備良好的電氣性能和熱穩定性,適用于高速、高頻信號的傳輸環境。這一材料的推出推動了積層多層板(BUM)和先進封裝技術的快速發展,并迅速在全球半導體制造行業中獲得廣泛應用,成為IC封裝中的關鍵材料之一。
這種膠膜材料通常被應用于IC載板的增層工藝中,通過半加成法(SAP)或改良半加成法(mSAP)將其壓合在芯板上,形成精細的導線圖形,支持更密集的互連布局。隨著芯片封裝的復雜性不斷增加,ABF材料在滿足高密度和高性能需求方面發揮著至關重要的作用,已成為現代高端封裝技術的標準材料之一。
三.工藝制備(增層SAP)介紹
有機IC載板是一種采用半加成法(SAP)工藝的封裝基板,通過在增層膠膜上構建電子線路。增層膠膜的一個顯著特點是其不含玻纖成分,這種設計使得它在制造高精細度電子線路方面表現優異。由于沒有玻纖的干擾,增層膠膜能夠更好地適應微小電路結構的需求,確保信號傳輸的可靠性和一致性。
此外,增層膠膜封裝基板的另一個重要優勢在于其疊層技術的應用。這種技術使得制造多層線路板成為可能,從而在有限的空間內實現高密度互連,滿足現代電子設備對小型化和高性能的要求。通過精確的層疊設計,增層膠膜可以支持多層電路的集成,極大地提升了電路板的功能密度和性能[2]。
通過這些技術和工藝的結合,有機IC載板在高端封裝領域中扮演著至關重要的角色,為現代電子產品提供了強大的支持。隨著技術的不斷進步,有機IC載板的應用前景將更加廣泛,成為推動電子行業發展的關鍵力量。
加工流程的核心包括多個關鍵步驟,每個環節都至關重要,以確保最終產品的高質量和可靠性。
真空壓合:首先,將增層膠膜與芯板進行真空壓合。此步驟需要在特定的溫度和壓力下進行,以確保兩者的緊密結合。通常會使用熱壓機,在精確控制的條件下使增層膠膜與芯板充分融合,形成穩定的基礎結構。良好的層壓質量對后續工藝的成功至關重要。
激光鉆孔:緊接著,通過激光鉆孔技術形成微孔。此過程利用高能激光束精確打孔,能夠在不損傷材料的情況下實現微米級的孔徑。關鍵在于激光的焦點控制和移動速度,確保孔的直徑和位置精確,且孔壁光滑,為后續的化學處理打下良好基礎。
除膠渣:鉆孔后,進行除膠渣,以清潔孔壁。這一步驟通常使用化學溶劑或超聲波清洗,確保孔內無任何殘留物。殘留物不僅會影響導電性,還可能導致電路缺陷,因此徹底清潔至關重要。
種子層形成:接下來,通過化學鍍銅或濺射技術形成導電的種子層。這個過程要求對化學藥水的濃度、溫度和反應時間進行嚴格監控,以實現均勻的鍍層厚度。種子層的質量直接影響后續電鍍的效果,是確保良好導電性能的基礎。
電鍍加厚:然后,進行電鍍工藝對線路進行加厚,并填充激光鉆孔形成的微孔。電鍍過程中,必須控制電流密度和時間,以確保電鍍層的均勻性和厚度。這一步驟至關重要,確保導電路徑的完整性,同時提供足夠的機械強度。
干膜移除:接下來,移除干膜,清除多余的材料。此步驟通常通過化學溶劑進行,目的是去掉覆蓋在電路上的保護膜,以露出電鍍完成的導電線路,確保電路的清晰和準確。
閃蝕:最后,通過閃蝕去除多余的種子層。閃蝕是一種選擇性去除技術,使用適當的化學藥水,僅去除未被電鍍覆蓋的種子層。這一步驟確保電路的純凈度,同時提升產品的電氣性能。
整個過程中,關鍵的挑戰在于精確控制每個步驟的化學藥水及工藝參數,確保形成高精度的導電互連線路,特別是在種子層的形成和微孔填充過程中。工藝必須高度精確,以確保電氣性能和結構完整性。由于這些特點,該封裝基板技術在先進封裝領域具有廣泛的應用,尤其適用于高密度封裝需求,如高性能計算、5G通信和人工智能設備等領域,推動著電子產品向更高性能和更小型化的方向發展。
四.國內發展的特點
1. 產業鏈高度集中,公司間關系穩定且緊密
有機封裝基板的產能集中度遠高于其他類型的印制電路板(PCB)。全球約80%的市場份額由日本、韓國和中國臺灣地區的前十大有機封裝基板生產商占據,展現出明顯的規模優勢。相比之下,中國大陸目前只有華南地區的少數幾家公司具備相對簡單的封裝基板生產技術。
最終采購需求主要集中在高通、三星、蘋果、小米和聯發科等大型科技公司。這些公司由于訂購數量龐大且交期集中,通常采用包產方式進行采購,以確保供應的穩定性。該行業對供應商資質要求極高,尤其是在產品質量和交期方面,認證過程復雜且耗時。例如,三星的供應商認證周期長達24個月。一旦供應商通過認證,企業通常不會輕易更換合作伙伴。
從產業鏈關系來看,相當一部分的有機封裝基板巨頭源自集成電路設計或封測行業,體現了垂直整合的特點。例如,矽品科技通過其封測業務拓展了全懋科技,進入有機封裝基板市場;聯電科技則通過欣興科技在這一領域展開業務。而南亞與景碩則來自其他行業背景。
2. 盡管技術發展迅速,但基板材料仍處于壟斷狀態
有機封裝基板在技術特征、工藝方法以及產品形態上,具備多種技術發展路線。其關鍵技術特征在于對線寬和線距(L/S)的把控。目前,有機封裝基板的典型線寬和線距達到15 μm/15 μm級別,而傳統的“板級”印制電路板(PCB)的線寬和線距則為30 μm/30 μm級別之間。為了滿足更高密度的芯片封裝需求,出現了一種介于二者之間的新產品形態——類載板(SLP),其線寬和線距小于30 μm/30 μm,特別適用于芯片封裝。
在工藝方法方面,有機封裝基板的發展趨勢呈現出減成蝕刻法、半加成法(SAP)和改良半加成法(mSAP)共同應用的趨勢。這些工藝方法不斷改進,不僅使引線扇出更加精細、導線間距更加密集,還減少了產品所需的層壓次數,提高了生產效率。
在產品形態方面,為了應對晶圓扇出封裝技術(InFo-WLP)帶來的潛在價值鏈轉移和產業鏈整合,有機封裝基板生產商逐漸從傳統的標準芯片級封裝(CSP)和焊球陣列(BGA)等產品形態,轉向開發更具前景的三維嵌入式基板產品。這種三維嵌入技術不僅能提升封裝密度,還能增強產品的整體性能。
盡管工藝技術在不斷進化,但大多數剛性有機封裝基板仍主要依賴幾種關鍵基材,尤其是雙馬來酞亞胺三嗪樹脂(BT樹脂)和增層膠膜(ABF)材料。這些材料由少數幾家日本公司壟斷,如三菱瓦斯和昭和電工掌握的BT樹脂,以及味之素公司掌握的ABF膠膜。由于這些材料經過多年測試和迭代,與客戶的生產工藝高度匹配,因此在市場上具有較強的壟斷性。
3. 企業和行業發展的關鍵是穩定的供應和用戶聯系
從當前行業現狀來看,有機封裝基板的發展面臨著兩大主要障礙:高技術難度和材料壁壘。由于這些基板的生產和應用需要較高的專業技術,許多潛在客戶在初始階段難以進入市場,這使得行業內競爭格局變得復雜且高度集中。
這一現狀說明了封裝基板發展必須依賴于兩個關鍵因素:一方面,需要建立廣泛的客戶基礎,以確保產品的市場需求和應用場景;另一方面,穩定的材料供應同樣至關重要,材料供應鏈的可靠性直接影響到生產效率和產品質量。這意味著行業參與者不僅要關注與下游客戶的緊密聯系,還需要積極整合上游材料供應商,以保障原材料的及時供應和技術支持。
一旦企業能夠成功構建起穩定的上下游關系,將有助于降低市場風險,并增強行業的整體競爭力。在我國集成電路快速發展的背景下,有機封裝基板的發展潛力巨大,有望再現中低端印制電路板在歷史上的快速崛起。因此,行業各方應共同努力,打破現有的技術壁壘和材料限制,以推動有機封裝基板的創新與應用,為未來的市場增長奠定堅實基礎[3]。
-
集成電路
+關注
關注
5420文章
11987瀏覽量
367536 -
半導體
+關注
關注
335文章
28694瀏覽量
234033 -
封裝
+關注
關注
128文章
8590瀏覽量
144972 -
IC載板
+關注
關注
6文章
54瀏覽量
16089
原文標題:高密度IC載板全解讀:從材料選擇到技術優勢,一文看懂
文章出處:【微信號:深圳市賽姆烯金科技有限公司,微信公眾號:深圳市賽姆烯金科技有限公司】歡迎添加關注!文章轉載請注明出處。
發布評論請先 登錄
器件高密度BGA封裝設計
高密度印制電路板(HDI)簡介
探討高密度小間距LED屏工藝
高密度PCB(HDI)檢驗標準
高密度印制電路板(HDI),高密度印制電路板(HDI)是什么
指導分享高密度光纖配線架安裝方法
高密度光纖配線架值得沖嗎
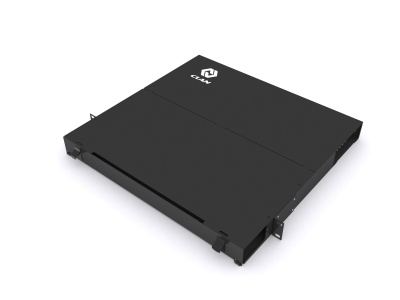
評論