內容概述
第 1 章:復合材料和機械測試簡介
第 2 章:拉伸試驗 (ASTM D3039)
第 3 章:壓縮試驗 (ASTM D3410)
第 4 章:彎曲和剪切測試
第 5 章:沖擊和疲勞測試
第 6 章:環境對機械性能的影響
第 7 章:復合材料的無損檢測 (NDT)
第 8 章:數據分析、解釋和質量控制
第 9 章:復合材料測試中的高級主題
第 10 章 未來趨勢和工業應用
第 1 章:復合材料和機械測試簡介
復合材料及其應用概述
復合材料,通常簡稱為復合材料,是由兩種或多種物理或化學特性明顯不同的組成材料制成的工程材料。當它們組合在一起時,它們產生的材料具有與單個組件不同的特性。在成品結構中,各個組件保持獨立和獨特,將復合材料與混合物和固溶體區分開來。
復合材料通常包括:
基體:第一相,它是連續的,圍繞著另一相。
增強材料:嵌入在矩陣中的第二相。
常見的復合材料類型包括:
纖維增強聚合物 (FRP)
金屬基復合材料 (MMC)
陶瓷基復合材料 (CMC)
由于其獨特的特性,復合材料被廣泛用于各種應用:
航空航天:飛機結構、航天器部件
汽車:車身面板、底盤零部件
船舶:船體、海上平臺
建筑:橋梁、建筑物、鋼筋
運動器材:網球拍、自行車架
風能:渦輪機葉片
復合材料機械試驗的重要性
復合材料的機械測試至關重要,原因如下:
材料表征:確定復合材料的機械性能,例如強度、剛度和韌性。
質量控制:確保制造的復合材料符合設計規范和行業標準。
設計驗證:驗證復合結構是否能夠承受預期的負載和環境條件。
失效分析:了解復合材料在各種載荷條件下的失效模式和機理。
材料開發:幫助開發新的復合材料和制造工藝。
認證:滿足安全關鍵型應用(如航空航天)的法規要求。
復合行為的基本原理
應力-應變關系
纖維、基體、復合材料的應力-應變
由于復合材料的異質性,它們表現出獨特的應力-應變關系:
線彈性:許多復合材料在達到一定應力水平時表現出線彈性行為。
各向異性:機械性能隨施加載荷的方向而變化。
纖維-基體相互作用:應力-應變行為受纖維和基體之間的載荷傳遞的影響。
漸進式失效:復合材料經常逐漸失效,在最終失效之前會出現多種損傷機制。
沿纖維方向加載的單向纖維增強復合材料的典型應力-應變曲線顯示:
初始線彈性區域
由于基體塑性或纖維-基體脫鍵而可能出現的非線性區域
纖維失效時應力突然下降
各向異性
各向異性是許多復合材料的基本特性,尤其是纖維增強復合材料:
定向特性:強度和剛度等機械性能隨方向變化很大。
正交各向異性行為:許多復合材料表現出正交各向異性行為,在三個相互垂直的方向上具有不同的特性。
層壓板理論:復合材料的各向異性特性需要使用層壓板理論進行結構分析和設計。
測試意義:各向異性需要在多個方向上進行測試,以充分表征材料特性。
了解復合材料的各向異性行為對于以下方面至關重要:
正確的材料選擇
精確的結構設計
針對特定應用優化纖維取向
復合材料的復雜行為,包括其各向異性性質和獨特的應力-應變關系,強調了全面和適當的機械測試的重要性。這些測試提供了必要的數據,用于了解、預測和優化復合結構在各種應用中的性能。
第 2 章:拉伸試驗 (ASTM D3039)
縱向 (a) 和橫向 (b) 單向纖維的拉伸試樣
拉伸試驗是復合材料最基本和應用最廣泛的機械試驗之一。它提供有關材料在單軸載荷條件下的強度、剛度和行為的關鍵信息。ASTM D3039 標準是對聚合物基復合材料進行拉伸試驗的最常用方法。
測試設置和試樣制備
試樣幾何形狀
基于纖維取向的物種幾何形狀
ASTM D3039 標準規定了試樣幾何形狀的幾個關鍵方面:
形狀:通常為扁平條或矩形橫截面
尺寸:根據鋼筋類型及其方向而變化
長度:通常為 250 毫米(10 英寸),用于單向和織物復合材料
寬度:0° 單向通常為 25 毫米(1 英寸),90° 單向通常為 25 毫米(1 英寸),織物復合材料為 25 毫米(1 英寸)
厚度:通常為 2-3 毫米(0.08-0.12 英寸),但可能會有所不同
試樣制備
切割:應小心切割標本,以避免分層或其他損壞。通常使用水射流切割或使用金剛石涂層刀片進行精密鋸切。
凸耳粘合:對于某些試樣類型,尤其是纖維取向為 0° 的試樣類型,端部凸片被粘合以防止夾具引起的失效。極耳通常由玻璃纖維/環氧樹脂復合材料或鋁制成。
表面處理:如果要直接在試樣上測量應變,則應為試樣表面的應變片應用做好準備。
測試設置
試驗機:一種能夠保持恒定橫梁速度和精確測量負載的萬能試驗機。
夾具:液壓或機械夾具,可以牢固地夾持試樣而不會造成損壞或打滑。
應變測量:直接粘接到試樣上的應變片或連接到測厚截面的引伸計。
數據采集系統:記錄整個測試過程中的載荷、位移和應變數據。
縱向和橫向測試
復合材料,尤其是那些具有單向增強的復合材料,表現出高度各向異性的行為。因此,縱向(0°,平行于纖維)和橫向(90°,垂直于纖維)方向的檢測對于完整表征至關重要。
縱向測試 (0°)
提供有關纖維主導特性的信息
通常會產生更高的強度和剛度值
失效通常是由于纖維斷裂而發生的
橫向測試 (90°)
提供有關矩陣主導屬性的信息
通常會導致較低的強度和剛度值
失效通常是由于基體開裂或纖維基體脫粘而發生的
這兩個方向之間的明顯性能差異凸顯了復合材料的各向異性以及在多個方向上進行測試的重要性。
數據分析和解釋
關鍵參數
極限拉伸強度 (UTS):材料在失效前可以承受的最大應力。
楊氏模量 (E):線性彈性區域中應力-應變曲線的斜率,表示材料的剛度。
泊松比 (ν):線彈性區域中橫向應變與軸向應變的負比。
失效應變 (εf):材料在失效前承受的最大應變。
應力-應變曲線分析
線性區域:確定應力-應變曲線的線性部分以計算楊氏模量。
屈服點:對于某些復合材料,尤其是那些具有延展性基體的復合材料,可能會觀察到屈服點。
Failure Point:失效時的極限抗拉強度和相應應變的點。
統計分析
鑒于復合材料固有的可變性,測試結果的統計分析至關重要:
平均值:計算強度、模量和其他參數的平均值。
標準差:確定數據的分布。
變異系數:評估數據的相對變異性。
故障模式分析
檢查拉伸試樣的失效模式可提供有價值的見解:
纖維主導的失效:通常見于 0° 試樣,以纖維斷裂為特征。
基體主導的失效:常見于 90° 試樣,通常表現為基體開裂或纖維-基體脫粘。
分層:復合層分離,這可能表明制造缺陷或不適當的測試設置。
了解和正確解釋拉伸試驗數據對于以下方面至關重要:
材料選擇和鑒定
結構設計和分析
制造過程中的質量控制
拉伸測試雖然看似簡單,但需要仔細注意試樣制備、測試執行和數據分析,以獲得可靠且有意義的復合材料結果。
第 3 章:壓縮試驗 (ASTM D3410)
壓縮試驗試樣的幾何形狀
壓縮試驗是表征復合材料的一個關鍵方面,特別是對于壓縮載荷較大的應用,例如航空航天結構。ASTM D3410 標準提供了一種確定由高模量纖維增強的聚合物基復合材料的面內壓縮性能的方法。
測試方法和夾具
復合材料的壓縮試驗比拉伸試驗更具挑戰性,因為很難在不引起屈曲或其他不良失效模式的情況下引入純壓縮載荷。已經開發了幾種測試方法和夾具來應對這些挑戰:
1. ASTM D3410(程序 B)- IITRI 測試方法
伊利諾伊理工學院研究所 (IITRI) 夾具是 ASTM D3410 中規定的最常用的方法:
夾具設計:由兩個楔形夾持塊組成,它們通過夾持端的剪切力將壓縮載荷施加到試樣上。
載荷引入:壓縮力通過錐形楔形夾具施加,該夾具將載荷均勻地分布在試樣寬度上。
對齊:夾具設計有助于保持正確對齊,降低因屈曲而過早失效的風險。
2. ASTM D695 - 針對復合材料進行改性
雖然該方法主要設計用于未增強塑料,但該方法也適用于復合材料:
夾具:使用簡單的支撐夾具來防止薄試樣屈曲。
試樣:通常需要較厚的試樣或端部片,以防止端部破碎失效。
3. ASTM D6641 - 組合載荷壓縮 (CLC) 測試
該方法結合了端部載荷和剪切載荷:
夾具:使用緊湊的夾具,對試樣施加端部載荷和剪切載荷。
優點:與 ASTM D3410 相比,降低了端部破碎失效的風險,并且可以容納較短的試樣。
試樣幾何形狀注意事項
正確的試樣幾何形狀對于獲得有效的壓縮測試結果至關重要:
1. 長厚比
典型比率:架空長度應為試樣厚度的 4-6 倍,以防止整體屈曲。
ASTM D3410 建議:大多數聚合物復合材料的標距長度為 12-25 毫米(0.5-1.0 英寸)。
2. 寬度
標準寬度:對于單向復合材料,通常為 6.4-12.7 毫米(0.25-0.50 英寸)。
考慮:寬度應足以代表材料,但又不能太寬以引起柱屈曲。
3. 厚度
典型范圍:1-6 毫米(0.040-0.24 英寸),具體取決于材料和測試夾具。
考慮因素:較厚的試樣可降低屈曲的風險,但可能無法代表實際結構中使用的薄層壓板。
4. 結束選項卡
目的:分配抓取力并防止端部破碎失效。
材料:通常由玻璃纖維/環氧樹脂復合材料或鋁制成。
幾何形狀:通常以 30-60 度斜面提供平滑的負載過渡。
復合材料壓縮試驗的挑戰
復合材料的壓縮試驗面臨幾個獨特的挑戰:
1. 防止屈曲
問題:復合材料試樣,尤其是薄層壓板,在壓縮載荷下容易屈曲。
解決方案:仔細的夾具設計、適當的試樣幾何形狀和可能的防屈曲導軌。
2. 結束效果
問題:載荷端的應力集中會導致過早失效。
解決方案:使用設計合理的端片并仔細制備試樣。
3. 對齊
問題:未對中會引入彎矩,從而導致過早或無效的失效。
解決方案:精確加工試樣和夾具,并仔細設置測試設備。
4. 應變測量
問題:短標距長度的應變片或引伸計的空間有限。
解決方案:使用小型應變片或非接觸式應變測量技術,如數字圖像相關 (DIC)。
5. 故障模式識別
問題:區分有效的壓縮失效和無效模式,如端部破碎或屈曲。
解決方案:仔細檢查失敗的樣本,并在測試過程中可能使用高速成像。
6. 環境影響
問題:復合材料對溫度和濕度敏感,這會顯著影響壓縮性能。
解決方案:受控的測試環境并在測試前對試樣進行適當的調節。
7. 材料各向異性
問題:復合材料的高度定向特性需要在多個方向上進行測試。
解決方案:對具有不同纖維取向(0°、90°和可能的離軸)的試樣進行測試。
復合材料的壓縮測試雖然具有挑戰性,但為材料表征和結構設計提供了關鍵數據。了解這些挑戰并實施適當的解決方案是獲得可靠和有意義的復合材料壓縮測試結果的關鍵。
第 4 章:彎曲和剪切測試
彎曲和剪切測試對于表征復合材料在彎曲和剪切載荷下的機械性能至關重要。這些測試為了解材料在彎曲和剪切應力較大的應用中的性能提供了寶貴的見解。
彎曲試驗 (ASTM D7264):三點彎曲和四點彎曲
(b) 四點彎曲試驗
彎曲測試確定材料在彎曲載荷下的行為。ASTM D7264 標準描述了三點和四點彎曲試驗的程序。
三點彎曲
測試設置:
試樣在兩個點處得到支撐,并在中點加載。
垂直于試樣的長軸施加載荷。
關鍵參數:
支撐跨度
裝載鼻直徑
十字頭速度
計算:
彎曲強度:σf = 3PL / (2bh2)
彎曲模量:Ef = L3m / (4bh3)其中:P = 載荷,L = 支座跨度,b = 寬度,h = 厚度,m = 載荷-撓度曲線的斜率
優點:
設置簡單
中點最大應力
限制:
支座附近的高剪切應力
裝載點可能造成局部損壞
四點彎曲
測試設置:
試樣在兩個外部點受到支撐,并在兩個內部點加載。
載荷分布在試樣的較大區域上。
關鍵參數:
支撐跨度
加載跨度(內部加載點之間的距離)
裝載鼻直徑
十字頭速度
計算:
彎曲強度:σf = 3PL / (4bh2)
彎曲模量:Ef = 0.21L3m / (bh3)其中:P = 載荷,L = 支座跨度,b = 寬度,h = 厚度,m = 載荷-撓度曲線的斜率
優點:
加載點之間的彎矩均勻
降低剪切失效的風險
限制:
更復雜的設置
裝載點可能造成局部損壞
樣本注意事項:
典型尺寸:100-200 mm 長,13-25 mm 寬
跨厚比:三點彎曲通常為 16:1,四點彎曲通常為 32:1
表面質量對于防止過早失效至關重要
面內剪切試驗 (ASTM D3518)
面內剪切試驗的試樣表示
ASTM D3518 測試方法確定了由高模量纖維增強的聚合物基復合材料的面內剪切性能。
測試原理:
在 ±45° 層壓板上進行拉伸試驗,以產生面內剪切。
該測試基本上是“拉伸”±45° 纖維,在材料中產生剪切狀態。
標本制備:
平衡對稱的 ±45° 層壓板
典型尺寸與拉伸試樣相似 (ASTM D3039)
測試程序:
作為標準拉伸試驗進行
在縱向和橫向測量的應變
計算:
剪切應力: τ12 = P / (2A)
剪切應變:γ12 = εx - εy
剪切模量: G12 = Δτ12 / Δγ12 其中: P = 施加的載荷,A = 橫截面積,εx = 縱向應變,εy = 橫向應變
優點:
使用標準拉伸試驗設備
提供完整的剪切應力-應變曲線
限制:
僅限于面內剪切特性
可能不代表所有載荷條件
層間剪切強度測試 (ASTM D2344)
層間剪切試驗示意圖
ASTM D2344 標準,也稱為短梁強度 (SBS) 測試,用于確定復合材料的層間剪切強度。
測試原理:
短梁承受三點彎曲
短跨度導致層間剪切破壞
標本制備:
典型的單向層壓板
長度 = 6 ×厚度
寬度 = 2 ×厚度
測試設置:
三點彎曲配置
跨度長度 = 4 ×厚度
計算:
層間剪切強度:ILSS = 0.75 × P / (b × h) 其中:P = 最大載荷,b = 試樣寬度,h = 試樣厚度
優點:
簡單快速的測試
需要小樣本
限制:
可能不會產生純粹的層間剪切破壞
結果會受到加載點應力集中的影響
故障模式:
層間剪切 (所需模式)
非彈性變形
柔性
非彈性變形和層間剪切
解釋故障模式對于驗證測試結果至關重要。
彎曲和剪切測試為了解復合材料在復雜載荷條件下的行為提供了必要的數據。這些測試與拉伸和壓縮測試相結合,可以全面表征復合材料的機械性能,這對于各種應用中的設計和分析至關重要。
第 5 章:沖擊和疲勞測試
拉伸 拉伸 疲勞試驗試樣
沖擊和疲勞測試對于了解復合材料在突然載荷和循環載荷條件下的行為至關重要。這些測試為了解材料的韌性、能量吸收能力和重復載荷下的長期性能提供了寶貴的見解。
沖擊試驗:簡支梁和懸臂梁試驗
沖擊試驗測量材料在斷裂過程中吸收能量的能力。對于復合材料,這些測試在評估損傷容限和能量吸收能力方面尤為重要。
簡支梁沖擊試驗
測試原理:
帶缺口的試樣作為水平梁支撐
擺錘撞擊與缺口相對的一側的試樣
測量骨折期間吸收的能量
標本制備:
復合材料通常為 55 mm x 10 mm x 10 mm
試樣中心的 V 型缺口或 U 型缺口
測試程序:
將試樣放置在測試夾具中,使缺口背對撞擊邊緣
鐘擺從已知高度釋放
吸收的能量是根據沖擊前后擺錘高度的差異計算的
計算:
沖擊能量 = mgh? - mgh? 其中:m = 擺錘的質量,g = 重力加速度,h? = 初始高度,h? = 最終高度
優點:
簡單且應用廣泛的測試
適合比較不同的材料
限制:
結果可能受試樣尺寸和缺口幾何形狀的影響
可能無法準確表示實際應用程序中的沖擊行為
懸臂梁沖擊試驗
測試原理:
與簡支梁試驗類似,但試樣是垂直夾持的
擺錘在與缺口相同的一側撞擊試樣
標本制備:
復合材料通常為 64 mm x 12.7 mm x 3.2 mm
試樣一端的 V 形缺口
測試程序:
垂直夾持試樣,使缺口朝向沖擊邊緣
鐘擺從已知高度釋放
吸收的能量的計算方式與簡支梁測試相同
優點:
適用于測試薄片材料
可用于測試不同方向的各向異性材料
限制:
夾緊會引入應力集中
結果會受到復合材料中纖維取向的影響
復合材料的注意事項:
纖維取向相對于沖擊方向會顯著影響結果
復合材料中的失效模式(纖維斷裂、基體開裂、分層)可能很復雜
可能需要具有不同取向的多個樣品才能進行完整表征
疲勞試驗 (ASTM D3479):拉伸-拉伸和壓縮-壓縮
疲勞測試評估材料在循環載荷條件下的性能。對于復合材料,疲勞行為至關重要,因為它們用于風力渦輪機葉片或飛機結構等長期循環載荷應用。
疲勞試驗的一般原則
測試目標:
確定不同應力水平下失效的循環次數
生成 S-N 曲線(應力與循環次數)
關鍵參數:
最大應力
應力比 (R = 最小應力 / 最大應力)
加載頻率
環境條件(溫度、濕度)
失敗標準:
完全骨折
剛度降低(例如,模量降低 10%)
特定數量的損傷或分層
拉伸-拉伸疲勞 (ASTM D3479)
測試設置:
與靜態拉伸試驗裝置類似
試樣通常類似于拉伸試驗中使用的試樣 (ASTM D3039)
測試程序:
施加在最小值和最大值之間變化的正弦拉伸載荷
典型的應力比 (R) 范圍為 0.1 至 0.8
頻率通常為 1-10 Hz,具體取決于材料和測試目標
數據分析:
繪制 S-N 曲線(應力幅值與失效循環次數)
確定疲勞極限或耐久極限(如果適用)
復合材料的注意事項:
損傷累積可能很復雜(基體開裂、纖維斷裂、分層)
疲勞行為在很大程度上取決于纖維取向和鋪層順序
壓縮 - 壓縮疲勞
測試設置:
與靜態壓縮測試設置類似
對于薄試樣,可能需要防屈曲導軌
測試程序:
施加正弦壓縮載荷
典型應力比 (R) > 1(例如,R = 10)
與張力-張力相比,通常使用較低的頻率(以避免加熱)
挑戰:
避免屈曲,尤其是在高循環次數時
處理管端破碎故障
復合材料的注意事項:
對于某些復合材料,壓縮疲勞通常比拉伸疲勞更重要
基體特性在壓縮疲勞行為中起著重要作用
復合材料疲勞試驗的一般注意事項
環境影響:
溫度和濕度會顯著影響疲勞壽命
考慮在相關條件下使用環境室進行測試
頻率效果:
較高的頻率會導致內部加熱,尤其是在熱塑性基復合材料中
在測試持續時間和避免熱效應之間取得平衡
損害監測:
非破壞性技術(例如聲發射、熱成像)可用于監測損傷進展
在整個測試過程中通常會監測剛度退化
可變性:
復合材料的疲勞數據通常顯示高散射
統計分析和多重測試對于可靠的表征至關重要
失效模式分析:
不合格試樣的試驗后檢查對于了解失效機制至關重要
不同的失效模式可能在不同的應力水平或循環次數中占主導地位
沖擊和疲勞測試提供有關復合材料在動態和循環載荷條件下性能的關鍵信息。這些測試對于預測復合材料結構在從航空航天到風能等各種應用中的長期行為和可靠性至關重要。
第 6 章:環境對機械性能的影響
環境因素會顯著影響復合材料的機械性能。了解這些影響對于預測長期性能和確保各種應用的可靠性至關重要。本章重點介紹吸濕性、溫度影響以及環境和機械組合測試。
吸濕性測試
吸濕性會顯著影響聚合物基復合材料的機械性能,尤其是那些具有環氧樹脂等吸濕性基體的復合材料。
測試方法
ASTM D5229:聚合物基復合材料吸濕性能和平衡調節的標準測試方法a)試樣制備:
通常為扁平的矩形試樣
尺寸:長度 25-100 毫米,寬度 25-100 毫米,制造厚度
b)測試程序:
將試樣干燥至恒重
浸入水中或暴露在受控濕度下
定期稱量試樣,直到達到平衡
c)計算方法:
水分含量:M = [(W - W0) / W0] × 100% 其中:W = 濕重, W0 = 干重
ASTM D570:塑料吸水率的標準測試方法
類似的程序,通常用于純樹脂樣品
關鍵考慮因素
擴散動力學:
繪制水分含量與時間平方根的關系圖
確定擴散系數
邊緣效果:
密封樣品邊緣以模擬厚層壓板中的一維擴散
溫度影響:
較高的溫度通常會加速水分吸收
光纖/矩陣接口:
水分會降解纖維/基體界面,影響機械性能
可逆性:
干燥后性能恢復試驗
溫度影響
溫度會顯著影響復合材料的機械性能,尤其是基體主導的性能。
測試方法
ASTM D3045:塑料空載熱老化的標準實踐
ASTM D5229:包括高溫調節程序
關鍵考慮因素
玻璃化轉變溫度 (Tg)):
使用動態機械分析 (DMA) 或差示掃描量熱法 (DSC) 測定 Tg
Tg 附近發生重大性質變化
熱膨脹系數 (CTE):
使用膨脹計或應變計進行測量
對于預測多材料系統中的熱應力非常重要
高溫測試:
在高溫下進行機械測試
使用環境箱和拉伸/壓縮試驗機
低溫測試:
對于航空航天應用尤為重要
使用低溫室進行極端低溫測試
熱循環:
模擬真實世界的溫度波動
監測微裂紋或分層
環境和機械測試相結合
實際應用通常涉及同時暴露于環境條件和機械負載下。組合測試提供更真實的性能數據。
測試方法
ASTM D2584:固化增強樹脂燒失量的標準測試方法
與機械測試結合使用,將性能變化與基體降解相關聯
ASTM E1640:通過動態機械分析分配玻璃化轉變溫度的標準測試方法
可在各種環境條件下進行
關鍵考慮因素
濕熱老化:
結合潮濕和溫度暴露
監測機械性能隨時間的變化
壓力環境暴露:
在環境調節期間施加恒定負載
評估環境暴露下的蠕變行為
惡劣環境下的疲勞:
在環境室中進行疲勞測試
評估循環載荷和環境因素的協同效應
紫外線照射:
使用風化室模擬戶外暴露
對于外部應用中使用的復合材料尤為重要
耐化學性:
將標本暴露于相關化學品(例如燃料、液壓油)中
暴露后進行機械測試
測試矩陣示例
RT:室溫
數據分析和解釋
物業保留:
計算環境暴露后關鍵性能(強度、模量)的保留百分比
時間-溫度-應力疊加:
開發模型以預測高溫下短期測試的長期行為
失效模式分析:
檢查環境因素如何影響失效機制
統計分析:
使用實驗設計 (DOE) 高效探索多種環境因素
開發各種條件下屬性變化的預測模型
微觀結構分析:
使用 SEM 或 micro-CT 等技術將環境影響與微觀結構變化相關聯
了解環境對機械性能的影響對于以下方面至關重要:
復合材料結構的準確壽命預測
針對特定環境條件的材料選擇
制定保護措施(例如涂料、密封劑)
在設計中建立適當的安全系數
通過在各種環境條件下全面測試復合材料,工程師可以確保復合材料結構在具有挑戰性的實際應用中的長期可靠性和性能。
第 7 章:復合材料的無損檢測 (NDT)
無損檢測 (NDT) 對于評估復合材料和結構的完整性而不造成損壞至關重要。這些技術對于制造、在役檢測和損壞評估過程中的質量控制至關重要。本章重點介紹復合材料的關鍵無損檢測方法:超聲檢測、熱成像和 X 射線計算機斷層掃描。
超聲波檢測
超聲檢測是復合材料使用最廣泛的無損檢測方法之一,因為它在檢測內部缺陷方面具有多功能性和有效性。
原則
高頻聲波(通常為 1-50 MHz)通過材料傳輸
分析來自缺陷或界面的反射
方法
脈沖回波
通過返回到傳感器的反射檢測到缺陷
直通式
在材料相對的兩側分離發射器和接收器
通過衰減或飛行時間變化檢測到的缺陷
相控陣
多晶傳感器
允許光束控制和聚焦,以改善檢測和成像
應用
分層檢測
孔隙度評估
厚度測量
異物檢測
優勢
對內部缺陷高度敏感
可以檢查較厚的層壓板
能夠提供深度信息
局限性
需要偶聯介質(通常為水或凝膠)
難以處理高衰減性或異質性材料
復雜的幾何形狀可能具有挑戰性
熱成像技術
熱成像技術使用紅外相機檢測材料表面的溫差,從而指示近表面缺陷。
原則
缺陷會影響材料中的熱流
表面的溫差表明地下異常
方法
被動熱成像
觀察自然溫差
適用于在役檢測(例如,檢測熱點)
主動熱成像
施加外部熱源(例如,閃光燈、熱風槍)
觀察熱響應隨時間的變化
鎖相熱成像
定期加熱
分析熱波的相位和振幅
應用
撞擊損害評估
分層檢測
進水檢測
粘接質量評估
優勢
快速、大面積檢測
非接觸式方式
對近表面缺陷有效
局限性
深度穿透有限
對表面條件敏感
需要仔細解釋熱圖像
X 射線計算機斷層掃描 (CT)
X 射線 CT 提供復合材料內部結構的詳細 3D 圖像,從而可以進行全面的缺陷分析。
原則
X 射線穿過材料,并因各種特征而以不同的方式衰減
將多個 2D X 射線圖像重建為一個 3D 體積
方法
工業 CT
用于大型或致密部件的高功率 X 射線源
高分辨率,便于詳細分析
顯微 CT
對于小樣品具有極高的分辨率
可用于微觀結構分析
原位 CT
將 CT 掃描與機械測試相結合
實時觀察傷害進展
應用
纖維取向分析
空隙含量測量
撞擊損害評估
復雜零件的質量控制
優勢
提供詳細的 3D 信息
可以檢測多種類型的缺陷
非破壞性橫截面
局限性
樣品量有限(尤其是高分辨率掃描)
采集和重建時間長
昂貴的設備
輻射安全問題
復合材料的其他無損檢測方法
聲發射
檢測由生長缺陷釋放的應力波
有助于在加載過程中進行實時監控
剪切圖
使用激光干涉測量法檢測表面變形
有效發現脫粘和分層
放射線照相術
使用 X 射線或伽馬射線進行 2D 成像
適用于檢測密度變化和異物
渦流檢測
僅限于導電復合材料(例如碳纖維)
適用于表面和近表面缺陷
激光超聲
非接觸式超聲波法
適用于復雜幾何形狀和高溫應用
選擇合適的 NDT 方法
需要考慮的因素:
要檢測的缺陷類型
材料特性(例如,纖維類型、疊層)
組件幾何形狀和尺寸
所需的分辨率和靈敏度
檢測速度和成本
可訪問性(在役與制造)
無損檢測 (NDT) 集成到復合材料制造和服務中
進程內監控
嵌入傳感器(例如光纖)用于實時固化監測
用于自動化制造過程的在線熱成像
質量管理
大型部件的自動超聲掃描
關鍵或復雜部件的 CT 掃描
在役檢查
用于現場檢測的便攜式無損檢測設備
用于持續監測的結構健康監測 (SHM) 系統
數據集成和分析
用于自動缺陷檢測的機器學習
整合 NDT 數據進行生命周期管理的數字孿生
挑戰和未來趨勢
自動化和機器人技術
用于復雜幾何形狀的自動掃描系統
基于無人機的大型結構檢查
數據融合
結合多種無損檢測技術進行全面評估
將 NDT 數據與結構分析和預測相結合
高級信號處理
通過高級算法提高分辨率和靈敏度
新技術
非導電復合材料的太赫茲成像
量子傳感,提高靈敏度
無損檢測是確保復合材料和結構的質量和可靠性的關鍵方面。通過采用無損檢測方法并緊跟技術進步,工程師和檢測員可以有效地檢測和表征缺陷,確保復合材料部件在其整個生命周期內的安全和性能。
第 8 章:數據分析、解釋和質量控制
適當的數據分析、解釋和質量控制對于從復合材料的機械測試中提取有意義的信息至關重要。本章介紹復合屬性的統計分析技術、失效模式識別、屬性預測和建模、相關標準和數據庫。
測試結果的統計分析
統計分析對于了解復合材料固有的可變性和對其特性進行可靠預測至關重要。
基本統計度量
均值 (Average)
計算方法是所有值之和除以觀測值個數
提供數據的集中趨勢
標準差
測量數據圍繞平均值的分布
計算為方差的平方根
變異系數 (CV)
標準差與平均值的比率,以百分比表示
可用于比較不同屬性或材料之間的差異
高級統計技術
方差分析 (ANOVA)
用于確定不同組的均值之間是否存在統計學顯著差異
有助于評估各種因素(例如纖維取向、制造工藝)對性能的影響
Weibull 分析
通常用于復合材料的強度數據
提供有關不同應力水平下失效概率的信息
實驗設計 (DOE)
確定影響過程的因素與該過程的輸出之間關系的系統方法
有助于優化材料成分或加工參數
處理異常值
鑒定
使用統計檢驗(例如,Grubbs 檢驗、Dixon Q 檢驗)來識別潛在的異常值
治療
調查異常值的原因(例如,制造缺陷、測試錯誤)
包含或排除的決定應基于工程判斷并記錄在案
報告結果
報告均值和標準差
包括測試的樣本數量
在適當的情況下提供置信區間
根據測量精度使用適當的有效數字
故障模式識別
了解失效模式對于改進材料設計和預測長期性能至關重要。
復合材料中的常見失效模式
纖維斷裂
通常發生在拉伸載荷下
其特征是垂直于纖維方向的干凈斷開
基體開裂
通常是首先發生的損害
如果不阻止,可能會導致其他故障模式
分層
相鄰層的分離
通常由層間應力或沖擊引起
光纖拉出
纖維從基質中拉出
表示光纖矩陣接口較弱
屈曲
常見于壓縮測試
可以是整體(整個樣本)或局部(單根纖維)
鑒定技術
目視檢查
故障模式的初步評估
可以通過放大進行增強
顯微術
用于表面分析的光學顯微鏡
掃描電子顯微鏡 (SEM) 用于詳細檢查斷裂表面
X 射線 CT 掃描
內部損傷的無損 3D 可視化
聲發射
在測試期間實時監控損壞進展
與測試數據的關聯
將觀察到的失效模式與應力-應變曲線中的特征聯系起來
使用失效模式信息來驗證或優化分析模型
屬性預測和建模
預測建模對于復合材料結構的設計和優化至關重要。
微機械模型
混合物規則
用于預測縱向特性的簡單模型
E1 = Ef * Vf + Em * (1-Vf),其中 E 是模量,V 是體積分數,f 是纖維,m 是基體
Halpin-Tsai 方程
更精確地實現橫向和剪切特性
考慮纖維幾何形狀和保壓
層壓板理論
經典層壓板理論 (CLT)
預測多向層壓板的行為
基于單個層屬性和堆垛順序
第一層失效理論
最大應力、最大應變、Tsai-Wu、Tsai-Hill 準則
預測層壓板的損壞開始
有限元分析 (FEA)
線性分析
預測應力分布和變形
適用于初始設計階段
漸進式故障分析
模擬損傷累積和傳播
需要高級材料模型和失效準則
機器學習方法
可以根據成分和加工參數預測特性
需要大型數據集進行訓練
高斯過程回歸
提供概率預測
可用于不確定性量化
ASTM、ISO 和其他相關標準概述
標準可確保不同實驗室和組織之間測試結果的一致性和可比性。
ASTM 標準
ASTM D3039:聚合物基復合材料的拉伸性能
ASTM D3410:聚合物基復合材料的壓縮性能
ASTM D3518:聚合物基復合材料的面內剪切響應
ASTM D7264:聚合物基復合材料的彎曲性能
ASTM D2344:聚合物基復合材料的短梁強度
ISO 標準
ISO 527:拉伸性能的測定
ISO 14126:面內方向壓縮性能的測定
ISO 14129:面內剪切應力/剪切應變響應的測定
ISO 14125:彎曲性能的測定
其他相關標準
SACMA(先進復合材料供應商協會)推薦方法
EN (European Norm) 標準
JIS(日本工業標準)
標準的關鍵方面
試樣幾何形狀和制備
測試設置和過程
數據分析和報告要求
質量控制措施
復合材料機械性能數據庫
數據庫是材料選擇、設計和研究的寶貴資源。
數據庫類型
公共數據庫
NIST Composites Data (英文)
CMH-17 (復合材料手冊)
ESDU (工程科學數據單元)
專有數據庫
由材料供應商或大型 OEM 維護
通常需要許可或合作協議
研究數據庫
由大學或研究機構編制
可能側重于特定類型的復合材料或特性
通常包含的信息
材料成分(纖維類型、基質、纖維體積分數)
加工方法
機械性能(強度、模量、泊松比)
物理特性(密度、熱膨脹系數)
環境數據(吸濕性、溫度影響)
統計信息(平均值、標準差、標本數量)
數據庫的利用率
材料選擇
比較特定應用的不同材料的特性
設計允許
根據數據庫條目的統計分析確定設計值
模型驗證
使用數據庫值驗證預測模型
識別研究差距
確定需要更多數據的區域
挑戰和注意事項
確保數據質量和可追溯性
標準化數據格式以實現互操作性
使用新材料和測試方法使數據庫保持最新狀態
平衡開放獲取與專有信息
有效的數據分析、解釋和質量控制對于最大限度地提高復合材料機械測試的價值至關重要。通過采用嚴格的統計技術、了解失效模式、利用預測模型、遵守既定標準以及利用全面的數據庫,工程師和研究人員可以在復合材料的設計、制造和應用方面做出明智的決策。
第 9 章:復合材料測試中的高級主題
隨著復合材料和制造技術的發展,表征這些先進材料所需的測試方法也在不斷發展。本章重點介紹夾層結構、3D 編織復合材料和連續纖維 3D 打印復合材料的測試方法。
夾層結構測試
夾層結構由兩塊薄而堅硬的面板組成,粘合到一個輕質芯上,由于其高剛度重量比而廣泛用于航空航天、船舶和風能應用。
主要測試方法
彎曲測試
ASTM C393:梁彎曲法測定夾層結構核心剪切性能的標準測試方法
確定端面彎曲強度、型芯剪切強度和面板彎曲剛度
平面拉伸試驗
ASTM C297:夾層結構平面拉伸強度的標準測試方法
評估面板和芯材之間的粘合強度
Edgewise 壓縮測試
ASTM C364:夾層結構邊緣抗壓強度的標準測試方法
評估整個夾層結構的抗壓強度
型芯剪切測試
ASTM C273:夾芯材料剪切性能的標準測試方法
確定芯材的剪切強度和模量
沖擊測試
ASTM D7766:夾層結構抗損傷測試的標準實踐
評估夾層結構對沖擊事件的抗損傷性
特別注意事項
尺寸影響:由于夾層結構的異質性,試樣尺寸會顯著影響結果
失效模式:可能會出現多種失效模式(例如,面板失效、型芯剪切、壓痕),需要仔細解釋
環境影響:濕度和溫度會極大地影響核心特性,因此需要進行環境測試
3D 編織復合材料的測試
與傳統的層壓復合材料相比,3D 機織復合材料具有更好的全厚度性能和損傷容限。
主要測試方法
拉伸測試
修改后的 ASTM D3039 程序
由于 3D 加固的規模,需要更大的試樣
壓縮測試
適用 ASTM D6641(組合載荷壓縮)
特別注意復雜光纖結構引起的末端效應
層間剪切強度
改良短梁剪切試驗 (ASTM D2344)
3D 光纖架構使解釋復雜化
Fracture Toughness
模式 I:雙懸臂梁 (DCB) 測試 (ASTM D5528)
模式 II:端部切口彎曲 (ENF) 測試
需要仔細考慮裂紋在 3D 結構中的擴展
沖擊測試
低速沖擊 (ASTM D7136)
沖擊后壓縮 (CAI) 測試 (ASTM D7137)
特別注意事項
光纖結構表征:Micro-CT 掃描以驗證 3D 光纖排列
縮放效果:代表性體積元素可能比傳統復合體大
各向異性:由于復雜的光纖結構,特性在不同方向上可能會發生顯著變化
失效模式分析:復雜的失效模式需要先進的成像技術進行解釋
連續纖維 3D 打印復合材料的測試
連續纖維 3D 打印是一項新興技術,可在部件內實現復雜、定制的纖維取向。
主要測試方法
拉伸測試
適用 ASTM D3039
特別考慮打印方向和纖維取向
彎曲測試
修改后的 ASTM D7264
注意層接口和光纖連續性
層間剪切強度
短梁剪切試驗 (ASTM D2344)
評估層粘合質量的關鍵
壓縮測試
適用 ASTM D6641
對于評估纖維排列和基質特性非常重要
疲勞測試
修改后的 ASTM D3479
對于了解打印部件的長期性能至關重要
特別注意事項
各向異性:特性可能會因打印方向和纖維放置策略而有很大差異
空隙含量:與傳統制造方法相比,3D 打印工藝可能會引入更多的空隙
纖維-矩陣接口:打印過程中的浸漬質量會影響機械性能
殘余應力:打印過程中的熱梯度會引入殘余應力
表面光潔度:可能影響測試結果,尤其是在疲勞測試中
新興的測試方法
原位測試
在打印過程中實時監控機械性能
利用嵌入式傳感器或無損檢測技術
多材料測試
表征多材料打印件中不同材料之間的界面
需要制定新的測試標準
功能分級材料測試
評估成分或纖維取向不斷變化的零件的性能
需要新的數據分析和解釋方法
高級復合材料檢測的常見挑戰
試樣制備
復雜的幾何形狀和加固結構會使試樣制備變得具有挑戰性
確保樣本的一致性和代表性至關重要
數據解釋
高級復合材料通常表現出復雜的失效模式
需要復雜的分析技術和通常的多尺度建模
標準化
許多高級復合材料形式缺乏既定的測試標準
研究人員通常需要調整現有標準或開發新方法
屬性可變性
先進的制造技術可以引入新的可變性來源
需要穩健的統計分析和可能更大的樣本量
縮放效果
在小型試樣上測得的特性可能無法準確反映全尺寸組件的行為
需要仔細考慮縮放規則并通過組件級測試進行驗證
高級復合材料檢測的未來趨勢
數字孿生集成
將物理測試與實時仿真相結合,以改進預測和優化
機器學習應用程序
使用 AI 預測屬性、優化測試計劃和解釋復雜數據集
高通量測試
開發快速測試方法以跟上加快的材料開發周期
多尺度測試
整合納米、微觀和宏尺度測試,全面了解材料行為
原位和在線監測
開發在制造和使用過程中進行實時特性測量的技術
先進的復合材料檢測帶來了獨特的挑戰,但也帶來了創新的機會。隨著材料和制造技術的不斷發展,測試方法必須進行調整,以便為這些先進材料的設計、質量控制和認證提供準確、可靠的數據。
第 10 章 未來趨勢和工業應用
隨著復合材料的不斷發展和新的應用,測試和分析這些材料的方法也在不斷進步。本章探討了復合材料測試的未來趨勢,重點關注自動化和人工智能,并研究了關鍵工業領域的案例研究。
測試自動化
自動化正在徹底改變復合材料測試,提高效率、可重復性和數據質量。
自動化的關鍵領域
試樣制備
自動切割和加工系統
機器人處理和定位試樣
測試執行
測試機器的自動裝卸
用于無損檢測的機器人系統(例如,自動超聲掃描)
數據采集
高速數據采集系統
集成多種傳感器類型(負載、應變、聲發射等)
環境控制
自動調節室
測試過程中精確控制溫度和濕度
新興技術
機器人測試單元
適用于多種試樣類型的全自動測試執行
將各種測試方法集成到單個單元中
原位過程監測
實時監控制造過程
生產過程中的自動化質量控制
數字主線實施
從制造到測試和分析的樣本跟蹤
確保數據完整性和可追溯性
用于遠程監測和控制的互聯測試設備
實時數據共享和分析
優勢和挑戰
好處:
提高吞吐量和效率
提高可重復性并減少人為錯誤
增強的數據質量和一致性
挑戰:
初期投資成本高
需要專門的維護和校準
測試程序可能失去靈活性
數據分析中的機器學習和 AI
人工智能 (AI) 和機器學習 (ML) 正在改變復合測試數據的分析和解釋方式。
AI/ML 在復合材料測試中的應用
自動缺陷檢測
用于識別無損檢測圖像中缺陷的機器學習算法
制造過程中的實時質量評估
屬性預測
用于根據成分和加工參數預測機械性能的神經網絡
減少對大量物理測試的需求
故障模式分類
用于故障模式分類的 AI 驅動的圖像分析
斷裂表面的自動測試后分析
測試參數優化
用于優化測試條件和樣本量的機器學習算法
基于實時數據分析的自適應測試程序
數據挖掘和模式識別
從歷史測試結果的大型數據集中提取見解
識別制造參數和材料特性之間的相關性
高級 AI/ML 技術
深度學習
卷積神經網絡 (CNN) 用于基于圖像的缺陷檢測
用于疲勞測試中時間序列數據分析的遞歸神經網絡 (RNN)
生成對抗網絡 (GAN)
生成綜合測試數據以增強有限的物理測試結果
創建復合結構的數字孿生
強化學習
優化測試程序和制造流程
自動化測試系統的自適應控制
自然語言處理 (NLP)
測試報告和研究論文的自動分析
從非結構化數據源中提取知識
挑戰和注意事項
數據質量和數量:ML 模型需要大型、高質量的數據集進行訓練
可解釋性:確保可以解釋和驗證 AI/ML 決策
與現有系統集成:與當前數據管理和分析工具兼容
道德考慮:解決數據集和算法中的偏見
工業應用案例研究
研究高級復合材料檢測在關鍵行業的實際應用,可以深入了解當前的實踐和未來的方向。
航空航天工業
案例研究:下一代飛機機翼
挑戰:開發和認證一種性能更高、重量更輕的復合材料機翼結構
測試方法:
從試樣到全尺寸組件的多尺度測試
使用機器人系統對大型部件進行自動無損檢測
用于預測長期疲勞表現的 AI 驅動的數據分析
成果:
與上一代產品相比,重量減輕 20%
提高損傷容忍度和疲勞壽命
通過虛擬測試和 AI 輔助數據解釋縮短認證時間
汽車工業
案例研究:電動汽車電池外殼
挑戰:為電動汽車設計輕質、防撞的復合電池外殼
測試方法:
使用自動化測試單元進行高通量沖擊測試
用于優化纖維取向的機器學習算法
對制造過程進行現場監控,以確保質量始終如一
成果:
與金屬替代品相比,重量減輕 30%
改善碰撞能量吸收
通過 AI 輔助設計優化縮短開發時間
風能行業
案例研究:下一代風力渦輪機葉片
挑戰:為海上應用開發更長、更耐用的風力渦輪機葉片
測試方法:
葉片截面的自動全尺寸疲勞測試
AI 驅動的結構健康監測系統
用于預測維護需求的數字孿生集成
成果:
刀片長度增加 25%,重量不成比例增加
提高疲勞壽命并降低維護要求
通過對運營數據進行 AI 分析,增強預測性維護功能
未來展望
復合材料測試的未來可能會看到:
提高物理和虛擬測試的集成度
將物理測試與實時仿真相結合的混合測試方法
通過經過驗證的虛擬模型減少對大量物理測試的依賴
高級傳感器和無損評估
開發用于實時監測復合材料結構的嵌入式傳感器
用于評估復雜 3D 打印或編織復合材料的新型無損檢測技術
可持續發展重點
回收和生物基復合材料的測試方法
將生命周期評估集成到材料測試和選擇流程中
多功能復合材料
具有集成傳感、自愈或能量收集功能的復合材料測試協議
評估非傳統復合材料性能的新標準
人工智能的進步
能夠自主規劃和執行測試的 AI 系統
持續學習算法,每次執行測試都會得到改進
復合材料測試的未來特點是自動化程度的提高、智能數據分析以及材料表征和結構性能的整體方法。隨著復合材料不斷突破材料性能的界限,測試方法將不斷發展以應對這些新挑戰,從而能夠在各個行業開發更安全、更高效、更可持續的復合材料結構。
-
測試
+關注
關注
8文章
5578瀏覽量
128131 -
復合材料
+關注
關注
2文章
245瀏覽量
13364
原文標題:【復合材料前沿】復合材料的機械性能測試詳解
文章出處:【微信號:深圳市賽姆烯金科技有限公司,微信公眾號:深圳市賽姆烯金科技有限公司】歡迎添加關注!文章轉載請注明出處。
發布評論請先 登錄
中國智能手機復合材料后蓋搭載量快速增長
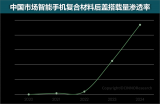
ATA-2031高壓放大器在復合材料板超聲無損探傷中的應用
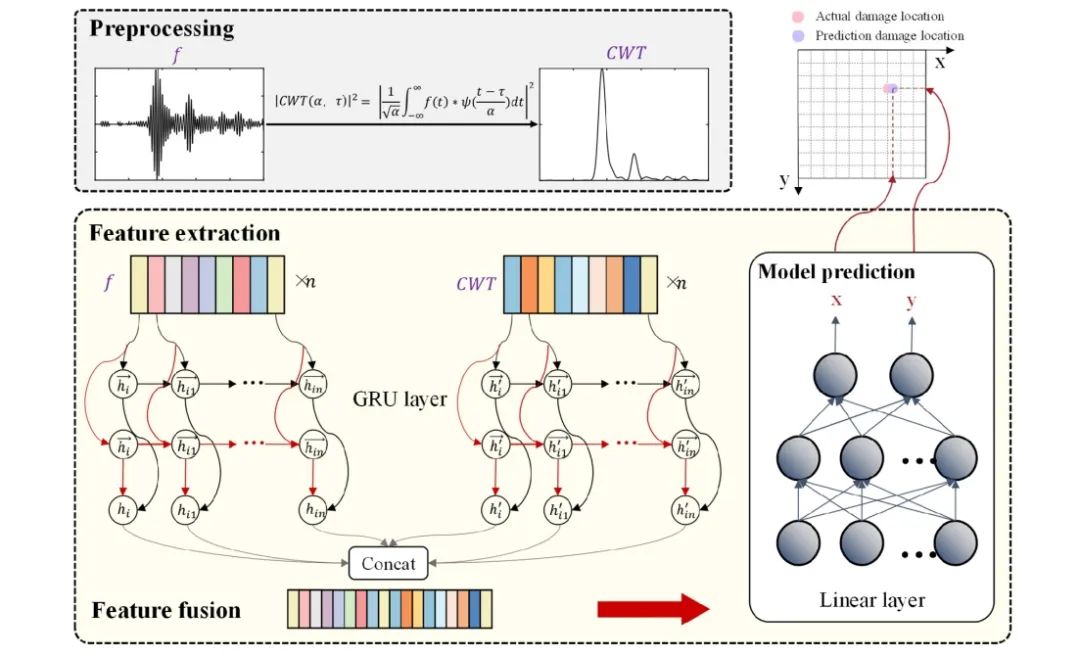
6分鐘看懂碳纖維增強聚合物復合材料界面研究方法
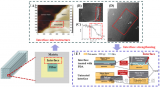
復合材料基礎知識及對制造和工程領域的變革性影響
可破損復合材料結構的建模與表征
探討金剛石增強復合材料:金剛石/銅、金剛石/鎂和金剛石/鋁復合材料
粉末涂料在復合材料部件上的應用
石墨烯化學鍍銅對放電等離子燒結石墨烯增強鋁基復合材料組織和性能的影響
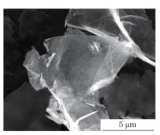
碳/碳復合材料的優點有哪些
焊點的微觀結構與機械性能
高絕緣散熱材料 | 石墨片氮化硼散熱膜復合材料
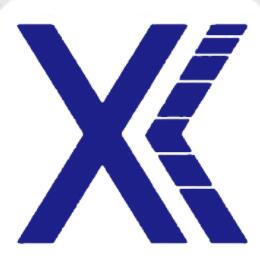
射頻功率放大器在紡織復合材料研究中的應用
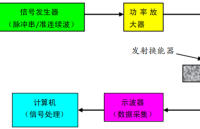
搪瓷釜脫瓷嚴重漏介質,用高分子復合材料輕松修補
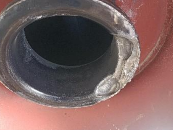
評論