文章來源:晶格半導(dǎo)體
原文作者:晶格半導(dǎo)體
本文主要介紹晶圓的劃片工藝流程
在半導(dǎo)體制造的復(fù)雜流程中,晶圓歷經(jīng)前道工序完成芯片制備后,劃片工藝成為將芯片從晶圓上分離的關(guān)鍵環(huán)節(jié),為后續(xù)封裝奠定基礎(chǔ)。由于不同厚度的晶圓具有各異的物理特性,因此需匹配不同的切割工藝,以確保切割效果與芯片質(zhì)量。
一、基于晶圓厚度的切割工藝選擇
1、厚度 100um 以上的晶圓 - 刀片切割
對于厚度超過 100um 的晶圓,刀片切割(Blade dicing or blade sawing)是常用的方法。這種方法在長期的實(shí)踐中展現(xiàn)出高效切割大量晶圓的能力,能夠滿足大規(guī)模生產(chǎn)的需求。在刀片切割過程中,諸多細(xì)節(jié)關(guān)乎切割質(zhì)量。為保護(hù)晶圓免受外部損傷,需事先在晶圓上貼敷膠膜。與 “背面減薄” 過程中膠膜貼在晶圓正面不同,刀片切割時膠膜要貼在晶圓背面,而在后續(xù)的共晶貼片(Die Bonding)過程中,這層貼在背面的膠膜會自動脫落。切割時,因刀片與晶圓間摩擦劇烈,需從各個方向連續(xù)噴灑 DI 水(去離子水),以降低摩擦產(chǎn)生的熱量并沖走切割碎屑。
同時,為實(shí)現(xiàn)更好的切片效果,葉輪上會附有金剛石顆粒。值得注意的是,切口(即刀片厚度與凹槽寬度)必須均勻,且不得超過劃片槽的寬度,以保證切割精度。然而,刀片切割并非毫無挑戰(zhàn)。若切片的進(jìn)給速度大幅提高,小芯片邊緣剝落的風(fēng)險將顯著增加。因此,通常需將葉輪的旋轉(zhuǎn)次數(shù)控制在每分鐘 30000 次左右,以平衡切割效率與切割質(zhì)量。此外,在切割較窄跡道(street)寬度的晶圓時,對設(shè)備精度要求極高。需要使用具有高分度軸精度、高光學(xué)放大和先進(jìn)對準(zhǔn)運(yùn)算的設(shè)備,以確保每次切割都能精確落在跡道中心幾微米范圍內(nèi)。而且,選擇刀片厚度也需謹(jǐn)慎權(quán)衡。雖窄跡道切割應(yīng)盡量選用最薄的刀片,但很薄的刀片(如 20μm)極為脆弱,容易過早破裂和磨損,導(dǎo)致其壽命期望和工藝穩(wěn)定性較厚刀片差。對于 50 - 76μm 跡道的刀片,推薦厚度為 20 - 30μm。
2、厚度不到 100um 的晶圓 - 激光切割
當(dāng)晶圓厚度不足 100um 時,激光切割成為更為適宜的選擇。激光切割利用高能量密度的激光束瞬間熔化或氣化被切割材料,從而實(shí)現(xiàn)晶圓的分離。這種方法的顯著優(yōu)勢在于能夠有效減少剝落和裂紋問題,尤其適用于對芯片邊緣質(zhì)量要求較高的場景。然而,激光切割在處理 100um 以上厚度的晶圓時,生產(chǎn)效率會大大降低,這限制了其在厚晶圓切割中的應(yīng)用。
3、厚度不到 30um 的晶圓 - 等離子切割
對于厚度小于 30um 的超薄晶圓,等離子切割展現(xiàn)出獨(dú)特的優(yōu)勢。等離子切割通過高溫、高速的等離子體射流將材料熔化并吹離,實(shí)現(xiàn)切割目的。該工藝速度快,且不會對晶圓表面造成損傷,能夠有效提高良率。但等離子切割工藝過程更為復(fù)雜,對設(shè)備和操作要求較高,需要專業(yè)的技術(shù)人員和精密的設(shè)備來確保切割的準(zhǔn)確性和穩(wěn)定性。
二、刀片切割工藝的關(guān)鍵要點(diǎn)
碎片問題及控制頂面碎片(TSC, top - side chipping):頂面碎片發(fā)生在晶圓的頂面,當(dāng)切片接近芯片的有源區(qū)域時,這一問題可能影響芯片合格率。其產(chǎn)生主要與刀片磨砂粒度、冷卻劑流量和進(jìn)給速度相關(guān)。合適的刀片磨砂粒度能夠確保切割的平滑性,避免對芯片表面造成過度損傷;穩(wěn)定的冷卻劑流量可以有效降低切割過程中的溫度,減少因熱應(yīng)力導(dǎo)致的碎片產(chǎn)生;而合理控制進(jìn)給速度則能保證切割的穩(wěn)定性,防止因過快或過慢的進(jìn)給導(dǎo)致芯片表面出現(xiàn)碎片。
背面碎片(BSC, back - side chipping):背面碎片出現(xiàn)在晶圓的底面,當(dāng)大的、不規(guī)則微小裂紋從切割的底面擴(kuò)散并匯合時,就可能引發(fā)這一問題。當(dāng)這些微小裂紋足夠長,導(dǎo)致不可接受的大顆粒從切口除掉時,BSC 便成為影響合格率的關(guān)鍵因素。一般而言,如果背面碎片的尺寸在 10μm 以下,可忽略不計(jì);當(dāng)尺寸大于 25μm 時,可看作潛在受損;不過,50μm 的平均大小在一定程度上可接受,具體還需視晶圓的厚度而定。為應(yīng)對這些挑戰(zhàn),切片系統(tǒng)與刀片之間的協(xié)作至關(guān)重要,特別是在高端應(yīng)用中。刀片的特性,如金剛石(磨料)尺寸、金剛石含量和粘結(jié)劑的類型,對切割質(zhì)量起著決定性作用。結(jié)合物作為分布有金剛石磨料的基體,其成分和結(jié)構(gòu)會影響刀片的性能。此外,進(jìn)給率和心軸速度等因素也會影響刀片的選擇。理解這些關(guān)鍵參數(shù)之間的關(guān)系,是為特定應(yīng)用選擇最合適刀片的必要前提。
刀片負(fù)載監(jiān)測(Blade Load Monitering)在切片或其他磨削過程中,新一代的切片系統(tǒng)能夠自動監(jiān)測施加在刀片上的負(fù)載或扭矩,確保在不超出可接受的切削質(zhì)量參數(shù)范圍內(nèi)進(jìn)行切割。對于每一套工藝參數(shù),都存在一個切片質(zhì)量下降和 BSC 出現(xiàn)的極限扭矩值。通過監(jiān)測切削質(zhì)量與刀片基板相互作用力的關(guān)系,并測量相關(guān)變量,可以及時發(fā)現(xiàn)工藝偏差和損傷的形成。進(jìn)而實(shí)時調(diào)整工藝參數(shù),使扭矩不超過極限值,同時獲得最大的進(jìn)給速度,實(shí)現(xiàn)高效、高質(zhì)量的切割。切片工序的關(guān)鍵環(huán)節(jié)之一是切割刀片的修整(dressing)。在非監(jiān)測的切片系統(tǒng)中,修整工序往往通過反復(fù)試驗(yàn)來確定。而在刀片負(fù)載受監(jiān)測的系統(tǒng)中,修整的終點(diǎn)可通過測量的力量數(shù)據(jù)來精準(zhǔn)判斷,從而建立最佳的修整程序。這種方法具有顯著優(yōu)勢,既無需限時保證最佳刀片性能,又能避免因使用部分修整的刀片切片而導(dǎo)致的合格率損失。
冷卻劑流量穩(wěn)定(Coolant Flow Stabilization)以穩(wěn)定的扭矩運(yùn)轉(zhuǎn)的切片系統(tǒng),要求進(jìn)給率、心軸速度和冷卻劑流量保持穩(wěn)定。冷卻劑在刀片上施加的阻力會造成扭力,因此,最新一代的切片系統(tǒng)通過精確控制冷卻劑流量,來維持穩(wěn)定的流速和阻力,進(jìn)而保持冷卻劑扭矩影響的穩(wěn)定性。當(dāng)切片機(jī)的冷卻劑流量穩(wěn)定且其他參數(shù)均受控制時,能夠維持一個穩(wěn)定的扭矩。若記錄到扭矩偏離穩(wěn)定值,可能是由于噴嘴堵塞導(dǎo)致冷卻劑流量變化、噴嘴調(diào)整不當(dāng)、刀片個體差異、刀片磨損情況或操作員錯誤等不受控因素引起。及時排查和解決這些問題,對于確保切割質(zhì)量和工藝穩(wěn)定性至關(guān)重要。
-
半導(dǎo)體
+關(guān)注
關(guān)注
335文章
28918瀏覽量
237946 -
晶圓
+關(guān)注
關(guān)注
53文章
5165瀏覽量
129795 -
工藝流程
+關(guān)注
關(guān)注
7文章
112瀏覽量
16575
原文標(biāo)題:晶圓的劃片工藝流程
文章出處:【微信號:bdtdsj,微信公眾號:中科院半導(dǎo)體所】歡迎添加關(guān)注!文章轉(zhuǎn)載請注明出處。
發(fā)布評論請先 登錄
晶圓級CSP的裝配工藝流程
半導(dǎo)體晶圓制造工藝流程
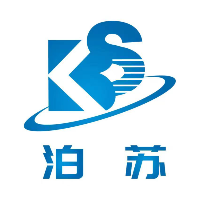
晶圓濕法清洗工作臺工藝流程
晶圓蝕刻擴(kuò)散工藝流程
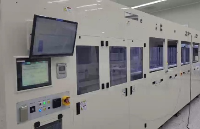
評論