文章來源:學習那些事
原文作者:前路漫漫
本文介紹了芯片封裝失效的典型現象:金線偏移、芯片開裂、界面開裂、基板裂紋和再流焊缺陷。
金線偏移
在封裝過程中,金線偏移是較為常見的失效類型。對于 IC 元器件而言,金線偏移量過大可能致使相鄰金線相互接觸,進而引發短路故障;極端情況下,金線甚至會被沖斷,造成斷路,使元器件出現缺陷。引發金線偏移的原因復雜多樣,具體如下:
樹脂流動拖曳力:在填充階段,若樹脂黏性過高、流速過快,產生的拖曳力會作用于金線,導致其偏移量增大,這是金線偏移失效的常見誘因 。
導線架變形:上下模穴中樹脂流動波前失衡,會在模流間形成壓力差。導線架受此壓力差產生彎矩發生變形,由于金線連接于導線架的芯片焊墊與內引腳,導線架變形便會引發金線偏移。
氣泡移動影響:填充過程中,空氣進入模穴形成小氣泡,氣泡在模穴內移動時碰撞金線,也會造成金線一定程度的偏移。
保壓異常:過保壓會使模穴內壓力過高,導致偏移的金線無法彈性恢復;遲滯保壓則會引起溫度上升,對于添加催化劑后反應活躍的樹脂,高溫使其黏性進一步增加,同樣阻礙金線恢復原狀。
填充物碰撞:封裝材料中添加的填充物,若顆粒尺寸較大(如 2.5 - 250μm),在封裝過程中與精細的金線(如 25μm)碰撞,也可能致使金線偏移 。
此外,隨著多引腳集成電路的發展,封裝內金線數量與引腳數目不斷增加,金線密度隨之提升,這也使得金線偏移現象更為顯著。為有效減少金線偏移,防范短路或斷路問題,封裝工程師需審慎選擇封裝材料,精準調控工藝參數,降低模穴內金線所受應力,避免出現過大的偏移量。
芯片開裂
IC 裸芯片的制造原料通常為單晶硅,這種材料雖具備高強度,卻因脆性大的特性,在遭受外力作用或表面存在瑕疵時,極容易出現破裂情況。在晶圓減薄、晶圓切割、芯片貼裝和引線鍵合等一系列需要施加應力的工藝操作過程中,芯片開裂的風險大幅增加,這一問題已成為致使 IC 封裝失效的重要因素之一。若芯片裂紋未蔓延至引線區域,通過常規手段很難發現;更有部分存在裂紋的芯片,在常規工藝檢查與電學性能檢測時,其性能表現與正常芯片并無明顯差異,使得裂紋問題極易被忽略。然而,這些隱藏的裂紋會對封裝后器件的穩定性與使用壽命造成嚴重威脅。由于常規電學性能測試無法有效識別芯片開裂,因此需要借助高低溫熱循環實驗進行檢測。該實驗利用不同材料熱膨脹系數的差異,在加熱和冷卻交替過程中,材料間產生的熱應力會促使裂紋逐步擴展,直至芯片徹底破裂,最終在電學性能上呈現出異常狀態。
鑒于外部應力是引發芯片開裂的主因,一旦檢測到芯片存在裂紋,就必須立即對芯片封裝的工藝流程和參數進行優化,最大程度減少工藝環節對芯片產生的應力影響。例如,在晶圓減薄工序中,采用更為精細的加工方式,提高芯片表面的平整度,以此消除潛在應力;晶圓切割時,運用激光切割技術替代傳統方法,降低切割過程對芯片表面造成的應力損傷;在引線鍵合環節,精準調控鍵合溫度和壓力參數,確保鍵合過程平穩安全。
界面開裂
開裂問題不僅存在于芯片內部,在不同材料的交界位置同樣會出現,這種現象被稱為界面開裂。在界面開裂的初始階段,各部件之間的電氣連接尚能維持正常,但隨著使用時間的延長,熱應力的持續作用以及電化學腐蝕的影響,會導致界面開裂程度不斷加劇,最終破壞部件間的電氣連通性,對集成電路的可靠性產生嚴重影響。封裝過程中應力過大、封裝材料受到污染等工藝缺陷,是引發界面開裂的主要根源。界面開裂可能出現在金線與焊盤的連接部位,造成電路斷路故障;也可能發生在外部塑料封裝體中,降低封裝對芯片的防護性能,導致芯片受到污染。因此,必須采用專業的檢測方法對潛在的界面開裂問題進行全面排查,并根據檢測結果對工藝方案進行針對性調整 。
基板裂紋
在倒裝焊工藝里,通過焊球實現芯片與基板焊盤的電氣連接,而在此過程中,基板開裂是較為常見的失效模式,在引線鍵合環節同樣可能出現此類問題。基板一旦開裂,會嚴重干擾芯片正常的電學性能,引發斷路、高阻抗等故障,影響集成電路的整體功能。
基板開裂的成因較為復雜,一方面,芯片或基板本身若存在材料缺陷、內部應力集中等問題,會降低其結構強度;另一方面,焊接過程中的工藝參數匹配不當也是關鍵因素。例如,鍵合力過大、基板溫度控制不合理、超聲功率設置不精準等,都會使基板承受額外應力,進而導致裂紋產生 。
再流焊缺陷
晶圓翹曲
再流焊工藝容易引發晶圓翹曲問題。由于封裝體由多種材料構成,各材料熱膨脹系數存在差異,同時還受流動應力和黏著力影響,在封裝過程中外界溫度變化時,封裝體內部會產生內應力,而翹曲變形便是材料釋放內應力的一種表現形式,這種現象在再流焊接階段尤為突出。翹曲受多個工藝參數協同作用,通過針對性調整部分參數,能夠有效緩解或消除這一問題。
器件受力不均衡是導致翹曲的主要根源。在預熱階段,因材料熱膨脹系數不匹配、焊膏涂覆不均或器件放置偏差等原因,器件一端可能脫離焊膏,阻礙熱量正常傳導。當熱量經器件傳導時,一端先熔化的焊料會形成新月形,其表面張力產生的旋轉力矩大于器件自身重力,從而致使器件發生翹曲變形。
為改善晶圓翹曲狀況,可從多方面著手優化工藝:首先,要嚴格把控焊膏印刷與器件放置精度,規范設備操作流程,定期維護印刷和安裝設備,確保生產過程穩定;其次,重視印刷清晰度與精確度控制,這直接關系到襯墊配置,若控制不當會加劇器件兩端受力失衡,需定期檢查印刷配準參數,及時修正偏差,清潔印刷模板防止堵塞,同時保證焊膏濕度適宜,支撐基板平整堅固;最后,關注器件放置環節,定期校準進料器位置,精準控制放置對準,降低放置速度,合理選擇拾取工具噴嘴尺寸,并確保支撐平臺平穩可靠。
此外,焊接材料和印刷電路板特性也會對翹曲產生影響。焊接合金熔點時的表面張力大小,與翹曲時的扭曲力呈正相關,雖目前尚無統一的合金標準評估體系,但部分廠商嘗試使用 Sn/Pb/In 合金,發現對翹曲有一定抑制作用,但效果有限。不同類型焊膏的特性差異,會改變其對器件的作用效果,焊膏活性越強,越易引發翹曲;印刷電路板和器件表面的光潔度,會影響焊膏濕潤性能,過量使用焊膏會增加熔化時的應力,適當減少用量有助于降低翹曲風險。在再流焊過程中,若器件兩端熱傳遞速率差異顯著,也會因受力不均導致翹曲現象發生 。
錫珠
在再流焊工藝中,錫珠是一種常見的缺陷類型,多聚集于無引腳片式元器件兩側。若錫珠未與其他焊點相連,不僅會影響封裝外觀,還可能干擾產品電性能。錫珠產生的原因涵蓋多個方面,涉及模板設計、印刷操作、錫膏使用及工藝參數設置等環節。
從模板開口角度來看,若鋼網開口尺寸過大,或開口形狀與元器件、焊盤不匹配,在貼裝片式元器件時,焊膏易溢出焊盤范圍,進而形成錫珠。為規避此問題,片式阻容元器件的模板開口尺寸通常應略小于印制板焊盤。考慮到線路板刻蝕因素,一般將焊盤的模板開口設置為印制板焊盤尺寸的 90% - 95%,同時還需依據實際生產情況靈活選擇合適的開口形狀,以此減少焊膏過量擠出的風險。
模板與印刷電路板的精準對位及穩固固定同樣關鍵。對位偏差會致使焊膏蔓延至焊盤外,增加錫珠產生幾率。印刷錫膏的方式包括手工、半自動和全自動,即便在全自動印刷模式下,壓力、速度、間隙等參數仍依賴人工設定。因此,無論采用何種印刷方式,都需協調好機器、模板、印刷電路板和刮刀之間的關系,確保印刷質量穩定。在錫膏使用方面,從冷藏室取出的錫膏若升溫時間不足、攪拌不均勻,容易吸濕。在高溫再流焊過程中,錫膏內水汽揮發,就會形成錫珠。所以,使用前應將錫膏在室溫下放置約 4 小時恢復溫度,并充分攪拌均勻 。
溫度曲線作為再流焊工藝的核心參數,包含預熱、保溫、回流、冷卻四個階段。預熱和保溫環節能夠降低元器件與印刷電路板所受熱沖擊,促使錫膏中溶劑充分揮發。若預熱溫度不足或保溫時間過短,將直接影響焊接質量,通常建議保溫階段控制在 150 - 160℃、持續 70 - 90 秒。此外,生產中若需重新印刷錫膏,務必徹底清理殘留錫膏,防止其形成錫珠,清理時應避免錫膏流入插孔造成通孔堵塞 。
空洞
空洞也是再流焊的主要缺陷之一,表現為焊點表面或內部存在氣孔、針孔。其形成原因多樣:焊膏中金屬粉末含氧量過高、使用回收焊膏、工藝環境差混入雜質等,需嚴格把控焊膏質量;焊膏受潮吸收水汽,可通過控制環境溫度在 20 - 26℃、相對濕度 40% - 70%,且待焊膏達室溫后再開蓋使用來解決;元件焊端、引腳、印制電路板焊盤氧化污染或印制板受潮,應遵循元件先進先出原則,避免在潮濕環境存放并注意使用期限;升溫速率過快導致焊膏中溶劑和氣體未充分揮發,可將 160℃前的升溫速率控制在 1 - 2℃/s。
再流焊過程中還存在多種其他缺陷。例如,焊膏熔融不完全,表現為焊點周圍部分或全部焊膏未熔化;濕潤不良,即元件焊端、引腳或焊盤出現不沾錫或局部不沾錫現象;焊料量不足,焊點高度未達規定標準,影響焊點機械強度與電氣連接可靠性,甚至引發虛焊、斷路;橋連(短路),元件端頭、引腳或與鄰近導線間出現不應有的焊錫連接;錫點高度異常,焊料向焊端或引腳根部遷移,高度觸及或超過元件體;錫絲,元件焊端、引腳間或與通孔間存在細微錫絲;元件或端頭出現裂紋、缺損;元件端頭電極鍍層剝落;冷焊(焊錫紊亂),焊點表面有焊錫紊亂痕跡;焊點表面或內部出現裂縫等。還有一些肉眼難以察覺的缺陷,如焊點晶粒大小、內部應力、內部裂紋等,需借助 X 射線檢測、焊點疲勞測試等手段才能發現 。
-
晶圓
+關注
關注
53文章
5154瀏覽量
129717 -
芯片封裝
+關注
關注
11文章
577瀏覽量
31431
原文標題:芯片封裝失效典型現象
文章出處:【微信號:bdtdsj,微信公眾號:中科院半導體所】歡迎添加關注!文章轉載請注明出處。
發布評論請先 登錄
基于扇出型封裝結構的芯片失效位置定位方法
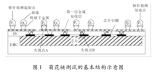
評論