在石油化工、冶金礦山、食品醫藥等工業領域,氣體泄漏是威脅生產安全與環境健康的隱形殺手。據應急管理部數據顯示,近五年全國化工行業重大事故中,因氣體泄漏引發的占比高達 68%。隨著《安全生產法》修訂實施及 “工業互聯網 + 安全生產” 行動計劃的推進,構建智能化、精準化的氣體泄漏檢測體系已成為企業實現安全發展的必由之路。
一、氣體泄漏檢測的行業特性與核心訴求
(一)檢測環境的復雜性與多樣性
工業場景中的氣體檢測環境差異顯著。石油化工園區需應對高溫高壓管道的揮發性有機物(VOCs)泄漏,這類氣體易燃易爆,濃度達爆炸極限易引發連鎖反應;冶金車間的高爐煤氣含一氧化碳等劇毒成分,微量泄漏就可能導致人員中毒;食品醫藥行業無菌車間,氨氣等制冷劑泄漏會污染生產環境,影響產品質量安全。
不同場景對檢測設備要求特殊:粉塵濃度高的礦山環境,檢測裝置需超強抗干擾能力;潮濕的污水處理區域要求設備達 IP68 級防水標準;防爆區域,檢測系統必須通過 ATEX、IECEx 等國際認證。
(二)管理體系的全流程與合規性
現代企業氣體安全管理已從 “事后處置” 轉向 “全生命周期防控”,需遵循相關標準,實現設備選型、安裝校準、日常巡檢到數據追溯全流程管控。完整的檢測數據鏈是事故溯源的關鍵依據。
企業需建立三級響應機制:檢測值達預警閾值,系統自動聲光報警;達警戒閾值,聯動通風設備啟動;達緊急閾值則立即切斷氣源并啟動應急預案。階梯式響應模式既避免過度反應導致生產中斷,又確保風險可控。
二、當前氣體泄漏檢測的痛點與挑戰
(一)技術層面的瓶頸制約
傳統檢測方式有明顯局限性。人工巡檢受檢測頻率、人員經驗影響大,曾有煉油廠因漏檢閥門微漏,導致裝置停車 23 小時;固定式檢測點覆蓋范圍有限,大型裝置區存在檢測盲區;實驗室分析方法精度高,但檢測周期長,無法實時監控。
檢測數據準確性面臨挑戰。環境溫濕度變化影響氣體傳感器靈敏度,某化工廠夏季高溫時段多次誤報致非計劃停機;不同氣體交叉干擾,硫化氫與二氧化硫在特定濃度比下,可能導致電化學傳感器讀數失真。
(二)管理層面的協同壁壘
多數企業氣體安全管理存在 “信息孤島”。檢測設備數據未與 DCS、MES 有效聯動,檢測到泄漏需人工傳遞信息至控制室,延誤應急處置。某工業園區事故中,泄漏發生到系統報警間隔達 47 秒,因數據傳輸鏈路斷裂。
責任劃分不清是普遍問題。設備采購部門關注硬件成本,可能選用不合需求的裝置;生產車間注重連續性,常屏蔽報警信號;維護團隊因缺乏標準化校準流程,導致設備長期 “帶病運行”。管理脫節使檢測系統難發揮效能。
三、智能化氣體泄漏檢測系統的技術架構
(一)多層級感知網絡的構建
現代氣體檢測系統采用 “點 - 線 - 面” 立體布防。關鍵閥門、法蘭等易泄漏點安裝微型傳感器,實現毫米級監測;沿管道敷設分布式光纖,通過激光光譜分析捕捉沿線氣體濃度變化;裝置區部署移動巡檢機器人,搭載紅外熱成像儀自主規劃路徑,形成無死角網絡。
混合部署模式使泄漏檢測覆蓋率從 68% 提升至 99.7%,平均響應時間縮至 0.8 秒。系統支持多種通信協議,通過 LoRaWAN 實現低功耗廣域網傳輸,或 5G 專網滿足高帶寬實時傳輸,適應不同企業網絡環境。
(二)智能算法的深度應用
基于機器學習的智能分析引擎是核心。采集歷史泄漏數據,構建含 128 種典型泄漏模式的數據庫,檢測到異常時自動比對特征參數,識別泄漏源類型與速率,準確率 98.3%。某乙烯裝置應用后,誤報率從每月 15 次降至 1 次以下。
預測性維護算法分析傳感器漂移趨勢、電池健康狀態等數據,提前 14 天預測設備故障風險,自動生成校準工單。主動維護模式使設備有效運行時間延長至 1800 小時,較傳統提升 3 倍。
四、全場景解決方案的實踐路徑
(一)系統部署的標準化流程
檢測系統部署遵循 “三步實施法”。前期調研繪制 “氣體風險熱力圖”,標注高風險區域氣體種類、壓力等級、歷史泄漏記錄等,為點位規劃依據;安裝調試采用激光校準,確保傳感器誤差≤±2% FS,進行 3 次以上泄漏模擬測試;驗收階段連續運行 30 天,確保數據傳輸穩定性 99.9%。
某煤化工企業按流程實施,系統投用后故障處理效率提升 40%。老廠改造采用磁吸式安裝等非侵入式方案,避免停車損失。
(二)數據應用的價值挖掘
系統積累的海量數據可作安全管理決策依據。某化肥廠分析泄漏頻次與設備運行時間關聯曲線,發現往復式壓縮機運行 1200 小時后泄漏概率上升,將維保周期從 1500 小時調為 1000 小時,泄漏次數減少 62%。
數據可視化平臺提供全局視角,總控室大屏實時顯示各區域泄漏濃度熱力圖、設備在線率等指標。出現異常時,系統自動推送處置預案,包括疏散路線、應關閉閥門編號等,讓應急指揮更具針對性。
五、標桿應用實踐
大型石化企業智能防控體系覆蓋多個生產裝置區、工藝管道,部署大量傳感器。采用 “邊緣計算 + 云平臺” 架構,邊緣節點 50ms 內完成本地報警判斷;開發專屬 AI 模型,區分閥門正常排氣與異常泄漏,解決對間歇性排放誤判;與企業 ERP 系統集成,自動核算泄漏物料損耗,及時處置挽回可觀損失。實施后重大泄漏事故發生率降至零,獲相關稱號。
醫藥園區潔凈環境解決方案針對生物制藥車間特殊性,采用復合傳感器檢測多種氣體,滿足 GMP 潔凈度要求;傳感器外殼用特殊不銹鋼材質,支持在線清洗,避免檢測中斷;數據記錄符合國際規范,可追溯檢測相關信息,通過國際認證審核。系統使環境類偏差事件減少 75%。
六、未來發展趨勢展望
隨著物聯網技術成熟,氣體泄漏檢測邁向 “自愈式防控”。下一代系統實現檢測 - 分析 - 處置閉環自動化,檢測到泄漏自動調節閥門開度、啟動通風、通知人員撤離,無需人工干預。
綠色低碳趨勢下,檢測系統融入碳足跡管理。精確計量泄漏氣體種類與量,自動換算碳排放數據,助企業實現 “安全防控 + 碳管理” 雙重目標。某煉化企業借此每年減少碳排放核算誤差約 3000 噸 CO?當量。
安全管理本質是風險管理,智能化氣體泄漏檢測系統是企業風險防控 “神經末梢”。技術創新重塑工業安全格局,選擇適配檢測方案是合規要求,更是企業可持續發展戰略投資,精準檢測守護生命與未來。
-
物聯網
+關注
關注
2931文章
46264瀏覽量
392935 -
檢測系統
+關注
關注
3文章
975瀏覽量
43945 -
設備管理系統
+關注
關注
0文章
81瀏覽量
2206
發布評論請先 登錄
如何使用arduino nano組裝氣體泄漏檢測報警系統
利用智慧消防系統筑牢高校檔案消防安全防線
ARDUINO LPG氣體泄漏檢測器
紅外氣體泄漏檢測中的圖像算法
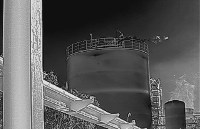
評論