深夜的化工車間,離心泵突然發出刺耳異響,半小時后徹底停機 —— 這樣的突發故障,曾讓某化工廠單月損失超50萬元。傳統運維中,設備故障就像 "不定時炸彈",人工巡檢漏檢率高達30%,單一溫度監測常因誤報讓工人疲于奔命。如今,中設智控推出的聲振溫三合一監測系統,正通過聲音、振動、溫度多維度感知,讓工業設備故障預警從"猜"變成"算"。
打破單參數監測局限,三維數據鎖定故障前兆
設備故障從來不是孤立事件:軸承磨損會先出現異常振動,隨后伴隨溫度升高,最終產生異響。中設智控這套系統的核心創新,在于將聲紋采集(20Hz-20kHz 全頻段)、振動分析(三軸加速度 ±70g)、溫度監測(-40℃~125℃)整合為一體,像醫生 "聽診 + CT + 體溫" 聯合診斷一樣,捕捉設備早期故障信號。
相較于傳統單一參數監測,這套系統解決了三大行業痛點:電機軸承缺油時,振動值先于溫度異常,避免 "溫度未超標卻突然卡死" 的窘境;風機葉輪積灰初期,聲紋特征變化早于振動峰值,提前 2 周預警潛在失衡風險;泵機氣蝕故障中,三維數據交叉驗證可將誤報率從 25% 降至 3%,讓運維人員不再被 "狼來了" 困擾。
從數據采集到智能預警,全鏈路技術支撐可靠監測
這套系統能在工業場景中穩定運行,背后是三層技術架構的硬核支撐。感知層采用 IP67 防護的一體化傳感器,磁吸式安裝設計可直接吸附在電機、泵機等設備表面,無需布線即可采集聲音波形、振動頻譜和溫度曲線,適應高溫、粉塵、潮濕等惡劣環境。
數據處理層搭載邊緣計算模塊,每秒完成 3000 組數據的特征提取,通過自研 AI 算法識別軸承外圈裂紋的 "高頻沖擊特征"、齒輪嚙合不良的 "周期性聲紋異常" 等典型故障模式。當監測值超出動態閾值時,系統會通過分級預警機制,將輕微異常推送給巡檢人員,嚴重隱患直接聯動 PLC 系統觸發停機保護。
應用層的可視化平臺則讓數據 "會說話":振動波形圖直觀顯示振幅變化,聲紋頻譜圖標注異常頻率峰值,溫度趨勢線自動生成溫升速率曲線。某汽車工廠通過平臺發現焊接機器人的 Z 軸振動值在 3 天內從 0.2g 升至 0.8g,提前更換軸承避免了生產線停擺,單此節約損失超 200 萬元。
多行業落地驗證,讓預測性運維不止是概念
在制造業車間,電機軸承的早期磨損曾是老大難問題。中設智控為某重型機械廠的 20 臺電機安裝監測系統后,通過分析 10-1000Hz 頻段的振動數據,精準識別出 3 臺電機的 "內圈剝落前兆",提前 15 天安排更換,將單臺維修成本從 5 萬元壓減至 0.8 萬元。
化工行業的泵機組更受益于聲振溫協同監測。某石化廠的輸油泵在運行中,系統捕捉到 "流量穩定但振動低頻分量增加 + 異音出現" 的復合信號,判斷為葉輪輕微汽蝕,通過調整進口壓力避免了泵體損壞,較傳統定期檢修模式減少非計劃停機 80 小時 / 年。
就連港口等高振動環境也能穩定發揮。某港口在10公里皮帶機的滾筒處部署傳感器,通過振動Z軸加速度與溫度變化的關聯性分析,提前預警5處軸承潤滑不良,將維護周期從"每月一次"優化為"按需保養",年節省潤滑脂消耗 30%。
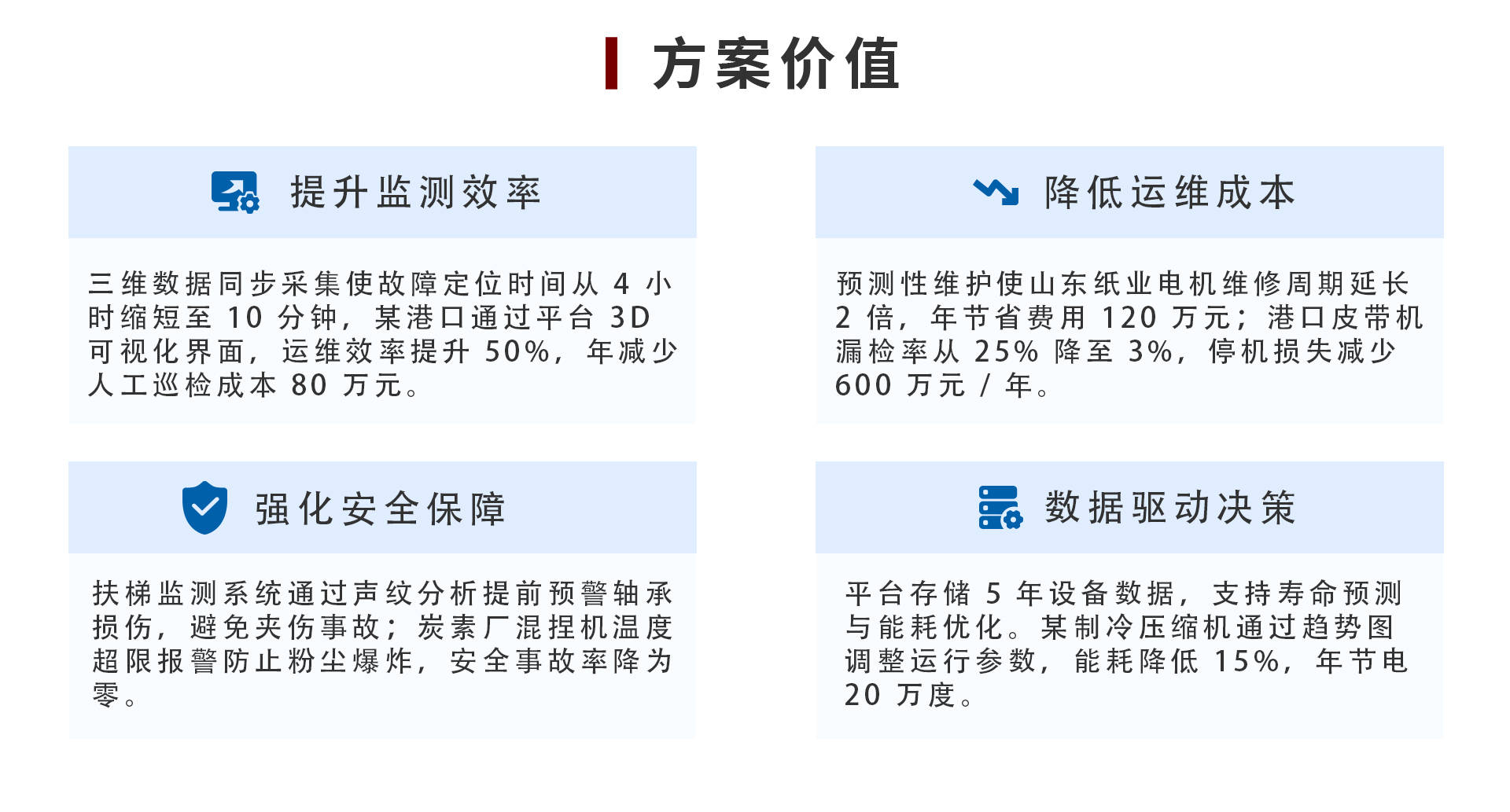
當工業設備的健康狀態可感知、故障趨勢可預測,運維模式便從 "被動救火" 轉向 "主動預防"。中設智控聲振溫監測系統用聲音、振動、溫度的三維數據,為工業設備裝上 "聽診器" 和 "體溫計",讓預測性運維從 PPT 概念變成車間里的真實場景,成為智能制造落地的重要支點。
-
工業設備
+關注
關注
1文章
247瀏覽量
10988 -
工業互聯網
+關注
關注
28文章
4363瀏覽量
95103 -
設備管理系統
+關注
關注
0文章
81瀏覽量
2206
發布評論請先 登錄
評論