貞光科技深耕汽車電子、工業(yè)及軌道交通領(lǐng)域十余年,為客戶提供車規(guī)MCU、車規(guī)電容、車規(guī)電阻、車規(guī)晶振、車規(guī)電感、車規(guī)連接器等車規(guī)級(jí)產(chǎn)品和汽車電子行業(yè)解決方案,成立于2008年的貞光科技是三星、VIKING、紫光芯能、基美、國(guó)巨、泰科、3PEAK思瑞浦等國(guó)內(nèi)外40余家原廠的授權(quán)代理商。獲取更多方案或產(chǎn)品信息可聯(lián)系我們。
800V架構(gòu)是全級(jí)別車型實(shí)現(xiàn)快充的主流選擇。對(duì)于電池端,快充實(shí)質(zhì)上是提升各電芯所在支路的充電電流,而隨著單車 帶電量超100kWh以上的車型持續(xù)推出,電芯數(shù)量增加,若仍繼續(xù)維持400V母線電壓規(guī)格,電芯并聯(lián)數(shù)量增加,導(dǎo)致母線電流增加,對(duì)銅線規(guī)格、熱管理帶來巨大挑戰(zhàn)。因此需要改變電池包內(nèi)電芯串并聯(lián)結(jié)構(gòu),減少并聯(lián)而增加串聯(lián),方能 在提升支路電流的同時(shí)維持母線電流在合理水平。由于串聯(lián)數(shù)量增加,母線端電壓將提升。而100kWh電池包實(shí)現(xiàn)4C快充所要求的母線電壓即為800V左右。為了兼容全級(jí)別車型快充功能,800V電氣架構(gòu)成為實(shí)現(xiàn)快充的主流選擇。
整車: 會(huì)戰(zhàn)高端化,800V車樁并舉。2019年豪車品牌保時(shí)捷推出全球首款800V車型Taycan 。2020年比亞迪漢采用了 800V架構(gòu),2021年上海車展發(fā)布的e平臺(tái)3.0亦搭載800V架構(gòu)。隨后華為、吉利、廣汽、小鵬、嵐圖等Tier1和整車廠/品 牌推出了車樁兩端的解決方案,以保障快充使用體驗(yàn)。
未來兩年高端化是整車廠主戰(zhàn)場(chǎng),軍備競(jìng)賽開啟。補(bǔ)能 時(shí)間是電動(dòng)車面臨的核心短板之一,升級(jí)800V結(jié)構(gòu)有利于實(shí)現(xiàn)快充,在短期內(nèi)形成對(duì)中低端車型的差異化競(jìng)爭(zhēng)力。長(zhǎng)期 看快充對(duì)于中低端車型亦是剛需,800V架構(gòu)升級(jí)具備長(zhǎng)期趨勢(shì)。
零部件與元器件:SiC和負(fù)極受益最大,其他部件平滑升級(jí)。從目前400V升級(jí)至800V ,變化最大的零部件和元器件主要是功率半導(dǎo)體和電池負(fù)極。其中SiC基功率半導(dǎo)體由于耐壓高、損耗低、開關(guān)頻率高等優(yōu)異性能,預(yù)計(jì)將全面替代Si基功率半導(dǎo)體。
由于快充瓶頸在于負(fù)極,如要將目前的1C倍充電率提升至2C,再提升至4C,主流技術(shù)包括石墨包覆/摻雜硬碳、硅碳負(fù)極。其余部件則需要重新選型,提升耐壓等級(jí),但整體來看成本變化平滑。短期來看高壓方案比目前方案整 車成本增加2%左右,長(zhǎng)期看有望低于目前成本,為整車廠推廣建立了良好基礎(chǔ)。 零部件與元器件:SiC和負(fù)極受益最大,其他部件平滑升級(jí)
400V->800V哪些零部件和元器件需要升級(jí)?
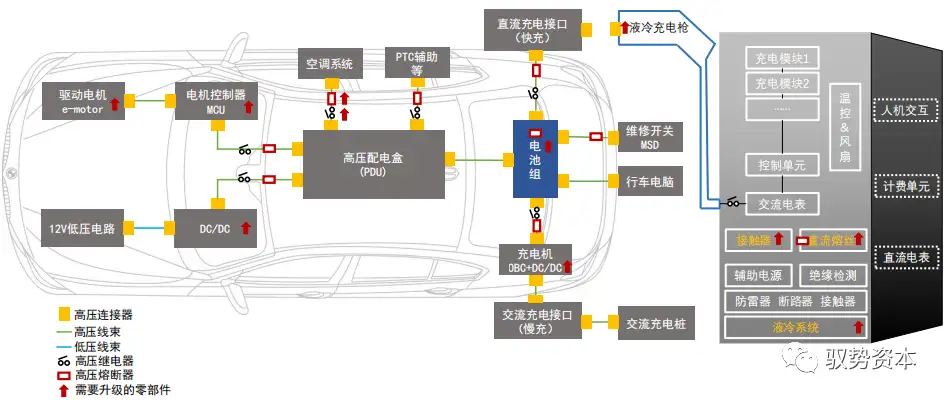
電控
800V下SiC性能優(yōu)異,替代Si基功率半導(dǎo)體趨勢(shì)明確:
- SiC基功率半導(dǎo)體相比Si基具備更高耐壓等級(jí)和開關(guān)損耗,以Si-IGBT為例,450V下其耐壓為650V,若汽車電氣架構(gòu)升級(jí)至800V,考慮開關(guān)電壓開關(guān)過載等因素,對(duì)應(yīng)功率半導(dǎo)體耐壓等級(jí)需達(dá)1200V,而高電壓下Si-IGBT的開關(guān)/導(dǎo)通損耗急劇升高,面臨成本上升而能效下降的問題。
- 800V下SiC的耐壓、開關(guān)頻率、損耗表現(xiàn)優(yōu)異,是800V趨勢(shì)下最大受益元器件。
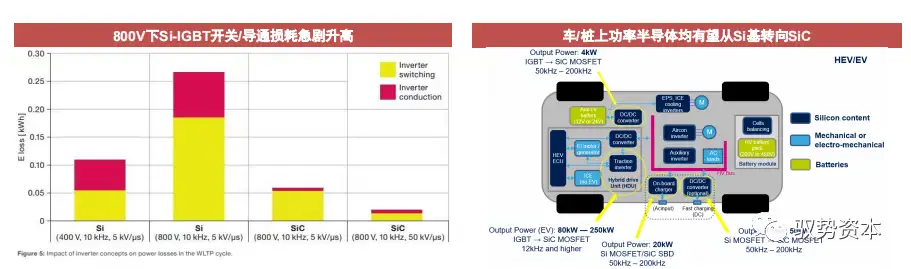
薄膜電容提升耐壓等級(jí),短期內(nèi)單車價(jià)值提升:
- 薄膜電容的作用是作為直流支撐電容器,從DC-link端吸收高脈沖電流,保護(hù)功率半導(dǎo)體。一般一個(gè)功率半導(dǎo)體配一個(gè)薄膜電容,新能源車上主要用于電機(jī)控制器、OBC上,若多電機(jī)車型,薄膜電容用量亦會(huì)隨之增加。另外,在直流快充樁上亦需要一個(gè)薄膜電容。
- 目前薄膜電容ASP為200元,800V趨勢(shì)下,薄膜電容的ASP需提升約20%。另外短期看,800V會(huì)在高端車率先應(yīng)用,高端車一般采用多電驅(qū)配置,提升薄膜電容用量。
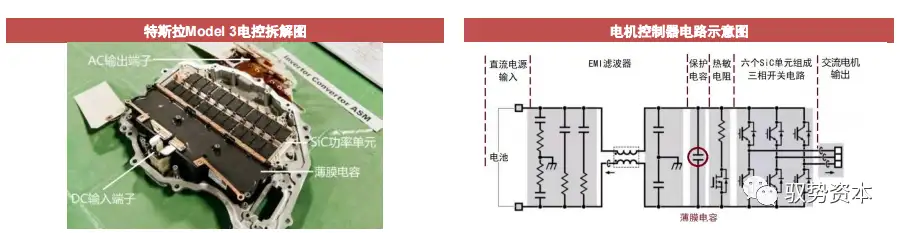
電池
負(fù)極快充性能要求提升。動(dòng)力電池快充性能的掣肘在于負(fù)極:
- 一方面石墨材料的層狀結(jié)構(gòu),導(dǎo)致鋰離子只能從端面進(jìn)入,導(dǎo)致離子傳輸路徑長(zhǎng);
- 另一方面石墨電極電位低,高倍率快充下石墨電極極化大,電位容易降到0V以下而析鋰。
解決方法主要有兩類:
- 石墨改性:表面包覆、混合無定型碳,無定型碳內(nèi)部為高度無序的碳層結(jié)構(gòu),可以實(shí)現(xiàn)Li+的快速嵌入。
- 硅負(fù)極:理論容量高(4200mAh/g,遠(yuǎn)大于碳材料的372mAh/g),適合快充的本征原因是嵌鋰電位高——析鋰風(fēng)險(xiǎn)小——可以容忍更大的充電電流。
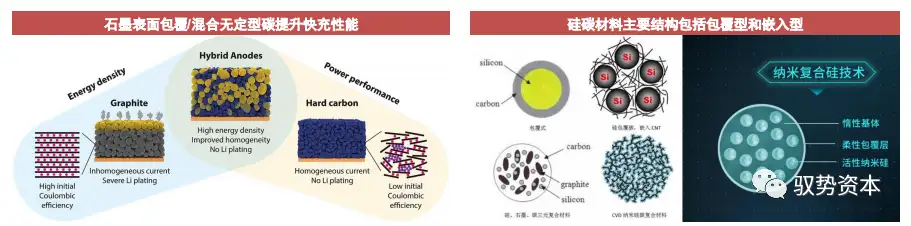
電機(jī)
軸承防腐蝕、絕緣要求增加。軸電壓的產(chǎn)生:
- 電機(jī)控制器供電為變頻電源,含有高次諧波分量,逆變器、定子繞組、機(jī)殼形成回路,產(chǎn)生感應(yīng)電壓,稱為共模電壓,在此回路上產(chǎn)生高頻電流。由于電磁感應(yīng)原理,電機(jī)軸兩端形成感應(yīng)電壓,成為軸電壓,一般來說無法避免。
- 轉(zhuǎn)子、電機(jī)軸、軸承形成閉合回路,軸承滾珠與滾道內(nèi)表面為點(diǎn)接觸,若軸電壓過高,容易擊穿油膜后形成回路,軸電流出現(xiàn)導(dǎo)致軸承腐蝕;
- 800V的逆變器應(yīng)用SiC,導(dǎo)致電壓變化頻率高,軸電流增大,軸承防腐蝕要求增加;
- 同時(shí),由于電壓/開關(guān)頻率增加,800V電機(jī)內(nèi)部的絕緣/EMC防護(hù)等級(jí)要求提升。
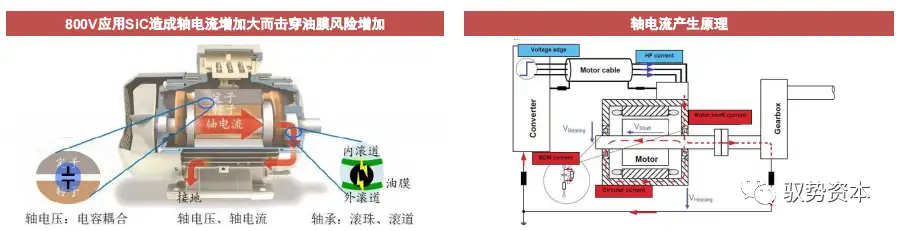
高壓直流繼電器:高性能要求驅(qū)動(dòng)附加值,單車價(jià)值量提升
性能升級(jí),優(yōu)勢(shì)廠商優(yōu)勢(shì)明顯:作為新能源車高壓電流回路的橋梁,升壓對(duì)連接器的可靠性、體積和電氣性能的要求增加,其在機(jī)械性能、電氣性能、環(huán)境性能三方面均將持續(xù)提升。
作為中高端產(chǎn)品,電動(dòng)汽車高壓連接器有較高的技術(shù)與工藝壁壘。傳統(tǒng)燃油車的低壓連接器被海外供應(yīng)商壟斷。電動(dòng)車快速增長(zhǎng)打開高壓連接器新增量,技術(shù)變化要求快速響應(yīng),整車平臺(tái)高壓化將進(jìn)一步提高行業(yè)壁壘,國(guó)產(chǎn)供應(yīng)商迎來國(guó)產(chǎn)替代機(jī)遇。
數(shù)量增加,單車價(jià)值量有望提升:目前單輛電動(dòng)車配置15-20個(gè)高壓連接器,單價(jià)在100-250元之間,雙電機(jī)或大功率驅(qū)動(dòng)電機(jī)車型需求量更多。從400V增至800V后,高壓連接器將重新選型,增加大功率快充接口及400V到800V的轉(zhuǎn)化接口,帶動(dòng)高壓連接器單車價(jià)值量上升。
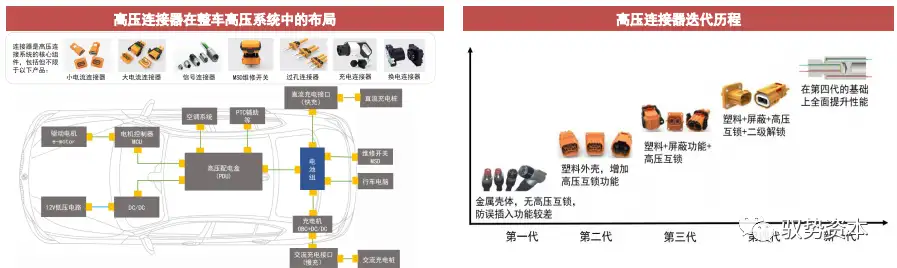
OBC/DCDC:主動(dòng)元件升級(jí),短期內(nèi)受益升壓增量
高電壓對(duì)功率器件提出更高要求,將驅(qū)動(dòng)OBC/DCDC成本短期內(nèi)攀升:
- 為滿足800v高電壓平臺(tái)在體積、輕量、耐壓、耐高溫等方面帶來的更為嚴(yán)苛的要求,OBC/DCDC等功率器件集成化趨勢(shì)明顯;
- 同時(shí),預(yù)計(jì)SiC碳化硅將借助耐高壓、耐高溫、開關(guān)損耗低等優(yōu)勢(shì)在功率器件領(lǐng)域進(jìn)行廣泛應(yīng)用,驅(qū)動(dòng)單車OBC/DCDC價(jià)值量提高約10%-20%。
800v高壓平臺(tái)有望為OBC/DCDC帶來新增量:
- 高壓平臺(tái)使車載充電機(jī)升級(jí)需求增加,為高壓OBC提供增量;
- 同時(shí),為能夠適配使用原有400v直流快充樁,搭載800v電壓平臺(tái)新車須配有額外DCDC轉(zhuǎn)換器進(jìn)行升壓,進(jìn)一步增加對(duì)DCDC的需求。
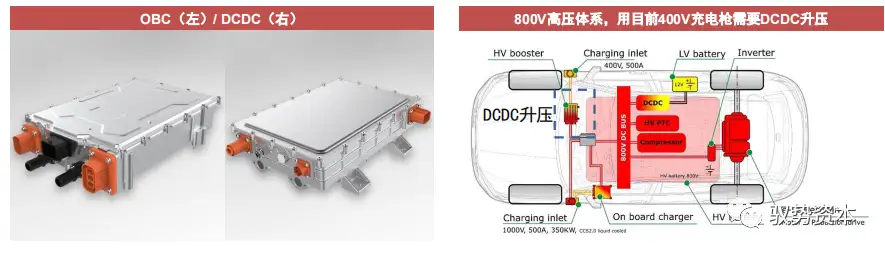
軟磁合金粉芯:升壓模塊提升用量需求
電感元件主要材料是由金屬磁粉芯:
- 800V體系升級(jí),中短期為了適配現(xiàn)存的400V充電樁,需加裝DCDC升壓模塊,獨(dú)立升壓模塊需要額外的電感。單車用量從原來0.5kg提升至約2.7kg;
- 插混車由于電池容量較小,電壓無法通過串聯(lián)做到400V,對(duì)升壓DCDC需求更大。一般而言,純電動(dòng)/插混單車用量0.5/4kg。
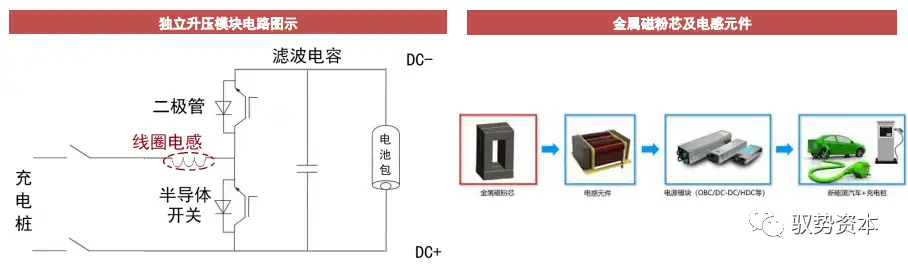
充電樁:高壓快充比低壓大電流快充節(jié)省約5%成本
相同功率下,由于電流減小,電壓由400v到800v仍不需要液冷,未來500A則需要增配液冷系統(tǒng)。
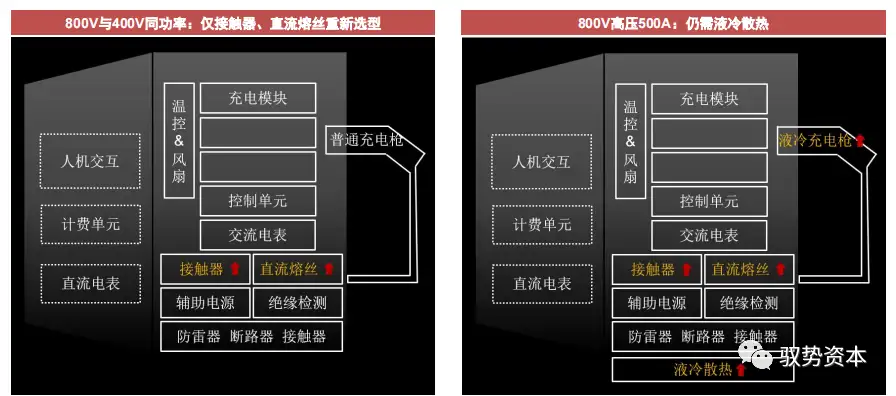
400V-800V車端成本變動(dòng)平滑,利好整車廠推廣
車端成本來看,高壓架構(gòu)比低壓架構(gòu)成本+2%。
- 電池端由于負(fù)極快充性能提升、BMS復(fù)雜程度提升等因素,成本+5%;
- 從整車部件來看,高壓架構(gòu)在熱管理、線纜輔料等部件成本變化小,優(yōu)于低壓高電流架構(gòu)。
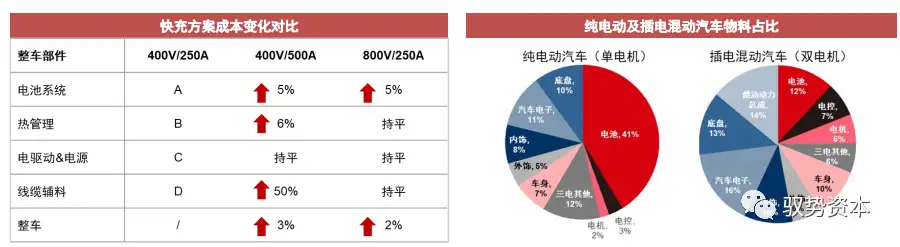
800V受益板塊單車價(jià)值量與產(chǎn)業(yè)鏈標(biāo)的:
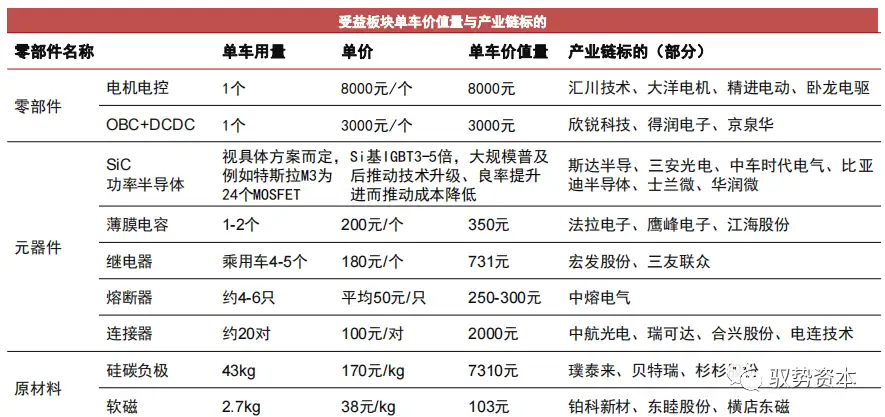
【免責(zé)聲明】版權(quán)歸原作者所有,本文僅用于技術(shù)分享與交流,文中觀點(diǎn)不代表貞光科技立場(chǎng),若有涉及版權(quán)等請(qǐng)聯(lián)系刪除。
-
碳化硅
+關(guān)注
關(guān)注
25文章
3044瀏覽量
50185
發(fā)布評(píng)論請(qǐng)先 登錄
麥科信光隔離探頭在碳化硅(SiC)MOSFET動(dòng)態(tài)測(cè)試中的應(yīng)用
派恩杰推出最新研發(fā)的高壓碳化硅功率器件與車規(guī)級(jí)碳化硅模塊產(chǎn)品
比亞迪推出全新一代車規(guī)級(jí)碳化硅功率芯片
碳化硅薄膜沉積技術(shù)介紹
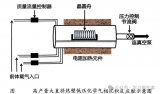
碳化硅在半導(dǎo)體中的作用
產(chǎn)SiC碳化硅MOSFET功率模塊在工商業(yè)儲(chǔ)能變流器PCS中的應(yīng)用
什么是MOSFET柵極氧化層?如何測(cè)試SiC碳化硅MOSFET的柵氧可靠性?
碳化硅在新能源領(lǐng)域的應(yīng)用 碳化硅在汽車工業(yè)中的應(yīng)用
碳化硅SiC在電動(dòng)車中的應(yīng)用
碳化硅襯底,進(jìn)化到12英寸!
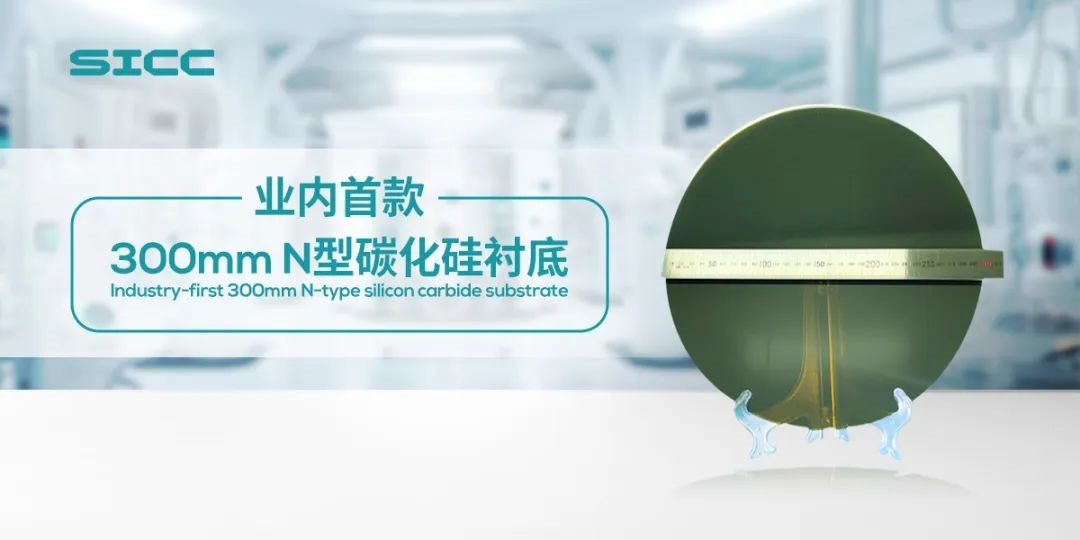
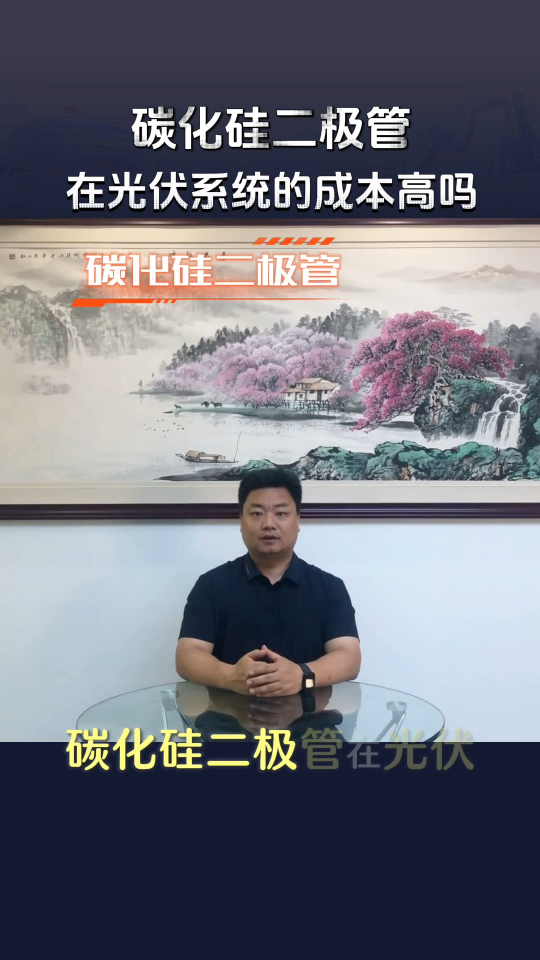
基本半導(dǎo)體碳化硅MOSFET通過AEC-Q101車規(guī)級(jí)認(rèn)證
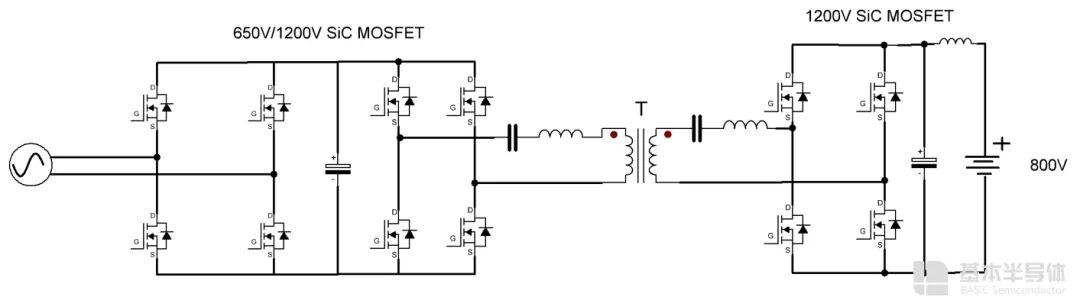
碳化硅功率器件的優(yōu)點(diǎn)和應(yīng)用
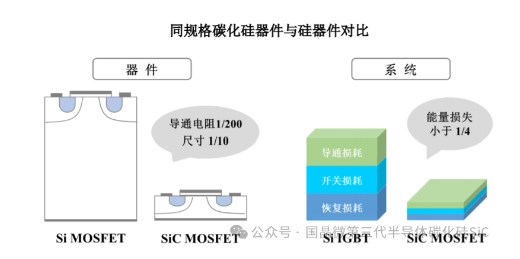
評(píng)論