一、TPM 的概念與起源
TPM,即全面生產維修(Total Productive Management),20 世紀 70 年代由日本中島清一首次提出,是一種旨在優化設備管理的維護方法。它從美國的 PM 活動(生產性保存或預防性保存)中演變而來。
在 20 世紀 50 年代,美國的設備制造業飛速發展,進行了各種設備的維護活動,稱為 PM 活動。到了 60 年代,日本意識到這一管理方法的重要性,開始推進和豐富 PM 活動內容。為促進 PM 活動的普及,日本設立了 PM 大獎。1971 年,豐田汽車公司的子公司日本電裝,在開展 PM 活動過程中,首次提出 TPM 概念,并以出色的 TPM 結果贏得了當年的 PM 獎。
TPM 具有全系統、全效率、全員參與的特點,核心是全員參與、預防為主。在 TPM 中,T(Total)代表公司全體員工,包括經營層領導、生產一線工人以及公司內各部門的開發、營銷、管理等員工。TPM 強調全員參與和團結合作,凝聚集體智慧,依靠全員共同完成經營使命。P(Productive)指公司業務的生產性,著重于經濟性、效益性和效率性。M(Maintenance)代表保全,涵蓋了針對生產系統整個生命周期的活動,旨在將生產體系保持在理想狀態。
二、TPM 的目標與特點
(一)明確的目標追求
TPM 以零停機、零廢品、零事故和零速度損失為目標,致力于提高設備綜合效率。這一目標的設定并非一蹴而就,而是需要通過一系列的管理措施和全員的共同努力來逐步實現。
零停機意味著計劃外的設備停機時間為零。計劃外的停機對生產造成的沖擊巨大,會使整個生產流程發生困難,造成資源閑置等浪費情況。為了實現這一目標,需要采取預防性維修、預測性維修等措施,及時發現并解決設備潛在的問題,確保設備的穩定運行。
零廢品要求由設備原因造成的廢品為零。“完美的質量需要完善的機器”,機器是保證產品質量的關鍵,而人是保證機器好壞的關鍵。通過全員參與設備的維護和管理,保證設備的精度和性能,從而減少因設備問題導致的廢品產生。
零事故是指設備運行過程中事故為零。設備事故的危害非常大,不僅會影響生產,還可能造成人身傷害,嚴重的甚至會 “機毀人亡”。這就需要加強設備的安全管理,提高員工的安全意識,建立完善的安全制度和應急預案。
零速度損失則是指設備速度降低造成的產量損失為零。由于設備保養不好,設備精度降低而不能按高速度使用設備,等于降低了設備性能。因此,要通過定期的設備保養和維修,確保設備始終保持在最佳運行狀態。
(二)顯著的特點呈現
TPM 具有全系統、全效率、全員參與的特點,核心是全員參與、預防為主。
全系統是指 TPM 管理中包含了 PM、MP、CM 等多種設備生產維修方法,對設備維修維護進行全方位、多層次的檢查,確保設備的安全性以及使用性。從設備的規劃、選型、安裝、調試到日常運行、維護保養,再到設備的改造、更新直至報廢,整個生命周期都納入了 TPM 的管理范圍。
全效率強調設備壽命周期費用評價和設備綜合生產效率。不僅關注設備的正常運行,更注重設備在整個生命周期內的綜合效率,包括設備的生產效率、質量、成本、交貨期、安全和環境等多個方面。通過提高設備的綜合效率,實現企業的經濟效益最大化。
全員參與是 TPM 的主要特點,也是區別于其他設備管理方法的關鍵因素。從企業的最高管理層到一線員工,每個人都對設備的維護和管理負有責任。通過開展自主保全、計劃保全等活動,培養員工的自主管理意識和能力,形成全員關心設備、維護設備的良好氛圍。
預防為主是 TPM 的核心管理思想。強調 “預防為主,治療為輔”,通過定期的設備檢查、保養和預防性維修,將設備故障消滅在萌芽狀態,降低設備故障率,延長設備使用壽命。同時,建立完善的預防管理體系,從設備的設計、選型、安裝等環節就融入預防思維,確保設備始終處于最佳運行狀態。
三、TPM 的具體內容
(一)管理活動組成
TPM 由設備保全、質量保全、個別改進、事務改進、環境保全、人才培養 6 個方面組成。
設備保全是 TPM 的核心內容之一,旨在確保設備的正常運行和延長設備的使用壽命。通過日常的維護保養、定期的檢修以及預防性維修等措施,降低設備故障率,提高設備的可靠性。例如,某制造企業通過實施嚴格的設備保全措施,設備故障停機時間從每月 20 小時降低到了 5 小時,大大提高了生產效率。
質量保全則強調通過設備管理來保證產品質量。設備的精度、穩定性等因素直接影響產品的質量,因此,通過對設備的維護和管理,確保設備能夠生產出符合質量標準的產品。據統計,實施 TPM 后,企業的產品合格率平均提高了 10% 以上。
個別改進是針對設備的特定問題進行的改進活動。當設備出現一些頻繁發生的小故障或者性能不達標的情況時,通過個別改進來解決這些問題,提高設備的性能。例如,某企業的一臺設備經常出現卡料現象,經過個別改進,調整了設備的進料裝置,卡料問題得到了徹底解決。
事務改進主要涉及管理流程的優化,提高管理效率。通過簡化審批流程、優化信息傳遞等方式,減少管理環節中的浪費,為設備管理提供更好的支持。
環境保全強調在設備管理過程中要注重環境保護。減少設備運行過程中的能源消耗、降低噪音和污染物排放等,實現可持續發展。
人才培養是 TPM 的重要組成部分。通過培訓和教育,提高員工的技能水平和設備管理意識,培養出一批既懂技術又懂管理的復合型人才。據調查,實施 TPM 的企業中,員工經過培訓后,對設備的操作和維護能力平均提高了 30%。
(二)主要手段
TPM 使用設備綜合效率(OEE)作為主要手段,它與六大損失相關聯,通過時間開動率、性能開動率和合格品率三個可測量指標反映設備運行狀況。
設備綜合效率(OEE)考慮了設備工作時間、性能和質量水平三個方面。公式表示為:設備綜合效率 = 時間開動率性能開動率合格品率。
- 時間開動率 = 實際工作時間 / 計劃工作時間。計劃工作時間 = 每班可用時間 - 計劃停機時間,實際工作時間 = 計劃工作時間 - 非計劃停機時間。例如,若每天單班生產,每班工作 8 小時,每班可用時間 480 分鐘,其中有 15 分鐘的換型時間,10 分鐘班前會時間,30 分鐘的非計劃設備故障。則計劃工作時間 = 每班可用時間 - 計劃停機時間 = 480-10=470(分鐘),實際工作時間 = 計劃工作時間 - 非計劃停機時間 = 470-15-30=425(分鐘),時間開動率 = 實際工作時間 / 計劃工作時間 = 425/475=90.4%。
- 性能開動率,是指理論產出和實際產出的比值,它考慮二個方面:凈開動率和速度運轉率。性能開動率 = 凈開動率速度運轉率。凈開動率 =(產量實際節拍)/ 實際工作時間,速度運轉率 = 理論節拍 / 實際節拍。仍用前面的例子,若加工量是 300 件,實際節拍是每件 1 分鐘,理論節拍是每件 40 秒,實際工作時間 425 分鐘,則:凈開動率 =(產量實際節拍)/ 實際工作時間 =(3001)/425=70.59%,速度運轉率 = 理論節拍 / 實際節拍 = 40/60=66.7%,性能開動率 = 凈開動率 * 速度運轉率 = 70.59%*66.7%=47.08%。
- 合格品率 =(合格品數量 / 生產數量)*100%。若質量合格率為 95%,那么設備綜合效率 OEE 是:設備綜合效率 OEE=90.4%*47.08%*95%=40.4%。
TPM 通過對這三個指標的分析和改進,致力于提高設備的綜合效率。當來自時間、速度、質量的損失被綜合在一起,最終 OEE 數字反映出任何設備或生產線的運行狀況。企業可以通過設定 OEE 目標和測量偏差,然后采取措施來消減差異,加強業績。
四、TPM 在企業中的作用
(一)提升產品質量
TPM 通過嚴格的設備保全措施,確保生產設備始終處于良好狀態。設備的精度和穩定性是影響產品質量的關鍵因素,而 TPM 中的質量保全活動,強調通過對設備的維護和管理來保證產品質量。例如,企業定期對設備進行精度調整和維護,確保設備能夠生產出符合質量標準的產品。據統計,實施 TPM 的企業,產品合格率平均提高了 10% 以上。同時,全員參與的設備管理模式,使得員工更加關注設備的運行狀態,能夠及時發現并解決設備問題,從而減少因設備故障導致的產品質量問題。
(二)保障及時生產制
TPM 能夠有效減少設備故障,提高生產率。通過預防性維護和計劃維護,及時發現并解決設備潛在問題,降低設備故障率,確保設備穩定運行。這減少了生產中斷的時間,加速了生產循環。同時,TPM 活動中的全員自主管理,使員工樹立 “我的設備我來管” 的理念,提高自主積極性和創造性。例如,某企業在實施全員自主管理后,設備故障率降低了 30%,生產準備時間也大大縮短。專業保全體系化,通過診斷技術提高對設備狀態的預知力,提前安排維護計劃,避免設備故障對生產的影響。
(三)降低生產成本
TPM 不僅關注制造成本,還重視維護費用。通過設備保全活動,降低設備故障率,減少設備維修成本。例如,某制造企業通過實施嚴格的設備保全措施,設備故障停機時間從每月 20 小時降低到了 5 小時,大大減少了維修費用。同時,提高設備效率,減少能源消耗和原材料浪費,降低制造成本。TPM 中的事務改進活動,優化管理流程,提高管理效率,減少管理環節中的浪費。
(四)提高設備生產能力
TPM 能夠保障企業生產能力,減少綜合效率低下問題。通過提高設備綜合效率(OEE),充分發揮設備的生產潛力。設備綜合效率考慮了時間開動率、性能開動率和合格品率三個可測量指標,反映設備運行狀況。企業可以通過對這三個指標的分析和改進,提高設備的生產能力。例如,通過提高時間開動率,減少設備停機時間;提高性能開動率,提高設備的性能和產出;提高合格品率,減少廢品產生。同時,重點改善項目管理活動,針對重點項目進行有針對性的管理,追求設備、工藝達到理想狀態,避免生產能力損失。
(五)符合環保與節能要求
TPM 滿足嚴格的環保認證要求,降低能耗,使設備效率最大化。環境保全活動強調在設備管理過程中要注重環境保護,減少設備運行過程中的能源消耗、降低噪音和污染物排放等。例如,通過優化設備運行參數,提高能源利用效率;采用環保型設備和材料,減少對環境的影響。同時,TPM 中的全員參與模式,使得員工更加關注環境保護,積極參與環保活動。此外,TPM 還通過提高設備的可靠性和穩定性,減少設備故障和維修次數,降低對環境的影響。這些措施符合現代社會對環保和節能的要求,實現了企業的可持續發展。
五、TPM 的有效實施方法
(一)小組活動
組織好 PM 小組活動,是推進 TPM 的核心。在生產部門建立 PM 小組,其它部門建立主題活動小組,多部門聯合組成專題項目小組,以小組為單位開展活動,各小組定期舉行例會,適時舉行成果展或總結表彰。
各小組活動的主要內容包括:
- 根據上級的 PM 方針制定小組的工作目標。例如,某企業的 PM 小組根據公司整體的設備管理目標,制定了本小組在一個季度內將設備故障時間降低 20% 的具體目標。
- 開展設備 5S 活動,即整理、整頓、清掃、清潔、素養。通過對設備及周邊環境進行整理,清除不必要的物品,使工作場所更加整潔有序。如一家制造企業在開展設備 5S 活動后,設備周圍的雜物減少了 80%,大大降低了因雜物堆積導致的設備故障風險。
- 針對生產中影響生產的設備六大損失,包括設備故障安裝與調整、試運行減產、空轉與短暫停機、減速、加工次品、閑置等,找出原因,制定并實施對策,加以解決。例如,某工廠通過對設備六大損失的分析,發現空轉與短暫停機主要是由于操作人員對設備操作不熟練導致的,于是組織了專門的操作培訓,使空轉與短暫停機時間減少了 30%。
- 填寫點檢記錄,根據所得數據分析設備的實際技術狀況,針對問題提出改善提案。如某企業的 PM 小組通過定期點檢,發現一臺關鍵設備的磨損情況較為嚴重,及時提出了更換零部件的提案,避免了設備故障的發生。
- 制定并實施教育培訓計劃,提高成員技能,采取各種方式開展技術經驗交流。可以組織內部培訓、邀請外部專家進行講座等形式,提升小組成員的業務能力。據統計,經過系統培訓的 PM 小組成員,在設備維護和問題解決方面的能力平均提高了 40%。
- 檢查各自小組的目標完成情況,進行成果總結評價。通過定期的檢查和總結,及時發現問題并調整策略,確保小組活動的有效性。
(二)教育培訓
教育培訓在 TPM 活動全過程中至關重要,是一切活動的基礎。
教育培訓的主要內容有:
- 必要的業務技能培訓、素質教育。針對不同崗位的員工,開展針對性的技能培訓,提高員工的操作水平和維修能力。例如,對設備操作人員進行設備操作規范培訓,使其能夠正確操作設備,減少因操作不當導致的設備故障。對維修人員進行專業維修技能培訓,提高維修效率和質量。
- 實施理論教育,為 TPM 推進打基礎、鋪道路。通過講解 TPM 的理論知識,讓員工了解 TPM 的重要性和實施方法,提高員工的參與度和積極性。據調查,經過理論教育的員工,對 TPM 的理解和支持度提高了 50% 以上。
- 根據企業相關管理制度的執行情況,確立典型的正面和反面事例,通過教育激勵先進、鞭策后進。例如,對在設備維護和管理方面表現突出的員工進行表彰和獎勵,對違反設備管理制度的員工進行批評和處罰,營造良好的設備管理氛圍。
- 采取 “走出去,請進來,經驗體會相傳” 的學習模式,根據活動具體主題進行針對性培訓、互補性培訓等。組織員工參觀其他企業的 TPM 實施情況,學習先進經驗;邀請外部專家進行培訓,拓寬員工的視野。同時,鼓勵員工之間進行經驗交流和分享,共同提高設備管理水平。
另外,在活動過程中建立優秀表彰制度也必不可少。這樣既可提高活動的積極性,又能挖掘員工的潛力,增強激勵機制,促進活動持久、有效地開展。例如,某企業設立了 “TPM 之星” 獎項,每月評選出在設備管理方面表現優秀的員工進行表彰和獎勵,極大地激發了員工的參與熱情。
(三)全面逐步推動
當示范區整改完成,相關的 TPM 制度也建立完善后,接下來就進入全面實施階段。全面推進實施的做法是以示范區為樣板,以 TPM 推進委員會及示范區人員為核心,擬定全面逐步實施計劃,一個區域一個區域的推進,逐步完成。
在全面逐步推動過程中,要注意以下幾點:
- 明確各階段的目標和任務。根據企業的實際情況,將全面實施過程劃分為若干個階段,每個階段都有明確的目標和任務。例如,在第一階段,重點推進設備 5S 活動;在第二階段,加強設備點檢和維護;在第三階段,提高設備綜合效率等。
- 建立有效的溝通機制。在全面實施過程中,各部門之間需要密切配合,及時溝通和協調。建立定期的溝通會議制度,及時解決實施過程中出現的問題。
- 持續改進和優化。在全面實施過程中,要不斷總結經驗教訓,對 TPM 制度和實施方法進行持續改進和優化。例如,根據設備運行情況和員工反饋,調整設備點檢標準和維護計劃,提高設備管理的效果。
如果企業規模大的話,有可能需要 3 - 5 年才能全部完成。TPM 設備管理改善只有起點,沒有終點,企業需要不斷地推進和完善 TPM 管理,提高設備管理水平和企業的競爭力。
-
TPM
+關注
關注
0文章
62瀏覽量
16207 -
管理系統
+關注
關注
1文章
2705瀏覽量
36576 -
設備管理
+關注
關注
0文章
141瀏覽量
9441 -
設備管理系統
+關注
關注
0文章
74瀏覽量
2114
發布評論請先 登錄
相關推薦
傳統設備管理的7大痛點,你的企業中了幾個?
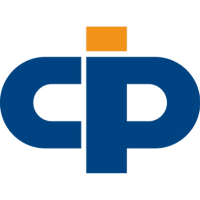
設備管理系統,終結設備管理難題
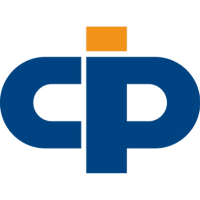
智能設備管理系統:如何讓企業效率飆升300%?
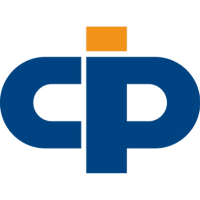
數字化技術在TPM設備管理中的具體應用
EasyControl賦能華為HarmonyOS系統的企業級移動設備管理方案
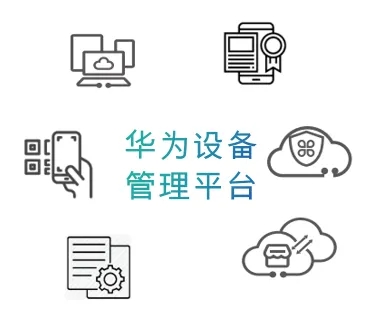
評論