在工業(yè)制造領(lǐng)域,設(shè)備管理是企業(yè)運營的核心環(huán)節(jié)。然而,許多企業(yè)仍沿用傳統(tǒng)管理模式,導(dǎo)致效率低下、成本高企。本文將從手工記錄維修歷史、備件浪費、部門數(shù)據(jù)孤島等七大痛點切入,結(jié)合EAM(企業(yè)資產(chǎn)管理)系統(tǒng)的解決方案,揭示數(shù)字化轉(zhuǎn)型如何幫助企業(yè)突破管理瓶頸,并通過實際案例展現(xiàn)轉(zhuǎn)型成效。
一、傳統(tǒng)設(shè)備管理的七大痛點
1. 手工記錄維修歷史:信息滯后與誤差頻發(fā)
傳統(tǒng)設(shè)備管理依賴紙質(zhì)或Excel表格記錄維修信息,不僅效率低,還容易因人為疏忽導(dǎo)致數(shù)據(jù)錯誤。例如,某企業(yè)設(shè)備部門需每月制定維護計劃,但手工記錄難以實時更新設(shè)備狀態(tài),導(dǎo)致計劃與實際需求脫節(jié):設(shè)備可能在計劃檢修前突發(fā)故障,或狀態(tài)良好卻被迫進行冗余維護。這種“盲人摸象”式的管理,使得設(shè)備故障率居高不下。
2. 備件浪費:庫存積壓與短缺并存
備件管理是傳統(tǒng)模式的另一大難題。企業(yè)常因缺乏數(shù)據(jù)支持而盲目采購,導(dǎo)致庫存積壓或緊急缺貨。某制造企業(yè)每月需提交備件采購計劃,但主管因無法判斷需求合理性,只能“照單全收”,最終造成資金占用和資源浪費7。據(jù)統(tǒng)計,過度庫存可占用企業(yè)20%以上的流動資金。
3. 部門數(shù)據(jù)孤島:協(xié)同效率低下
設(shè)備管理涉及生產(chǎn)、維修、采購等多個部門,但傳統(tǒng)模式下數(shù)據(jù)分散,信息無法共享。例如,維修部門無法實時獲取設(shè)備運行狀態(tài),采購部門難以及時響應(yīng)備件需求。這種“各自為戰(zhàn)”的格局,導(dǎo)致決策滯后和資源內(nèi)耗。
4. 設(shè)備壽命短:缺乏科學維護策略
許多企業(yè)采用“壞了再修”的被動維護模式,忽視預(yù)防性維護。例如,兩家使用同型號設(shè)備的企業(yè),因維護策略不同,設(shè)備壽命差異顯著:一家通過定期保養(yǎng)延長設(shè)備使用周期,另一家則因頻繁故障被迫提前報廢。
5. 合規(guī)性風險:記錄缺失與追溯困難
傳統(tǒng)管理模式下,設(shè)備維護記錄分散且不完整,難以滿足行業(yè)監(jiān)管要求。例如,某化工企業(yè)因無法提供完整的設(shè)備檢修記錄,面臨巨額罰款。
6. 資源利用率低:設(shè)備閑置與超負荷并存
缺乏實時監(jiān)控導(dǎo)致設(shè)備使用不均衡。某鋼鐵企業(yè)部分設(shè)備長期閑置,而核心設(shè)備卻因超負荷運行頻繁故障,整體利用率不足60%。
7. 決策依賴經(jīng)驗:缺乏數(shù)據(jù)支撐
管理人員多憑經(jīng)驗制定維護計劃,忽視設(shè)備實際運行數(shù)據(jù)。例如,某電力公司因未分析設(shè)備歷史故障規(guī)律,導(dǎo)致重復(fù)性故障頻發(fā),每年損失超百萬元。
二、EAM系統(tǒng):擊破痛點的數(shù)字化利器
1. 標準化流程:從“人治”到“數(shù)治”
EAM系統(tǒng)通過工單管理、預(yù)防性維護、預(yù)測性維護三大核心功能,重構(gòu)設(shè)備管理流程:
工單自動化:系統(tǒng)自動生成維護計劃,并實時跟蹤執(zhí)行進度,減少人為干預(yù)。
預(yù)防性維護:基于設(shè)備運行時間或使用周期,制定標準化保養(yǎng)計劃,避免突發(fā)故障。
預(yù)測性維護:通過物聯(lián)網(wǎng)傳感器采集數(shù)據(jù),結(jié)合AI算法預(yù)測故障,實現(xiàn)“精準維修”。
2. 數(shù)據(jù)整合:打破信息孤島
EAM系統(tǒng)集成設(shè)備臺賬、運行監(jiān)控、備件庫存等模塊,構(gòu)建統(tǒng)一數(shù)據(jù)平臺:
實時監(jiān)控:通過2.5D/3D可視化界面,直觀展示設(shè)備狀態(tài),支持跨部門協(xié)同。
全生命周期管理:從采購到報廢,所有數(shù)據(jù)集中存儲,便于追溯與分析。
KPI與OEE分析:量化設(shè)備綜合效率(OEE),為決策提供科學依據(jù)。
3. 智能優(yōu)化:降本增效的實踐路徑
備件庫存優(yōu)化:系統(tǒng)根據(jù)維護計劃自動生成備件需求,結(jié)合安全庫存模型,減少資金占用。
資源調(diào)度優(yōu)化:通過分析設(shè)備利用率,動態(tài)調(diào)整生產(chǎn)計劃,避免閑置與超負荷。
合規(guī)性保障:自動生成合規(guī)報告,滿足ISO 55000等資產(chǎn)管理標準。
三、智能運維新范式
隨著 AI 與物聯(lián)網(wǎng)技術(shù)深度融合,設(shè)備管理正邁向 "三自" 新境界:
- 自感知:通過邊緣計算實現(xiàn)設(shè)備狀態(tài)實時診斷
- 自決策:AI 算法自動生成優(yōu)化方案
- 自執(zhí)行:機器人系統(tǒng)完成自主維護
-
設(shè)備管理
+關(guān)注
關(guān)注
0文章
143瀏覽量
9491 -
EAM
+關(guān)注
關(guān)注
1文章
16瀏覽量
6946 -
智慧工廠
+關(guān)注
關(guān)注
2文章
449瀏覽量
28043
發(fā)布評論請先 登錄
設(shè)備管理系統(tǒng)新范式:區(qū)塊鏈存證+動態(tài)權(quán)限管理
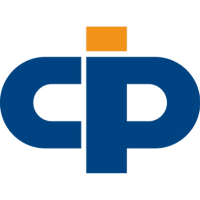
明達云平臺賦能車間設(shè)備管理
設(shè)備管理系統(tǒng),終結(jié)設(shè)備管理難題
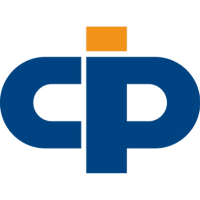
智能設(shè)備管理系統(tǒng):如何讓企業(yè)效率飆升300%?
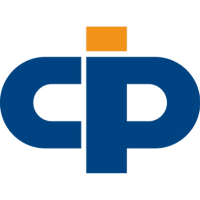
傳統(tǒng) VS 智能,這款設(shè)備管理系統(tǒng)讓管理大不同
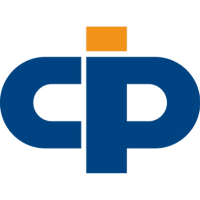
設(shè)備管理系統(tǒng)如何實現(xiàn)一鍵智控?
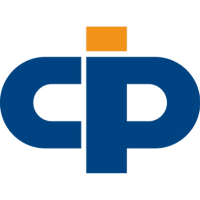
數(shù)據(jù)驅(qū)動變革:設(shè)備管理系統(tǒng)如何重塑企業(yè)競爭力
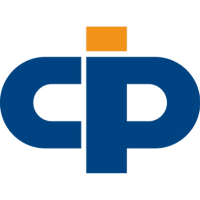
中小企業(yè)設(shè)備管理系統(tǒng)的特點及技術(shù)
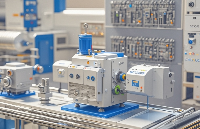
自動化設(shè)備遠程運維的痛點與解決方案
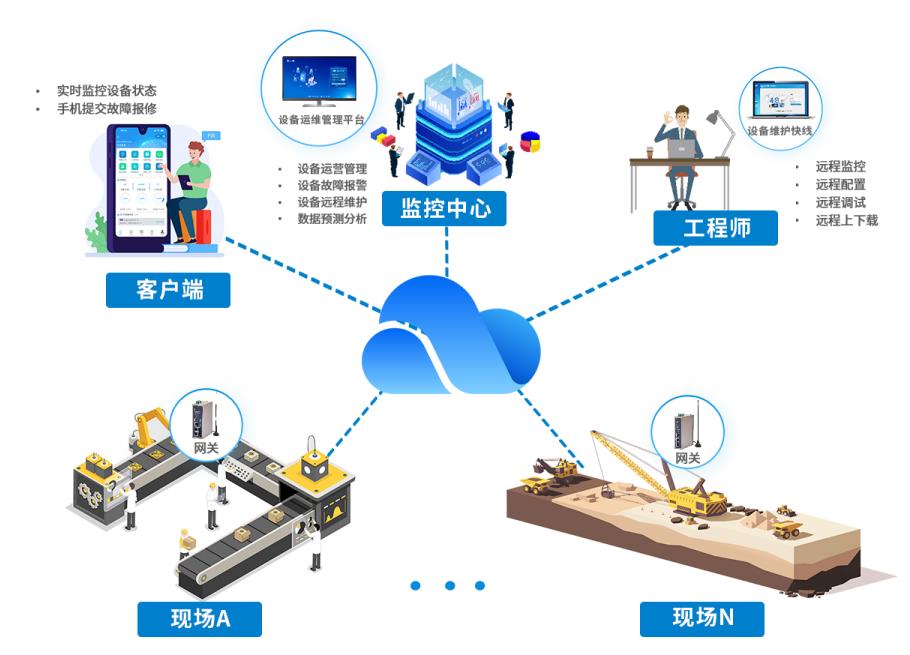
TPM:企業(yè)設(shè)備管理的卓越策略
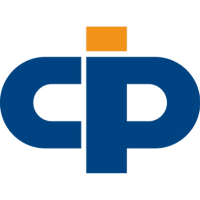
設(shè)備管理流程優(yōu)化的優(yōu)勢
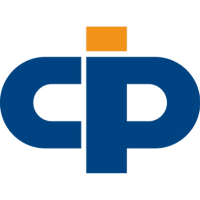
設(shè)備管理——先進的工業(yè)設(shè)備管理模式與策略
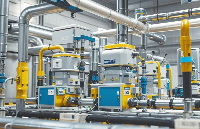
企業(yè)設(shè)備管理的創(chuàng)新與優(yōu)化之道
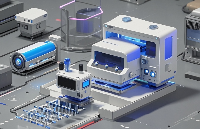
設(shè)備管理:優(yōu)化策略與未來展望
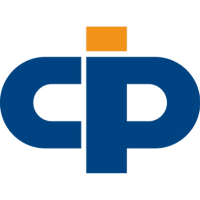
設(shè)備管理系統(tǒng):是什么、誰需要、推薦設(shè)備管理系統(tǒng)
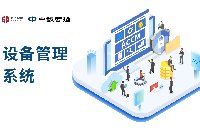
評論