貼片電容的編帶工藝是電子制造領域中一項精細且關鍵的工序,旨在將單個貼片電容有序排列并封裝在編帶中,便于后續的自動化貼片生產。其核心步驟如下:
一、前期準備
首先需將陶瓷粉與粘合劑、溶劑等按嚴格比例混合,經球磨形成均勻的陶瓷漿料。通過流延機將漿料涂布在PET膜上,經干燥后得到厚度10-30微米的陶瓷膜片。隨后利用絲網印刷技術,將內電極漿料精準印刷到膜片上,形成規則排列的電極層。
二、層疊與壓制
將印刷好電極的陶瓷膜片按設計要求錯位疊壓,形成多層陶瓷坯體。通過等靜壓技術對坯體進行加壓處理,使各層間緊密結合,確保結構穩定性。該過程需在無塵環境中進行,防止雜質混入影響電容性能。
三、切割與排膠
將壓制后的多層坯體切割成獨立的電容單體,隨后進行排膠處理。通過390℃高溫烘烤,去除坯體中的粘合劑等有機物質,防止燒結時產生分層或開裂現象。該步驟對最終產品的形狀完整性和電氣性能至關重要。
四、燒結與倒角
排膠后的電容單體在1140-1340℃高溫下燒結,形成具有高機械強度和優良電氣性能的陶瓷體。隨后通過球磨或行星磨對燒結體進行倒角處理,使棱角圓潤并暴露內部電極,確保后續電鍍效果。
五、端電極處理
采用電鍍工藝在電容端頭依次沉積鎳層和錫層。鎳層用于提高焊接可靠性,錫層則增強可焊性。該過程需嚴格控制鍍層厚度和均勻性,避免影響焊接質量。
六、測試與分選
對電容進行全性能測試,包括容量、損耗、絕緣電阻、耐壓等指標。通過100%測量分檔,剔除不良品,確保產品質量符合標準。
七、編帶封裝
將合格電容按規格要求逐個裝入編帶載體中。編帶通常采用紙帶或塑料袋,通過專用設備實現自動排列和封裝。該步驟需確保電容位置精準、間距均勻,為后續SMT貼片提供穩定可靠的物料供應。
貼片電容編帶工藝通過標準化流程將微米級精密元件轉化為可批量生產的標準化組件,其技術細節直接影響電子產品的性能與可靠性。隨著電子設備向小型化、集成化發展,編帶工藝的精度和效率成為衡量制造能力的重要指標。
審核編輯 黃宇
-
貼片電容
+關注
關注
13文章
558瀏覽量
28691
發布評論請先 登錄
貼片電容代理商如何做好詢價需求?
貼片電容為什么會發熱?
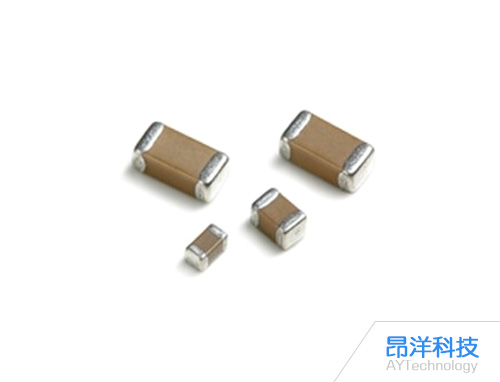
貼片電容代理-貼片電容的標志方法
貼片電容代理:高容值貼片電容的應用
貼片電容代理商如何選擇適合?
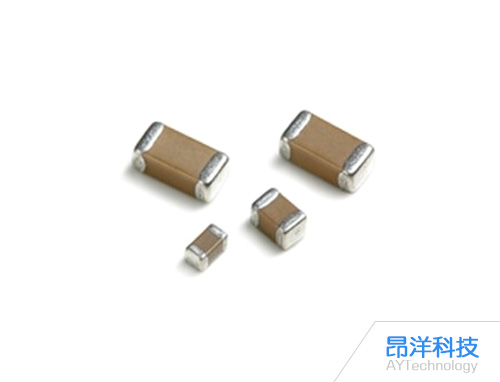
評論