在半導(dǎo)體制造工藝中,化學(xué)機(jī)械拋光(CMP)是實(shí)現(xiàn)晶圓表面全局平坦化的關(guān)鍵技術(shù),而CMP固定環(huán)(保持環(huán))作為拋光頭的核心易耗部件,其性能影響著晶圓加工的良率和生產(chǎn)效率。隨著半導(dǎo)體技術(shù)向更小制程節(jié)點(diǎn)發(fā)展,對(duì)CMP固定環(huán)的材料性能要求日益嚴(yán)苛,聚醚醚酮(PEEK)和聚苯硫醚(PPS)作為兩種高性能工程塑料,通過(guò)注塑成型工藝制造的CMP固定環(huán)正逐步成為半導(dǎo)體制造領(lǐng)域的關(guān)鍵部件。
一、PEEK與PPS注塑成型的CMP固定環(huán)特性比較
在半導(dǎo)體CMP固定環(huán)應(yīng)用中,PEEK和PPS作為兩種高性能熱塑性工程塑料,因其出色的綜合性能而備受青睞。比較這兩種材料的物理化學(xué)特性差異,揭示它們各自在半導(dǎo)體制造中的優(yōu)勢(shì)與局限。
- 耐磨性:注塑PEEK固定環(huán)的耐磨性顯著優(yōu)于PPS,其耐磨性是PPS的三倍左右。在氧化物和鎢拋光液等惡劣環(huán)境下,PEEK固定環(huán)的使用壽命更長(zhǎng),是常用的PPS固定環(huán)的2倍以上,能夠更好地承受CMP工藝中的高壓力和高摩擦力,減少因磨損導(dǎo)致的設(shè)備更換頻率。
- 尺寸穩(wěn)定性:PEEK固定環(huán)具有高尺寸穩(wěn)定性,PPS固定環(huán)的尺寸穩(wěn)定性良好,但不如PEEK固定環(huán),其線脹系數(shù)與金屬鋁非常接近,即使在高溫條件下,也能維持較高的模量,從而保證固定環(huán)在使用過(guò)程中的尺寸精度和穩(wěn)定性,減少因熱膨脹或收縮導(dǎo)致的設(shè)備精度下降問(wèn)題。
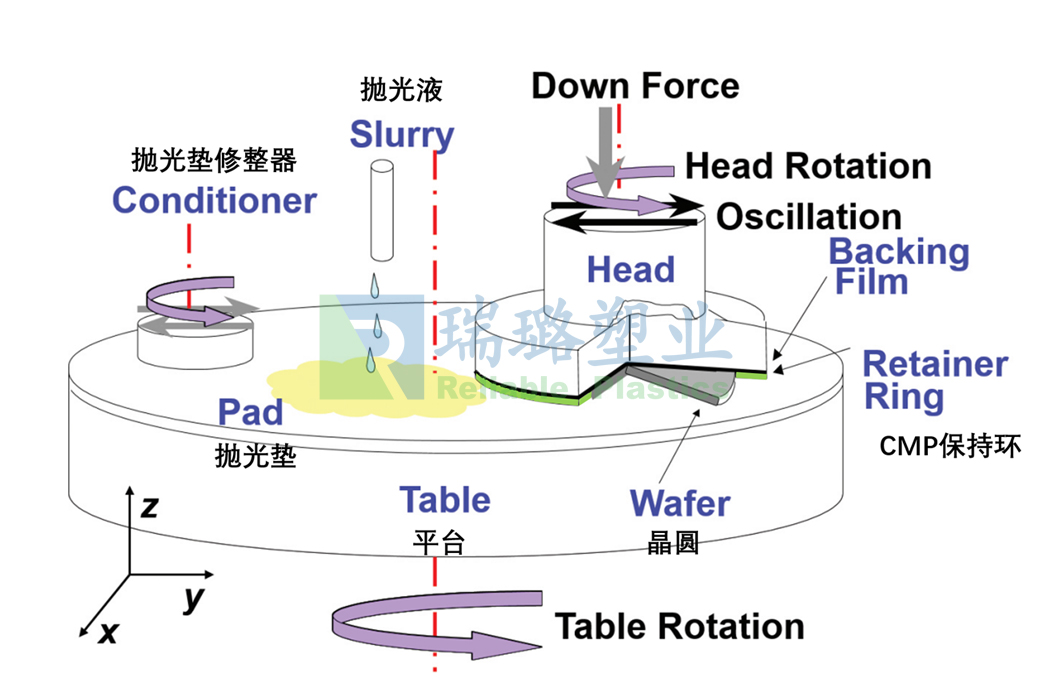
- 耐化學(xué)性:PEEK固定環(huán)對(duì)大多數(shù)有機(jī)溶劑有強(qiáng)耐化學(xué)性,室溫下不溶于常見(jiàn)溶劑,可耐受pH1-14的酸堿環(huán)境,長(zhǎng)期使用下能抵抗弱酸弱堿。PPS耐強(qiáng)酸(尤其無(wú)機(jī)酸)性能優(yōu)于PEEK,但在氧化性酸和某些極性溶劑中可能溶脹或降解。對(duì)于CMP工藝中的過(guò)氧化氫、氨水、鹽酸等,兩者均適用,但PEEK長(zhǎng)期性能衰減更慢。
- 使用壽命:PPS固定環(huán)的使用壽命較短,一個(gè)PPS研磨環(huán)通常只能持續(xù)約4次研磨墊更換。這與PEEK固定環(huán)相比,其使用壽命明顯較短,無(wú)法滿足長(zhǎng)時(shí)間連續(xù)生產(chǎn)的需求,需要更頻繁地更換固定環(huán),增加了生產(chǎn)成本和設(shè)備維護(hù)工作量。
- 加工性能:在注塑加工過(guò)程中,PPS的熔體粘度較低,比PEEK更易于流動(dòng),這使得PPS在注塑薄壁或復(fù)雜結(jié)構(gòu)部件時(shí)更容易充模。此外,PPS的結(jié)晶速率快,冷卻時(shí)間短,有助于縮短注塑周期,提高生產(chǎn)效率。然而,PEEK雖然加工條件更為苛刻,但其收縮率低于PPS,制品尺寸穩(wěn)定性更高。
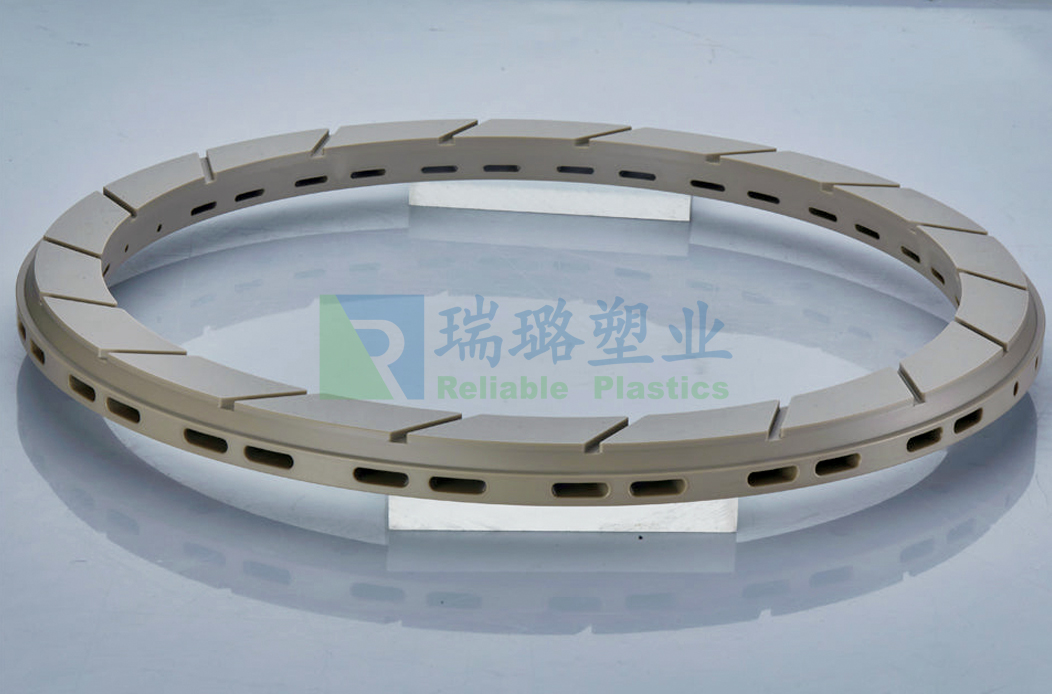
二、CMP固定環(huán)的注塑成型工藝
- 材料預(yù)處理:PEEK和PPS在注塑前需要進(jìn)行充分的干燥處理,以去除材料中的微量水分。PEEK的吸濕率雖然較低(約0.5%),但其對(duì)水分極為敏感,一般要求在150℃下干燥4-6小時(shí)。PPS的吸濕性更弱(約0.05%),但因加工溫度較低,可在120-140℃干燥3-4小時(shí)。
- 模具設(shè)計(jì):PEEK需要較高溫度保證流動(dòng)性,PPS流動(dòng)性相對(duì)較差,模具的流道設(shè)計(jì)應(yīng)盡量減少流動(dòng)阻力,需要使用較大直徑的噴嘴,以利于材料順利填充模具型腔。同時(shí),要確保模具溫度均勻,具備有效的冷卻系統(tǒng),以保證制品的質(zhì)量和尺寸穩(wěn)定性。
- 工藝參數(shù):PEEK和PPS都應(yīng)采用中高速注射(充模時(shí)間約2-5秒),以確保熔體前沿溫度均勻,避免冷料或流痕缺陷。注射壓力上PEEK需要100-150MPa,PPS約80-120MPa。保壓壓力一般為注射壓力的50-70%,保壓時(shí)間根據(jù)制品壁厚確定。
- 后處理:脫模后的固定環(huán)通常需要進(jìn)行去毛刺處理,特別是對(duì)于需要高精度配合的固定環(huán),任何微小的飛邊或毛刺都可能影響其使用性能。對(duì)于PEEK材料,由于其結(jié)晶溫度范圍較寬,脫模后還需進(jìn)行退火處理,進(jìn)一步提高制品的結(jié)晶度和尺寸穩(wěn)定性,減少后期使用中的變形。
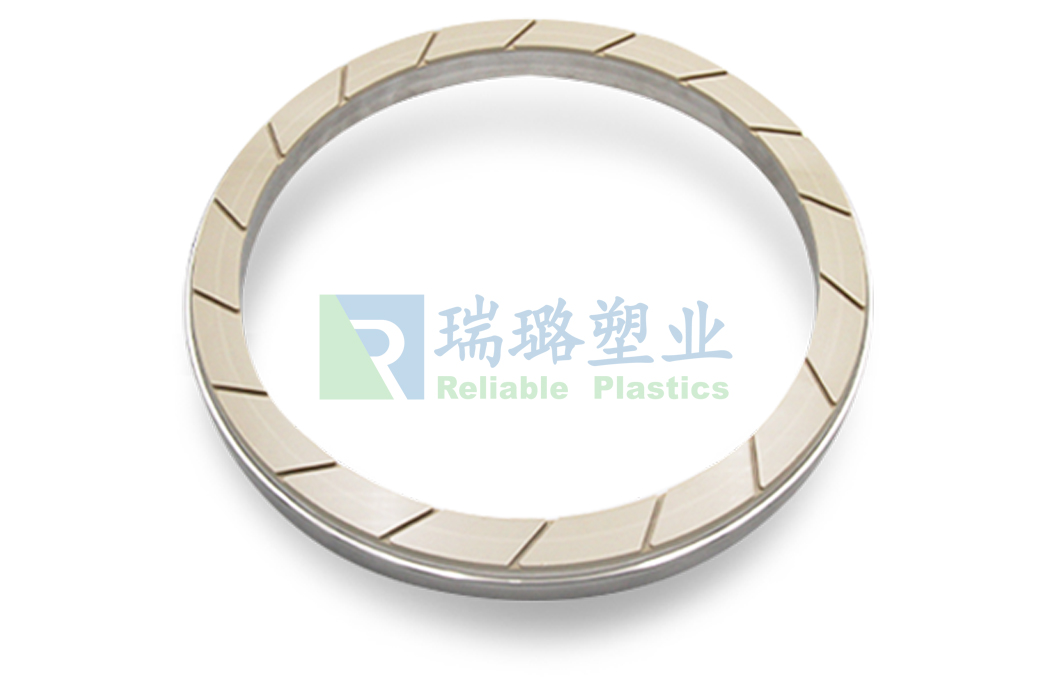
總結(jié):
在半導(dǎo)體制造向更先進(jìn)制程邁進(jìn)的過(guò)程中,注塑成型的PEEK和PPS CMP固定環(huán)憑借其高精度、高效率、復(fù)雜結(jié)構(gòu)一體化成型的優(yōu)勢(shì),正成為晶圓平坦化工藝的核心部件。盡管PEEK在綜合性能上更具優(yōu)勢(shì),但PPS在加工效率和成本控制方面表現(xiàn)突出。未來(lái),通過(guò)進(jìn)一步優(yōu)化注塑成型工藝和材料改性,這兩種材料將在半導(dǎo)體制造領(lǐng)域發(fā)揮更重要的作用,為晶圓加工的良率和生產(chǎn)效率提供堅(jiān)實(shí)保障。
審核編輯 黃宇
-
PPS
+關(guān)注
關(guān)注
0文章
30瀏覽量
10792 -
CMP
+關(guān)注
關(guān)注
6文章
154瀏覽量
26551 -
半導(dǎo)體制造
+關(guān)注
關(guān)注
8文章
442瀏覽量
24612
發(fā)布評(píng)論請(qǐng)先 登錄
注塑加工半導(dǎo)體CMP保持環(huán):高性能材料與精密工藝的結(jié)合
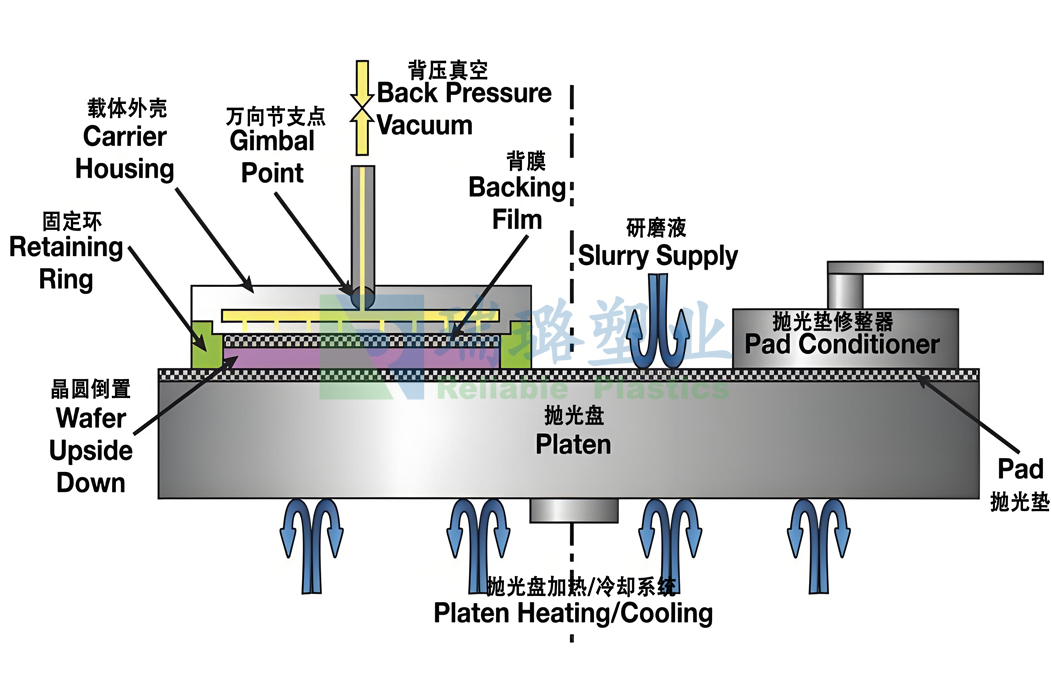
PEEK注塑軸向磁通電機(jī)的輕量化高性能解決方案
PEEK注塑電子封裝基板的創(chuàng)新應(yīng)用方案
PPS注塑IC元件封裝中的應(yīng)用優(yōu)勢(shì)與工藝
注塑PEEK光伏接線盒的高性能與工藝優(yōu)勢(shì)
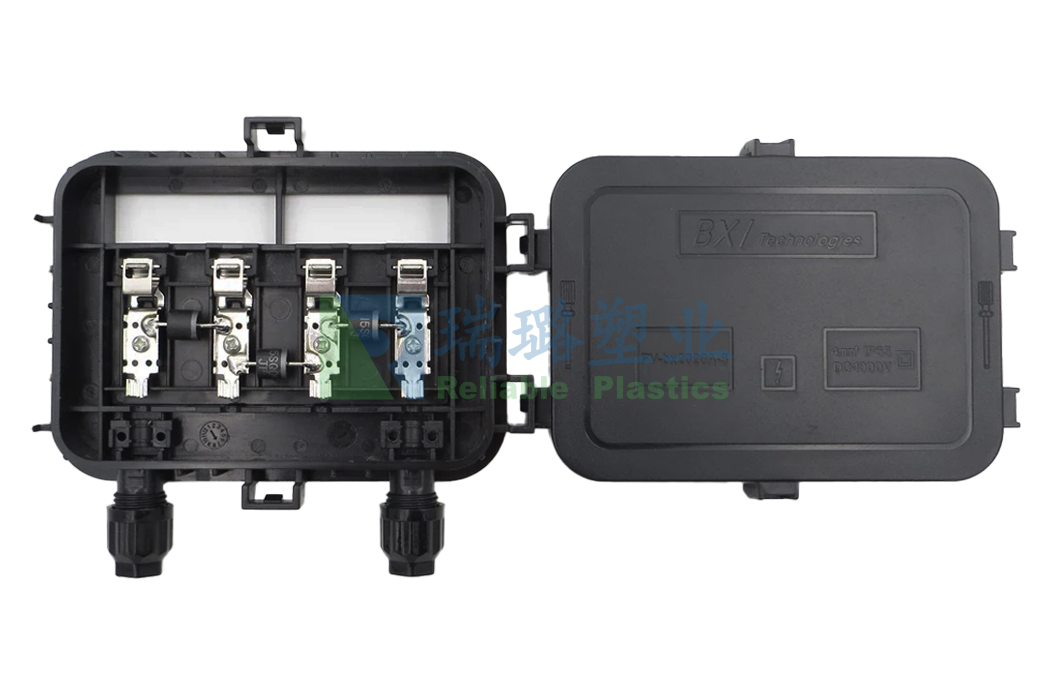
功率半導(dǎo)體器件IGBT模塊:PPS注塑加工案例
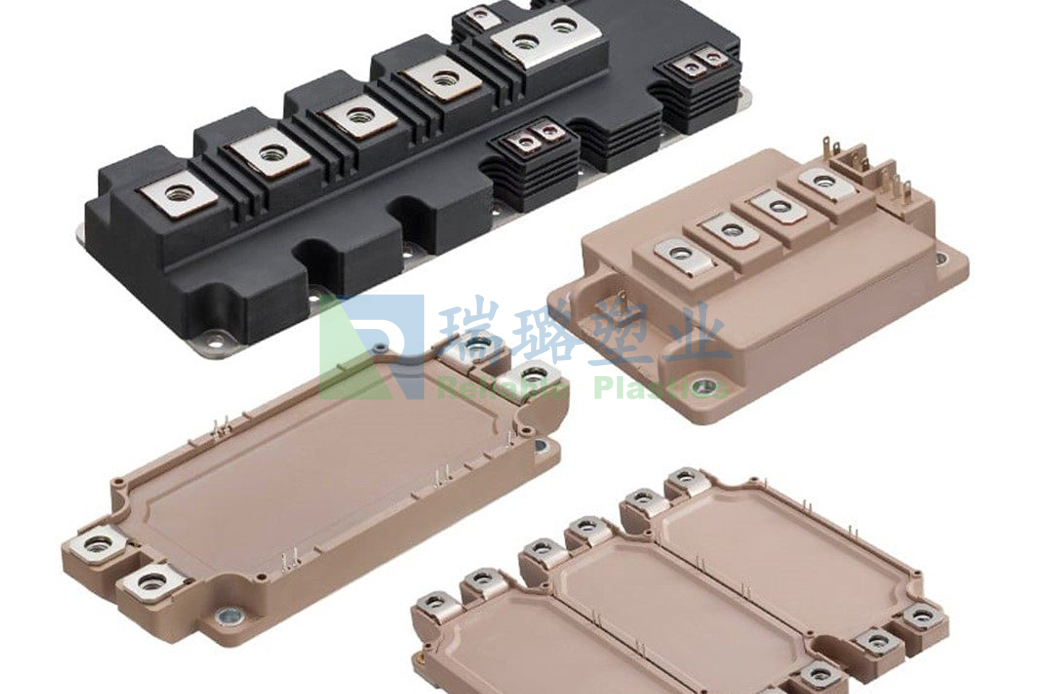
從性能到應(yīng)用—PEEK零件加工在電子電氣行業(yè)的卓越表現(xiàn)
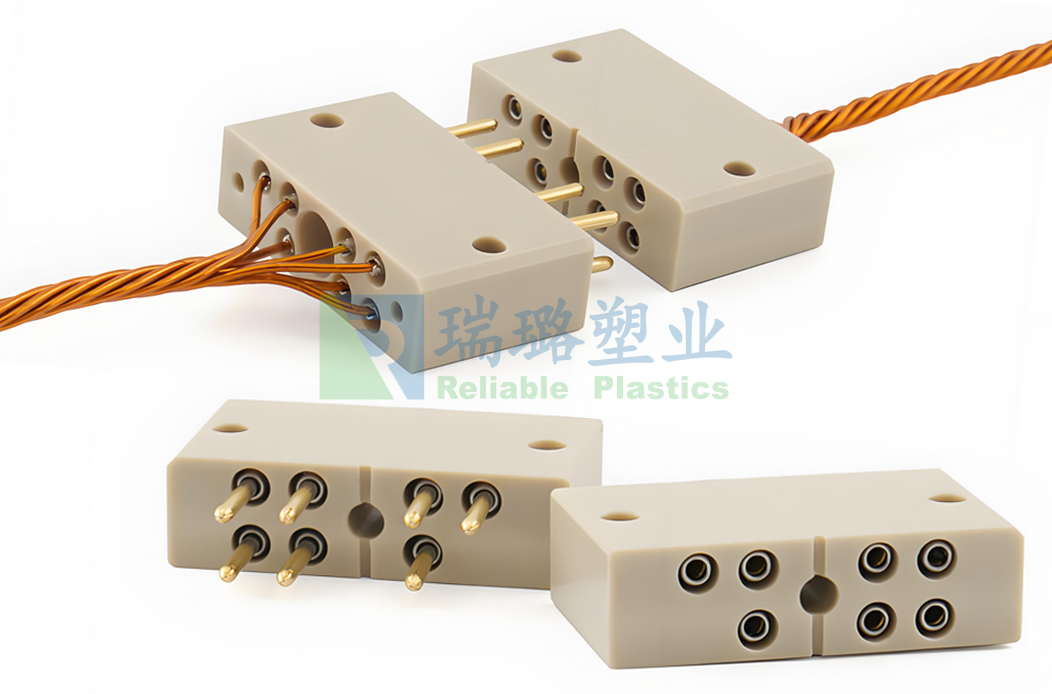
借助工業(yè)邊緣網(wǎng)關(guān)實(shí)現(xiàn)注塑機(jī)智能監(jiān)測(cè)管理
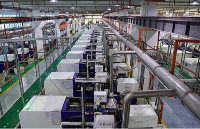
注塑工藝—推動(dòng)PEEK晶圓夾在半導(dǎo)體的高效應(yīng)用
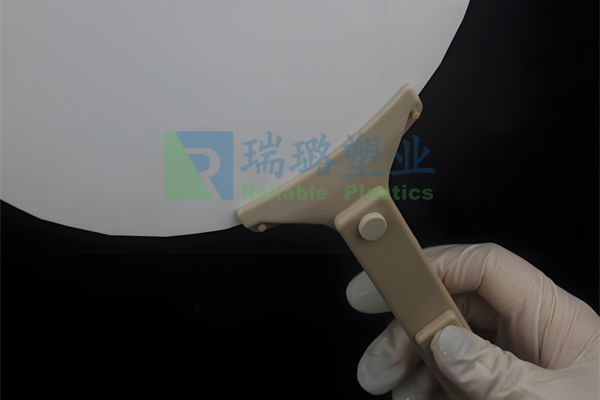
評(píng)論