在工業(yè)自動化控制系統(tǒng)中,PLC(可編程邏輯控制器)作為核心控制設(shè)備,其穩(wěn)定性和可靠性直接影響整個生產(chǎn)線的運行效率。然而,在實際應(yīng)用中,PLC產(chǎn)品難免會出現(xiàn)各種故障問題。為了確保PLC設(shè)備的正常運行,必須對故障問題進行系統(tǒng)化測試。本文將詳細介紹PLC產(chǎn)品故障問題測試的四個關(guān)鍵部分,幫助技術(shù)人員快速定位和解決問題。
一、硬件測試
硬件測試是PLC故障診斷的首要環(huán)節(jié),主要針對PLC設(shè)備的物理部件進行檢查。首先,需要檢查電源模塊是否正常工作。電源故障是PLC常見問題之一,表現(xiàn)為設(shè)備無法啟動或運行不穩(wěn)定。測試時需測量輸入電壓是否在允許范圍內(nèi)(通常為AC 85-264V或DC 24V),并檢查電源模塊的輸出電壓(如5V、24V)是否穩(wěn)定。若發(fā)現(xiàn)電源異常,可能是濾波電容老化、保險絲熔斷或穩(wěn)壓電路故障導(dǎo)致。
其次,對I/O模塊進行測試。輸入模塊的故障常表現(xiàn)為信號無法采集,可通過短接輸入點與COM端,觀察PLC輸入指示燈狀態(tài)來驗證;輸出模塊故障則表現(xiàn)為執(zhí)行機構(gòu)無動作,可通過強制輸出指令測試繼電器或晶體管是否正常導(dǎo)通。此外,還需檢查端子排接線是否松動、氧化,以及模塊與基板間的連接是否牢固。例如,某案例中因輸出端子接觸不良導(dǎo)致電磁閥間歇性失靈,重新壓接端子后故障消失。
對于CPU模塊,需觀察運行指示燈狀態(tài)(RUN/STOP/ERR),若出現(xiàn)頻繁重啟或通信中斷,可能是CPU板卡元器件損壞或程序存儲器故障。此時可通過更換備用模塊進行交叉驗證。值得注意的是,環(huán)境因素如溫度、濕度、振動等也會引發(fā)硬件故障,因此測試時需結(jié)合設(shè)備運行環(huán)境綜合分析。
二、軟件測試
軟件測試主要針對PLC程序邏輯及系統(tǒng)配置進行驗證。首先需檢查程序是否完整下載至PLC,并確認程序版本與設(shè)備型號匹配。常見的軟件故障包括:掃描周期過長導(dǎo)致控制滯后、子程序調(diào)用錯誤、定時器/計數(shù)器設(shè)置不當?shù)取Mㄟ^在線監(jiān)控功能,可實時查看變量狀態(tài)和程序執(zhí)行流程,定位異常跳轉(zhuǎn)或死循環(huán)。
在通信配置測試中,需驗證PLC與上位機、HMI、變頻器等設(shè)備的通信參數(shù)(如波特率、站地址、協(xié)議類型)是否一致。例如,Modbus RTU通信失敗可能是因奇偶校驗設(shè)置沖突,而Profinet通信中斷常與IP地址分配錯誤有關(guān)。通過通信診斷工具(如Wireshark抓包分析)可快速識別協(xié)議層問題。
此外,需特別關(guān)注特殊功能模塊(如PID控制、高速計數(shù))的軟件配置。某案例顯示,因PID參數(shù)未整定導(dǎo)致溫度控制超調(diào),通過自整定功能優(yōu)化后系統(tǒng)恢復(fù)穩(wěn)定。軟件測試還應(yīng)包括內(nèi)存使用率檢查,防止因數(shù)據(jù)塊溢出引發(fā)隨機故障。
三、外圍設(shè)備測試
PLC系統(tǒng)的故障往往并非源自控制器本身,而是由外圍設(shè)備異常引發(fā)。傳感器測試是重點環(huán)節(jié),如接近開關(guān)、光電傳感器等可通過萬用表測量輸出信號是否隨觸發(fā)狀態(tài)變化。對于模擬量傳感器(4-20mA/0-10V),需校準零點和滿量程值,避免因漂移導(dǎo)致數(shù)據(jù)失真。
執(zhí)行機構(gòu)測試包括接觸器、電磁閥、伺服驅(qū)動器等。可通過手動強制輸出檢查動作響應(yīng),同時監(jiān)測反饋信號(如限位開關(guān)狀態(tài))。典型案例中,某生產(chǎn)線因氣缸磁性開關(guān)失效導(dǎo)致PLC誤判位置,更換傳感器后故障排除。電機類設(shè)備還需測試過載保護功能,防止因堵轉(zhuǎn)損壞PLC輸出點。
對于分布式I/O系統(tǒng)(如ET200),需測試遠程站點的供電和通信穩(wěn)定性。實踐中,DP從站頻繁掉站可能是終端電阻未接或電纜屏蔽層破損所致。建議使用總線分析儀檢測信號質(zhì)量,確保通信波形無畸變。
四、綜合診斷與預(yù)防措施
完成上述測試后,需進行系統(tǒng)性診斷。通過PLC自診斷功能查看事件日志(如西門子S7-300的OB塊錯誤代碼),結(jié)合故障現(xiàn)象分析根本原因。例如,某設(shè)備頻繁報"看門狗超時"錯誤,最終確認為電磁干擾導(dǎo)致CPU異常復(fù)位,通過加裝信號隔離器解決問題。
建立預(yù)防性維護體系至關(guān)重要:定期清潔PLC散熱風(fēng)扇,防止灰塵堆積影響散熱;備份程序參數(shù)并實施版本管理;對關(guān)鍵設(shè)備實施冗余配置(如雙電源模塊)。統(tǒng)計表明,80%的PLC故障可通過定期維護避免。建議每半年進行一次系統(tǒng)點檢,包括接地電阻測試(要求<4Ω)、后備電池電壓檢測等。
隨著技術(shù)進步,現(xiàn)代PLC已集成更強大的診斷功能。如羅克韋爾ControlLogix的FactoryTalk Analytics模塊能預(yù)測設(shè)備潛在故障,而西門子TIA Portal的拓撲識別功能可自動檢測網(wǎng)絡(luò)配置錯誤。掌握這些智能診斷工具將大幅提升運維效率。
通過以上四個維度的系統(tǒng)化測試,技術(shù)人員能夠快速定位PLC故障根源。在實際操作中,需堅持"先外圍后核心、先簡單后復(fù)雜"的原則,結(jié)合理論分析與實踐經(jīng)驗,才能有效保障自動化控制系統(tǒng)的穩(wěn)定運行。
審核編輯 黃宇
-
傳感器
+關(guān)注
關(guān)注
2564文章
52788瀏覽量
765298 -
plc
+關(guān)注
關(guān)注
5031文章
13844瀏覽量
473191 -
電源模塊
+關(guān)注
關(guān)注
33文章
1895瀏覽量
94308
發(fā)布評論請先 登錄
用于 GSM/ GPRS (824-915 MHz) (1710-1910 MHz) 的 Tx-Rx 四頻前端模塊,帶四個線性 TRx 開關(guān)端口 skyworksinc
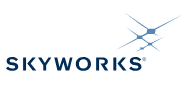
用于 GSM/GPRS (824-915 MHz) (1710-1910 MHz) 的 Tx-Rx 四頻前端模塊,帶四個線性 TRx 開關(guān)端口 skyworksinc
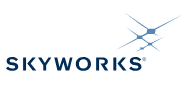
用于四頻 GSM / GPRS / EDGE 的 Tx-Rx FEM,具有四個線性 TRx 開關(guān)端口和雙頻 TD-SCDMA skyworksinc
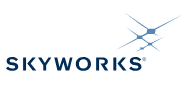
PLC應(yīng)用技巧,輕松解決PLC故障
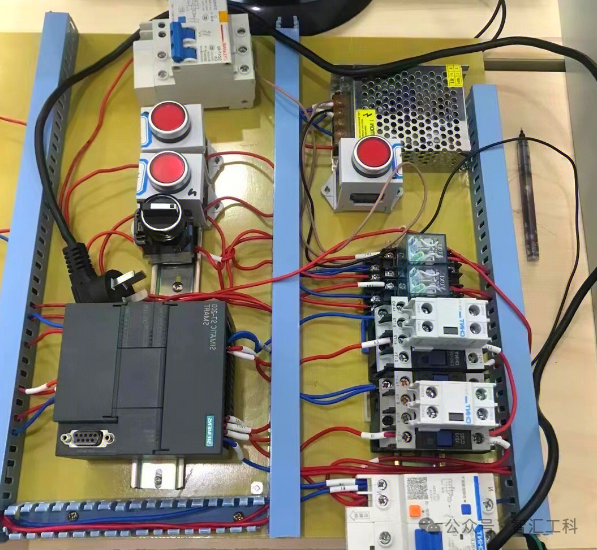
評論