在航空發動機關鍵部件制造中,復雜曲面工件的高精度打磨對定位技術提出了極高要求。本文基于中國科學院沈陽自動化研究所等單位的科研成果,詳細解析 “激光位移測量機器人自動定位打磨系統” 的工程實施過程,涵蓋從硬件搭建、算法開發到現場驗證的全流程技術要點。
一、系統硬件平臺搭建:構建精密測量與加工基礎
(一)核心硬件配置與集成
工業機器人系統
選用 KUKA KR600 R2830 六軸機器人(重復定位精度 ±0.08mm,負載 600kg),末端通過定制剛性連接裝置(剛度≥50N/μm)安裝LTP150 激光位移傳感器(量程 ±40mm,重復精度 1.2μm)。傳感器采用 M12 17 芯接插件與機器人控制柜通信,支持 TCP/IP 和 RS485 雙模式,確保高速數據傳輸(采樣頻率 50kHz)。
工件定位工裝
設計三工位精密旋轉工作臺(定位精度 ±5″),臺面均布 3 組伺服驅動定位夾緊滑塊(行程 ±20mm,分辨率 1μm),每個滑塊集成氣動吸盤(吸力≥500N)和高精度直線導軌(直線度 ±5μm/m)。滑塊呈 120° 對稱分布,通過三角形幾何約束實現工件徑向(X/Y 軸)和角向(θ 軸)的解耦調整。
輔助設備集成
配置快換工具系統(換刀時間≤15 秒),支持傳感器與砂帶機工具頭(接觸力控制 ±5N)的自動切換。
搭建工控機控制柜,集成西門子 PLC(CPU 1516TF-3 PN/DP)和研華工業主板,通過 EtherCAT 總線同步控制機器人、旋轉臺及滑塊伺服電機(控制周期≤1ms)。
(二)硬件標定與坐標系對齊
傳感器外參標定
使用三坐標測量機(精度 ±1μm)采集傳感器測量坐標系與機器人基坐標系的轉換關系,通過九點法標定求解旋轉矩陣 R(誤差≤0.01°)和平移向量 T(誤差≤20μm),建立公式:P基坐標?=R?P傳感器?+T
工作臺基準校準
通過激光跟蹤儀(精度 ±5μm)測量旋轉工作臺中心,調整其與機器人基坐標系的 Z 軸同軸度(偏差≤±10μm),確保工件旋轉中心與理論加工坐標系對齊。
二、軟件系統開發:從數據采集到智能控制
(一)測量分析軟件核心模塊
數據采集模塊
支持 “機器人聯動掃描” 與 “定點觸發采樣” 兩種模式,針對回轉體工件設計螺旋線掃描路徑(層間距 0.5mm,采樣點密度 1 點 /°),避免型面干涉。
集成噪聲濾波算法:對原始測量數據(含高斯噪聲 σ=5μm)進行中值濾波(窗口大小 5×5)和滑動平均(n=10),確保有效數據信噪比≥40dB。
偏差計算模塊
徑向偏差求解:采用 Kasa 迭代擬合算法,將圓周等分點(n≥72)的極坐標數據(θ?, δ?)轉換為平面坐標(X?, Y?),通過最小二乘法擬合圓心(Xc, Yc),計算公式如下:{Xi?=(R+δi?)cosθi?Yi?=(R+δi?)sinθi??
擬合精度通過殘差平方和(SSE≤10μm2)實時驗證。
角向偏差檢測:在工件基準點(如 0° 位置)設置定位銷塊,傳感器沿切線方向測量實際與理想銷塊的弦長差 λ,通過 φ=λ/R(R 為工件半徑)計算角向偏差,分辨率達 0.0001°。
運動控制模塊
基于三角形幾何關系推導三滑塊移動量:????M1?=Xc?tan30°?Yc?M2?=M1?/sin30°?Xc?/cos30°M3?=M1?/sin30°+Xc?/cos30°?
采用 “先退后進” 策略(滑塊先退回 5mm 釋放空間,再按計算量移動),避免調整過程中工件與夾具干涉。
(二)控制軟件流程設計
全自動定位流程(圖 1):
工件型號輸入 → 工裝預定位(滑塊移動至理論位置) → 機器人掃描圓周特征(72點,耗時120s) → 偏差計算(徑向ΔX/ΔY、角向φ) → 滑塊自動調整(單軸運動速度5mm/s,調整時間≤90s) → 二次測量驗證(精度達標則進入加工,否則重復調整)
安全機制:
設置硬件限位(滑塊行程 ±20mm)和軟件閾值(徑向偏差 > 1mm 或角向偏差 > 0.5° 時報警)。
傳感器集成激光關閉功能,避免加工階段(砂帶機工作時)的粉塵干擾,通過外部 IO 信號實現 “測量 - 加工” 模式切換。
三、關鍵實施步驟:從實驗室到生產線
(一)典型工件預處理
以某型發動機鈦合金機匣(直徑 350mm,葉片型面曲率半徑 20-100mm)為例:
毛坯定位:通過工件三維數模生成初始定位點云,導入測量軟件生成預掃描路徑。
夾具適配:根據工件外形定制定位銷塊(材料為硬質鋁合金,表面粗糙度 Ra≤0.4μm),確保傳感器測量光束垂直于銷塊切線方向(角度偏差≤±1°)。
(二)仿真驗證與參數優化
構建含 10mm 徑向偏差和 1° 角向偏差的虛擬工件,模擬傳感器掃描過程,注入高斯噪聲(σ=2μm)和溫度漂移(ΔT=10℃,補償量 8μm)。
結果:徑向定位誤差從 ±10mm 降至 ±8μm,角向偏差檢測誤差≤±0.0002°,驗證算法魯棒性。
實際加工參數調試:
打磨工具:選用 60# 砂帶(接觸輪直徑 50mm,硬度邵氏 80A),加工速度 800mm/s,接觸壓力 30N(通過力傳感器實時反饋調整)。
路徑規劃:針對葉片前緣(曲率半徑 25mm)采用五軸聯動插補,步長 0.2mm,確保刀軸矢量與型面法向夾角≤15°,避免過切。
(三)現場加工與精度閉環
首件調試流程:
測量階段:機器人以 50mm/s 速度掃描工件外圓,采集 72 個點(耗時 120s),生成偏差報告(圖 2)。
調整階段:三滑塊同步運動(最大位移 12mm),調整后二次測量顯示徑向偏差從 + 0.32mm/-0.28mm 降至 + 0.015mm/-0.012mm,角向偏差從 + 0.8° 降至 + 0.0012°。
加工階段:砂帶機按修正后的加工程序(角向補償 - 0.0012°)打磨,單次加工時間 5.5 小時,較人工打磨效率提升 45%。
精度檢測與反饋:
使用 ZEISS 三坐標測量機對 10 個關鍵型面點進行檢測,結果顯示:
徑向尺寸公差從 ±0.3mm 縮至 ±0.015mm,滿足設計要求(±0.02mm)。
表面粗糙度 Ra 從 1.2μm 降至 0.18μm,達到航空部件鏡面打磨標準(Ra≤0.2μm)。
四、實施難點與解決方案
(一)復雜型面測量干涉問題
問題:葉片根部等凹腔區域易遮擋傳感器光束,導致數據缺失。
方案:開發自適應路徑規劃算法,根據工件三維模型預計算傳感器視角,在遮擋區域自動增加測量點(密度提升至 2 點 /°),并通過曲面擬合補全缺失數據(補點誤差≤±5μm)。
(二)加工現場環境干擾
問題:打磨粉塵(粒徑≤5μm)和機床振動(振幅≤10μm)影響測量精度。
方案:
傳感器集成氣簾保護裝置(氣壓 0.3MPa),實時吹掃鏡頭表面粉塵。
采用動態濾波算法,在振動頻率(55Hz)處設置陷波濾波器,將振動噪聲影響降低 90% 以上。
(三)多工位快速切換
問題:不同型號工件定位銷塊位置差異大,傳統手動切換耗時(≥30 分鐘)。
方案:建立工件參數數據庫,包含各型號的定位點坐標、滑塊初始位置、傳感器掃描路徑等,通過掃碼槍讀取工件二維碼自動加載對應參數,切換時間縮短至 8 分鐘。
五、實施效果與工程價值
(一)核心技術指標
項目 | 實施前(人工定位) | 實施后(系統自動定位) | 提升幅度 |
---|---|---|---|
徑向定位精度 | ±0.5mm | ±15μm | 33 倍 |
角向定位精度 | ±1° | ±0.001° | 1000 倍 |
單工件加工時間 | 8-10 小時 | 5.5 小時 | 45% |
產品良率 | 85% | 98% | 15% |
(二)工程應用意義
打破技術壁壘:突破國外對復雜曲面精密加工設備的壟斷,實現航空關鍵部件打磨技術的自主可控。
柔性制造支撐:通過參數化配置,兼容多型號工件(直徑 100-500mm,曲率半徑≥10mm),滿足航空發動機小批量多品種的生產需求。
質量追溯體系:測量與加工數據實時存檔(存儲周期≥5 年),支持 ISO 26262 功能安全標準,為航空部件全生命周期管理提供數據基礎。
六、總結與展望
本系統的實施過程深度融合了激光測量、機器人控制、精密機械設計等多學科技術,通過 “測量 - 計算 - 調整 - 加工” 的全閉環控制,解決了航空復雜曲面工件的定位難題。未來可進一步拓展以下方向:
多傳感器融合:集成視覺傳感器(檢測表面缺陷)和超聲傳感器(測量壁厚),構建全要素檢測加工一體化系統。
數字孿生應用:通過實時采集的工件位置數據,在虛擬空間鏡像加工過程,提前預測定位誤差并優化調整策略。
無人化生產線:與 AGV 物流系統、智能倉儲對接,實現從工件上料、定位、加工到檢測的全流程無人化操作,推動航空制造向智能化轉型。
審核編輯 黃宇
-
機器人
+關注
關注
212文章
29303瀏覽量
211003 -
激光
+關注
關注
20文章
3389瀏覽量
65653
發布評論請先 登錄
【「# ROS 2智能機器人開發實踐」閱讀體驗】視覺實現的基礎算法的應用
【啟揚方案】基于RK3588的建筑測量機器人應用解決方案
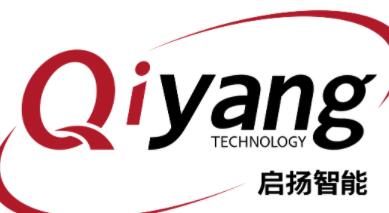
【「具身智能機器人系統」閱讀體驗】2.具身智能機器人的基礎模塊
【「具身智能機器人系統」閱讀體驗】2.具身智能機器人大模型
【「具身智能機器人系統」閱讀體驗】+初品的體驗
《具身智能機器人系統》第1-6章閱讀心得之具身智能機器人系統背景知識與基礎模塊
三坐標測量機應用領域 三坐標測量機與激光測量的區別
RK3588高性能處理器助力測量機器人精準作業
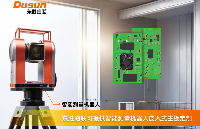
開源項目!用ESP32做一個可愛的無用機器人
復雜工件的高效測量方案:自動化三坐標測量與影像測量技術集成
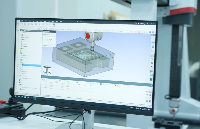
評論