在工業(yè)自動化控制系統(tǒng)中,多臺變頻器按比例運行是常見的需求,例如在輸送帶系統(tǒng)、風機群控或水泵并聯(lián)等場景中。傳統(tǒng)方案通常依賴比例給定器(如電位器或?qū)S?a target="_blank">信號分配器)來實現(xiàn)主從設備的頻率分配,但這類硬件存在成本高、接線復雜、易受干擾等缺點。本文將深入探討三種無需專用比例給定器的替代方案,并結(jié)合實際應用場景分析其技術原理與實施要點。
一、基于模擬量信號的主從控制方案
(技術原理)
通過PLC或DCS系統(tǒng)輸出1路公共模擬量信號(如0-10V或4-20mA)并聯(lián)至所有變頻器,利用變頻器內(nèi)部參數(shù)實現(xiàn)比例分配。以三臺變頻器按50%:30%:20%運行為例:
1. 主變頻器(50%)直接接收模擬量信號,參數(shù)設置為100%基準。
2. 從機1(30%)通過"頻率增益"參數(shù)設置為60%(30/50=0.6)。
3. 從機2(20%)設置增益為40%(20/50=0.4)。
(實施要點)
1. 需選用支持模擬量信號增益調(diào)節(jié)的變頻器(如西門子G120、ABB ACS880)。
2. 信號傳輸建議采用屏蔽雙絞線,末端加250Ω電阻抗干擾。
3. 動態(tài)響應測試時需驗證階躍信號下的同步性,延遲應<100ms。
(典型案例)
某水泥廠原料輸送帶系統(tǒng)采用此方案,通過4-20mA信號控制5臺變頻器,比例精度達到±2%,節(jié)省了3萬元硬件成本。
二、基于通信總線的數(shù)字分配方案
(協(xié)議選擇)
采用PROFIBUS-DP、Modbus RTU或CANopen等現(xiàn)場總線,通過通信報文直接下發(fā)各變頻器的目標頻率。以Modbus RTU為例:
1. PLC周期性地發(fā)送多播指令(如功能碼16)。
2. 各變頻器根據(jù)站號解析預設的比例系數(shù)。
3. 支持動態(tài)比例調(diào)整,修改寄存器值即可改變分配比例。
(參數(shù)配置示例)
從站1(主設備):
● 站號=1,頻率基準值1000(對應50Hz)。
從站2:
● 站號=2,比例系數(shù)=0.3(30%)。
從站3:
● 站號=3,比例系數(shù)=0.2(20%)。
(優(yōu)勢分析)
● 比例精度可達±0.5%,支持在線動態(tài)調(diào)整。
● 省去模擬量信號衰減問題,傳輸距離可達1200m(RS485)。
● 某污水處理項目實測顯示,通信方案比模擬量方案節(jié)能8%。
三、基于頻率跟隨的級聯(lián)控制方案
(工作原理)
第一臺變頻器采用速度控制模式,后續(xù)設備設置為"速度跟隨"模式:
2. 從機通過AO端子采集主機實際輸出頻率。
3. 在從機參數(shù)中設置"外部頻率修正系數(shù)"。
(參數(shù)設置關鍵點)
● 安川GA700需設置H4-01=3(主速度跟隨)。
● 臺達VFD-EL系列配置09-00=05(比例追蹤模式)。
● 需啟用速度環(huán)PID調(diào)節(jié)(參數(shù)C5-01~C5-05)。
(注意事項)
● 級聯(lián)層數(shù)建議不超過4級,避免累積誤差。
● 需在從機增加0.5Hz的死區(qū)補償,防止震蕩。
● 某造紙機械應用案例顯示,該方案同步誤差<0.3Hz。
四、技術方案對比與選型建議
方案類型 | 成本 | 精度 | 動態(tài)響應 | 適用場景 |
模擬量增益 | 低 | ±2% | 中等 | 固定比例、短距離控制 |
通信總線 | 中 | ±0.5% | 快 | 需頻繁調(diào)整比例的系統(tǒng) |
頻率跟隨 | 較低 | ±1% | 較慢 | 主從明確的級聯(lián)設備 |
(特殊場景解決方案)
對于需要比例動態(tài)切換的場合(如紡織機械張力控制),推薦采用"通信總線+PLC在線計算"的組合方案:
2. 根據(jù)負載變化自動調(diào)整比例系數(shù)。
3. 通過EtherCAT總線實現(xiàn)μs級同步。
五、實施中的常見問題與對策
1. 信號干擾問題
● 現(xiàn)象:模擬量方案出現(xiàn)頻率波動。
● 對策:增加信號隔離器(如魏德米勒MACX-AX)。
2. 比例失調(diào)故障
● 案例:某包裝線因從機參數(shù)丟失導致比例錯誤
● 預防:啟用變頻器參數(shù)自動備份功能
3. 緊急同步方案
● 配置硬件應急電路:當通信中斷時,通過DI端子切換至預設固定比例
通過上述方案的實施,用戶可顯著降低系統(tǒng)復雜度。某汽車焊裝車間的實際數(shù)據(jù)表明,采用通信總線方案后,設備調(diào)試時間縮短了60%,維護成本降低45%。未來隨著工業(yè)物聯(lián)網(wǎng)發(fā)展,基于云平臺的動態(tài)比例優(yōu)化將成為新的技術方向。
審核編輯 黃宇
-
變頻器
+關注
關注
253文章
6840瀏覽量
149277 -
定器
+關注
關注
0文章
2瀏覽量
1681
發(fā)布評論請先 登錄
如何實現(xiàn)PC對多臺TD3000變頻器的實時監(jiān)控?
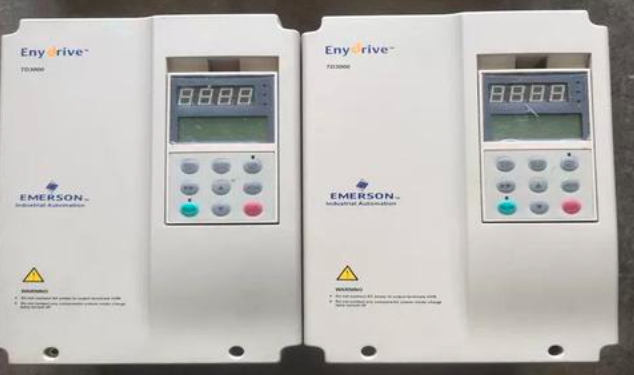
變頻器參數(shù)的電流環(huán)與速度環(huán)調(diào)節(jié)方法
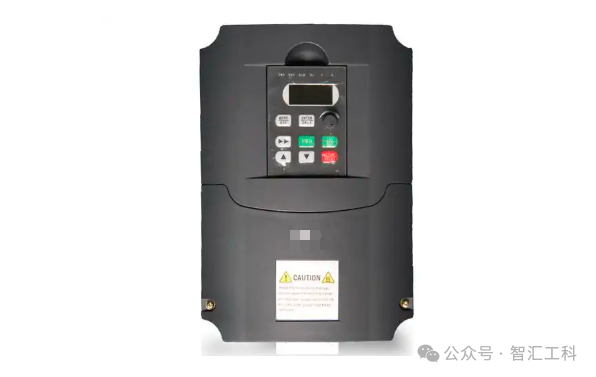
如何實現(xiàn)變頻器與負載的匹配?
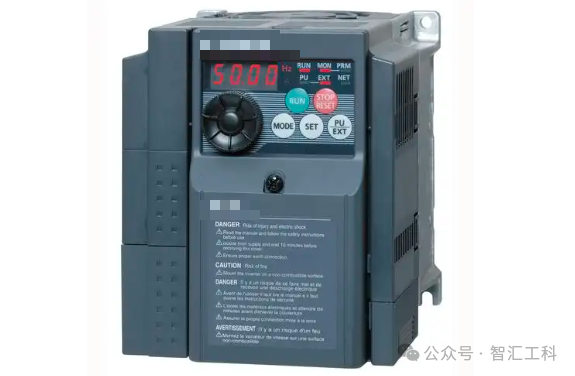
為什么需要變頻器?如何調(diào)節(jié)變頻器速度?
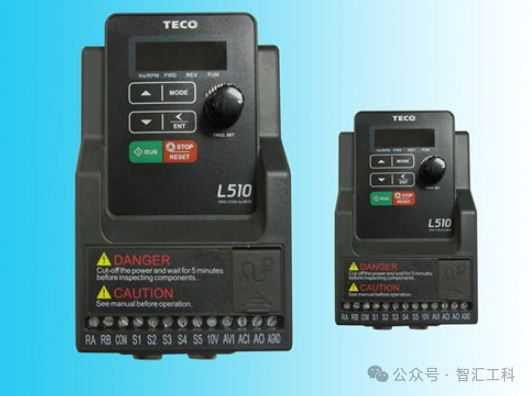
變頻器的頻率給定方式有幾種?
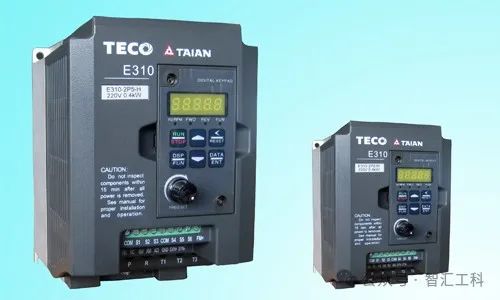
評論