加減速控制是CNC 系統(tǒng)的關(guān)鍵技術(shù)之一,也是實(shí)現(xiàn)數(shù)控系統(tǒng)高實(shí)時性的瓶頸。在CNC裝置中,為了保證機(jī)床在啟動或停止時不產(chǎn)生沖擊、失步、超程或振蕩,必須對進(jìn)給電機(jī)的脈沖頻率或電壓進(jìn)行加減速控制。即在機(jī)床加速啟動時,保證加在電機(jī)上的脈沖頻率或電壓逐漸增加;而當(dāng)機(jī)床減速停止時。保證加在電機(jī)上的脈沖頻率或電壓逐漸減小。好的加減速控制算法除了應(yīng)保證數(shù)控機(jī)床運(yùn)動平穩(wěn),在啟停和程序段間速度有變化時不產(chǎn)生失步、超程、沖擊和振蕩外;還應(yīng)當(dāng)具有算法簡單、系統(tǒng)加減速處理時間短、實(shí)時性強(qiáng)的特點(diǎn)。此外,很好的柔性(通用性)也是必要的,以便適應(yīng)不同配置的機(jī)床,特別是在高速加工中,這顯得尤為重要。
1 加減速控制方法
1.1 直線加減速控制方法
直線加減速控制方法是加減速控制方法中最為簡單的一種,也是最常用的一種。數(shù)控系統(tǒng)每插補(bǔ)一次,都要進(jìn)行穩(wěn)定速度、瞬時速度和加減速處理。整個過程共有加速、勻速、減速三個階段。
1.2 S 曲線加減速控制方法
直線加減速啟動和加減速結(jié)束時存在加速度突變,產(chǎn)生沖擊,因而不適合用于高檔的數(shù)控系統(tǒng)。一些先進(jìn)的CNC 系統(tǒng)采用S 形加減速,通過對啟動階段即高速階段的加速度衰減,來保證電機(jī)性能的充分發(fā)揮和減小啟動沖擊。正常情況下S 曲線加減速的運(yùn)行過程可分為7段:加加速段、勻加速段、減加速段、勻速段、加減速段、勻減速段、減減速段。
1.3 四次曲線加減速控制方法
是一種四次位移曲線,三次速度曲線的加減速控制方法。非常實(shí)用于高檔的數(shù)控系統(tǒng)上,具有算法簡單,柔性好的優(yōu)點(diǎn),是一種值得推廣的加減速模式。
2 四次位移曲線加減速系統(tǒng)總體結(jié)構(gòu)與組成
2.1 系統(tǒng)硬件結(jié)構(gòu)
本數(shù)控系統(tǒng)采用通用PC 機(jī)和單片機(jī)構(gòu)成的主從式二級控制總體結(jié)構(gòu),系統(tǒng)硬件組成如圖1 所示,上位機(jī)采用通用PC 機(jī),完成系統(tǒng)參數(shù)的設(shè)置、加工數(shù)據(jù)的實(shí)時計算和仿真等任務(wù),而下位單片機(jī)系統(tǒng)完成不同方向的進(jìn)給驅(qū)動控制,并從外部機(jī)器上獲取加工狀態(tài)的反饋信息,上、下位機(jī)間以中斷方式進(jìn)行串行通信。
圖1 硬件系統(tǒng)結(jié)構(gòu)框圖
下位機(jī)系統(tǒng)能根據(jù)主機(jī)命令,獨(dú)立完成全部數(shù)控功能,基于單片機(jī)技術(shù)設(shè)計的速度位置控制單元,用于同時對三軸((x, Y, z 向)電機(jī)進(jìn)行多功能的控制。速度位置控制單元采用Winbond78E58 作為主控芯片。整個電路主要由開關(guān)量輸入控制電路、脈沖控制電路及通訊電路等組成。脈沖控制電路由三個定時/計數(shù)器8254 來實(shí)現(xiàn)對三個驅(qū)動電機(jī)的位置及速度控制。當(dāng)前加工軌跡段運(yùn)行完畢后可向主機(jī)申請中斷,78E58 也可通過查詢中斷的方式獲得當(dāng)前運(yùn)行狀態(tài)。開關(guān)量輸入電路可檢測限位開關(guān)、對刀儀等狀態(tài),并向78E58 申請中斷。
2.2 系統(tǒng)軟件結(jié)構(gòu)
根據(jù)數(shù)控機(jī)床的功能控制要求,并結(jié)合圖1 硬件總體結(jié)構(gòu),本數(shù)控系統(tǒng)的系統(tǒng)軟件,由PC 系統(tǒng)控制軟件和驅(qū)動接口卡軟件兩大部分組成,它們之間相互獨(dú)立,如圖2 所示。其中PC 機(jī)上的系統(tǒng)控制軟件采用面向?qū)ο蟮?a target="_blank">編程技術(shù)((OOP)、由高級編程語言Visual C++編制而成,各個功能模塊被獨(dú)立地封裝在不同的對象中,系統(tǒng)具有良好的擴(kuò)充性和可移植性。驅(qū)動卡上的軟件部分由匯編語言編制而成。
PC 系統(tǒng)控制軟件負(fù)責(zé)整個系統(tǒng)的綜合管理、人機(jī)交互和數(shù)據(jù)處理等工作。具體由以下幾部分組成:人機(jī)接口部分、數(shù)據(jù)處理軟件部分、工作模式控制軟件部分、通信部分、診斷部分和聯(lián)機(jī)幫助系統(tǒng)軟件部分,各個部分各自包含一些獨(dú)立的功能模塊。其中,人機(jī)接口部分用于管理機(jī)床參數(shù)、提供NC 程序全屏幕編輯窗口并且可以在加工過程中動態(tài)顯示機(jī)床加工狀態(tài),以實(shí)現(xiàn)用戶與系統(tǒng)之間的信息交互。數(shù)據(jù)處理軟件部分用于對NC 程序進(jìn)行語法檢查和譯碼,間隙補(bǔ)償、加減速控制和插補(bǔ)運(yùn)算等強(qiáng)實(shí)時功能。工作模式控制軟件部分提供各種常見的工作模式控制,協(xié)調(diào)控制機(jī)床實(shí)時運(yùn)動,并實(shí)現(xiàn)動態(tài)圖形仿真功能。通信軟件部分用于實(shí)現(xiàn)PC 機(jī)和接口卡之間的雙向串行數(shù)據(jù)通信,保證數(shù)據(jù)通訊暢通。診斷軟件部分可以在系統(tǒng)工作過程中隨時發(fā)現(xiàn)系統(tǒng)故障、并指示故障類型,以實(shí)現(xiàn)在線診斷功能,保證系統(tǒng)正常運(yùn)行。聯(lián)機(jī)幫助系統(tǒng)提供聯(lián)機(jī)幫助功能。
圖2 系統(tǒng)軟件的組成圖
接口卡軟件接收計算機(jī)發(fā)送的加工信息,驅(qū)動電機(jī)完成刀具幾何位置及運(yùn)動速度的控制,并且反饋加工信息。PC 機(jī)和接口卡之間通過RS-232C 接口,按照自行定義的通信協(xié)議,以中斷機(jī)制實(shí)現(xiàn)具體功能的數(shù)據(jù)傳輸。整個系統(tǒng)已通過與驅(qū)動器和電機(jī)的聯(lián)機(jī)調(diào)試,取得了符合要求的控制效果。該系統(tǒng)的運(yùn)行過程分為以下幾步:
2.2.1 開啟計算機(jī),運(yùn)行本系統(tǒng)控制軟件,檢測下位機(jī)的連接狀態(tài)是否正常,如異常會出現(xiàn)提示對話框。軟件啟動時,計算機(jī)上首先顯示啟動畫面,隨后便可進(jìn)入系統(tǒng)控制界面。
2.2.2 設(shè)定或復(fù)位相關(guān)的系統(tǒng)參數(shù)后,可進(jìn)行輔助加工工作:手動控制、回機(jī)械零點(diǎn)、對刀、碰邊對中((1/2 功能)及各方向置零、溫機(jī)等。
2.2.3 讀入加工代碼文件,前臺還原顯示加工路徑文件描述的圖形,可檢查加工的工件是否超過出了工作臺面的范圍,后臺解釋該文件,提取出數(shù)控命令和數(shù)控數(shù)據(jù),將其存儲在約定的數(shù)據(jù)結(jié)構(gòu)中,以供后續(xù)加工重復(fù)使用。
2.2.4 選擇不同加工方式:自動、模擬、選段。加工時,系統(tǒng)實(shí)時跟蹤加工過程及顯示加工進(jìn)程中相關(guān)信息。另外在不關(guān)閉控制軟件的情況下,用戶可在計算機(jī)上操作其它軟件,不會影響系統(tǒng)的正常運(yùn)行。
2.2.5 加工過程中,可執(zhí)行急停和暫停命令。在暫停狀態(tài)下,可用手動控制任意移動主軸頭位置,不會影響繼續(xù)加工。在加工結(jié)束或急停后,自動將主軸頭Z 方向提升到安全高度。
2.3 工作過程
本系統(tǒng)共使用了三種加減速控制方法,分別是直線加減速、四次曲線加減速、S 曲線加減速。可以任意選擇一種加減速方式來進(jìn)行實(shí)際加工,同時可根據(jù)實(shí)際情況,調(diào)整相應(yīng)的參數(shù)使加工效果更趨于理想。
3 四次位移曲線加減速系統(tǒng)的實(shí)驗(yàn)及結(jié)果分析
為了驗(yàn)證微線段軌跡加工的實(shí)際效果,設(shè)計了三種插補(bǔ)器,一種是傳統(tǒng)的直線插補(bǔ)器,一種是具有微線段終點(diǎn)控制算法的直線插補(bǔ)器,最后一種是具有微線段插補(bǔ)終點(diǎn)控制算法的四次曲線插補(bǔ)器。對最具代表性的圓弧進(jìn)行了實(shí)際加工,由于篇幅所限,圓弧的代碼段不顯示了,讀者需要請與作者聯(lián)系。
圖3 是經(jīng)過傳統(tǒng)直線插補(bǔ)器插補(bǔ)后的理論曲線和實(shí)際加工曲線,由于速度變換頻繁,加工過程不穩(wěn)定,從圖中可以看到在實(shí)際加工曲線中有微小的鋸齒型誤差存在。加工時間為2.960s。
圖3 采用傳統(tǒng)直線插補(bǔ)器的加工實(shí)例
圖4 是經(jīng)過具有微線段終點(diǎn)控制算法的直線插補(bǔ)器插補(bǔ)后的理論曲線和實(shí)際加工曲線,從圖上可以看出理論曲線和實(shí)際加工曲線的差別已經(jīng)很小,同時基本保持一個較高的速度在運(yùn)行,在很短的線段內(nèi)甚至可以達(dá)到最高速度,運(yùn)行時間是1.704s。與上面的方法相比較,效率有很大的提高。
圖4 基于微線段終點(diǎn)控制算法的直線插補(bǔ)器加工實(shí)例
圖5 是經(jīng)過具有微線段插補(bǔ)終點(diǎn)控制算法的四次曲線插補(bǔ)器插補(bǔ)出來的,實(shí)際加工曲線和理論加工曲線已經(jīng)很逼近,同時速度基本上保持以較大值運(yùn)行。運(yùn)行時間是1.820s,雖然加工時間比基于微線段插補(bǔ)終點(diǎn)算法的直線插補(bǔ)器稍微慢一些,但它的柔性和平穩(wěn)性卻是最好的。
圖5 四次曲線插補(bǔ)器加工實(shí)例
4 學(xué)術(shù)價值和創(chuàng)新點(diǎn)
由以上實(shí)驗(yàn)數(shù)據(jù)結(jié)果表明,四次位移曲線加減速系統(tǒng)在加減速、定位、微線段插補(bǔ)終點(diǎn)控制等方面都取得了良好的效果。與傳統(tǒng)的數(shù)控系統(tǒng)相比,性能得到很大的改善。好的加減速算法要求進(jìn)給過程中速度變化盡可能平穩(wěn),即要求系統(tǒng)加減速具有高度的柔性,同時程序復(fù)雜度要較小。傳統(tǒng)的直線加減速在進(jìn)給過程中存在柔性沖擊,而S 曲線加減速程序分為很多段,變化復(fù)雜,實(shí)現(xiàn)起來有比較大的困難。而四次曲線加減速具有算法簡單,柔性好的優(yōu)點(diǎn),是一種值得推廣的加減速模式。
-
單片機(jī)
+關(guān)注
關(guān)注
6067文章
44991瀏覽量
650427 -
CAN
+關(guān)注
關(guān)注
57文章
2920瀏覽量
467793 -
數(shù)控系統(tǒng)
+關(guān)注
關(guān)注
5文章
264瀏覽量
24944
發(fā)布評論請先 登錄
基于四次位移曲線的CNC數(shù)控系統(tǒng)的研究
基于四次位移曲線的CNC數(shù)控系統(tǒng)的研究
基于四次位移曲線的CNC 數(shù)控系統(tǒng)的研究
CNC數(shù)控系統(tǒng)加減速控制方法研究與實(shí)現(xiàn)
數(shù)控系統(tǒng)加減速的實(shí)現(xiàn)方法
數(shù)控系統(tǒng)參數(shù)曲線、曲面插補(bǔ)算法及加減速控制研究
基于五次位移加減速的NURBS實(shí)時插補(bǔ)技術(shù)研究
解析四次位移曲線的CNC數(shù)控系統(tǒng)的研究
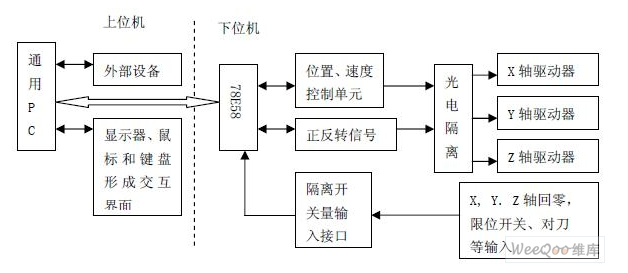
評論