最簡便實用的散熱裝置就是散熱器。一個有許多葉片的散熱器或一個面積較大的散熱板都會大大增加散熱面積,給熱的傳導、對流和輻射都會帶來很大的方便。就理論而言,卞介面積無
2012-03-19 10:29:47
2388 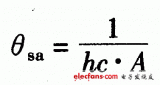
散熱器非常重要!作為電路設計的一個重要方面,散熱器提供了一種有效的途徑,將熱量從電子器件(如 BJT、MOSFET 和線性穩壓器)傳遞出去并散發到周圍空氣中。
2019-09-02 13:46:58
10210 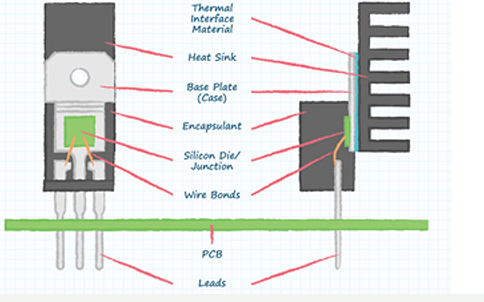
EAK為設計工程師提供了一種開放式屏蔽基板器件,用于需要卓越熱性能的應用,開發了一種額定功率高達 50W 的厚膜功率電阻器。該電阻器采用 TO-220 開放式屏蔽基板封裝,并具有與基板粘合的絕緣錐形
2024-03-18 08:21:47
IRAUDAMP22,雙通道,50W(2歐姆)半橋D類音頻功率放大器,使用IR4322。 IRAUDAMP22參考設計是一個雙通道,50W / ch(無散熱片)/ 100W / ch(帶散熱片)半橋
2020-08-26 15:17:17
;輸出恒流驅動 LED 的功率從 0.1W~50W 全系列;LED 模組可以串聯,并聯,串并聯結合等多種連接方式;電路拓樸支持降壓,升壓,升降壓等多種結構;可以實現多領域多條件下的 LED恒流
2016-02-19 14:56:33
;輸出恒流驅動 LED 的功率從 0.1W~50W 全系列;LED 模組可以串聯,并聯,串并聯結合等多種連接方式;電路拓樸支持降壓,升壓,升降壓等多種結構;可以實現多領域多條件下的 LED恒流
2016-02-24 15:30:59
;輸出恒流驅動 LED 的功率從 0.1W~50W 全系列;LED 模組可以串聯,并聯,串并聯結合等多種連接方式;電路拓樸支持降壓,升壓,升降壓等多種結構;可以實現多領域多條件下的 LED恒流
2016-02-29 15:07:40
;輸出恒流驅動 LED 的功率從 0.1W~50W 全系列;LED 模組可以串聯,并聯,串并聯結合等多種連接方式;電路拓樸支持降壓,升壓,升降壓等多種結構;可以實現多領域多條件下的 LED恒流
2016-03-07 13:40:27
;輸出恒流驅動 LED 的功率從 0.1W~50W 全系列;LED 模組可以串聯,并聯,串并聯結合等多種連接方式;電路拓樸支持降壓,升壓,升降壓等多種結構;可以實現多領域多條件下的 LED恒流
2016-03-11 15:58:32
;輸出恒流驅動 LED 的功率從 0.1W~50W 全系列;LED 模組可以串聯,并聯,串并聯結合等多種連接方式;電路拓樸支持降壓,升壓,升降壓等多種結構;可以實現多領域多條件下的 LED恒流
2016-03-15 13:01:45
;輸出恒流驅動 LED 的功率從 0.1W~50W 全系列;LED 模組可以串聯,并聯,串并聯結合等多種連接方式;電路拓樸支持降壓,升壓,升降壓等多種結構;可以實現多領域多條件下的 LED恒流
2016-03-23 14:20:24
;輸出恒流驅動 LED 的功率從 0.1W~50W 全系列;LED 模組可以串聯,并聯,串并聯結合等多種連接方式;電路拓樸支持降壓,升壓,升降壓等多種結構;可以實現多領域多條件下的 LED恒流
2016-03-28 15:28:12
;輸出恒流驅動 LED 的功率從 0.1W~50W 全系列;LED 模組可以串聯,并聯,串并聯結合等多種連接方式;電路拓樸支持降壓,升壓,升降壓等多種結構;可以實現多領域多條件下的 LED恒流
2016-04-06 13:24:25
;輸出恒流驅動 LED 的功率從 0.1W~50W 全系列;LED 模組可以串聯,并聯,串并聯結合等多種連接方式;電路拓樸支持降壓,升壓,升降壓等多種結構;可以實現多領域多條件下的 LED恒流
2016-04-11 13:17:46
;輸出恒流驅動 LED 的功率從 0.1W~50W 全系列;LED 模組可以串聯,并聯,串并聯結合等多種連接方式;電路拓樸支持降壓,升壓,升降壓等多種結構;可以實現多領域多條件下的 LED恒流
2016-04-22 09:38:32
市場追求的是高性價比,產品主要還是以風冷散熱器為主,水冷散熱器隨著價格的不斷下調,將占有越來越大的市場份額,隨著熱管散熱器的工藝成熟和成本控制,將是未來發展的熱門。
2019-09-30 09:01:41
現在在用一個CPU散熱器,可是它有三根線,紅黃黑,紅是電源,黑是地,黃色是什么線?信號線?輸入輸出?我搜過有不同的說法,有方法測一下嗎?
2014-08-07 19:35:06
DVRFD631-475,開發板是一種通用電路板,旨在簡化IXRFD631柵極驅動器的評估,并為電源電路開發提供構建模塊。 IXRFD631柵極驅動器出廠時已安裝在評估板上,并經過全面測試。電路板設計允許將驅動器和MOSFET連接到散熱器,這樣做可以將電路板組件用作接地參考的低側電源開關
2019-08-07 08:48:20
一種改進的熱效率與凸輪型安裝夾,不需要任何工具。夾子安全地將設備保持在散熱器上。陶瓷散熱器采用可焊引腳垂直安裝。該陶瓷體具有大的介電性能,從夾子到散熱體可達4kV。WC散熱器的熱阻降到8°C/W。散熱器
2018-11-06 16:22:08
25℃~+100℃ 換熱功率 50~1000w 熱 阻 ≤0.1 K/W 材 質 翅片材質:鋁;熱管材質:紫銅 外形結構 (3)產品性能測試圖例 圖1 熱管散熱器散熱功率模擬測試
2012-06-19 13:54:59
本帖最后由 電力電子2 于 2012-6-19 17:00 編輯
IGBT模塊散熱器產品介紹 (1)防爆電氣用熱管散熱器:專門為爆炸性氣體環境中的電氣設備用電力電子器件、功率模塊散熱而開發
2012-06-19 13:52:17
IGBT模塊散熱器產品介紹 (1)防爆電氣用熱管散熱器:專門為爆炸性氣體環境中的電氣設備用電力電子器件、功率模塊散熱而開發的新一代散熱產品。具有熱阻小、熱響應速度快、熱傳導迅速、冷熱源可分離、等溫
2012-12-12 21:01:48
IGBT模塊散熱器最基本的使用說明?! 、?依據裝置負載的工作電壓和額定電流以及使用頻率,選擇合適規格的模塊。用戶使用模塊前請詳細閱讀模塊參數數據表,了解模塊的各項技術指標;根據模塊各項技術參數
2012-06-19 11:38:41
的進展,形成了一個新的器件應用平臺。 2智能MOS柵IGBT模塊散熱器化 由于IGBT高頻性能的改進,可將驅動電路、保護電路和故障診斷電路集成在一起,制成智能功率模塊,一般情況下采用電壓觸發
2012-06-19 11:17:58
IGBT模塊散熱器的應用 隨著電力電子技術的快速發展,以及當前電子設備對高性能、高可靠性、大功率元器件的要求不斷提高,單位體積內的熱耗散程度越來越高,導致發熱量和溫度急劇上升。由于熱驅動
2012-06-20 14:58:40
端子?! 、?驅動端子需要焊接時,設備或電烙鐵一定要接地?! ?.選擇和使用 ?、?請在產品的最大額定值(電壓、電流、溫度等)范圍內使用,一旦超出最大額定值,可能損壞產品,特別是IGBT散熱器外加超出
2012-06-19 11:20:34
本帖最后由 電力電子2 于 2012-6-20 14:35 編輯
IGBT模塊散熱器選擇及使用原則 一、散熱器選擇的基本原則 1, 散熱器選擇的基本依據 IGBT散熱器選擇要綜合根據器件
2012-06-20 14:33:52
IGBT水冷散熱器IGBT熱管散熱器該產品具備以下質量優勢:1、產品美觀大方,安全可靠。采用優質的鋁合金材料,材質熱傳導性好,價格低廉,材料硬度強而且不易氧化。2、進一步優化散熱器水盒內部結構,在
2012-06-19 11:42:12
和觸發特性定性測試,請用專用測試儀或到廠商進行測定。 特別建議: 在重復使用IGBT模塊水冷散熱器時,應特別注意檢查其臺面是否光潔、平整,水腔內是否有水垢和堵塞,若出現了上述情況應予以更換。 文章來源:中國電力電子網-IGBT模塊散熱器 區熔單晶 陶瓷覆銅板
2012-06-20 14:50:14
高導熱塑料散熱器最近發展很快,高導熱塑料散熱器一種全塑料的散熱器,它的導熱系數比普通塑料高幾十倍,達2-9w/mk,具有優異的熱傳導、熱輻射能力;可應用于各種功率燈具的新型絕緣散熱材料,可廣泛
2017-09-19 10:36:57
DC-AC 50W逆變電源的設計與實現1、帶漢字液晶顯示;2、輸入直流電壓10-16V;3、輸出交流電壓12-24V可調;4、最大輸出功率50W;5、輸出頻率47Hz至63Hz可調。
2016-05-30 18:25:00
tms320c6457是否需要散熱器?如果需要請推薦一種與之比較配套的被動式散熱器。謝謝
2018-06-21 14:57:27
IGBT模塊散熱器的安裝 ① 散熱器應根據使用環境及模塊參數進行匹配選擇,以保證模塊工作時對散熱器的要求。 ?、?散熱器表面的光潔度應小于10mm,每個螺絲之間的平面扭曲小于10mm。為了減少
2012-06-19 11:40:53
從16754A LA板更換FPGA芯片散熱器有什么困難嗎?我已經(重新)應用了幾次導熱膏和散熱器用于普通GPU和CPU但是我想知道這些FPGA散熱器的外部/邊緣粘貼是否有些特殊膠水膏。 以上
2018-11-20 10:31:39
我司專業生產各種電源模塊散熱器,型材散熱器,散熱片,冷鍛散熱器!QQ:1720988358,手機:***
2016-04-01 09:35:45
請教各位高手給一張,可控LED電源原理圖 要50W到100W發熱量要小
2012-03-11 20:56:31
這種基于音頻電路的50W音頻放大器電路TDA1514能夠使用專用音頻IC和其他一些常見組件提供高音頻功率輸出。TDA1514
50W音頻放大器電路支持4或8歐姆負載,并且需要很少的外部元件
2023-09-08 16:47:21
作為電路設計的一個重要方面,散熱器提供了一種有效的途徑,將熱量從電子器件(如 BJT、MOSFET 和線性穩壓器)傳遞出去并散發到周圍空氣中。散熱器的作用是在發熱器件上形成更大的表面積,從而更有
2019-01-25 09:38:38
我正在使用c28085001散熱器和舊cpu風扇進行激光二極管散熱器組件的原型設計。我需要知道組件的散熱能力和尺寸,以便我知道我是否可以使用它。數據表會很有幫助。以上來自于谷歌翻譯以下為原文I am
2018-12-05 10:50:49
請教大牛怎么用LM3478設計50W DC-DC升降壓變換器了?
2021-04-14 06:20:55
Function): 公式1 代價函數 式中,W為代價權重;R為目標輸出變量?! ≥斎胱兞吭O定 在Input Variables選項卡中的Root Assembly下找到散熱器。(此組件的順序與PM中
2020-07-07 16:58:31
在脈沖能力和額定功率方面較厚膜電阻有一定提高。無論是厚膜技術還是薄膜技術的,在連續高功率下運行時一定要配合合適的散熱器,90%以上的的故障均源自散熱器適配問題。下文就開步電子生產的50W額定功率
2019-04-26 11:55:56
電子產品設計中,如何選擇散熱器,要做哪些方面的考量
2019-05-13 07:55:01
作為電路設計的一個重要方面,散熱器提供了一種有效的途徑,將熱量從電子器件(如 BJT、MOSFET 和線性穩壓器)傳遞出去并散發到周圍空氣中。利用器件應用中的熱數據并結合散熱器供應商提供的規格,對散熱器的選擇問題進行選擇。
2019-02-18 10:25:51
現在大家用的筆記本散熱器底座大都是一直不停運轉的(不管筆記本的溫度高還是低),這樣的話,不但浪費了電量,還會增加筆記本運行負載,縮短了筆記本的使用壽命
2013-11-12 12:50:51
與LED燈珠板密切組合的散熱器來導出熱量。散熱器必須具備熱傳導、熱對流、熱輻射的功能。任何散熱器,除了要能快速地把熱量從發熱源傳導到散熱器的表面,最主要的還是要靠對流和輻射把熱量散發到空氣中去。導熱只解決了
2018-01-17 17:38:24
PCB背面的過孔,使用紅色圈起來了,安裝鋁散熱器的時候,
不擔心散熱器和過孔里面的電信號短路嗎? 如何保證絕緣的?
2023-11-16 08:02:28
你好呀我計劃使用 EVAL6498L 來構建具有同步整流功能的升壓 DC-DC 轉換器。我注意到,如果我安裝兩個 TO-220 開關,它們會非常靠近,因此我不確定我可以使用什么散熱器,因為如果我
2023-01-06 06:00:52
利用555定時器設計一個12V 50W的調速雨刮器,電路圖如何設計
2018-12-24 10:25:28
CPU散熱器選擇誤區一:越大的風扇就越好? 不同散熱器有不同尺寸的風扇,多樣化的產品為用戶提供了更為豐富的選擇,而大尺寸的風扇不僅在視覺上更有沖擊力,在一般人的印象中大尺寸的風扇也可以帶動更大
2020-11-30 17:21:22
熱電偶傳感器在工程測試應用—自冷狀態下散熱器的熱阻測試
熱電偶是熱阻測試中常用的傳感器之一。而熱阻測試是電子設備熱設計一項最基本的
2008-10-16 00:06:09
820 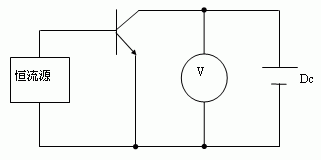
水冷散熱器的安裝與使用
一. 安裝注意事項
1. 散熱器(散熱體)臺面必須與管芯臺面相匹配,嚴禁壓扁壓歪,損壞元件。
2. 安裝時管芯臺面與兩個散
2009-07-28 08:14:42
2505 散熱器散散熱方式
2009-12-26 14:21:39
958 散熱器風量
風量是指風冷散熱器風扇每分鐘送出或吸入的空氣總體積,如果按立方英尺來計算,單位就是CFM;如果按立方米來算,就
2009-12-26 14:25:03
1354 散熱器軸承形式
軸承形式是指風冷散熱器風扇所使用的軸承類形。在機械工程上,軸承的類形
2009-12-26 14:29:41
643 散熱器散熱片材質 散熱片材
2009-12-26 14:35:46
1166 銅比鋁吸熱快,銅沒有鋁散熱快。所以純銅底座的散熱器一般都配備高轉速、大風量的風扇,增加銅底座的散熱能力。廠商也借這個理念推出了塞銅、鑲銅的散熱器,理由是用銅迅速帶走熱
2012-02-21 15:34:09
5600 應用ANSYS有限元分析軟件,在散熱器重量不變的情況下,成功模擬分析了梳形截面散熱器的散熱效果和散熱器長度變化的關系,得到了熱阻核心溫度隨齒長變化的云圖和散熱器長度優化曲線。通過綜合分析,得出了優化
2013-01-25 16:30:25
0 本文介紹了長虹功率晶體管散熱器樣本與插片式散熱器,以及各系列散熱器的介紹。
2017-11-20 14:48:51
5 散熱器是熱水(或蒸汽)采暖系統中重要的、基本的組成部件。熱水在散熱器內降溫(或蒸汽在散熱器內凝結)向室內供熱,達到采暖的目的。散熱器的金屬耗量和造價在采暖系統中占有相當大的比例,因此,散熱器的正確選用涉及系統的經濟指標和運行效果。
2018-11-23 15:41:58
4566 散熱器是一種高效的加熱設備,廣泛應用于北方家庭取暖區。 隨著家庭條件的改善,散熱器開始轉移到中部和南部地區。 越來越多的家庭開始放棄空調供暖,并使用散熱器進行供暖。 散熱器已成為中國最受歡迎的家用暖氣設備之一。
2018-11-23 15:51:59
9702 大家在選擇電腦硬件的時候,都會選擇投入大量的金錢精力花在CPU、顯卡、內存條等這上面。往往將散熱器給忽略掉了,小伙伴們,如果你們認為散熱器不重要的話,那么你們就錯了,散熱器不僅能降低電腦的溫度,而且
2020-01-31 09:10:00
6564 風冷散熱器:塔式散熱器 下壓式散熱器。塔式散熱器:單塔弱于雙塔(散熱面積決定)。下壓式散熱器:大銅芯英特爾散熱器和熱管散熱器!
2020-04-20 20:44:50
22535 每個使用過臺式機的人都知道在機箱里有著許多個風扇,這些風扇讓炙熱的機箱能夠保持一定的溫度,不至于過熱死機或是損壞硬件,在機箱里的多個風扇中,最重要的單獨散熱設備就是CPU散熱器了,為什么不說CPU風扇?因為有的散熱器不是靠風冷散熱的,那么CPU散熱器都有多少類型?到底哪種散熱更好用?
2020-04-27 10:16:45
6961 CPU在工作的時候會產生大量的熱,如果不將這些熱量及時散發出去,輕則導致死機,重則可能將CPU燒毀,CPU散熱器就是用來為CPU散熱的。 散熱器對CPU的穩定運行起著決定性的作用,組裝電腦時選購一款好的散熱器非常重要。
2020-04-27 10:20:37
2447 所有的光排管散熱器系列產品共分為兩大型號規格,也就是A型與B型的區分,A型主要應用于蒸汽采暖系統使用,被稱之為蒸汽排管散熱器,散熱管統一嚴格選用國標無縫鋼管進行交給加工制作,而B型主要應用于熱水采暖系統而使用,被稱之為熱水排管散熱器,散熱管可以選用國標焊接鋼管進行制作。
2021-07-21 16:40:00
560 發動機冷卻系統的散熱器由散熱器芯、上水室、下水室、散熱器蓋等組成。
2021-05-01 17:36:00
9336 導熱相變化材料大約在50℃~60℃的時候會發生相變,并在壓力作用下流進并填沖發熱體和散熱器之間的不規則間隙,以形成良好的導熱界面。那么怎么在散熱器上貼導熱相變化材料呢?
2021-05-13 11:28:42
1275 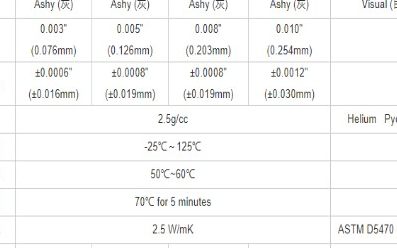
鋼管四柱散熱器承壓力高,散熱性能好,表面光滑,便于清潔,無需勞神的擦拭;此外,該類型散熱器外形色彩豐富,線條簡約流暢,造型大方多樣,容易與家裝所融合。較為重要的是鋼制柱式散熱器水流量大、水阻小、不易
2021-07-21 15:46:14
544 光排管散熱器選用了優質低碳精密鋼管,利用可靠的特殊焊接工藝制成的新型高效節能散熱器。散熱器是推陳出新的換代產品,替代了傳統鋼制和鑄鐵柱型散熱器。光排管散熱器的內腔采用優質防腐材料精心處理和焊接,使用壽命長,散熱器具有良好的防腐和防氧化性能,一般的水作熱媒均可適應。
2021-07-21 15:42:18
728 結合了散熱器的散熱特性和使用插座的優點,即避免設備暴露在高溫焊料和被污染的清洗液中,能夠輕松地將設備PCB從設備上取下,無需人工和脫焊風險。與熱電制冷器(TEC)不同,ANDON散熱器插座??熱量被吸走并遠離設備主體,不需要電源,
2021-11-10 15:03:53
334 由于鋼制散熱器的外形尺寸可以改變,使散熱器不僅是一個散熱的建筑設備,可以把鋼制散熱器作為室內裝飾的一部分:如樓梯扶手和護欄可用鋼制散熱器加工制作;用格柵型建筑裝飾式散熱器作為大房間的隔斷和門廳的花飾,會有一個好的裝修效果。
2021-07-30 11:22:09
848 鋼三柱散熱器采用靜軋低碳鋼管經過氬弧焊接技術制作而成,市場上通用鋼三柱暖氣片的管壁厚度為1.5mm,內部按照要求要做防腐處理,使用年限在十年以上。鋼制散熱器在歐洲已有近50年的使用歷史,現已占70
2021-08-20 09:52:52
1146 光排管散熱器能發揮良好的散熱效果,到那時前提是需要有良好的水質,因為如果水質有問題的話會對散熱器有很多不利的影響。有問題的水中會含有很多雜質,這些雜質可能會對光排管散熱器的散熱排管內壁產生腐蝕作用,這樣就要縮短設備的使用壽命。
2021-09-04 10:39:33
861 選擇合適的散熱器 散熱器是一種通過從電子設備的熱表面吸收熱量,并將其輻射到較冷的環境介質(通常是空氣)中來增強散熱效果的物料。選擇適當的散熱器有助于解決電路中的很多熱相關的問題。那么如何為自己
2021-10-11 16:42:56
3820 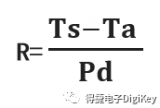
板級散熱器的選型說明,提供豐富的板級散熱器型號。
2022-05-09 17:25:36
3 我們在前面的文章中也提到過,共模干擾分為電流驅動型,電壓驅動型和電磁耦合型。而散熱器不接地屬于共模干擾的電壓驅動型。通常在使用散熱器時,需要將散熱器接地,這樣可以大大減少EMI問題,因為大地為共模干擾提供了低阻抗路徑,當然了,地的阻抗要低。不然會引起地彈現象,引發新的干擾問題。
2022-07-04 10:11:32
1082 本文要點散熱器中的輻射傳熱。傳熱的電路類比。推導輻射熱阻。散熱器是電子產品中常用的熱管理系統,利用傳導、對流、輻射或三者的組合等傳熱方式將熱能從電路傳遞到環境中。散熱器系統的傳熱可以用電路類比來描述
2023-03-31 10:32:52
1340 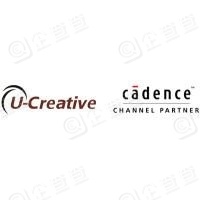
在整體設計上,超頻三G6散熱器采用了雙塔造型,擁有6條6mm純銅熱管,散熱底座為熱管直觸設計。
2023-07-19 14:45:12
211 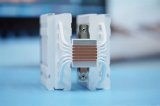
散熱器是現代電子設備不可缺少的部分,經常需要在不同的環境下進行使用。為了確保散熱器的穩定性和高效性,其氣密性檢測非常重要。連拓精密本文將介紹我們針對一款散熱器進行的氣密性測試案例,且采用的是連拓精密
2023-09-01 11:13:04
360 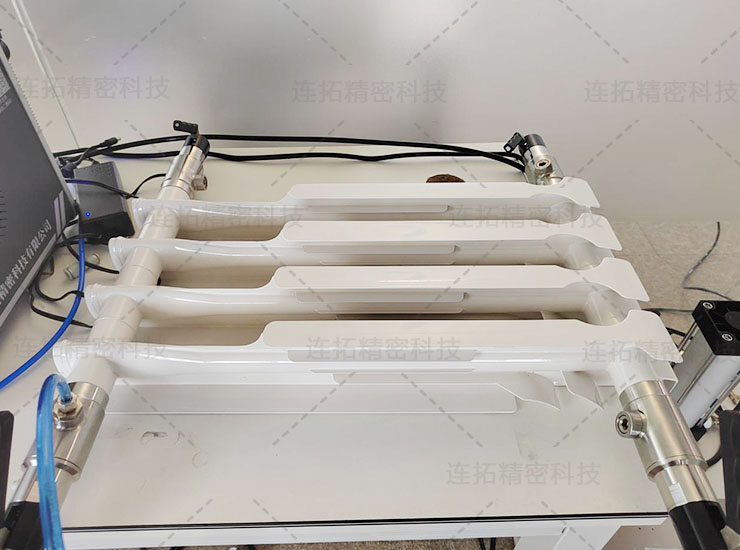
電子元器件中的散熱器:作用與重要性
在電子元器件的世界里,散熱器扮演著至關重要的角色。作為一種專門用于散發電子元件產生的熱量的裝置,散熱器對于維護電子設備的穩定性和可靠性具有不可替代的作用。本文將詳細介紹散熱器在電子元器件中的定義、分類、作用以及應用,并探討其設計原則和維護方法。
2023-11-01 09:20:06
514 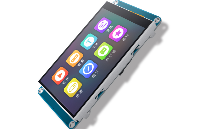
電子發燒友網站提供《車用電控單元散熱器的設計測試.pdf》資料免費下載
2023-11-02 09:11:25
0 探討半導體散熱器的原理和工作機制 半導體散熱器是一種用于散熱的設備,主要用于散熱處理器、顯卡等電子設備中的發熱元件。在本文中,我們將詳細討論半導體散熱器的原理和工作機制。 半導體器件在工作
2024-02-02 17:06:06
223
評論