在將晶圓制成半導(dǎo)體的過程中需要采用數(shù)百項(xiàng)工程。其中,一項(xiàng)最重要的工藝是蝕刻(Etch)——即,在晶圓上刻畫精細(xì)電路圖案。蝕刻(Etch)工程的成功取決于在設(shè)定的分布范圍內(nèi)對(duì)各種變量進(jìn)行管理,并且每一臺(tái)刻蝕設(shè)備都需做好在最佳條件下運(yùn)行的準(zhǔn)備。我們的刻蝕工藝工程師運(yùn)用精湛的制造技術(shù),完成這一細(xì)節(jié)工藝的處理。
SK海力士新聞中心對(duì)利川DRAM Front Etch(蝕刻)Middle Etch以及End Etch技術(shù)團(tuán)隊(duì)成員進(jìn)行了訪談,以此來進(jìn)一步了解他們的工作。
蝕刻(Etch):生產(chǎn)率提升之旅
在半導(dǎo)體制造業(yè)中,蝕刻(Etch)指在薄膜上雕刻圖案。圖案使用等離子體噴涂而成,形成每個(gè)工藝步驟的最終輪廓。它的主要目的是根據(jù)布局完美呈現(xiàn)精確圖案,在任何條件下都保持統(tǒng)一一致的結(jié)果。
如果沉積或光刻(Photolithography)工程中出現(xiàn)問題,可通過選擇性蝕刻(Etch)技術(shù)解決問題。但是,如果蝕刻(Etch)工程過程中出現(xiàn)問題,則情況無法逆轉(zhuǎn)。這是因?yàn)闊o法在雕刻區(qū)域填充相同材料。因此,在半導(dǎo)體制造過程中,刻蝕對(duì)于確定總體良品率和產(chǎn)品質(zhì)量至關(guān)重要。
刻蝕工藝包括八個(gè)步驟:ISO、BG、BLC、GBL、SNC、M0、SN和MLM。
首先,ISO(Isolation)階段進(jìn)行晶圓上的硅(Si)蝕刻(Etch),創(chuàng)建有源單元區(qū)。BG(Buried Gate)階段形成行地址線路(Word Line)1和柵極,打造電子通道。接下來,BLC(Bit Line Contact)階段會(huì)在單元區(qū)內(nèi)創(chuàng)建ISO與列地址線路(Bit Line)2之間的連接。GBL(Peri Gate+Cell Bit Line) 階段將同時(shí)創(chuàng)建單元列地址線路與外圍3中的柵極。
SNC(Storage Node Contract)階段繼續(xù)創(chuàng)建有源區(qū)域和存儲(chǔ)節(jié)點(diǎn)4之間的連接。隨后,M0(Metal0)階段形成外圍S/D(Storage Node)5的連接點(diǎn)以及列地址線路與存儲(chǔ)節(jié)點(diǎn)之間的連接點(diǎn)。SN(存儲(chǔ)節(jié)點(diǎn))階段確認(rèn)單元容量,之后的MLM(Multi Layer Metal)階段創(chuàng)建外部電源和內(nèi)部布線,整個(gè)蝕刻(Etch)工程過程隨之完成。
鑒于蝕刻(Etch)技術(shù)人員主要負(fù)責(zé)半導(dǎo)體的圖案化工作,因此DRAM部門被細(xì)分為三個(gè)團(tuán)隊(duì):Front Etch(蝕刻)(ISO、BG、BLC);Middle Etch(蝕刻)(GBL、SNC、M0);End Etch(蝕刻)(SN、MLM)。這些團(tuán)隊(duì)也會(huì)按照制造崗位和設(shè)備崗位劃分。
制造崗位負(fù)責(zé)管理和改進(jìn)單元生產(chǎn)工藝。制造崗位通過變量控制和其他生產(chǎn)優(yōu)化措施來提高良品率和改善產(chǎn)品質(zhì)量,因而具有十分重要的地位。
設(shè)備崗位負(fù)責(zé)管理和強(qiáng)化生產(chǎn)設(shè)備,以便規(guī)避刻蝕工藝過程中可能出現(xiàn)的問題。設(shè)備崗位的核心職責(zé)是確保設(shè)備的最佳性能。
雖然職責(zé)分明,但所有團(tuán)隊(duì)均朝向共同的目標(biāo)而努力——即,管理和改進(jìn)生產(chǎn)工藝及相關(guān)設(shè)備,進(jìn)而提高生產(chǎn)率。為此,各團(tuán)隊(duì)積極分享各自的成果以及亟待改善的領(lǐng)域,通過合作提高業(yè)務(wù)表現(xiàn)。
如何應(yīng)對(duì)小型化技術(shù)挑戰(zhàn)
SK海力士于2021年7月開始量產(chǎn)適用10nm(1a)級(jí)工藝的8Gb LPDDR4 DRAM產(chǎn)品。
半導(dǎo)體存儲(chǔ)器電路圖案已經(jīng)進(jìn)入10nm時(shí)代,并且經(jīng)過改進(jìn)后,單個(gè)DRAM中可容納約1萬個(gè)單元。因此,即使在刻蝕過程中,工藝裕度也會(huì)有所不足。
如果形成的空穴(Hole)6過小,可能會(huì)出現(xiàn)“未打開”狀態(tài),從而阻塞芯片下端部分。此外,如果形成的空穴過大,可能會(huì)出現(xiàn)“橋接”現(xiàn)象。當(dāng)兩個(gè)空穴之間的間隙不足時(shí),就會(huì)出現(xiàn)“橋接”現(xiàn)象,導(dǎo)致后續(xù)步驟中出現(xiàn)相互粘接問題。隨著半導(dǎo)體日益精細(xì)化,空穴的尺寸數(shù)值范圍正在逐漸縮小,這些風(fēng)險(xiǎn)也將逐步消除。
為了解決上述問題,刻蝕技術(shù)專家們不斷改進(jìn)工藝,包括修改工藝配方和APC7算法,以及引入ADCC8和LSR9等全新刻蝕技術(shù)。
隨著客戶需求愈發(fā)多樣化,另一個(gè)挑戰(zhàn)隨之出現(xiàn)——多產(chǎn)品生產(chǎn)趨勢(shì)。為滿足客戶的此類需求,每種產(chǎn)品的優(yōu)化工藝條件需要單獨(dú)設(shè)定。對(duì)于工程師們來說,這是一項(xiàng)非常特殊的挑戰(zhàn),因?yàn)樗麄冃枰屃慨a(chǎn)技術(shù)同時(shí)滿足既定條件和多元化條件的需求。
為此, Etch(蝕刻)工程師們引入了“APC offset”10技術(shù)來管理基于核心產(chǎn)品(Core Product)的各種衍生品,同時(shí)建立并利用“T-index系統(tǒng)”來綜合管理各項(xiàng)產(chǎn)品。通過這些努力,系統(tǒng)得到持續(xù)改進(jìn),得以滿足多產(chǎn)品生產(chǎn)需求。
審核編輯:陳陳
-
DRAM
+關(guān)注
關(guān)注
40文章
2343瀏覽量
185302 -
刻蝕
+關(guān)注
關(guān)注
2文章
203瀏覽量
13349
原文標(biāo)題:DRAM的9大刻蝕技術(shù)(Etch Technology)
文章出處:【微信號(hào):半導(dǎo)體設(shè)備與材料,微信公眾號(hào):半導(dǎo)體設(shè)備與材料】歡迎添加關(guān)注!文章轉(zhuǎn)載請(qǐng)注明出處。
發(fā)布評(píng)論請(qǐng)先 登錄
一文詳解干法刻蝕工藝
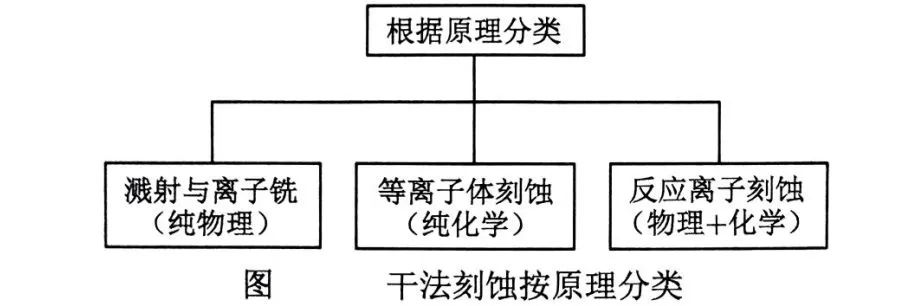
一文詳解濕法刻蝕工藝
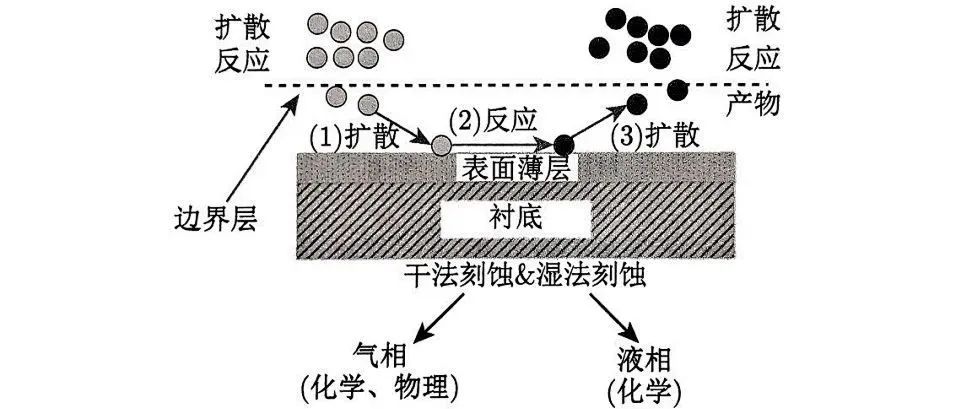
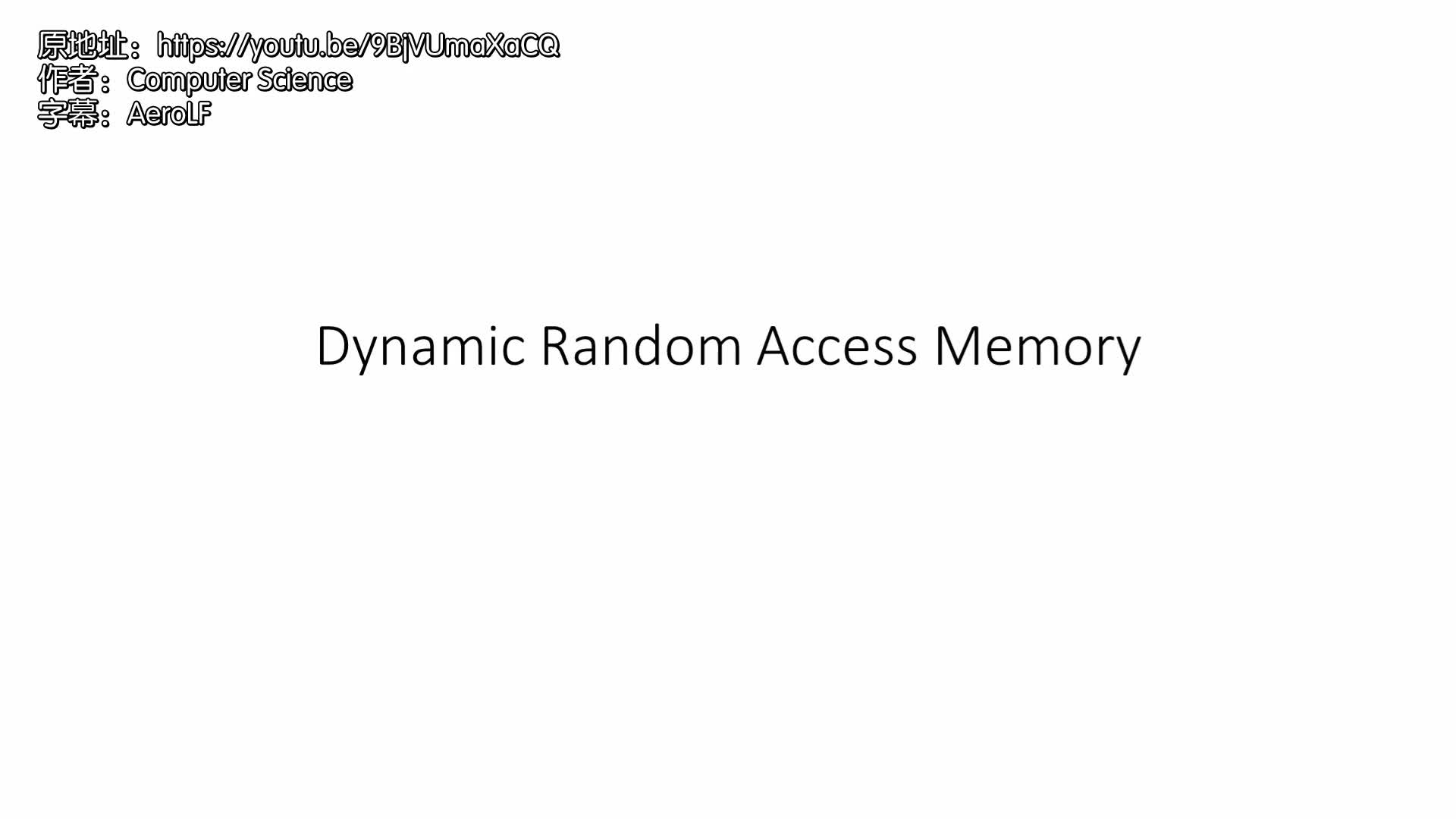
【內(nèi)存知識(shí)】DRAM芯片工作原理
釋放MEMS機(jī)械結(jié)構(gòu)的干法刻蝕技術(shù)
【轉(zhuǎn)帖】干法刻蝕的優(yōu)點(diǎn)和過程
一文解讀HEVC視頻標(biāo)準(zhǔn)的環(huán)內(nèi)濾波,看完你就懂了
請(qǐng)教碳化硅刻蝕工藝
AOE刻蝕系統(tǒng)
一文讀懂SRAM和DRAM資料下載
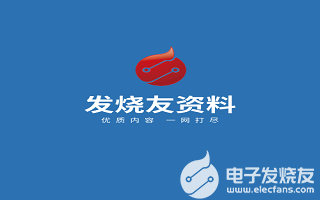
半導(dǎo)體行業(yè)之刻蝕工藝技術(shù)
干法刻蝕與濕法刻蝕各有什么利弊?
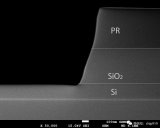
一文解讀GNSS信號(hào)對(duì)網(wǎng)絡(luò)中授時(shí)應(yīng)用的益處
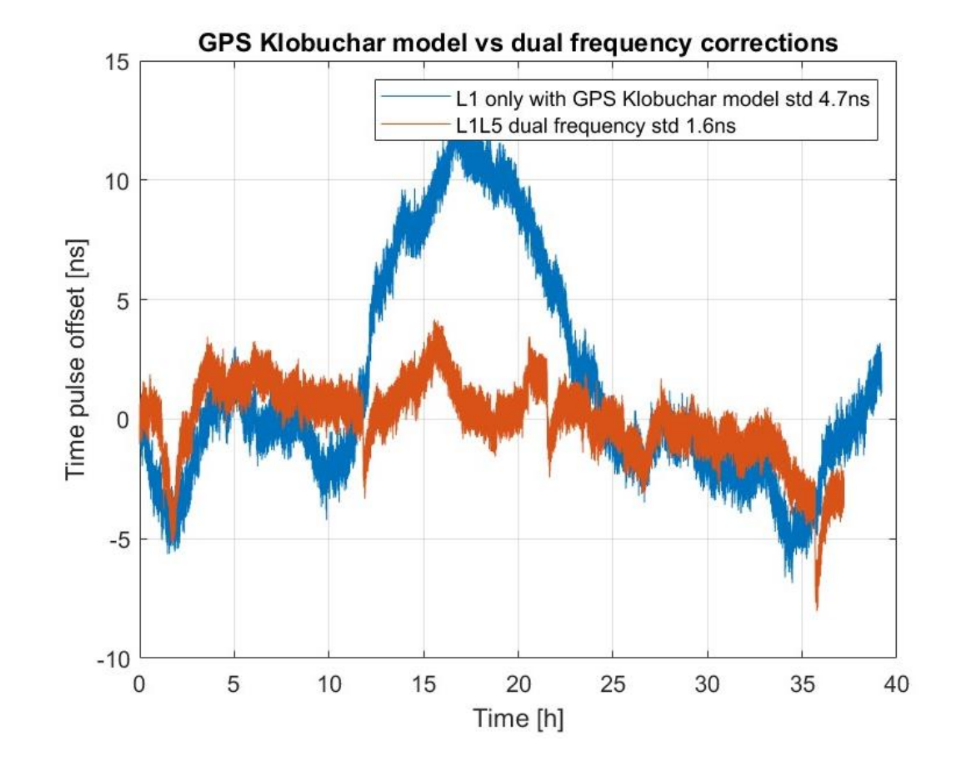
半導(dǎo)體干法刻蝕技術(shù)解析
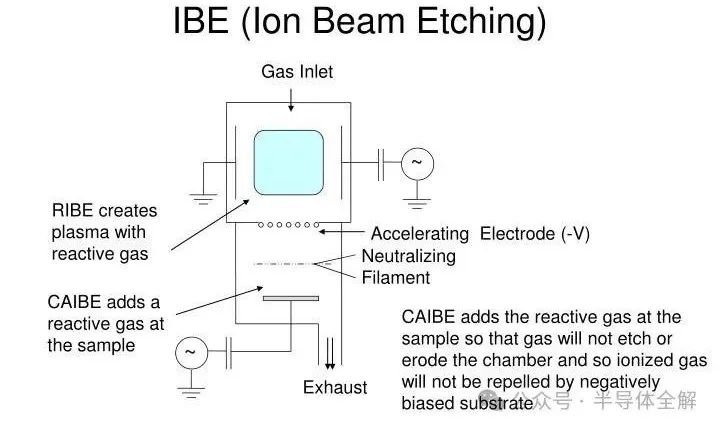
評(píng)論