一、項目背景
在鐵路與公路等工程建設領域,混凝土質量堪稱工程質量的核心要素。過往因混凝土質量不達標而引發的工程事故屢見不鮮。混凝土質量的保障依賴于嚴謹的生產控制、精細的材料控制以及嚴格的實驗檢測控制。其生產控制流程涵蓋開盤令的申請與審核、含水率的測定及配料通知單的下達,還有拌合站控制系統的操作;材料控制關聯材料過磅入庫的準確性、庫存信息的實時性以及材料消耗的精確性;實驗檢測控制則取決于材料出廠編號的完整性、實驗委托的及時性和檢測報告的嚴謹性。然而,傳統拌合站管理主要依賴紙質單據人工流轉與口頭傳達,面對每日數百車數千方混凝土的生產規模以及大量原材料的過磅處理,難以滿足混凝土生產的大規模與實時性需求,無法為混凝土質量管控提供高效且可靠的管理手段。
在此背景下,中鐵六局陽信高速項目部使用萬物智慧拌合站系統,在1號拌合站、2號拌合站進行了有益的探索,并取得預期效果。
二、實施智慧拌合站系統前存在的問題
1.生產控制方面
1.開盤令申請與審核依賴人工跑腿傳遞紙質文件,效率低下且易延誤生產進程。
2.含水率測定及配料通知單下達多靠人工計算與手動操作,易出現人為錯誤,導致配合比失誤。
3.操作樓手動生產模式存在較大操作風險,易因人為因素引發生產事故或質量問題。
4.生產過程數據采集與監控不足,無法及時察覺異常情況,難以實現質量隱患的事前防范與事中控制。
2.材料控制方面
1.材料過磅入庫依靠人工記錄,數據真實性與準確性難以保障,存在作弊風險。
2.材料庫存信息更新滯后,無法實時掌握庫存動態,不利于材料的及時調配與供應。
3.材料消耗統計依靠人工計算,誤差較大,難以精確控制成本。
3.實驗檢測控制方面
1.材料出廠編號、實驗委托單及檢測報告管理混亂,多采用紙質文檔存儲,查詢與追溯困難。
2.對于無合格檢測報告的材料缺乏有效管控機制,易使不合格材料流入生產環節。
3.難以實現對材料及生產問題的精準追溯,責任界定模糊,不利于質量問題的整改與預防。
三、實施過程
1.調研階段:萬物需求調研團隊深入陽信項目的拌合站現場,對現有生產流程、材料管理、實驗檢測流程以及人員操作習慣等進行全面細致的調研。收集傳統管理模式下存在的問題與痛點,了解各崗位對信息化管理系統的功能需求與期望,與一線操作人員、管理人員及技術人員進行充分溝通交流,為系統開發提供精準的需求依據。
2.軟件開發階段:基于調研結果,萬物專業的軟件開發團隊,運用物聯網、大數據、云計算、人工智能等前沿技術進行智慧拌合站管理系統的開發。開發過程遵循軟件工程規范,采用模塊化設計理念,確保系統各功能模塊的獨立性與可擴展性。例如,開發開盤令申請審核模塊、配料通知單生成模塊、生產數據采集與預警模塊、材料庫存管理模塊、實驗檢測報告管理模塊等,并進行嚴格的內部測試與優化,保證系統的穩定性與可靠性。
3.安裝調試階段:在陽信高速 1 號拌合站、2 號拌合站項目現場進行系統的安裝部署。安裝過程涵蓋系統部署、各類傳感器與智能設備(如地磅傳感器、攝像頭、車牌識別設備等)的安裝調試,以及軟件系統在操作終端(電腦、手機等)的安裝與配置。針對不同拌合站的設備差異與網絡環境,進行個性化的調試工作,確保系統與現有設備(如拌合站控制系統、地磅系統等)實現無縫對接,數據傳輸穩定流暢。
4.培訓階段:為使各崗位人員能夠熟練掌握并運用智慧拌合站系統,組織了全面系統的培訓工作。培訓對象包括架子隊人員、實驗員、操作樓工作人員、管理人員等。培訓內容涵蓋系統的基本功能操作(如開盤令申請、配料通知單下達、生產數據查詢等)、異常情況處理(如預警信息響應、設備故障報修等)以及數據錄入規范與要求等方面。通過理論講解、現場演示與實際操作相結合的培訓方式,確保各崗位人員能夠快速上手并高效運用系統。
四、實施后的效果
1.生產控制優化
1.架子隊可通過手機便捷申請開盤令并上傳監理簽字,大幅提升了申請流程的效率,減少了人工奔波時間與溝通成本。
2.實驗員借助系統自動生成含水率并在限定范圍內下達配料通知單,有效避免了人為輸錯配合比的風險,保障了混凝土配合比的準確性。
3.操作樓禁用手動生產,生產任務與配合比由智慧系統直接控制,杜絕了因人為操作失誤導致的生產事故與質量問題,提高了生產的穩定性與可靠性。
4.系統能夠實時采集生產數據,并與生產任務進行比對分析,及時發現并預警配比不符、計量超標、攪拌不均、消耗異常、過磅偏差等異常情況,實現了對生產質量隱患的有效防范與實時控制,保障了混凝土生產質量的穩定性。
2.材料控制精準化
1.地磅過磅系統與 ERP 系統無縫對接并結合視頻監控,實現了對材料過磅、入庫、消耗、庫存的全程精準控制。過磅監控系統與過磅量方系統聯動,可實時精確掌握材料的重量與方量,并實時計算材料含水率,顯著降低了人為測算含水率的誤差,提高了材料計量的準確性。
2.過磅系統與拌合站控制系統聯動,能夠隨時精準掌握筒倉庫存量,為材料的及時供應提供了可靠保障,避免了因庫存不足導致的生產中斷,同時也減少了庫存積壓,降低了材料管理成本。
3.實驗檢測控制提升
1.系統通過物聯網技術對接相關系統,實現了對材料出廠編號、材料實驗委托單、實驗檢測報告的有效管理與控制。對于無合格檢測報告的材料,系統自動執行鎖倉操作,嚴禁其流入生產環節,有效杜絕了不合格材料的使用,從源頭上保障了混凝土質量。
2.借助系統的追溯功能,能夠對涉及材料和生產的任何問題進行精準追溯,明確材料廠家、供應商、收貨人、檢測報告出具人、生產班組、運輸司機等相關責任主體,為質量問題的調查與整改提供了有力依據,促進了質量管控的規范化與精細化。
4.整體效益提高
1.實現了自動生產、自動派車、智能調度功能,在確保混凝土質量的前提下,生產效率顯著提升,提高幅度達 10% - 20%,同時大幅減少了人工成本,降低了勞動強度。
2.系統能夠自動核算原材料消耗、混凝土成品,自動生成物資流向與混凝土節操分析等報告,為拌合站的科學管理提供了豐富準確的定性定量數字化工具,有助于管理者進行精細化決策,提升了拌合站的整體運營管理水平。
五、應用價值效益分析
1.質量保障價值:通過對生產全過程、材料管理及實驗檢測控制的全方位優化與嚴格把控,有效降低了混凝土質量問題的發生率,提高了工程結構的安全性與耐久性,減少了因質量事故導致的返工、維修及工程延誤等損失,為工程質量提供了堅實可靠的保障,提升了企業在工程建設領域的質量聲譽與品牌形象。
2.成本控制效益:
1.材料成本降低:精準的材料控制功能減少了材料過磅誤差、庫存積壓以及因質量問題導致的材料浪費。例如,材料庫存管理的優化可減少庫存5% - 10%,材料損耗降低2% - 5%,每年可為單個拌合站節省材料成本數十萬元。
2.人工成本減少:自動化生產與智能管理模式大幅減少了人工操作環節,降低了對人工的依賴程度。如操作樓自動生產控制減少了操作人員需求,調度自動化降低了調度人員工作量,綜合人工成本降低 15% - 20%。
3.設備維護成本優化:系統對設備的實時監控與預警功能有助于及時發現設備潛在故障,提前安排維護保養,避免設備突發故障導致的高額維修費用及生產中斷損失,設備維護成本降低 10% - 15%。
3.管理提升效益:系統的應用實現了拌合站管理的制度化、流程化、標準化,不受地域與管理風格差異的限制,提高了管理的透明度與可控性。總部能夠實時監控各拌合站的產供銷數據,便于進行集中管理與資源調配,提升了對項目的整體管控能力與決策效率,促進了管理水平的現代化與信息化轉型。
4.行業示范價值:作為 “老基建” 與 “新基建” 結合的成功范例,為工程建設行業內其他企業的拌合站信息化管理提供了有益的借鑒與參考,推動了行業整體向智能化、數字化管理方向的發展,有助于提升整個行業的工程質量與管理水平,具有積極的行業示范與引領作用。
審核編輯 黃宇
-
物聯網
+關注
關注
2930文章
46168瀏覽量
391376
發布評論請先 登錄
水穩拌合站質量監測管理系統在路面施工質量管理中起到重要作用
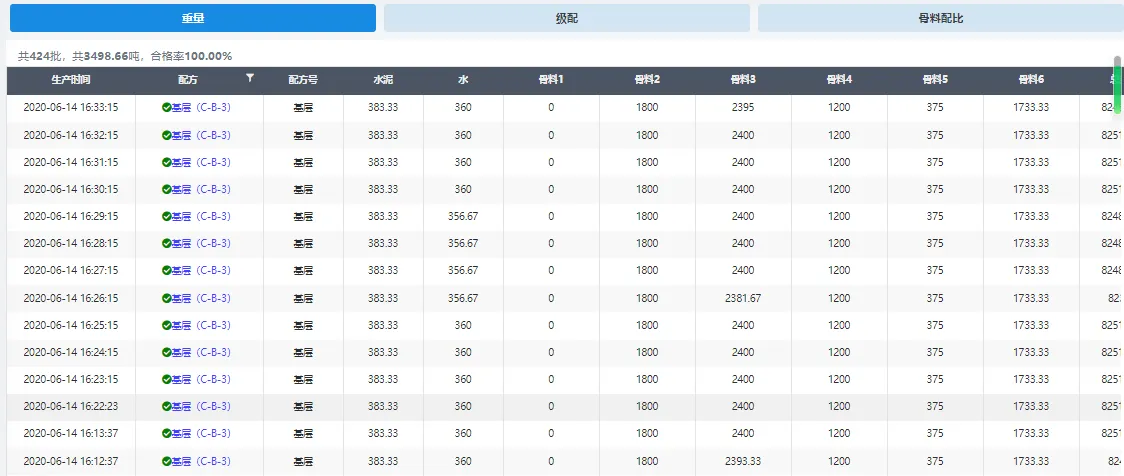
水泥拌合站質量監測管理系統應用介紹
水穩拌合站智能監測管理系統在水穩拌合站質量管理中起到關鍵作用
探討瀝青拌合站管理系統如何通過信息技術提升瀝青拌合站質量控制
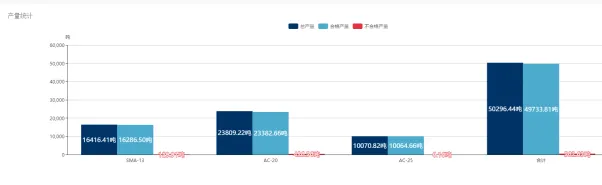
水泥混凝土拌合站管理系統提升混凝土的質量和工程進度
水穩拌合站管理系統成為項目質量管理中的重要關鍵技術
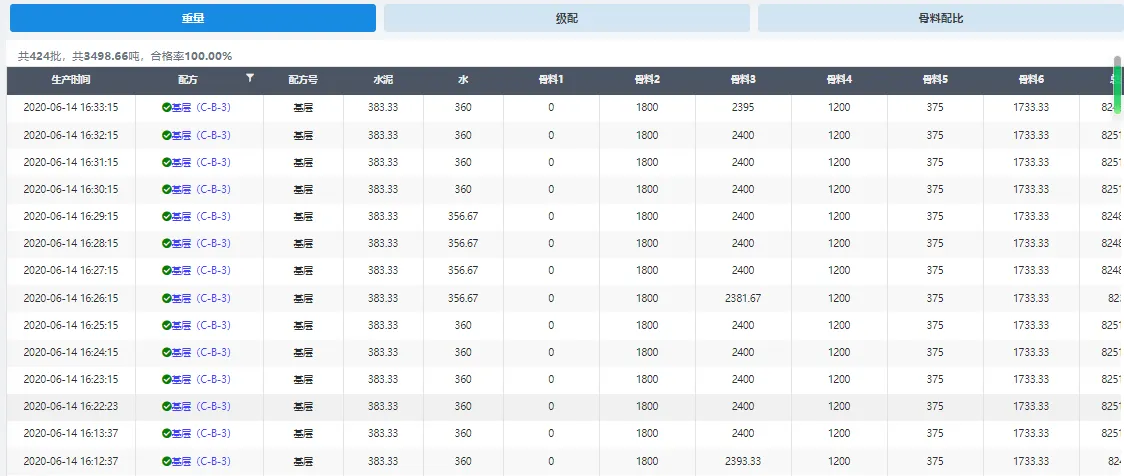
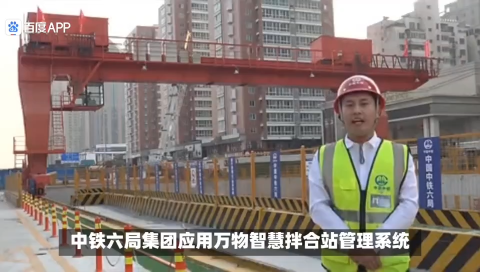
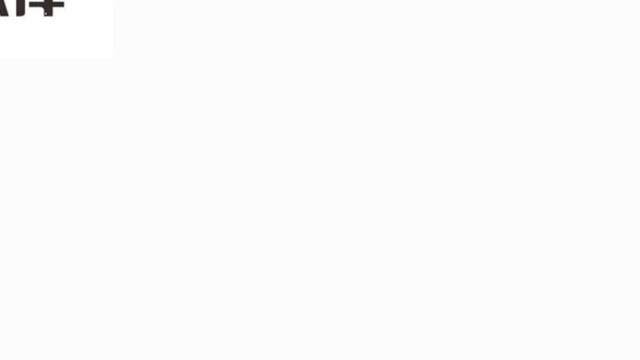
水穩拌合站管理系統助力公路信息技術管理
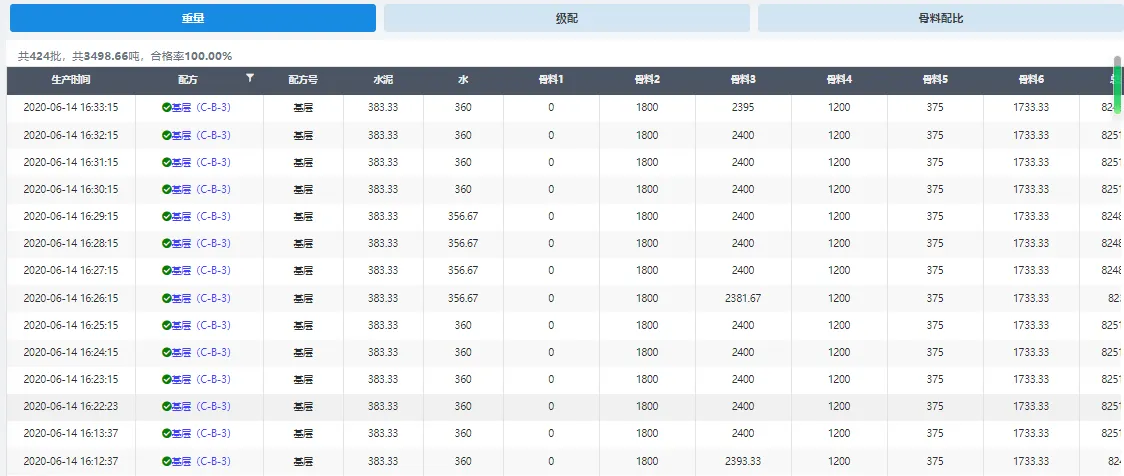
全面探討瀝青拌合站管理系統在公路建設中的重要性
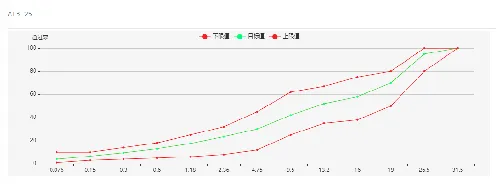
水泥混凝土拌合站監測管理系統主要應用介紹
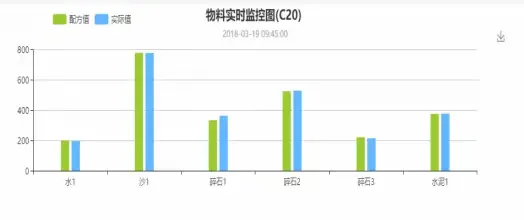
評論