重型燃氣輪機是我國能源發展戰略中的關鍵裝備。在高溫和熱腐蝕環境下工作的透平葉片,是重型燃機的核心熱端部件。與航空發動機葉片比較,先進重型燃氣輪機透平葉片,在高溫熱腐蝕環境下長期工作,而且葉片的尺寸較大,因此,對葉片使用的高溫合金材料及其制造工藝均提出了特殊的要求。用于燃氣輪機葉片的抗熱腐蝕高溫合金材料,經歷了從多晶到定向和單晶的發展歷程,其合金在設計中具有高Cr,高Ti,Al比等幾個顯著區別于航空發動機葉片材料的特征。兼顧高強度、優異抗熱腐蝕性能及長期組織和性能穩定性的燃氣輪機用鑄造高溫合金的研發,因此更具挑戰。定向凝固是重型燃氣輪機用大型定向結晶葉片制造工藝中最為關鍵的技術之一。介紹了先進定向凝固技術——高溫度梯度液態金屬冷卻定向凝固技術的發展,對比了不同定向凝固工藝對高溫合金典型組織及力學性能的影響,并簡單介紹了我國近期在大型定向結晶葉片研制方面的進展。
燃氣輪機包括各類航空航天噴氣發動機、發電和驅動燃氣輪機、艦船動力燃氣輪機以及各種微型燃氣輪機。目前,由燃氣輪機和蒸汽輪機組成的燃氣-蒸汽聯合循環,是人類掌握的熱-功轉換效率最高的大規模商業化發電方式[1]。近年來,全世界每年增長的發電容量中,大約有36%為燃氣輪機聯合循環機組提供[2],燃氣輪機的功率和效率仍在不斷提高。
目前,燃煤發電在我國火力發電工業中仍占絕對主導地位,燃氣輪機發電主要用于調峰,占總發電量的比例很小。僅從環保角度看,煤電的污染排放(SO2、NOx)已經成為電力工業可持續發展的重要制約因素。基于燃氣輪機在我國潔凈能源可持續發展中的重要性和其廣闊的市場前景,重型燃氣輪機已經被列入國家中長期科學和技術發展規劃綱要中能源領域優先發展的主題——煤的清潔高效開發利用、液化及多聯產的研究內容之中。未來我國將大力發展燃氣輪機產業,預計到2020年,將建成裝機容量約為6萬MW的燃氣輪機電站[2-3]。
重型燃氣輪機的核心技術,主要掌握在幾家國外公司手中。美國GE、德國Siemens、法國Alstom和日本MHI等公司經過多年的發展,已經形成了燃氣輪機系列產品。盡管近年來國內引進了E級和F級燃氣輪機的部分制造技術,在重型燃氣輪機的國產化進程中取得了長足進步,但是重型燃氣輪機的設計技術、控制技術、燃燒技術和熱端部件制造技術等幾項核心技術始終掌握在上述幾家國外公司手中。顯然,面對我國龐大的燃氣輪機市場需求,以及燃氣輪機在我國未來能源結構中的重要地位,開展重型燃氣輪機核心技術的研發和產業化,對我國有著極為重要的戰略意義。
重型燃氣輪機中使用的關鍵熱端部件——一、二級大型導向和渦輪葉片,基本采用定向柱晶或單晶高溫合金,通過定向凝固技術制造。國外相關技術已經成熟,大型定向和單晶葉片穩定批產,國內目前尚無制造能力,而相關材料和技術與先進航空發動機葉片密切相關,國外對中國實行嚴格的技術封鎖和價格壟斷。因此,重型燃氣輪機定向結晶葉片的材料與制造技術,目前已成為我國自主發展先進燃機裝備業的瓶頸。
2 重型燃氣輪機渦輪葉片的特點
重型燃氣輪機使用的燃料主要是天然氣和燃油,近年來發展的整體煤氣化聯合循環(Integrated Gasification Combined Cycle,IGCC)技術,還將煤氣化合成氣作為燃料。重型燃機的工作環境和特點與航空發動機截然不同,這也對重型燃機熱端渦輪葉片使用的材料及其制造技術提出了不同的要求。表1簡單對比了兩種葉片的典型特征[4]。圖1是兩種定向結晶葉片——GE公司 F級燃氣輪機高壓一級渦輪葉片與典型航空發動機渦輪葉片的照片[5]。首先,重型燃氣輪機的葉片尺寸和質量遠大于航空發動機葉片,與典型航空發動機長30~150 mm、質量100~200 g重的葉片相比,重型燃氣輪機定向結晶葉片的長度可達910 mm,質量達到18kg[6];第二,重型燃氣輪機葉片的運行時間和狀態與航空發動機葉片不同。重型燃機葉片主要在穩態工作,葉片大修周期長達24 000~40 000 EOH(等效運行小時),總壽命長達6~8萬EOH[1,7]。航空發動機葉片的峰值工作時間短,溫度高于燃機葉片,但其巡航工作溫度又低于燃氣輪機葉片的穩定工作溫度;第三,與航空發動機使用的潔凈燃料比較,重型燃氣輪機使用的燃料種類多,一般含有會對高溫合金材料造成熱腐蝕損傷的V,S等元素。因此,重燃葉片在保證高強度的同時,必須使用抗熱腐蝕的高溫合金材料。航空發動機使用的高溫合金材料通常具有優異的抗氧化性能(圖2a),但在熱腐蝕環境中短時間內就會發生嚴重損傷(圖2b)。與航空發動機葉片相似,先進燃氣輪機使用的渦輪葉片也具有復雜的冷卻結構[7-8],采用定向(DS)或單晶(SC)高溫合金、表面使用熱障涂層(Thermal Barrier Coating,TBC)。典型重型燃氣輪機葉片及涂層的使用情況見表 2[9]。
表1 航空發動機葉片與重型燃氣輪機葉片的比較
圖3簡單總結了GE公司燃氣輪機熱端葉片材料、冷卻方式和工作溫度的發展歷程[10]。可以看出,在20世紀70年代之前,燃氣輪機燃燒溫度的提升,完全依賴于高溫合金葉片材料本身的承溫能力,隨后冷卻技術的發展使燃氣輪機的燃燒溫度不斷提高,材料的工作溫度也隨之提高到850℃以上,這不僅要求材料具有優異的高溫力學性能,也對材料的抗熱腐蝕性能提出了更苛刻的要求。20世紀80年代以來,燃氣輪機開始使用具有復雜冷卻結構的定向結晶葉片,冷卻效率顯著提高,燃機的燃燒溫度也因此明顯提升。
表2 燃氣輪機渦輪葉片材料和涂層的使用情況
圖3 GE公司燃氣輪機熱端葉片材料、冷卻方式和工作溫度的發展歷程圖
3 重型燃氣輪機葉片使用的高溫合金材料
與航空發動機渦輪葉片使用的高溫合金材料的發展歷程相似,國外燃氣輪機葉片使用的抗熱腐蝕高溫合金材料也經歷了從傳統等軸晶(CC)鑄造合金,到定向柱晶和單晶合金的發展(圖 4[11])。
圖4 國外航空發動機和燃氣輪機用高溫合金的發展歷程圖
燃氣輪機葉片用高溫合金必須兼顧材料的抗熱腐蝕性能、高溫強度、組織穩定性以及鑄造工藝性能,表3列出了國外典型抗熱腐蝕高溫合金的主要成分。可以看出,燃氣輪機用高溫合金的成分主要有以下幾個特點:①合金中的Cr含量一般大于12%(質量分數,下同)。較高的Cr含量可以保證在熱腐蝕環境中,合金表面能夠形成基本連續的Cr2O3保護膜。但Cr是高溫合金中的有害相-TCP相的形成元素,它作為固溶強化元素,在鎳基高溫合金中的強化效果也不如W,Mo,Ta等,因此抗熱腐蝕高溫合金中的Cr含量必須控制在合理的水平,以免影響合金的組織穩定性和力學性能;②合金從多晶發展到定向和單晶,合金中Ta元素的含量逐漸增加。隨著燃氣輪機葉片工作溫度的提高,對抗熱腐蝕高溫合金高溫強度的要求不斷提升,Ta作為重要的強化元素,在抗熱腐蝕合金中的含量也逐漸增加。除了有效提高合金的高溫強度外,由于Ta在枝晶間偏析,它還可以通過調整定向凝固中糊狀區枝晶間液體的密度,降低鑄件中雀斑等缺陷的形成傾向[16-17]。一般認為Ta對高溫合金的抗氧化性能也有一定的改善[18-21]。最近的研究還發現,Ta對提高合金抗氧化性能的貢獻有限,但可以顯著提高合金的抗熱腐蝕性能[22-23];③合金中Mo元素含量較低。Mo是高溫合金中有效的固溶強化元素,但由于其在熱腐蝕環境中容易引起酸性熔融反應,產生嚴重的熱腐蝕[12,24],因此,在燃氣輪機用抗熱腐蝕高溫合金中,Mo的含量一般較低;④合金中Ti、Al兩種元素的總量基本維持在7% ~8%的水平,但Ti含在鎳基高溫合金中的強化效果也不如W,Mo,Ta等,因此抗熱腐蝕高溫合金中的Cr含量必須控制在合理的量一般高于Al含量。Ti和Al是主要的γ'相形成元素,兩種元素的總量維持在7%~8%的水平可以充分保證合金中γ'相的體積分數,從而保證合金的沉淀強化效果。由于Ti可能會與S反應形成穩定的固態硫化物,延緩金屬-金屬硫化物液態共晶的形成,從而延緩熱腐蝕反應進程[13],改善合金的抗熱腐蝕性能。因此,抗熱腐蝕合金中的Ti含量一般較高。但合金中Ti含量增加,會顯著提高定向合金的熱裂傾向[25-26],因此必須合理控制合金中的Ti/Al比;⑤抗熱腐蝕高溫合金中一般不含Re,Ru等貴金屬元素。Re和Ru是航空發動機用先進定向和單晶高溫合金中的重要強化元素,可以顯著提升合金的高溫強度。隨單晶高溫合金承溫能力的不斷提高,合金中的Re,Ru元素的含量也在不斷增加,第4代單晶合金中兩種元素的含量已經分別達到6%和3%左右。但是,兩種元素的價格昂貴,資源稀缺,考慮燃氣輪機的制造成本,目前大規模商業化的重型燃氣輪機使用的葉片材料,以及國外正在研制的高強抗熱腐蝕單晶高溫合金中均不含Re和Ru。正在推向市場的G/H級燃氣輪機中,僅有美國GE公司使用了含3%Re元素的第2代單晶高溫合金;⑥單晶合金中一般含有微量的C,B,Hf等元素。由于重型燃氣輪機的葉片尺寸很大,在定向凝固中更容易出現小角度晶界等缺陷,因此近年來傳統的晶界強化元素C和B被重新添加到抗熱腐蝕單晶合金中,以提高合金對小角度晶界等缺陷的容限[21,27]。例如,當小角度晶界超過 10°時,PWA1483單晶合金的橫向持久性能會顯著降低,但含微量C,B,Hf的合金中,即使晶界角度高達25°,合金的持久性能仍然沒有明顯的降低(橫向持久樣品的應力軸為<100>方向)[27]。
表3 國外典型鎳基抗熱腐蝕高溫合金的主要成分(質量百分數)
在我國,中國科學院金屬研究所最早開展了抗熱腐蝕高溫合金的研發工作,研制了我國第1個抗熱腐蝕高溫合金K438。近年來,鋼鐵研究總院等單位也開始針對重型燃氣輪機用抗熱腐蝕定向合金的研制工作[28]。
從表7中可以看到,除了自我效能感與人際關系績效相關性不顯著之外,其余各維度都是顯著正相關的。根據驗證結果可以發現,人格特質與工作績效存在顯著相關。成就需要、控制源、自我效能感與工作績效都是正向相關,但成就需要對任務績效、人際關系影響最大;控制源與工作奉獻的關系更為密切;自我效能感對任務績效、人際關系、工作奉獻影響較小。
圖5為中科院金屬所研制的部分燃氣輪機葉片用抗熱腐蝕高溫合金材料持久性能與典型國外同類合金的比較。從早期的仿制合金K438(等軸晶)開始,經過幾十年的發展,合金的強度水平不斷提高,正在逐步形成具有自主知識產權的燃氣輪機用抗熱腐蝕高溫合金體系,例如多晶合金K444、K452,定向合金DZ38G、DZ411,單晶合金DD8、DD10等。其中抗熱腐蝕定向合金DZ411和單晶合金DD10與國外重燃機廣泛使用的定向合金DS-GDT111和單晶合金PWA1483的持久性能水平基本相當[27-31](圖6)。圖7為兩種合金的涂鹽熱腐蝕實驗結果[32],可以看出,兩種合金的抗熱腐蝕性能與著名的抗熱腐蝕合金K438基本相當。900℃燃氣熱腐蝕實驗也得到了類似的結果。
圖7 DZ411(a)和DD10(b)合金950℃熱腐蝕實驗曲線。實驗采用涂鹽法(80%Na2SO4+20%K2SO4飽和溶液),涂鹽量為~2 mg/cm2
對DZ411合金的組織穩定性研究表明,合金經900℃,24 000 h長期時效后,組織穩定,無TCP相析出。圖8是DZ411合金熱處理態,900℃,12 000 h和900℃,24 000 h長期時效后的顯微組織比較。隨時效時間延長,合金中的γ'相立方度降低,并逐漸長大,特別是晶界位置析出了大塊、連續的γ'相[33]。利用掃描電鏡的背散射電子衍射(EBSD)分析發現,900℃,24 000 h長期時效后,合金中的γ'相會沿[011]和[111]方向以枝晶形態長大,導致合金的持久性能降低[34]。時效12 000 h的樣品經恢復熱處理后,可以得到比較理想的γ'相尺寸和形態,晶界形貌也回復到接近熱處理后的狀態(圖9)。力學性能測試結果(表4)也表明,恢復熱處理可能是燃氣輪機葉片延壽的有效手段。
DD10單晶合金是目前國內強度水平最高的抗熱腐蝕單晶合金,對合金的凝固過程、析出相種類,單晶制備工藝及熱處理制度等開展的系統研究表明[32, 35-37],合金組織穩定,而且具有良好的鑄造工藝性能。圖10是DD10單晶合金熱處理態和經900℃長期時效后的γ'相形貌。與DZ411合金中觀察到的現象相似,γ'相在長期時效中合并長大,部分溶解,立方度降低,但合金中沒有TCP相析出,表現出良好的組織穩定性[32, 37]。
表4 DZ411合金900℃,12 000 h時效和恢復熱處理后的性能比較
圖10 DD10單晶合金熱處理態(a),900℃,6 500 h時效(b)和900℃,8 500 h時效(c)后的顯微組織
4 葉片制造技術
重型燃氣輪機用大型定向結晶葉片制造工藝,包括復雜大尺寸陶瓷型芯和陶瓷型殼的制造、定向凝固過程中的參數控制、葉片的熱處理和加工及長壽命防護涂層制備等。其中,定向凝固技術是大型定向結晶葉片的關鍵制造技術之一。
從20世紀80年代開始,快速凝固技術(High Rate Solidification,HRS)被廣泛應用于航空發動機定向和單晶葉片的制造。隨著航空發動機相關技術向燃氣輪機的轉移,HRS技術也被用來制造燃氣輪機使用的大型定向結晶葉片。由于尺寸差別巨大,利用HRS技術制造重燃機葉片時,必須重新優化關鍵工藝,例如改善陶瓷型殼、型芯的材料和制造工藝,優化蠟模材料和設計,對定向凝固參數進行更精確的控制等[38]。但是,隨重型燃氣輪機葉片尺寸的增加,傳統的HRS技術在制造大型定向結晶葉片時遇到了越來越多的挑戰。
圖11是定向凝固中葉片尺寸與鑄造缺陷關系的示意圖[11, 39]。由于HRS工藝定向凝固中,隨葉片尺寸的增加,固液界面前沿的溫度梯度不斷降低,為了維持固液界面穩定的溫度梯度,獲得無凝固缺陷的鑄件,必須把液態高溫合金的溫度保持在很高的水平,同時降低凝固速率(近似定向凝固過程的抽拉速率)。但在1 500~1 600℃,甚至更高溫度下,活潑的液態高溫合金長時間與陶瓷型殼和型芯接觸,很容易發生反應,陶瓷型殼和型芯本身也容易發生蠕變、斷裂。因此,大型定向結晶葉片的工藝窗口很小(圖11中的灰色區域),而且很容易出現等軸晶、縮孔、雀斑等缺陷。這同時也給型殼、型芯、葉片后處理等帶來一系列問題[4, 11, 40]。
圖11 定向凝固中鑄件尺寸與凝固缺陷關系示意圖
20世紀90年代,國際重型燃氣輪機市場發展迅速,對大型定向結晶渦輪葉片的需求也越來越迫切,為了解決HRS技術制造大型定向結晶葉片時面臨的上述問題,Siemens,GE和Alstom均開始高溫度梯度液態金屬冷卻(Liquid Metal Cooling,LMC)定向凝固技術的工程化應用研究。到2000年左右,歐洲已經完成了LMC技術的工程化研究,掌握了大型LMC葉片的批產技術。由于LMC工藝使用低熔點合金作為冷卻介質,大幅度提高了整個定向凝固過程的溫度梯度,因此可以顯著細化鑄件的顯微組織、提高抽拉速率。除了合金組織與性能的顯著改善,LMC技術的另一個巨大優勢體現在大型葉片的定向凝固制造工藝中。由于LMC定向凝固中固液界面的溫度梯度始終很高,因此完全可以使液態高溫合金溫度保持在較低的水平,采用較快的抽拉速率,避免大尺寸陶瓷型殼、型芯發生上述HRS工藝中容易出現的問題。文獻[40]針對LMC工藝中低熔點合金冷卻介質的選擇,LMC設備參數和工藝參數的優化,以及LMC工藝制備的高溫合金的典型組織與力學性能做了較為詳細的介紹。
近幾年,國外結合數值模擬,針對LMC技術開展了進一步的研究。例如Pollock等人[41-43]利用LMC技術制備了第二代單晶高溫合金,模擬了定向凝固過程中固液界面的位置,以及單晶合金的一次枝晶間距,研究了工藝參數對枝晶間距和縮孔尺寸與分布的影響。通過與傳統HRS工藝的對比,進一步證實了LMC技術可以有效地細化組織,減少缺陷。Singer等人[44-45]還發現,由于LMC工藝使合金中縮孔的尺寸和體積分數明顯減少,合金的疲勞性能得到明顯提升。
在我國,西北工業大學利用LMC技術高溫度梯度的特點,在合金凝固理論方面開展了大量的研究工作,對高溫度梯度下定向和單晶合金的凝固特征、顯微組織等進行了較為系統和深入的研究[46-50]。鋼鐵研究總院利用傳統HRS技術,結合數值模擬,研制了總長約300 mm的定向結晶燃氣輪機葉片[51]。
中國科學院金屬研究所從2003年開始探索LMC技術的工程化應用,突破了抗熱沖擊模殼、低熔點金屬污染控制等關鍵技術,2009年成功研制了可滿足750 mm長定向結晶葉片研制的大型LMC設備,為重型燃氣輪機大型定向結晶渦輪葉片的研制,奠定了裝備和技術基礎[52-53]。近年來,利用LMC技術,針對定向和單晶合金的定向凝固工藝[35,54-55]、顯微組織[56]、熱處理工藝[57]、典型性能[58-59]和鑄造工藝性能[60]等開展了較為系統的工作。研究表明,LMC技術可以獲得顯著細化的定向凝固組織,某些合金甚至可以鑄態直接使用,避免了后續固溶熱處理帶來的再結晶等問題。特別是在難以充分實現均勻化熱處理的大型定向結晶鑄件中,LMC工藝可使合金的疲勞性能得到明顯提升[61]。
重型燃氣輪機熱端部件的研制工作在國內起步較晚,近年來中科院金屬所、鋼鐵研究總院等單位與國內相關企業合作,研制了多種重型燃氣輪機使用的等軸晶渦輪和導向葉片,同時也開展了大型定向結晶渦輪葉片的研發工作[62]。
近年來,金屬所成功研制了430 mm長的實心定向葉片;在突破大尺寸抗熱沖擊型殼、復雜型芯、定向凝固等關鍵技術的基礎上,利用LMC技術成功研制了450 mm長、具有復雜冷卻內腔結構的大型DZ411定向結晶渦輪葉片。
由于較慢的拉伸速率和較低的凝固速率,傳統HRS工藝制造的大型定向結晶鑄件的一次枝晶間距約為350~550 μm[63-64],在葉片中容易出現由于宏觀偏析造成的雀斑等缺陷[65]。對LMC工藝制備的大型定向結晶葉片的鑄態顯微組織進行分析表明,一次枝晶間距(PDAS)和二次枝晶間距(SDAS)均隨離開冷卻底盤的距離的增加而增加,在葉片延伸段和榫頭位置,PDAS最大,約為320 μm(圖12)。鑄態葉片不同位置的共晶尺寸和體積分數的統計結果見圖13,鑄造縮孔尺寸和體積分數見圖14。由于LMC工藝較高的溫度梯度減輕了定向凝固中的偏析,所有葉片中均未出現大型鑄件中容易產生的雀斑等缺陷。
圖12 葉片不同位置的一次枝晶間距(a)和二次枝晶間距統計(b)
圖15 LMC葉片經1 210℃ (a),1 220℃ (b),1 230℃(c)固溶熱處理后,DZ411合金的典型顯微組織
固溶處理溫度對DZ411合金的組織影響很大,圖15是葉片延伸段取樣經不同溫度固溶處理后的典型顯微組織。可以看出,隨固溶溫度的提高,合金中枝晶間的殘留共晶逐漸減少,較高的固溶處理溫度可以使鑄態枝晶間的共晶完全溶解,實現合金的充分均勻化。但是,較高的固溶處理溫度也可能帶來再結晶、初熔等缺陷[6]。合金經固溶和時效熱處理后,基體中析出了立方度較好、尺寸約為300 nm的γ'相,在γ基體通道中,還析出了細小的二次γ'相(圖16)。
在上述工作的基礎上,近年來,金屬所也開展了大型單晶葉片的研制工作。結合計算模擬技術,通過合理設計單晶葉片澆注系統,精確控制定向凝固參數,成功制備了300 mm長的大型單晶葉片(圖17)。
圖16 DZ411葉片熱處理后的典型γ'相形貌
圖17 利用計算模擬技術得到的單晶葉片定向凝固中的溫度場分布(a),和利用DD10合金研制的燃氣輪機單晶葉片(b)
5 結語
大尺寸定向和單晶渦輪葉片是現代和未來先進重型燃氣輪機的關鍵熱端部件,因此研制具有優異綜合性能(力學性能,抗熱腐蝕和抗氧化性能,鑄造工藝性能,涂層工藝性能,長期組織和力學穩定性等)的定向和單晶高溫合金材料,掌握大型定向結晶渦輪葉片的關鍵制造技術,是我國自主研發先進燃氣輪機的重要保障。
盡管目前國內抗熱腐蝕鑄造高溫合金,已經基本形成了等軸晶、定向柱晶和單晶合金的體系,但實現現有合金的工程化應用,保證重型燃氣輪機的自主研發和高效、高可靠性運轉,仍需要開展大量深入的工作,主要包括合金、合金-涂層體系的長壽命性能數據積累,近服役工況條件的性能測試與考核,合金的長壽命組織性能演化規律及損傷機制,部件的壽命評估與壽命預測等等。此外,針對未來先進燃氣輪機的需要,必須開展工作溫度更高的抗熱腐蝕定向和單晶合金的研制。由于重燃葉片的尺寸越來越大,大型定向和單晶葉片中的某些缺陷,例如單晶葉片中的小角度晶界很難完全消除,所以在合金研制中,在系統研究缺陷對合金性能影響的同時,必須考慮如何提高合金的缺陷容限。
大型葉片制造包括定向凝固及后續處理和加工、涂層等。其中定向凝固技術、長壽命涂層技術,是定向和單晶葉片的核心制造技術。除高溫度梯度LMC技術外,還涉及大型陶瓷模殼、型芯、蠟模的制造與脫除,固溶熱處理及其它熱工藝過程中的再結晶控制,涂層材料及制造工藝等。因此,為實現大型定向結晶和單晶葉片的工程化制造與應用,仍需開展大量工作。未來先進重型燃氣輪機熱端葉片的工作溫度不斷提升,由于單晶高溫合金材料本身的承溫能力提升幅度較小,而且需要添加Re等貴金屬元素,因此先進冷卻技術(例如,先進航空發動機使用的層板冷卻技術)和熱障涂層技術的應用對未來大型單晶葉片的發展和應用意義重大,這也對大型復雜單晶葉片的制造工藝提出了更高的要求。
材料與工藝的計算模擬技術,是優化重型燃氣輪機關鍵熱端部件制造工藝,推動關鍵技術發展和應用的重要手段。從先進高溫合金的成分設計,熱處理制度設計,力學行為,氧化腐蝕行為,大型鑄件的定向凝固工藝優化與缺陷控制,到材料和部件的使役行為,損傷與壽命評估及預測,均需要依托研發工作中的大量基礎數據積累,開展相應的計算模擬工作,不斷豐富相關材料理論,同時指導先進材料與復雜熱端部件的研發與應用。
-
燃氣輪機
+關注
關注
1文章
39瀏覽量
11607 -
渦輪葉片
+關注
關注
0文章
9瀏覽量
2385
原文標題:中科院金屬所:重型燃氣輪機定向渦輪葉片的材料與制造工藝
文章出處:【微信號:AMTBBS,微信公眾號:世界先進制造技術論壇】歡迎添加關注!文章轉載請注明出處。
發布評論請先 登錄
2025渦輪技術大會暨民用航空發動機與燃氣輪機展在蘇召開
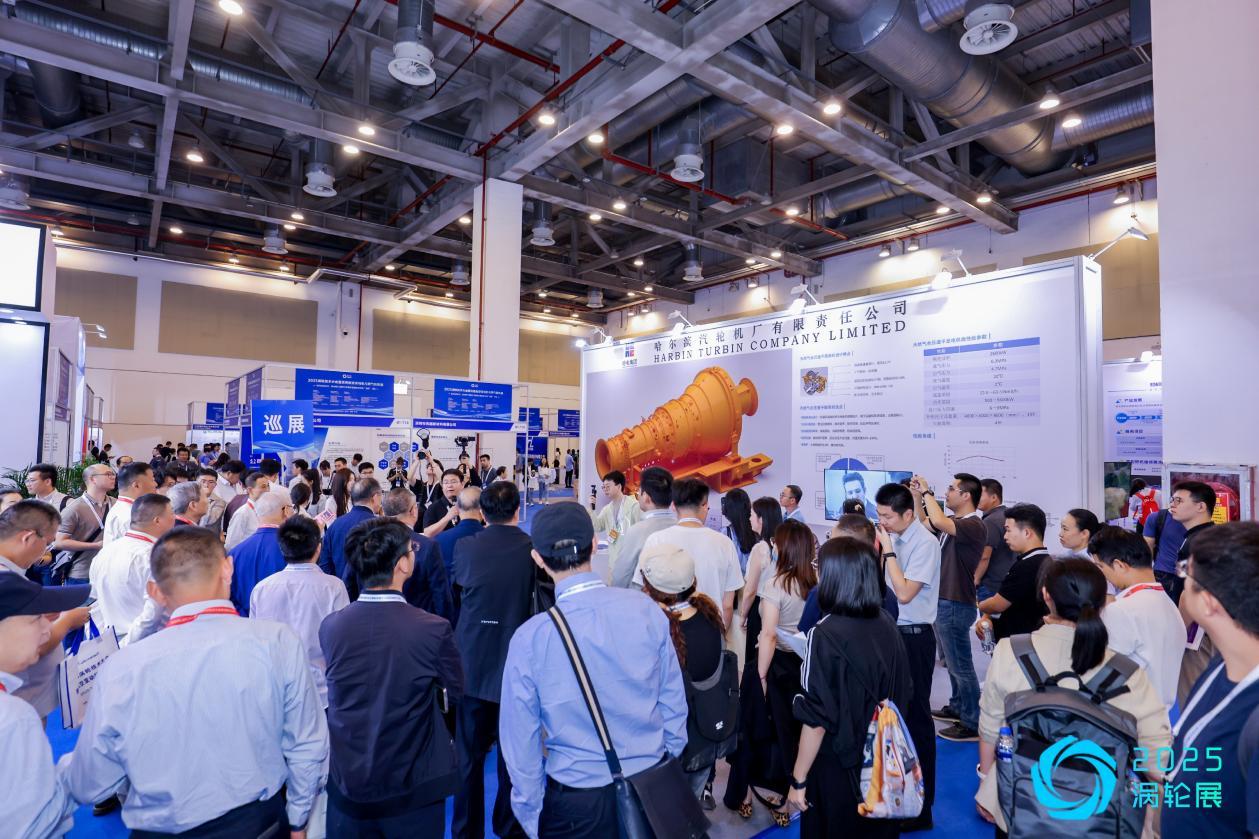
Cadence邀您相約2025渦輪展
中科曙光助力中科院高能物理研究所打造溪悟大模型
國之重器燃氣輪機100問全解析
汽輪機與煤氣輪機的區別
703所:某型燃氣輪機熱障涂層對渦輪動葉冷卻效果的影響機制研究
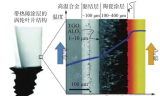
2025(第七屆)民用航空發動機與燃氣輪機行業大會暨渦輪技術展覽會震撼登陸蘇州
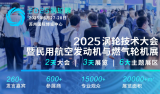
我國重型燃氣輪機小型化取得新突破
蔡司掃描儀3D抄數建模設備助力渦輪機葉片檢測
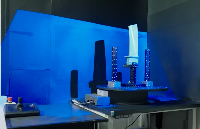
卡特彼勒旗下索拉透平亮相2024進博會
重磅定檔!2025渦輪技術大會暨民用航空發動機與燃氣輪機展將于2025年5月舉辦
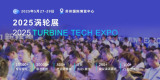
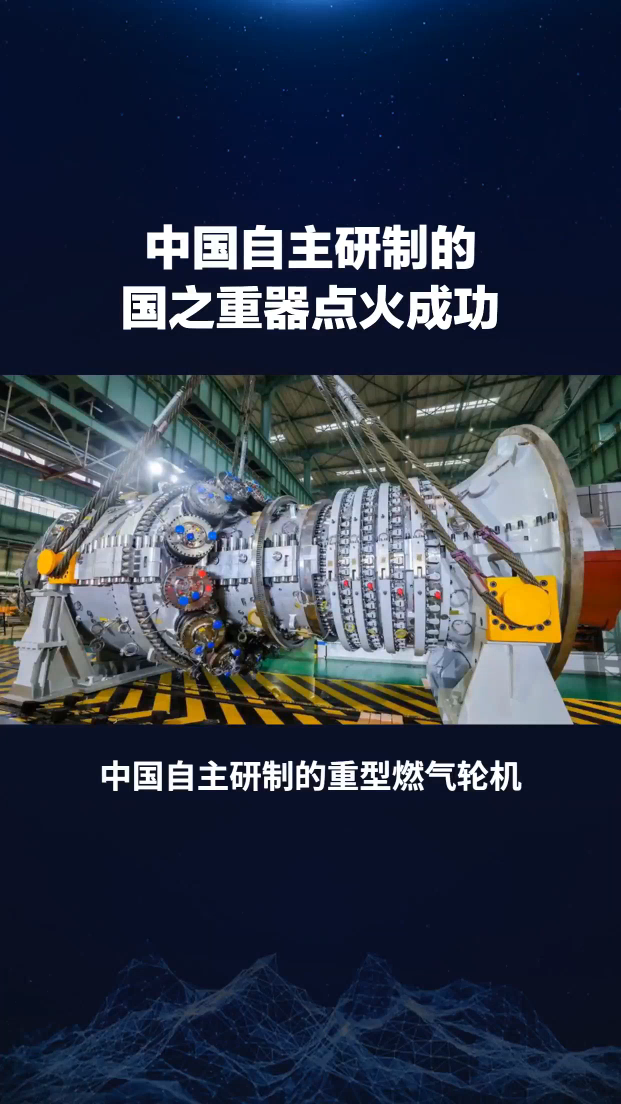
評論