在PCBA代工代料加工中,**透錫不良**是導致焊點失效的“隱形殺手”。傳統目檢和AOI(自動光學檢測)難以穿透封裝觀察焊點內部,而X-Ray檢測技術憑借其“透視眼”能力,成為診斷透錫不良的核心工具。本文將結合實際案例,解析如何通過X-Ray圖像快速識別透錫問題,并提供優化方案,助力企業提升良率。
一、透錫不良的常見類型與X-Ray特征
透錫不良主要表現為焊料未充分潤濕焊盤或引腳,常見類型及X-Ray圖像特征如下:
1. 虛焊(Non-Wet-Open, NWO)
X-Ray特征:焊點與焊盤間存在明顯間隙,焊料邊緣呈鋸齒狀或收縮形態,錫球體積偏小。
成因:焊膏活性不足、回流溫度偏低或焊盤氧化。
2. 冷焊(Cold Solder)
X-Ray特征:焊點表面粗糙,內部結構不均勻,錫球邊緣模糊,可能伴隨微小空洞。
成因:回流時間不足、溫度曲線不匹配或元件熱容差異。
3. 空洞(Void)
X-Ray特征:焊點內部呈現圓形或橢圓形高亮度區域(因空氣密度低,X射線穿透性強),空洞率超過10%需重點關注。
成因:助焊劑揮發不充分、焊膏印刷不均勻或元件排氣不暢。
4. **枕頭效應(HIP, Head-In-Pillow)
X-Ray特征:BGA焊球與PCB焊盤呈“枕頭狀”分離,錫球頂部與焊盤接觸但底部未融合。
成因:BGA翹曲、PCB變形或回流熱應力不均。
二、X-Ray圖像快速診斷5步法
通過以下步驟,可在30秒內初步鎖定透錫問題:
步驟1:定位關鍵焊點
- 優先檢查BGA、QFN、LGA等底部不可見焊點,以及大電流、高發熱區域的焊點。
步驟2:對比焊點形態
- 正常焊點應飽滿圓潤,邊緣清晰;透錫不良焊點體積偏小、邊緣收縮或存在不規則突起。
示例:某電源板BGA焊點透錫不良,X-Ray顯示錫球直徑較周邊縮小20%,判定為虛焊。
步驟3:分析灰度對比
空洞區域因密度低,在X-Ray圖像中呈現高亮度;冷焊焊點因結構松散,灰度分布不均勻。
步驟4:多角度旋轉觀察
傾斜載物臺(±60°)檢查焊點三維結構,避免因投影重疊導致誤判。例如,BGA枕頭效應需通過側視角度確認錫球分離情況。
步驟5:量化參數評估
使用軟件測量焊點面積、空洞率、偏移量等參數,對比IPC標準(如空洞率≤25%為可接受)。
三、透錫不良的優化方案
基于X-Ray診斷結果,針對性優化工藝:
1. 焊膏印刷調整
鋼網開孔比例從1:1擴大至1:1.1,增加外延0.2mm,提升焊膏釋放量。
2. 回流曲線優化
針對無鉛焊膏(如SAC305),峰值溫度需達240-250℃,活性區時間延長至90秒,確保助焊劑充分活化。
3. **元件與PCB預處理
對氧化焊盤進行等離子清洗,或采用氮氣回流焊減少氧化風險。
4. 進階檢測技術應用
復雜案例可使用3D X-Ray CT斷層掃描,檢測微米級裂紋或層間對準偏差,精度可達0.5μm。
四、典型案例解析
案例背景:某汽車電子PCBA批次BGA焊點故障率超5%。
X-Ray診斷:
圖像顯示30%焊點存在枕頭效應,錫球頂部與焊盤未融合。
根因分析:
PCB翹曲導致BGA與焊盤熱膨脹系數不匹配。
解決方案:
優化PCB層壓工藝,增加回流焊預熱時間(從60秒延長至80秒),透錫不良率降至0.3%。
五、結語:X-Ray是品質管控的“戰略武器”
在PCBA代工中,X-Ray檢測不僅能快速定位透錫不良,還可通過數據積累優化工藝參數。建議企業:
建立焊點圖像數據庫,標注典型缺陷特征;
定期校準設備,確保圖像分辨率(推薦≥1μm);
結合SPI(焊膏檢測)與AOI,實現全鏈路品控閉環。
下期預告:《如何通過3D X-Ray預判BGA壽命?深度解析焊點疲勞裂紋》
參考設備:日聯科技X-Ray檢測儀(支持BGA多角度成像)、際諾斯3D CT掃描儀(微裂紋診斷)。
審核編輯 黃宇
-
pcb
+關注
關注
4362文章
23458瀏覽量
408232 -
x-ray
+關注
關注
1文章
122瀏覽量
13773
發布評論請先 登錄
PCBA加工廠中X-RAY檢測技術應用與重要性
X-Ray檢測助力BGA焊接質量全面評估
從捷多邦案例看X-Ray檢測在BGA焊接評估中的作用
X-Ray檢測設備能檢測PCBA的哪些缺陷
SMT加工質量新保障:X-ray檢測設備的作用與重要性
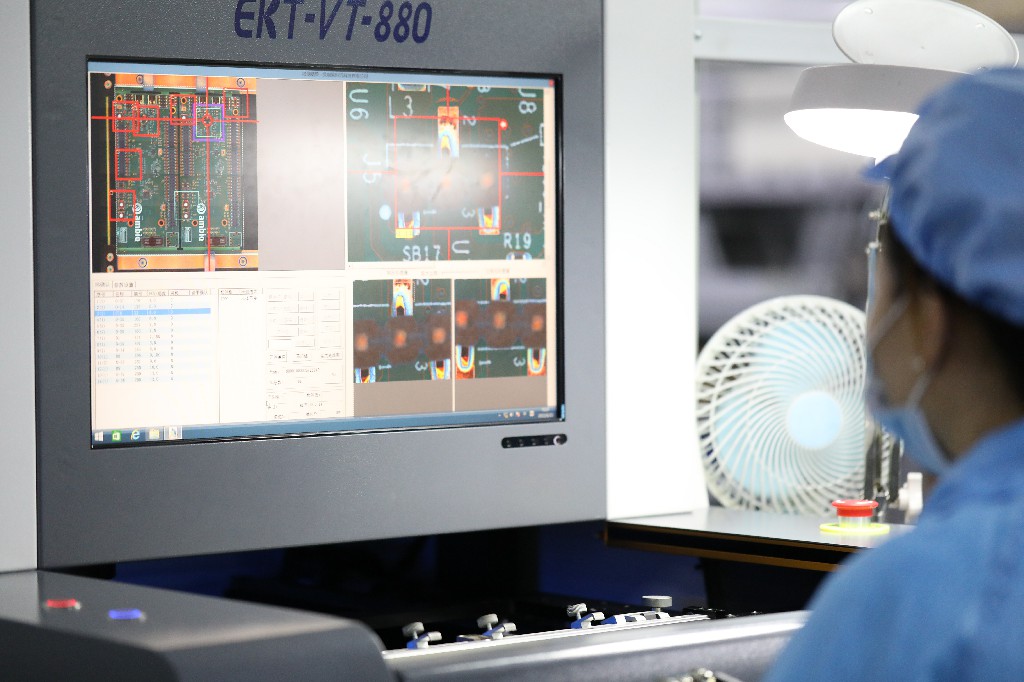
X-RAY與SAT檢測原理:為什么X-RAY只能掃描空洞不能掃描分層
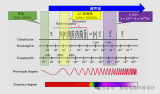
X-ray在芯片失效分析中的應用
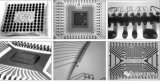
這些因素影響X-RAY射線檢測設備的價格
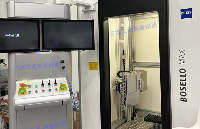
TLV8544 X-RAY框架變動,是否是因為DC差距導致的變動呢?
x-ray射線無損檢測第三方檢測機構廠家
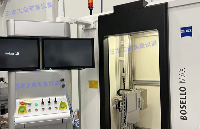
評論