在消費(fèi)電子追求極致顯示的浪潮中,Mini LED 以百萬(wàn)級(jí)對(duì)比度和長(zhǎng)壽命優(yōu)勢(shì)成為焦點(diǎn),而其核心工藝 —— 固晶,正面臨前所未有的挑戰(zhàn):如何將 50-100 微米的微型芯片,以亞微米級(jí)精度固定在基板上,并實(shí)現(xiàn)高效散熱與均勻發(fā)光?這一過(guò)程中,固晶錫膏作為 “隱形核心”,正通過(guò)材料創(chuàng)新與工藝協(xié)同,破解微型化帶來(lái)的多重難題。
一、Mini LED 固晶的三大核心挑戰(zhàn):精度、散熱與均勻性的微觀博弈
Mini LED 的微型化直接放大了固晶環(huán)節(jié)的技術(shù)難度。當(dāng)芯片尺寸縮小至傳統(tǒng) LED 的 1/10,每平方厘米需集成數(shù)千顆芯片,對(duì)固晶提出三重考驗(yàn):
1、精度極限:芯片間距縮小至 50 微米以下時(shí),固晶機(jī)需實(shí)現(xiàn) ±5 微米的位置精度,相當(dāng)于在指甲蓋大小的區(qū)域內(nèi)放置數(shù)百顆芯片,且位置誤差不超過(guò)人類頭發(fā)絲的 1/10。傳統(tǒng)單點(diǎn)轉(zhuǎn)移技術(shù)效率不足,而新興的巨量轉(zhuǎn)移技術(shù)雖提升速度,但芯片的吸附力控制、基板熱膨脹補(bǔ)償?shù)热孕柰黄疲駝t易導(dǎo)致發(fā)光單元位置偏移,形成顯示畫面的 “錯(cuò)位像素”。
2、散熱瓶頸:Mini LED 的功率密度高達(dá) 100W/cm2,熱量若無(wú)法及時(shí)導(dǎo)出,芯片結(jié)溫超過(guò) 125℃將導(dǎo)致光衰加速。傳統(tǒng)銀膠的導(dǎo)熱率僅 5-15W/m?K,難以滿足需求,而固晶錫膏憑借錫基合金的金屬鍵合特性,導(dǎo)熱率可達(dá) 60-70W/m?K,是銀膠的 5 倍以上,成為構(gòu)建高效散熱路徑的關(guān)鍵。
3、均勻性挑戰(zhàn):微型芯片的間隙僅 5-50 微米,錫膏的顆粒度與潤(rùn)濕性直接影響焊點(diǎn)質(zhì)量。若錫粉團(tuán)聚或氧化,易形成焊點(diǎn)空洞,導(dǎo)致局部散熱不良或機(jī)械強(qiáng)度不足,最終表現(xiàn)為顯示畫面的亮度不均或死燈現(xiàn)象。
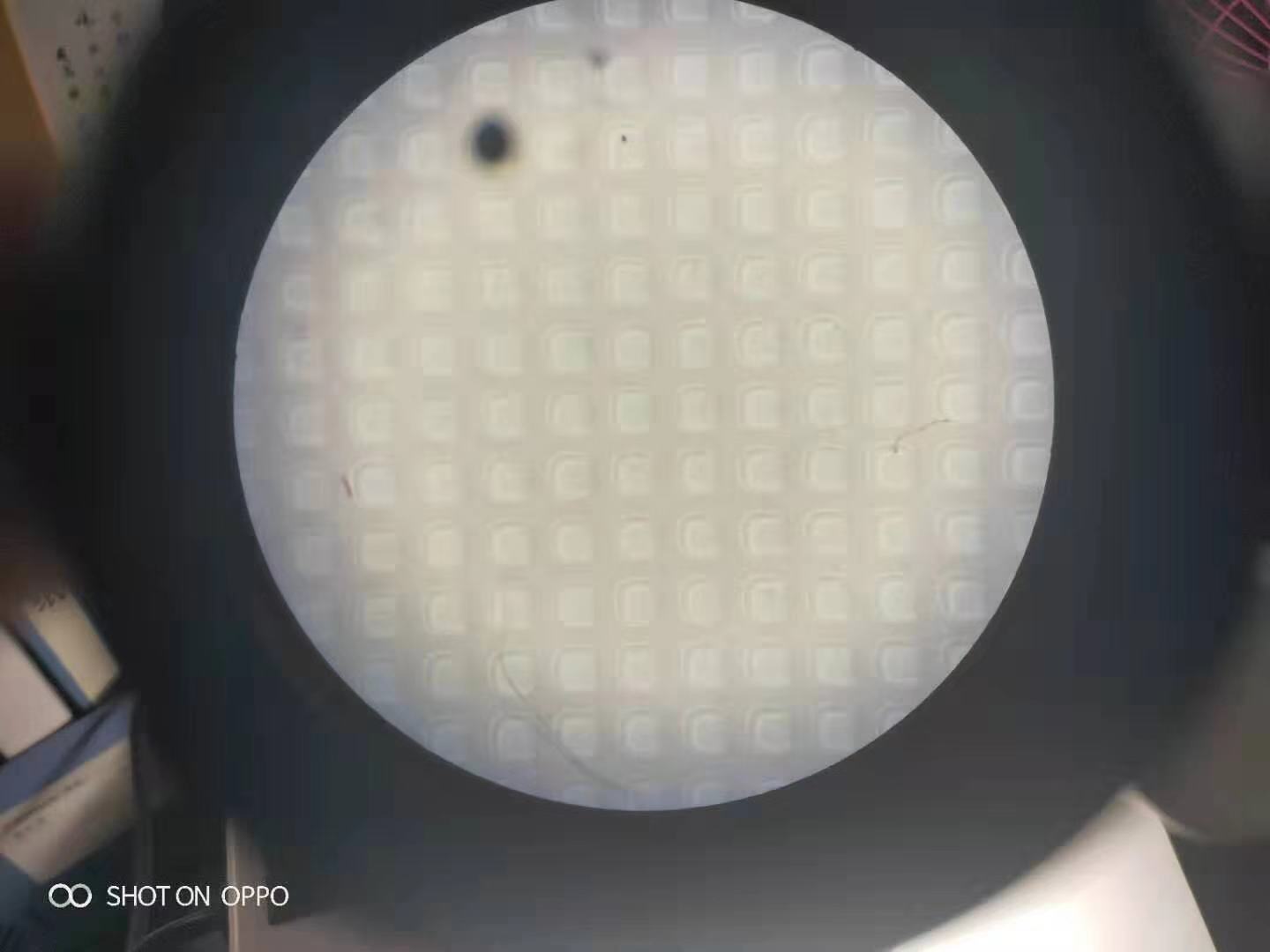
二、封裝工藝迭代:從基板選擇到結(jié)構(gòu)創(chuàng)新的系統(tǒng)適配
為應(yīng)對(duì)微型化挑戰(zhàn),Mini LED 封裝形成多種工藝路線,每種工藝均對(duì)固晶錫膏提出差異化需求:
1、COB(Chip on Board)直貼工藝:將芯片直接固晶在 PCB 或陶瓷基板上,通過(guò)去除支架結(jié)構(gòu)實(shí)現(xiàn)高密度集成(如 P0.6 以下微間距)。此工藝依賴基板平整度,要求錫膏具備低黏度(50-80Pa?s)與超細(xì)顆粒(5-15μm),以填滿 5-30 微米的間隙,確保芯片與基板的緊密貼合,避免因應(yīng)力集中導(dǎo)致的芯片破裂。
2、COG(Chip on Glass)玻璃基板工藝:利用玻璃的高平整度(粗糙度 Ra≤0.1μm)和低熱膨脹系數(shù),實(shí)現(xiàn) 50 微米以下超精密固晶,適用于車載顯示等高精度場(chǎng)景。由于玻璃基板的剛性特征,錫膏需兼顧高強(qiáng)度與柔韌性,通過(guò)添加微量 Ni、Co 等金屬增強(qiáng)相,將焊點(diǎn)剪切強(qiáng)度提升至 40MPa 以上,同時(shí)降低熱膨脹不匹配導(dǎo)致的焊點(diǎn)疲勞風(fēng)險(xiǎn)。
3、MiP(Mini LED in Package)芯片級(jí)封裝:先將芯片封裝成獨(dú)立模塊(如 2mm×2mm 的 RGB 單元),再通過(guò) SMT 貼裝到基板上。此工藝對(duì)錫膏的耐溫性要求更高 —— 首次固晶需采用中溫錫膏(熔點(diǎn) 170℃)固定芯片,二次焊接使用高溫錫膏(熔點(diǎn) 217℃)連接引腳,形成 “雙重保護(hù)” 焊點(diǎn),確保模塊在回流焊中不發(fā)生底層焊點(diǎn)重熔。
三、固晶錫膏的關(guān)鍵性能:從材料配方到微觀結(jié)構(gòu)的深度優(yōu)化
在 Mini LED 固晶中,錫膏的性能指標(biāo)直接決定封裝可靠性,其核心技術(shù)突破集中在三個(gè)維度:
1、超細(xì)顆粒與精密填充:采用氣霧化法制備 5-15μm 的 T6 級(jí)球形錫粉,圓度超過(guò) 0.95,表面氧化率控制在 0.5% 以下。這種 “微米級(jí)球形顆粒” 在印刷時(shí)可均勻滾動(dòng),配合低黏度載體,實(shí)現(xiàn) ±3μm 的焊點(diǎn)厚度控制,確保 5-50 微米間隙的填充率超過(guò) 98%,從源頭避免空洞缺陷。
2、高導(dǎo)熱合金體系:主流 SnAgCu 合金通過(guò)添加 0.5%-1% 的納米銀線或銅增強(qiáng)相,將導(dǎo)熱率提升至 65-70W/m?K,較純 SnAgCu 合金提升 10% 以上。這種 “金屬網(wǎng)絡(luò)增強(qiáng)” 結(jié)構(gòu),可快速疏導(dǎo)芯片產(chǎn)生的高熱量,將結(jié)溫降低 10-15℃,延緩光衰并延長(zhǎng)器件壽命。
3、環(huán)境適應(yīng)性配方:針對(duì)車載等高溫場(chǎng)景,開發(fā)耐高溫型錫膏(熔點(diǎn) 220-240℃),通過(guò)調(diào)整 Sn、Ag、Bi 的配比,使焊點(diǎn)在 150℃長(zhǎng)期運(yùn)行時(shí)強(qiáng)度保持率超過(guò) 95%;針對(duì)戶外顯示的高濕環(huán)境,采用無(wú)鹵素助焊劑,確保殘留物表面絕緣電阻>10^14Ω,避免電化學(xué)遷移導(dǎo)致的短路風(fēng)險(xiǎn)。
四、行業(yè)趨勢(shì):設(shè)備、材料、工藝的協(xié)同進(jìn)化推動(dòng)規(guī)模化落地
當(dāng)前,Mini LED 固晶技術(shù)正從單一環(huán)節(jié)優(yōu)化轉(zhuǎn)向全鏈條協(xié)同創(chuàng)新。
在設(shè)備端,高精度固晶機(jī)通過(guò)雙視覺(jué)對(duì)位系統(tǒng)與振動(dòng)補(bǔ)償算法,將固晶精度提升至 ±2 微米,配合巨量轉(zhuǎn)移技術(shù)(如電磁吸附、激光釋放),實(shí)現(xiàn)每小時(shí)數(shù)百萬(wàn)顆芯片的高速貼裝,解決效率與精度的平衡難題。
材料端的固晶錫膏持續(xù)突破,除了現(xiàn)有 Sn 基合金,新型 AuSn 合金錫膏憑借更高的熔點(diǎn)(280℃)和抗腐蝕能力,開始應(yīng)用于極端環(huán)境下的 Mini LED 封裝,而低溫固晶材料(如 SnBi 合金)則針對(duì) MEMS 傳感器等熱敏元件,將焊接溫度控制在 150℃以下。
工藝端的創(chuàng)新則體現(xiàn)在系統(tǒng)集成 ——COW(Chip on Wafer)晶圓級(jí)固晶技術(shù)興起,在晶圓階段完成芯片的批量焊接與封裝,從源頭控制波長(zhǎng)均勻性與焊點(diǎn)一致性,推動(dòng) Mini LED 從 “單芯片處理” 進(jìn)入 “晶圓級(jí)制造” 時(shí)代,大幅降低生產(chǎn)成本與良率損耗。
從精度控制到散熱優(yōu)化,從材料創(chuàng)新到工藝協(xié)同,固晶錫膏在 Mini LED 的微觀世界里扮演著 “連接基石” 的角色。它不僅是物理固定的粘合劑,更是構(gòu)建高效散熱路徑、保障長(zhǎng)期可靠性的核心材料。
隨著設(shè)備精度的提升、材料配方的迭代、工藝路線的成熟,Mini LED 正從高端小眾應(yīng)用走向消費(fèi)電子、車載顯示等大規(guī)模市場(chǎng),而固晶錫膏的持續(xù)創(chuàng)新,將不斷拓寬微型化封裝的可能性 —— 因?yàn)樵谖⒚准?jí)的精密連接中,每一次材料與工藝的進(jìn)步,都是顯示技術(shù)邁向極致的關(guān)鍵一步。
-
COB封裝
+關(guān)注
關(guān)注
4文章
72瀏覽量
15451 -
固晶
+關(guān)注
關(guān)注
0文章
8瀏覽量
6329 -
miniled
+關(guān)注
關(guān)注
18文章
868瀏覽量
40001
發(fā)布評(píng)論請(qǐng)先 登錄
教你判別固晶錫膏的品質(zhì)
Mini LED封裝時(shí)代,錫膏與共晶孰優(yōu)孰劣?
晨日率先在LED封裝領(lǐng)域提出倒裝封裝固晶錫膏、倒裝硅膠的解決方案
大為錫膏帶你認(rèn)識(shí)固晶錫膏的品質(zhì)
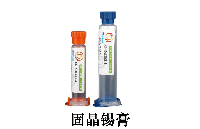
引領(lǐng)未來(lái)封裝技術(shù),大為打造卓越固晶錫膏解決方案
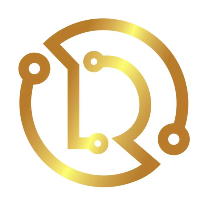
革新封裝工藝,大為引領(lǐng)中低溫固晶錫膏新時(shí)代
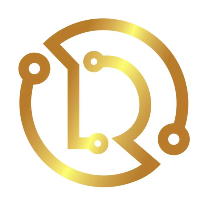
除了固晶工藝還有哪些封裝連接技術(shù)?錫膏為何成為高端制造的 “剛需”?
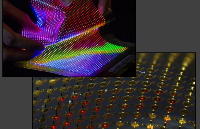
評(píng)論