凌晨三點,我被刺耳的手機鈴聲驚醒。電話那頭,夜班班長的聲音帶著焦慮:“張工,三號生產(chǎn)線的溫度傳感器報警了,我們已經(jīng)按照流程停機檢查,但暫時沒發(fā)現(xiàn)明顯異常。” 掛掉電話,我心里一沉。類似的情況這半年已經(jīng)發(fā)生了七八次,每次都是虛驚一場,卻造成了不小的經(jīng)濟損失,光是生產(chǎn)線重啟和物料浪費,就帶來了巨大的成本消耗。
在工業(yè) 4.0 浪潮下,我們工廠早就引入了預測性維護系統(tǒng),這原本是為了降本增效,讓設備管理從 “定期檢修” 邁向 “故障預警”。可現(xiàn)實卻不盡如人意,基于單一傳感器數(shù)據(jù)的系統(tǒng),就像 “盲人摸象”,難以準確把握設備的真實狀態(tài)。傳統(tǒng) AI 模型對噪聲數(shù)據(jù)、環(huán)境干擾的抵抗力也不足,誤報成了困擾我們的大難題。
記得有一次,振動監(jiān)測系統(tǒng)頻繁發(fā)出故障警報,維修人員緊急拆機檢查,結(jié)果卻發(fā)現(xiàn)設備并沒有問題,只是當時的負載波動較大。一次次的誤報,不僅消耗了大量的人力物力,也讓運維人員對這套系統(tǒng)失去了信任,甚至有人調(diào)侃:“這報警聲還不如直接當鬧鐘用。”
直到多模態(tài) AI 技術的出現(xiàn),給我們帶來了新的希望。它就像給設備維護工作注入了新的活力,為預測性維護提供了全新的解題思路。多模態(tài) AI 通過融合設備運行中的振動、溫度、聲音、電流、視覺圖像乃至工藝參數(shù)等多維度數(shù)據(jù),讓 AI 系統(tǒng)如同擁有 “視覺、聽覺、觸覺” 的工業(yè)醫(yī)生,能夠交叉驗證信息、挖掘隱性關聯(lián),顯著提升診斷可靠性。
為了引入這項技術,我們工廠開展了一系列的升級工作。在數(shù)據(jù)層,整合了 6 類傳感器、2 類視覺檢測單元及 MES 系統(tǒng)實時工藝參數(shù),每秒能處理超 2 萬數(shù)據(jù)點;決策層,通過聯(lián)邦學習實現(xiàn)跨產(chǎn)線知識共享,同時保障數(shù)據(jù)隱私;應用層,自動生成 “故障概率 - 緊急程度 - 維修建議” 三維度診斷報告,指導人員精準介入。
系統(tǒng)上線后的第一個月,就展現(xiàn)出了強大的能力。一天,系統(tǒng)同時捕捉到了設備的振動頻譜異常和潤滑油顆粒圖像變化,經(jīng)過分析,準確地預測出軸承即將出現(xiàn)故障。維修人員根據(jù)診斷報告,提前進行了維修,避免了一次可能導致生產(chǎn)線長時間停機的重大故障。
實施半年后,效果顯著。我們工廠的非計劃停機時間減少了 43%,備件庫存成本降低了 28%,更重要的是,再也沒有出現(xiàn)過因誤報導致的無謂拆機檢查。曾經(jīng)讓人頭疼的預測性維護系統(tǒng),如今真正成為了我們的 “決策大腦”。
不過,多模態(tài) AI 的規(guī)模化落地也并非一帆風順。在實際應用過程中,我們遇到了不少挑戰(zhàn)。數(shù)據(jù)融合成本就是一大難題,跨協(xié)議設備的接入、多模態(tài)數(shù)據(jù)的時間同步等技術細節(jié),都需要更成熟的工業(yè)級解決方案。高并發(fā)數(shù)據(jù)處理對本地化部署提出了新要求,邊緣算力瓶頸也亟待突破,輕量化模型與邊緣計算架構(gòu)成為了我們攻關的重點。而且,如何讓 AI 的 “黑箱決策” 轉(zhuǎn)化為可解釋的運維建議,贏得大家的信任,也是擺在我們面前的關鍵問題。
但我相信,隨著技術的不斷發(fā)展,這些問題都將被逐步解決。未來,隨著數(shù)字孿生、5G 專網(wǎng)、AI 生成式技術的融合,預測性維護或許會實現(xiàn)更大的跨越。設備不再僅僅是被動地等待故障被發(fā)現(xiàn),而是能夠?qū)崿F(xiàn) “健康自治”,系統(tǒng)可自主調(diào)整設備運行參數(shù)延緩故障,甚至通過模擬仿真提前規(guī)避風險。
回想起這一路走來的艱辛與收獲,我深刻地感受到,誤報困局的突破,本質(zhì)是工業(yè)認知智能的升維。當多模態(tài) AI 讓設備 “會說話”、讓數(shù)據(jù) “能思考”,預測性維護 2.0 正在重新定義工業(yè)運維的邊界。對于我們工廠來說,這場變革不僅是技術升級,更是一場圍繞設備全生命周期價值的效率革命。它讓我們在激烈的市場競爭中,有了更堅實的底氣和更廣闊的發(fā)展空間。
-
智能制造
+關注
關注
48文章
5871瀏覽量
77708 -
智慧工廠
+關注
關注
2文章
453瀏覽量
28109 -
設備管理系統(tǒng)
+關注
關注
0文章
78瀏覽量
2161 -
數(shù)字工廠
+關注
關注
0文章
64瀏覽量
5933 -
預測性維護
+關注
關注
1文章
48瀏覽量
3579
發(fā)布評論請先 登錄
海康威視發(fā)布多模態(tài)大模型AI融合巡檢超腦
設備遠程監(jiān)控與預測性維護系統(tǒng)架構(gòu)設計及應用實踐
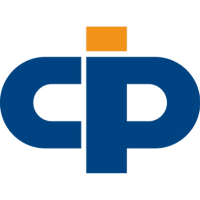
安霸在ISC West上推出下一代前端多模態(tài)AI技術
2025設備管理新范式:生成式AI在故障知識庫中的創(chuàng)新應用
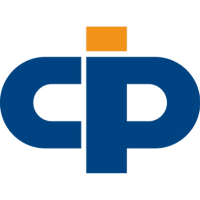
移遠通信智能模組全面接入多模態(tài)AI大模型,重塑智能交互新體驗
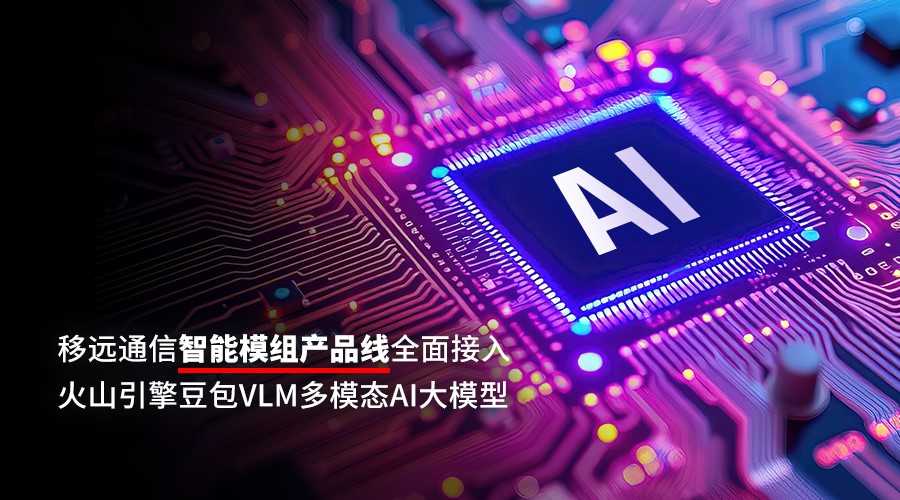
移遠通信智能模組全面接入多模態(tài)AI大模型,重塑智能交互新體驗
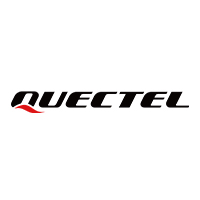
FPGA+AI王炸組合如何重塑未來世界:看看DeepSeek東方神秘力量如何預測......
設備“罷工”損失百萬?AI預測性維護來“救場”
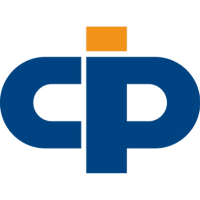
AI賦能邊緣網(wǎng)關:開啟智能時代的新藍海
設備管理系統(tǒng):如何實現(xiàn)預測性維護與故障預防?
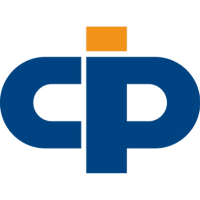
麻省理工科技評論:2025年AI領域突破性技術
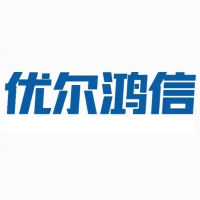
評論