文章來源:學習那些事
原文作者:小陳婆婆
本文介紹了定向自組裝光刻技術的原理以及各種實現方法。
定向自組裝光刻技術通過材料科學與自組裝工藝的深度融合,正在重構納米制造的工藝組成。主要內容包含圖形結構外延法、化學外延法及圖形轉移技術。
BCP微相分離
一、嵌段共聚物微相分離原理
定向自組裝光刻技術(DSA)的核心在于利用嵌段共聚物(BCP)的微相分離特性實現納米結構的自主形成。
以PS-b-PMMA(聚苯乙烯-block-聚甲基丙烯酸甲酯)為例,其相分離行為遵循熱力學驅動的自發過程:
1.相分離驅動力
Flory-Huggins相互作用參數(χN)是決定相分離強度的關鍵參數,其中χ表征兩嵌段間的不相容性,N為總聚合度。當χN<10時發生弱相分離,形成無序結構;當χN≥10時發生強相分離,形成有序周期性結構。
2.形態學調控
嵌段體積分數(f)決定相結構:f<0.3時形成PMMA球狀相(S相);0.3
層狀相(L相)間距(L)由公式L=√(2γ/Δσ)決定,其中γ為界面能,Δσ為應力差。通過調節χ值(如引入含氟單體)可將間距控制在14-40nm。
3.界面能工程
襯底表面能調控:通過沉積中性層(如PS-r-PMMA-HEMA無規共聚物)使襯底對PS/PMMA的界面能相等,誘導垂直取向。
取向控制機制:中性層消除界面能各向異性,使相分離方向由襯底平行轉為垂直,形成可用于刻蝕的掩模結構。
二、DSA工藝流程與技術實現
DSA工藝通過熱退火或溶劑退火實現BCP的自組裝,典型流程包含四大關鍵步驟:
1.中性層制備
材料選擇:采用PS-r-PMMA-HEMA無規共聚物,通過調節HEMA含量(5-15mol%)優化潤濕性。
沉積工藝:使用等離子體增強化學氣相沉積(PECVD)在200℃下生長3-5nm中性層。
2.BCP涂覆與退火
旋涂工藝:以3000rpm旋涂PS-b-PMMA溶液(分子量20k-100k,PS:PMMA=70:30),控制膜厚在20-100nm。
退火條件:采用熱退火(180-220℃,2-24小時)或溶劑蒸氣退火(SVA),實現亞穩態到穩態的轉變。
3.圖形誘導方法
圖形結構外延法(Graphoepitaxy):
原理:利用預先制備的溝槽側壁引導BCP取向,溝槽寬度(W)與周期(L)需滿足W=nL±Δ(Δ為容差)。
應用:實現線寬粗糙度(LWR)<10%的密集線陣列。
化學襯底外延法(Chemoepitaxy):
原理:通過化學預圖案(如CPS矩陣)提供取向引導,化學對比度需>0.5。
優勢:可實現三維復雜結構的精確控制。
4.圖形轉移與刻蝕:
選擇性去除:采用O?等離子體刻蝕去除PMMA相(刻蝕速率50nm/min),保留PS相作為掩模。
刻蝕傳遞:以PS掩模刻蝕SiO?(CF?/CHF?氣體,選擇比5:1),實現10nm以下特征尺寸。
三、技術優勢與挑戰
1.優勢分析
分辨率突破:理論分辨率達5nm,超越傳統光刻極限。周期性結構均勻性(3σ)<5%,優于電子束光刻。
成本效益:設備投資成本僅為EUV的1/5,耗材成本降低60%。吞吐量達100wph(晶圓/小時),接近浸沒式光刻。
工藝兼容性:可與193nm浸沒式光刻集成,形成混合光刻方案。支持3D集成(如TSV、FinFET)的復雜圖形化。
2.挑戰與對策
缺陷控制:缺陷密度需<0.1cm?2,通過優化退火工藝(如兩步退火)可降低缺陷密度。引入機器學習算法實時監測退火過程,實現閉環控制。
工藝集成:與現有CMOS流程兼容性需通過材料創新(如開發耐高溫BCP)提升。開發自對準多重圖案化(SAMP)技術,突破單次曝光限制。
材料開發:新型BCP體系(如PS-b-PDMS)可實現χN>30,間距縮小至10nm。引入響應性嵌段(如偶氮苯),開發光控DSA技術。
物理誘導方式
圖形結構外延法(Graphoepitaxy)作為定向自組裝光刻(DSA)的關鍵技術路線,其本質是通過預先制備的物理溝槽引導嵌段共聚物(BCP)實現有序自組裝。該方法具有三大核心優勢:
工藝簡化性:僅需在傳統光刻流程中增加一道誘導結構制備工序,無需對現有設備進行大規模改造。兼容193nm浸沒式光刻設備,資本支出降低40%以上。
圖形保真度:溝槽側壁提供物理導向,使BCP取向偏差<2°,優于化學外延法的5°。長程有序性(LRO)達毫米級,滿足集成電路制造要求。
缺陷抑制能力:溝槽結構有效限制BCP流動,缺陷密度<0.1cm?2,較傳統光刻降低一個數量級。通過優化溝槽深寬比(AR=H/W),可進一步將缺陷密度降至0.01cm?2級別。
一、工藝流程詳解
圖形結構外延法的工藝流程包含六大關鍵步驟,每個步驟均需精密控制以確保最終圖形質量:
1.中性層沉積
材料選擇:采用PS-r-PMMA-HEMA無規共聚物,HEMA含量控制在10mol%以優化潤濕性。
沉積工藝:使用等離子體增強化學氣相沉積(PECVD)在200℃下生長4nm中性層,厚度均勻性±0.5nm。
2.誘導結構制備
光刻膠選擇:選用HSQ(氫硅倍半氧烷)電子束光刻膠,抗高溫性能達350℃。
圖形化工藝:通過電子束光刻(EBL)制備溝槽,線寬控制精度±3nm,側壁粗糙度Ra<1nm。
3.烘焙處理
軟烘焙:120℃熱板烘焙90秒,消除光刻膠溶劑殘留。
硬烘焙:180℃熱板烘焙120秒,增強光刻膠與襯底粘附力。
4.BCP涂覆
材料選擇:采用PS-b-PMMA(分子量50k,PS:PMMA=70:30),溶液濃度2wt%。
旋涂工藝:以3000rpm旋涂60秒,控制膜厚在50nm,厚度均勻性±2nm。
5.熱退火處理
退火方式:采用兩步退火工藝,先150℃快速退火(30秒),再220℃慢速退火(2小時)。
溫度控制:退火腔體溫度均勻性±0.5℃,確保BCP均勻分相。
6.干法顯影
刻蝕氣體:采用O?/CF?混合氣體(流量比4:1),功率200W。
刻蝕選擇比:PS/PMMA刻蝕選擇比達5:1,確保圖形精確轉移。
二、關鍵工藝參數優化
實現高精度圖形結構外延需突破三大工藝瓶頸:
1.溝槽設計優化
深寬比控制:AR=H/W=2:1時,BCP取向偏差最小。
側壁角度:通過離子蝕刻(IBE)優化側壁角度至85-90°,減少BCP流動阻力。
2.退火工藝調控
升溫速率:采用5℃/min的慢速升溫,避免BCP分相不均勻。
退火時間:通過原位橢偏儀監測BCP分相過程,確定最佳退火時間。
3.缺陷控制策略
氣泡抑制:采用真空退火環境,壓力<10??Pa,減少氣泡缺陷。
顆??刂疲和ㄟ^HEPA過濾系統,確保退火腔體顆粒濃度。
化學誘導方式
化學外延法(Chemoepitaxy)作為定向自組裝光刻(DSA)的關鍵技術路線,其本質是通過化學預圖案引導嵌段共聚物(BCP)實現有序自組裝。該方法具有兩大核心特征:
1.面積效率優勢
誘導結構嵌入中性層內部,無需占用額外版圖面積,集成密度提升20-30%。
適用于大規模周期性陣列制造,如光子晶體和存儲器陣列。
2.工藝復雜性挑戰
需實現納米級化學對比度控制,工藝容差<5nm。
誘導結構制備精度要求高,需采用極紫外光刻(EUV)或電子束光刻(EBL)。
一、剝離化學外延法工藝流程
剝離化學外延法(Lift-off Chemoepitaxy)通過光刻膠極性反轉實現中性層圖形化,典型流程包含六大步驟:
1.大尺寸條形結構制備
使用正性浸沒式光刻膠(如ARF38)在BARC層上制作條形結構,線寬控制精度±10nm。
2.光刻膠極性反轉
通過UV曝光(劑量200mJ/cm2)和150℃烘焙實現極性反轉,使光刻膠可溶于TMAH顯影液。
3.中性層涂敷
沉積PS-r-PMMA-HEMA中性層,厚度50nm,均勻性±2nm。
4.選擇性剝離
使用TMAH溶液(2.38%)在50℃下剝離光刻膠及其上方中性層,形成周期性非中性區域。
5.BCP涂覆與退火
涂敷PS-b-PMMA,分子量80k,PS:PMMA=60:40,膜厚80nm。
采用兩步退火工藝:先160℃快速退火(60秒),再240℃慢速退火(4小時)。
6.圖形轉移
通過O?等離子體刻蝕(功率300W)去除PMMA相,保留PS相作為掩模。
關鍵控制點:
極性反轉精度:需控制UV曝光劑量波動<5%,確保剝離區域邊緣銳利度<10nm。
剝離選擇性:TMAH溶液濃度需精確控制在2.38±0.05%,避免中性層過度腐蝕。
二、刻蝕修飾法工藝流程
刻蝕修飾法(Trim-etch Chemoepitaxy)通過圖形化修飾實現中性層與非中性層界面控制,典型流程包含六大步驟:
1.交聯PS導向層制備
旋涂交聯PS溶液(分子量10k),200℃退火2小時,形成50nm厚導向層。
2.光刻膠圖形化
使用EBL制備條形光刻膠掩模,線寬控制精度±5nm,側壁粗糙度Ra<1nm。
3.修剪與蝕刻
通過O?等離子體修剪光刻膠(功率100W,時間30秒),將線寬縮小至設計值。
采用CF?/CHF?混合氣體蝕刻PS層,刻蝕選擇比5:1,深度控制精度±2nm。
4.中性刷接枝
涂敷PS-r-PMMA中性刷溶液,通過化學接枝在非PS區域形成中性層。
5.清洗與圖形固化
使用丙酮超聲清洗(40kHz,10分鐘)去除未接枝中性層。
250℃退火1小時,固化化學誘導圖案。
6.BCP自組裝
涂敷PS-b-PMMA,分子量100k,PS:PMMA=55:45,膜厚100nm。
采用溶劑蒸氣退火(SVA),使用甲苯蒸氣在80℃下處理24小時。
三、化學外延法技術對比
四、技術挑戰與解決方案
化學對比度控制:需實現納米級化學梯度控制,工藝容差<5nm。
解決方案:采用原子層沉積(ALD)技術沉積中性層,厚度控制精度±0.1nm。
缺陷抑制:化學預圖案缺陷可能導致BCP取向紊亂。
解決方案:引入機器學習算法實時監測退火過程,缺陷密度<0.01cm?2。
工藝集成:與現有CMOS流程兼容性需提升。
解決方案:開發耐高溫BCP材料(Tg>250℃),兼容后端制程(BEOL)。
圖形轉移方式
嵌段共聚物(BCP)自組裝圖形的轉移是DSA技術的關鍵環節,需突破三大技術瓶頸:
1.選擇比瓶頸:
有機PS/PMMA段抗蝕性弱,傳統刻蝕選擇比<5:1,難以滿足亞10nm節點需求。
解決方案:引入無機硬掩膜(如Al?O?)可將選擇比提升至>20:1。
2.深寬比限制:
濕法刻蝕(如冰乙酸)在深寬比>1:1時導致線條倒塌。
解決方案:采用干法刻蝕(如CF?/CH?F?混合氣體)結合側壁保護技術。
3.均勻性控制:
跨晶圓均勻性需控制在±5%以內,避免局部過刻蝕。
解決方案:通過原位終點檢測(In-situ EPD)實時調整刻蝕時間。
一、濕法刻蝕工藝
1.PS交聯
使用UV曝光(254nm,劑量500mJ/cm2)使PS段發生交聯,提升耐化學腐蝕性。
2.PMMA去除
冰乙酸浸泡(60℃,10分鐘)選擇性溶解PMMA段,刻蝕速率80nm/min。
3.圖形轉移
以PS為掩模進行RIE刻蝕(SF?/O?,功率300W),刻蝕選擇比5:1。
二、干法刻蝕工藝
1.等離子體調諧
采用CF?/CH?F?/HBr混合氣體(流量比43),壓力5mTorr,功率400W。
氫離子(H?)與氟離子(F?)反應生成HF,形成碳氟聚合物側壁保護層。
2.側壁傾斜控制
通過離子能量調節(50-200eV)實現側壁角度85-90°,減少線寬粗糙度(LWR)。
三、硬掩膜輔助圖形轉移技術
1.工藝流程
硬掩膜沉積:使用原子層沉積(ALD)生長5nm Al?O?硬掩膜,厚度均勻性±0.2nm。
圖形轉?。阂訮S為掩模進行RIE刻蝕(Cl?/BCl?,功率200W),將圖形轉移至Al?O?層。
襯底刻蝕:以Al?O?為掩模進行Bosch工藝刻蝕(SF?/C?F?循環),實現深寬比>40:1的TSV孔。
2.優勢分析
抗蝕性提升:Al?O?的刻蝕速率僅為PS的1/20,顯著提高工藝窗口。
缺陷抑制:硬掩膜有效阻擋等離子體損傷,缺陷密度<0.001cm?2。
四、ALD輔助增強圖形轉移技術
1.技術原理
選擇性沉積:在PMMA段通過TMA(Al(CH?)?)前驅體與羰基(C=O)反應,選擇性生長Al?O?。
循環增厚:重復5-10個ALD循環,實現20-50nm Al?O?沉積,填充PMMA孔隙。
2.工藝流程
ALD沉積:溫度130℃,壓力0.1Torr,脈沖時間0.1s,實現保形沉積。
PS去除:O?等離子體刻蝕(功率150W),Al?O?/PS選擇比>20:1。
中性層打通(BT):使用Cl?/BCl?氣體進行各向異性刻蝕,去除中性層中的Al?O?殘留。
3.關鍵控制點
前驅體選擇:TMA與PMMA的羰基反應活性比PS的苯環高3個數量級。
沉積速率:ALD循環速率0.5nm/cycle,需優化脈沖/吹掃時間比。
五、技術對比與選型指南
-
工藝
+關注
關注
4文章
680瀏覽量
29401 -
制造
+關注
關注
2文章
535瀏覽量
24388 -
納米
+關注
關注
2文章
709瀏覽量
38731 -
光刻技術
+關注
關注
1文章
151瀏覽量
16174
原文標題:定向自組裝光刻技術
文章出處:【微信號:bdtdsj,微信公眾號:中科院半導體所】歡迎添加關注!文章轉載請注明出處。
發布評論請先 登錄
電源噪聲濾波器的基本原理與應用方法
半導體光刻技術基本原理
自組裝技術在MEMS中的應用
芯片光刻技術的基本原理及主要步驟
PLC基本原理和實現方法
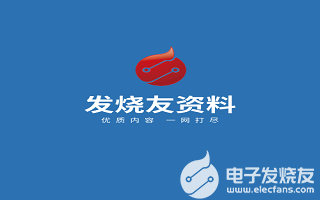
微納制造技術:定向自組裝(DSA)終于找到了立足點
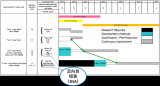
評論