文章來源:學習那些事
原文作者:小陳婆婆
本文介紹了快速熱處理技術的原理、特點與應用。
在納米尺度集成電路制造領域,快速熱處理(RTP)技術已成為實現器件性能突破與工藝優化的核心工具。相較于傳統高溫爐管工藝,RTP通過單片式作業模式與精準的熱過程控制,有效解決了先進制程中熱預算控制、超淺結形成及工藝一致性的技術痛點。
快速熱處理工藝機理與特點
一、技術演進背景與核心需求
隨著半導體工藝向5nm及以下節點推進,器件特征尺寸持續縮小與300mm乃至450mm晶圓尺寸擴展成為并行趨勢。這一技術演進對熱處理工藝提出雙重挑戰:
超淺結形成:源漏區雜質分布需同時滿足低薄層電阻與亞10nm結深要求,傳統爐管工藝因升溫速率不足(<50℃/s)導致雜質橫向擴散加劇,難以維持陡直度;
熱預算限制:大尺寸晶圓在爐管退火中存在徑向溫度梯度(>10℃/cm),邊緣過沖效應顯著,制約了工藝窗口的擴展。
二、快速熱處理技術機理與實現路徑
RTP技術通過輻射加熱機制實現晶圓級瞬時熱沖擊,其技術特征可歸納為:
超快溫變速率:采用高功率鹵素燈陣或激光加熱,升溫/降溫速率突破250℃/s,遠超傳統爐管的5-10℃/s;
精準熱控制:嵌入式紅外測溫系統與閉環反饋控制,實現片內溫度均勻性±1℃(3σ),支持400-1400℃寬溫區動態調控;
低熱應力設計:石英支架三點支撐結構最小化熱接觸阻抗,配合真空或低壓環境,消除對流散熱干擾。
三、與傳統爐管工藝的性能對比
四、典型工藝及應用場景
超淺結雜質激活:針對超低能離子注入(<1keV),RTP通過毫秒級退火實現雜質電激活率>95%,同時將瞬時增強擴散(TED)效應抑制在2nm以內,有效緩解短溝道效應。
金屬硅化物形成:在Ni/Co硅化物制備中,RTP兩步法工藝(500℃成核+850℃合金化)可獲得低電阻率(<10μΩ·cm)的硅化物層,相較爐管工藝界面粗糙度降低60%。
介質層熱處理:對于摻磷二氧化硅(PSG)回流工藝,RTP的階梯式升溫曲線(400℃ → 600℃ → 900℃)實現間隙填充能力提升3倍,同時將硼穿透效應控制在0.5nm/s以下。
先進柵極工程:在高k金屬柵(HKMG)工藝中,RTP用于激活界面層氮化與金屬柵沉積后的快速退火,確保等效氧化層厚度(EOT)及柵極漏電流。
快速熱處理技術分類與應用
在先進半導體制造領域,快速熱處理(RTP)技術憑借其毫秒級溫變控制能力,已成為實現納米尺度器件性能突破的關鍵工藝。
根據加熱機制與能量傳輸方式的差異,RTP技術可細分為絕熱型、熱流型與等溫型三大技術路線,各類技術在熱沖擊特性、工藝適用性及集成度方面展現出獨特的優勢與挑戰。
一、絕熱型RTP:超快表面熱沖擊技術
技術特征:采用寬束相干光源(如準分子激光器),通過納秒級脈沖激光實現晶圓表面瞬時熔融。激光脈沖寬度<100ns,能量僅在表面數納米深度被吸收,形成縱向溫度梯度>10?℃/cm。如圖(a)所示,激光照射后熔融層在亞微秒內快速凝固,熱量尚未傳導至襯底即完成再結晶過程。
核心優勢:超淺結形成能力:表面熔融深度可通過能量密度精準調控(5-50nm),適用于超低能離子注入后的超淺結激活(結深<10nm);零熱預算損耗:熱量未傳導至襯底,完美規避雜質擴散問題,特別適用于需要嚴格限制熱影響的3D NAND垂直溝道制備。
技術挑戰:需解決激光能量密度均勻性(±2%)控制難題,避免局部過熱導致的表面粗糙化;設備成本高昂,單脈沖能量穩定性需達到±1%以內,對光源壽命管理提出嚴苛要求。
典型應用:22nm以下節點FinFET的源漏區超淺結激活;3D集成中TSV側壁鈍化層的快速修復。
二、熱流型RTP:選擇性局部加熱方案
技術特征:采用高功率密度點光源(如CO?激光或電子束),通過光柵式掃描實現局部加熱。光束直徑<1mm,掃描速度可達100mm/s,單點停留時間10??~10?2s。如圖(b)所示,熱量在表面累積后向縱深傳導,形成深度約10μm的熱影響區。
核心優勢:空間選擇性加熱:可實現納米級熱區控制,適用于三維集成中的局部退火(如TSV底部歐姆接觸);低熱應力設計:通過掃描路徑優化,可將熱應力梯度控制在<5MPa/μm,顯著降低晶圓翹曲風險。
技術挑戰:掃描重疊區域易產生過熱(>5%),需采用閉環反饋系統實時修正功率輸出;加熱效率低,單晶圓處理能耗是等溫型RTP的3-5倍。
典型應用:5nm節點GAA FET納米片邊緣鈍化;異質集成中III-V族材料與硅基底的低溫鍵合。
三、等溫型RTP:量產型全片均勻加熱
技術特征:采用寬束非相干光源(如鎢鹵燈陣列),通過石英窗對晶圓進行全片輻照加熱。退火時間1-100s,溫度均勻性±1℃(3σ),熱預算控制精度達0.1℃·s。如圖(c)所示,熱量通過熱輻射與熱傳導雙重機制傳遞,實現片內橫向/縱向溫度梯度<2℃/cm。
核心優勢:高吞吐量設計:單腔體處理能力>150wph(12英寸晶圓),設備綜合效率(OEE)>90%;工藝兼容性廣:支持從離子注入激活到金屬硅化物形成的全流程熱處理,特別適用于:NiSi/CoSi?硅化物制備(退火溫度400-600℃,電阻率<10μΩ·cm);摻磷二氧化硅(PSG)介質層回流(溫度梯度<1℃/cm,填充能力提升3倍)。
技術挑戰:全片加熱導致熱預算較高,需通過脈沖式功率調制(PWM)將熱沖擊降低30%;燈管壽命管理至關重要,鎢鹵燈壽命>5000h,需配備自動更換模塊以維持產能。
典型應用:28nm以下節點后端制程(BEOL)的低介電常數(Low-k)介質固化;高遷移率溝道材料(如Ge、SiGe)的應變層退火。
四、技術路線對比與選型建議
研發階段超淺結探索:優先選用絕熱型RTP,以實現亞10nm結深控制;
先進封裝局部修復:熱流型RTP為首選,兼顧精度與熱應力控制;
大規模量產:等溫型RTP憑借高吞吐量與低成本優勢成為主流方案。
快速熱處理(RTP)退火技術特點
在先進半導體制造領域,快速熱處理(RTP)技術憑借其獨特的熱力學特性與工藝優勢,已成為突破深亞微米制程瓶頸的核心工具。相較于傳統高溫爐管工藝,RTP在加熱機制、熱響應速度及工藝可控性方面展現出革命性差異,其技術特性可歸納為以下六大維度:
一、加熱機制革新:從熱對流到輻射主導
傳統爐管依賴電阻絲加熱,通過熱對流與熱傳導實現晶圓升溫,屬于典型的“熱壁工藝”。而RTP采用寬譜輻射光源(如鎢鹵燈、氙燈),其波長范圍精準匹配硅材料的本征吸收帶,使晶圓吸收效率>90%。石英腔壁對此波段輻射透明,維持低溫狀態(<100℃),形成“冷壁工藝”,顯著降低背景粒子沾污風險。
二、溫度控制精度:從宏觀平衡到納米級調控
傳統爐管通過熱平衡實現溫度均勻性(±2℃),但響應速度滯后(時間常數>10min)。RTP則采用嵌入式紅外測溫儀(響應時間<1ms)與閉環反饋系統,實現:
片內均勻性:通過動態功率調制(PWM),將溫度偏差控制在±1℃(3σ);
空間分辨率:支持局部加熱(<1mm2),適配三維集成中的TSV熱處理需求;
熱沖擊控制:脈沖式加熱(1000℃/s升溫)結合快速冷卻(>200℃/s降溫),實現超淺結(<8nm)激活。
三、熱響應速度:從分鐘級到毫秒級跨越
RTP的升降溫速率達10-200℃/s,較傳統爐管(5-50℃/min)提升2-3個數量級。這一突破源于:
低熱容設計:單片作業模式(300mm晶圓熱容~0.5J/℃)替代批處理(25片批熱容~12.5J/℃);
高效能量耦合:輻射加熱直接作用于晶圓表面,熱傳遞路徑縮短90%;
快速抽氣系統:真空環境消除對流散熱,加速冷卻過程。
四、工藝環境優化:從熱壁污染到冷壁潔凈
傳統爐管的熱壁環境易導致:
金屬沾污:爐管內壁在1000℃以上釋放Fe、Cr等金屬離子(濃度>1E10atoms/cm2);
顆粒生成:熱應力導致石英件剝落(顆粒尺寸>0.3μm)。
RTP的冷壁工藝將背景溫度控制在<150℃,使金屬污染降低90%;顆粒缺陷密度<0.01顆/cm2,滿足先進制程(<7nm)的潔凈度要求。
五、作業模式變革:從批處理到單片化生產
RTP的單片作業模式實現:
工藝靈活性:支持不同晶圓獨立設置工藝參數(溫度、時間、氣氛);
產能優化:通過快速換片機構(<5s),實現UHP(單位小時產出)>150wph;
成本效益:相較于批處理爐管,單片RTP設備占地面積減少50%,能耗降低60%。
六、熱預算控制:從高能耗到綠色制造
傳統爐管的熱預算(Thermal Budget)高達1000℃·s以上,導致:雜質擴散失控:硼/磷擴散長度>50nm;界面劣化:高k介質/金屬柵界面層增厚(>1nm)。
RTP通過以下技術實現熱預算<10℃·s:瞬時加熱,毫秒級脈沖退火,抑制雜質擴散;選擇性激活,僅對注入層加熱,保護深埋層結構;低溫工藝擴展,支持200℃以下介質固化,適配柔性電子需求。
-
集成電路
+關注
關注
5422文章
12030瀏覽量
368161 -
半導體
+關注
關注
335文章
28848瀏覽量
236643 -
工藝
+關注
關注
4文章
680瀏覽量
29408
原文標題:半導體工藝制造——快速熱處理
文章出處:【微信號:bdtdsj,微信公眾號:中科院半導體所】歡迎添加關注!文章轉載請注明出處。
發布評論請先 登錄
2019年德國熱處理暨工業爐展覽會
快速循環熱處理對(Co0.35Fe0.65)99O1薄膜磁性
快速熱處理設備
高強度緊固件熱處理技術提升
國外熱處理技術現狀及熱處理設備
真空熱處理爐的節能技術
軸承熱處理發展歷程及技術應用效果
熱處理生產線淬火技術策略的設計與通訊
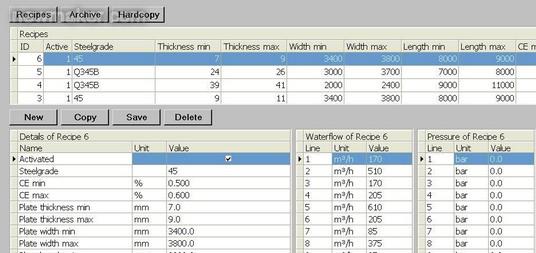
熱處理生產線淬火技術策略的設計與通訊
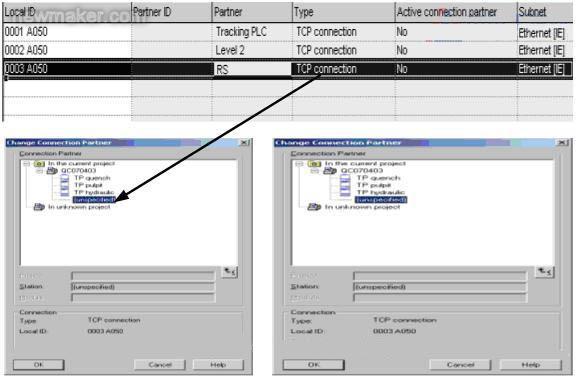
超大規模集成電路快速熱處理技術
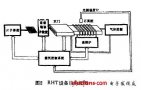
熱處理的定義與激光熱處理原理
半導體行業常用熱處理設備
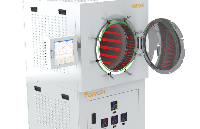
評論