電子發(fā)燒友網(wǎng):本文主要講述了汽車系統(tǒng)中的功率電子技術(shù)。
摘要:20世紀(jì)初,電子產(chǎn)品就被運(yùn)用到汽車系統(tǒng)中。此外,在20世紀(jì)60年代,隨著固體電子產(chǎn)品的出現(xiàn),汽車電子因此變得盛行起來(lái)。現(xiàn)今存在著幾種推動(dòng)汽車市場(chǎng)對(duì)電子產(chǎn)品的需求,尤其是功率半導(dǎo)體器件需求的趨勢(shì)。它們分別是:
(1)先進(jìn)的動(dòng)力傳動(dòng)系控制系統(tǒng)提高了燃油經(jīng)濟(jì)性,減少了車輛排放。這些系統(tǒng)必須更精確地控制燃燒過(guò)程,連續(xù)不斷地提供狀態(tài)檢查,同時(shí)在系統(tǒng)需要正常運(yùn)作所必需的功率和模擬控制功能。飛兆半導(dǎo)體的40V和60V PowerTrench MOSFET器件、高側(cè)開關(guān)以及智能點(diǎn)火產(chǎn)品能夠滿足這些要求。
(2)對(duì)于乘客舒適性和便利性功能的顯著需求,如座椅加熱和座椅制冷、自動(dòng)座椅定位、高級(jí)照明以及多區(qū)暖通空調(diào)(HVAC)。這些系統(tǒng)應(yīng)用都需要更大的功率和更多的功率管理。飛兆半導(dǎo)體的集成高側(cè)開關(guān)等產(chǎn)品具有高效控制和管理上述功率負(fù)載的功能。
(3)電動(dòng)和混合電動(dòng)推進(jìn)系統(tǒng)等替代動(dòng)力傳動(dòng)系技術(shù)需要顯著增加汽車的功率處理能力,需要能夠處理1kW~40kW的DC/DC轉(zhuǎn)換器等新型汽車電子產(chǎn)品。根據(jù)車輛的結(jié)構(gòu),需要使用集成化混合動(dòng)力總成(Integrated Starter Generator, ISG)和牽引馬達(dá)逆變器來(lái)處理5kW~120kW或更高功率。飛兆半導(dǎo)體的PowerTrench MOSFET、場(chǎng)截止IGBT、智能開關(guān)和柵極驅(qū)動(dòng)器等通過(guò)了汽車產(chǎn)品認(rèn)證的功率電子產(chǎn)品,采用分立或先進(jìn)模塊形式提供,為這些先進(jìn)系統(tǒng)提供了高成本效益解決方案。
(4)電動(dòng)助力轉(zhuǎn)向等成熟的輔助系統(tǒng)正在越來(lái)越多地從機(jī)械式轉(zhuǎn)向電子式。隨著發(fā)展,這些系統(tǒng)要求更大的電流密度和更低的功率消耗。飛兆半導(dǎo)體的30/40V MOSFET和汽車功率模塊(APM)技術(shù)是提供這些應(yīng)用所需的高效率和高功率密度解決方案的基礎(chǔ)。
使用飛兆半導(dǎo)體智能功率和功率技術(shù)的系統(tǒng)
1.分立式功率器件(DC-DC轉(zhuǎn)換器)
目前,最重要的環(huán)境問(wèn)題之一就是作為運(yùn)輸主要能源之一的碳?xì)浠衔锶紵a(chǎn)生的污染。混合動(dòng)力車(HEV)和電動(dòng)車(EV)正逐漸成為“綠色”運(yùn)輸?shù)奶娲鷦?dòng)力傳動(dòng)系統(tǒng)。這些車輛不僅涉及牽引部件,而且推動(dòng)了電能轉(zhuǎn)換方面的新應(yīng)用。混合動(dòng)力車輛內(nèi)的一種關(guān)鍵模塊便是用于電氣負(fù)載輔助電源的DC/DC轉(zhuǎn)換器,因?yàn)镠EV和EV仍然使用頭/尾燈、加熱風(fēng)扇以及音頻系統(tǒng)等輔助負(fù)載。該轉(zhuǎn)換器必須具有處理從高電壓轉(zhuǎn)換至12V電壓的能力,如圖1所示。
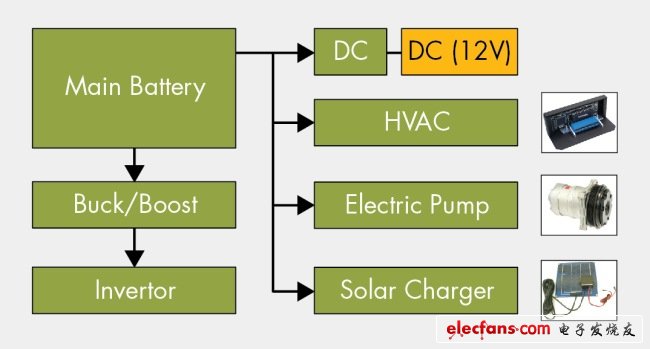
圖1 HEV/EV電氣負(fù)載需要能量轉(zhuǎn)換。
因此,應(yīng)用工程師們將注意力集中在HEV和HE系統(tǒng)中的MOSFET和IGBT等高電壓功率器件上。有幾種控制從高電壓到低電壓的能量轉(zhuǎn)換方法。通常使用高電壓和低電壓之間隔離的全橋和移相技術(shù),這類應(yīng)用中的輔助功率轉(zhuǎn)換器代表著電池組對(duì)高壓直流總線的高效管理,根據(jù)電動(dòng)馬達(dá)的功率不同,范圍在200V~800V之間。
此外,系統(tǒng)的效率是一個(gè)關(guān)鍵特性,并且是設(shè)計(jì)選擇的重要參數(shù)。轉(zhuǎn)換器的設(shè)計(jì)趨勢(shì)是在寬負(fù)載條件范圍內(nèi)達(dá)到90%或者更高的效率。
轉(zhuǎn)換器的可靠性是至關(guān)重要的,因?yàn)楣收蠒?huì)引起12V電池的泄放,從而造成所有靠電池電力驅(qū)動(dòng)的附件的故障。另一方面,不能忽略效率和電磁兼容(EMC)問(wèn)題。因此,有源箝位等軟開關(guān)和能量回收技術(shù)非常有益。
2.汽車照明
為了處理系統(tǒng)性和隨機(jī)性故障,使用分立MOSFET、智能MOSFET功率開關(guān)以及IGBT等電子器件來(lái)替代機(jī)械式開關(guān)和繼電器,用于控制車燈、柴油車預(yù)熱塞系統(tǒng)、點(diǎn)火系統(tǒng)以及馬達(dá)。智能功率器件(SPD)可以在消除機(jī)械噪聲和燃弧的同時(shí)提高質(zhì)量和可靠性。
圖2所示的智能功率器件是一款N溝道功率場(chǎng)效應(yīng)管(FET),具有一個(gè)內(nèi)部電源、電流受控輸入、帶負(fù)載電流感測(cè)的診斷反饋功能以及嵌入式保護(hù)功能。使用chip-on-chip和chip-by-chip技術(shù)集成功率級(jí)、控制、驅(qū)動(dòng)以及保護(hù)電路。
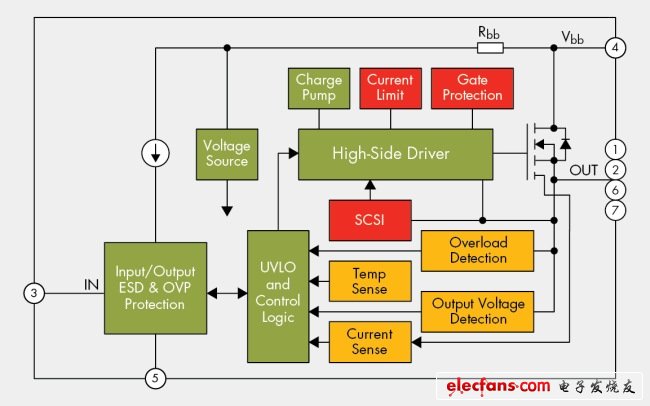
圖2 智能MOSFET結(jié)構(gòu)圖。
SPD的主要目標(biāo)是替代汽車?yán)^電器和熔斷器。智能開關(guān)能夠?qū)㈤_關(guān)和保護(hù)功能結(jié)合在單一芯片中。因此,從總體成本角度看,SPD可以提供較繼電器和熔斷器更便宜的解決方案。除了保護(hù)功能外,SPD具有減少線束,加入診斷功能和實(shí)現(xiàn)脈寬調(diào)制的更多優(yōu)勢(shì),所以,SPD不僅能夠保護(hù)自身,還能保護(hù)與其相連的負(fù)載和鄰近器件。可以使用帶有一些外部元件的應(yīng)用電路,依照應(yīng)用系統(tǒng)正確地運(yùn)作系統(tǒng)。
3.汽車功率模塊(APM)
高壓(600 VDC)和低壓(12-24VDC)系統(tǒng)都可以使用APM。飛兆半導(dǎo)體向汽車市場(chǎng)提供用于高壓和低壓系統(tǒng)的APM器件,它們幾乎都用來(lái)驅(qū)動(dòng)三相馬達(dá)和制動(dòng)器。兩種電壓范圍的APM都采用直接鍵合銅(DBC)技術(shù)來(lái)實(shí)現(xiàn)熱傳導(dǎo)。
低壓(LV)意味著以更大的電流來(lái)驅(qū)動(dòng)通常與該類型解決方案相關(guān)聯(lián)的較大負(fù)載。低壓應(yīng)用使用30V~60V N溝道MOSFET。電動(dòng)助力轉(zhuǎn)向和電驅(qū)動(dòng)液壓混合轉(zhuǎn)向是兩種最普遍的LV-APM解決方案。峰值相位電流能夠達(dá)到100A以上。這需要大的銅質(zhì)內(nèi)部結(jié)構(gòu),用于芯片焊盤(die paddle)和電流通路以及多個(gè)大電流粘合引線。正溫度系數(shù)(PTC)器件、無(wú)源EMC元件、分流器都達(dá)到了更高的集成度并提高了可靠性。電動(dòng)助力轉(zhuǎn)向中使用APM是實(shí)現(xiàn)機(jī)電一體化封裝和低系統(tǒng)成本的關(guān)鍵。在靜態(tài)停車時(shí),相比液壓系統(tǒng),降低寄生引擎負(fù)載可以減小車輛引擎的尺寸,從而更小型車輛。低壓模塊用于EV/HEV車輛,也用在傳統(tǒng)的內(nèi)燃式引擎汽車上。
高壓應(yīng)用主要包括由高母線電壓或主電池組供電的泵和風(fēng)扇。典型的峰值相位電流<20A。這一市場(chǎng)中的模塊化解決方案類似于許多工業(yè)市場(chǎng)中的應(yīng)用,并使用類似的功率模塊,IGBT和MOSFET解決方案均可使用。典型的模塊有高壓柵極驅(qū)動(dòng)器,以及在共橋回路處用于診斷的某種電流水平感測(cè)。高壓結(jié)構(gòu)必須考慮到引腳間隙要求。在熱管理方面,產(chǎn)品分為帶或不帶增強(qiáng)熱傳導(dǎo)的類型。模塊化解決方案是小型集成解決方案的關(guān)鍵,功率處理器件位于制動(dòng)器附近,甚至工作于變速箱等極端環(huán)境中。高壓模塊幾乎都用于EV/HEV車輛中。
?? 詳細(xì)的應(yīng)用示例
1.用于DC-DC應(yīng)用的高壓分立式解決方案
在現(xiàn)今的HEV和EV中,高壓電池組為電氣牽引系統(tǒng)提供行駛所需的能量。普通的12V系統(tǒng)仍然存在,為平常的汽車負(fù)載(輔助電池為頭/尾燈、加熱風(fēng)扇以及音頻系統(tǒng)等所有電氣負(fù)載供電)提供能量,而高壓總線則為牽引逆變器和馬達(dá)供電。
如下所示,需要使用汽車DC-DC轉(zhuǎn)換器。建議DC/DC轉(zhuǎn)換器具有以下關(guān)鍵功能:
(1)一個(gè)輸入的低壓端標(biāo)稱電壓為12V,在充電和放電過(guò)程中在9V~16V之間變化。(2)根據(jù)用戶情況,標(biāo)稱高側(cè)電壓可以從144V變化到288V或更高。(3)標(biāo)稱充電和放電功率為1.5kW。(4)開關(guān)頻率可以從50kHz變到70kHz。(5)由于安全原因,高壓端和低壓端之間應(yīng)有電隔離。在這種情況下,使用高頻變壓器。(6)工作溫度在-40°C~85°C之間。(7)保證期為10年或者150,000km。(8)輸出電流在80A~150A左右。
圖3所示為DC/DC轉(zhuǎn)換器示意圖。它由一個(gè)全橋Q1-Q4通過(guò)一個(gè)高頻變壓器與一個(gè)帶有升壓電感的推挽級(jí)連接而成。在升壓模式下,使用兩個(gè)PWM信號(hào)來(lái)控制器件Q5和Q6。
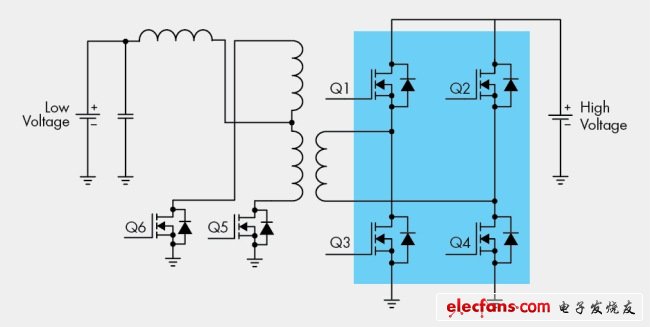
圖3 全橋同步DC/DC轉(zhuǎn)換器。
如圖4所示,有幾種實(shí)現(xiàn)DC/DC轉(zhuǎn)換的方法。全橋方法常常用來(lái)減小車輛的重量并提高效率。
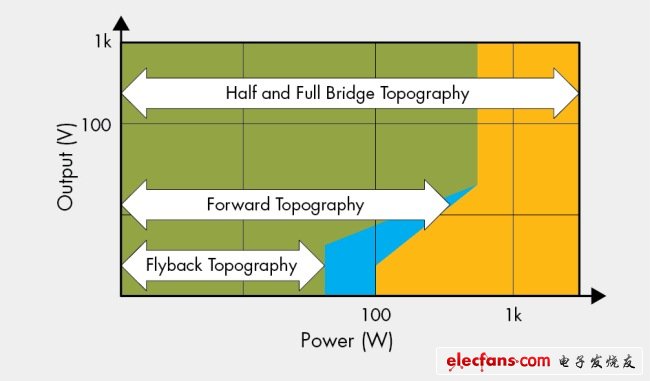
圖4 DC/DC轉(zhuǎn)換器對(duì)比輸出功率。
在這種運(yùn)作過(guò)程中,DC/DC轉(zhuǎn)換器作為一種降壓轉(zhuǎn)換器,將電壓從200V或者更高,降低至12V。原則上不能驅(qū)動(dòng)低壓端的開關(guān)。它們的二極管僅作為電壓整流級(jí)。為了提高整流器的效率,必須用MOSFET替代二極管。
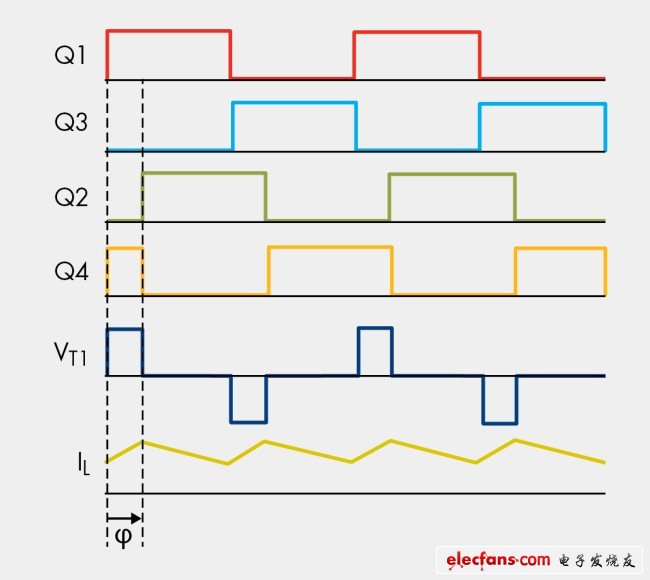
圖5 移相時(shí)序圖。
而在高壓端,移相調(diào)制能夠?qū)崿F(xiàn)MOSFET的零電壓開關(guān)(ZVS),幾乎消除了開關(guān)損耗。在移相調(diào)制中,具有相同引腳的兩個(gè)器件由兩個(gè)具有50%占空比和正確死區(qū)時(shí)間設(shè)置的互補(bǔ)信號(hào)驅(qū)動(dòng)。在兩個(gè)引腳之間,通過(guò)反饋環(huán)路將信號(hào)移相一個(gè)角度。該方法能夠?qū)崿F(xiàn)均衡使用變壓器,防止鐵芯飽和。移相造成的交疊為降壓轉(zhuǎn)換器設(shè)定了占空比,以便調(diào)整輸出電壓。圖5為所描述的控制信號(hào)。
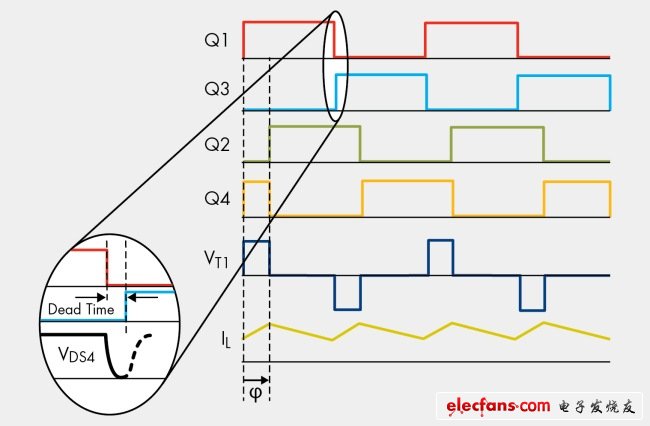
圖6 移相調(diào)制中的零電壓開關(guān)動(dòng)作。
圖6所示為如何通過(guò)正確設(shè)定驅(qū)動(dòng)全橋逆變器的兩個(gè)互補(bǔ)對(duì)的死區(qū)時(shí)間,讓MOSFET的導(dǎo)通發(fā)生在零電壓點(diǎn)。這是因?yàn)楫?dāng)先前處于導(dǎo)通狀態(tài)的MOSFET(例如圖11中的Q3)關(guān)斷時(shí),由于死區(qū)時(shí)間的緣故,Q5仍然處于關(guān)斷,半橋的中點(diǎn)處于懸浮,并且開始出現(xiàn)一種自然振蕩,這是由于在半橋的中點(diǎn),變壓器的泄漏電感和寄生電容構(gòu)成了諧振電路。
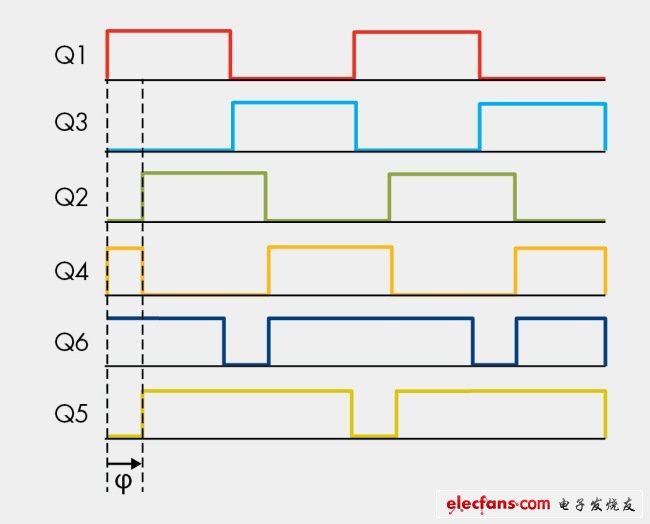
圖7 同步整流和移相調(diào)制。
這引發(fā)VDS4以固定頻率振蕩,通過(guò)正確設(shè)定死區(qū)時(shí)間,Q4可以在零電壓處導(dǎo)通。最后,為了進(jìn)一步提高轉(zhuǎn)換器效率,采用圖7所示的方式來(lái)控制Q5和Q6,在其續(xù)流二極管假定導(dǎo)通時(shí)減小電壓降。
2.汽車前燈應(yīng)用
車前燈是汽車的最重要部件之一。車燈應(yīng)用中電池的標(biāo)稱電壓是13.2V。但是,電池的電平隨著駕駛條件而變化。高輸入電壓(13.2V ~ 16V)可能影響車前燈的耐用性。如圖8所示,電池電壓升高6%,車燈的使用壽命減少50%。
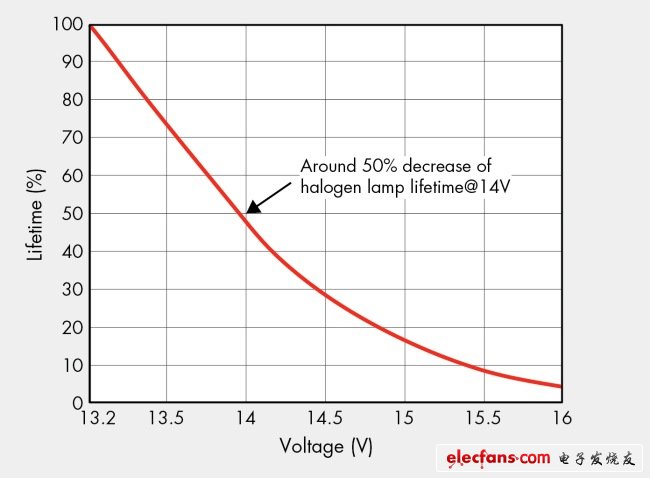
圖8 各種電壓下的車燈壽命曲線。

此處,車燈壽命為小時(shí)數(shù)。此外,在打開車前燈時(shí),大的涌入電流會(huì)縮短車燈的使用壽命,因?yàn)闊襞轃艚z的熱阻低。
例如:55/60W燈泡在13.2V下的使用壽命是1,000小時(shí)。使用等式1:
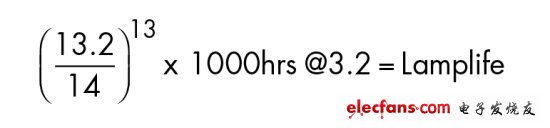
14V下燈泡的壽命時(shí)間約為465小時(shí),因而,將PWM控制用于帶有智能MOSFET的燈泡,可以延長(zhǎng)燈泡的使用壽命。為了延長(zhǎng)車前燈的使用壽命,在電池電壓高于標(biāo)稱電壓13.2V時(shí),使用限制電流的方式來(lái)實(shí)現(xiàn)功率調(diào)節(jié)。使用PWM來(lái)控制輸入電壓。等式3使用占空比定義了RMS電壓:
此處,D——占空比,VBAT——電池電壓。
當(dāng)電池電壓高于標(biāo)稱電壓時(shí),如圖9所示,確定PWM占空比。
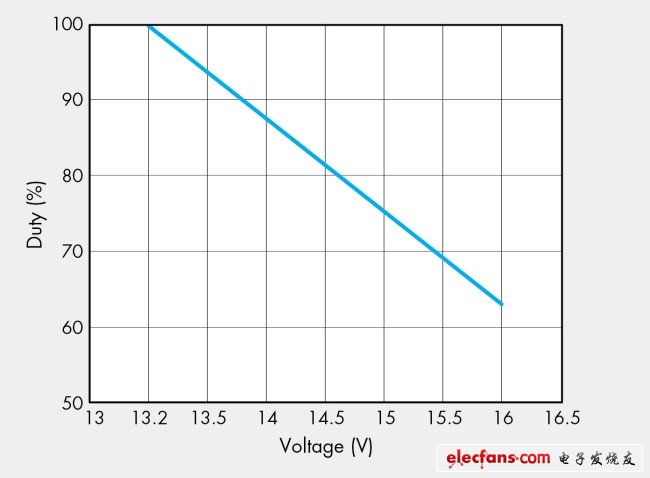
圖9 不同電壓下的穩(wěn)定功率消耗。
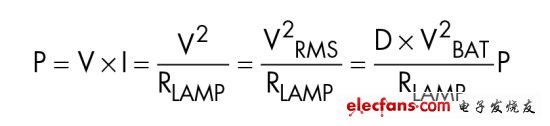
此處:VNOM——標(biāo)稱電壓;VRMS ——RMS電壓;VBAT ——電池電壓;RLAMP ——燈泡電阻。
這種計(jì)算占空比的方法是采用PWM平方或者電壓的二次式(square PWM or quadratic voltage regulation)使用軟啟動(dòng)方式限制涌入電流。在一種測(cè)試應(yīng)用中,使用PWM在100Hz頻率下實(shí)現(xiàn)功率調(diào)制。圖9顯示電壓處于標(biāo)稱電壓附近時(shí)功率沒(méi)有上升,從而保護(hù)了燈泡。
圖10 不受限與受限制的啟動(dòng)電流比較。
燈使用智能功率器件和PWM技術(shù),實(shí)現(xiàn)以下功能:(1)在安裝位置減小熔斷器和熔斷器座的尺寸;(2)防止負(fù)載線出現(xiàn)過(guò)載或短路;(3)減少電纜和連接器;(4)改善燈的故障診斷,檢查它們的功率額定值是否正確;(5)通過(guò)功率調(diào)整并使用PWM對(duì)燈進(jìn)行預(yù)熱,延長(zhǎng)使用壽命;(6)通過(guò)激活其它具有所需亮度的可用燈,實(shí)現(xiàn)故障管理;(7)通過(guò)優(yōu)化開關(guān)邊緣和錯(cuò)時(shí)開關(guān)方式減小電磁輻射。
在車前燈開啟的初時(shí),由于燈泡燈絲的熱阻低,會(huì)出現(xiàn)大的涌入電流。為了減小涌入電流,可以使用智能功率器件來(lái)實(shí)現(xiàn)軟啟動(dòng)。圖10(a)所示為直流電源下燈泡的典型沖擊電流。峰值電流達(dá)到穩(wěn)態(tài)電流的10~14倍,持續(xù)時(shí)間為數(shù)毫秒。在250ms~500ms后,啟動(dòng)過(guò)程結(jié)束。理論上,由于10倍左右的涌入電流縮短了燈泡的壽命。因此,軟啟動(dòng)過(guò)程應(yīng)達(dá)到500ms,以延長(zhǎng)燈的壽命,如圖10(b)所示。
3.汽車功率模塊
針對(duì)大電流馬達(dá)應(yīng)用的典型APM使用了六個(gè)低RDSON MOSFET,采用三個(gè)半橋方式布局,共用一個(gè)VBAT供電。可選擇的EMC元件對(duì)導(dǎo)通輻射進(jìn)行抑制。典型的調(diào)制頻率為10kHz~15kHz。APM工作于-40°C ~125°C。內(nèi)部的熱敏電阻可以在極端溫度下對(duì)輸出功率進(jìn)行溫和的關(guān)斷(foldback)。電流分流器的公共返回位置可以實(shí)現(xiàn)電流的同步解調(diào),將其與相位操作進(jìn)行關(guān)聯(lián)。這種拓?fù)溥m用于電動(dòng)助力轉(zhuǎn)向等靜態(tài)轉(zhuǎn)矩控制,或者是電動(dòng)液壓助力轉(zhuǎn)向的旋轉(zhuǎn)泵等連續(xù)的速度和轉(zhuǎn)矩控制。
4.智能IGBT點(diǎn)火器
流行的汽車點(diǎn)火結(jié)構(gòu)是每個(gè)汽缸使用一個(gè)線圈(鉛筆線圈),直接安裝在火花塞的上方,以省去點(diǎn)火引線。IGBT和控制裝置常常位于單獨(dú)的電子模塊中,通常為引擎或者動(dòng)力傳動(dòng)控制器。現(xiàn)今,某些線圈包含IGBT,從電子模塊中消除了高壓。然而,為了控制線圈電流,必須為控制器提供一個(gè)電流反饋信號(hào)。這樣就需要額外的引線。
為線圈的IGBT組件添加控制IC,可以在不增加引線的情況下提供其它功能。使用復(fù)雜的引線框可以將無(wú)源元件與控制芯片和IGBT封裝在一起。
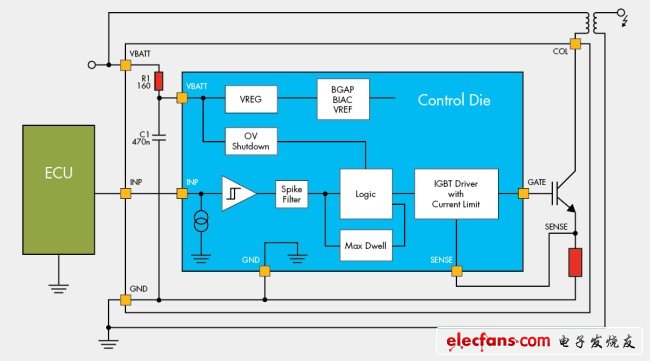
圖11 智能點(diǎn)火(一個(gè)線圈)。
注意,在圖11所示的智能鉛筆線圈連接器上,VBAT、輸入以及地線是僅有的連接。這款控制IC包含自主功能:(1)限流,實(shí)現(xiàn)最長(zhǎng)駐留時(shí)間;(2)過(guò)壓保護(hù);(3)超溫保護(hù);(4)輸入信號(hào)完整性:(5)抗瞬變能力;(6)消除火花的軟關(guān)斷。
針對(duì)高壓開路電路,IGBT典型額定值在300mJ~500mJ。使用高性能線圈,提供的火花能量目標(biāo)值可以達(dá)到70mJ以上,標(biāo)稱線圈電流為10A。為達(dá)到此目標(biāo),控制和保護(hù)功能必須處理從冷啟動(dòng)到高RPM工作的全范圍運(yùn)作狀況。還可以實(shí)現(xiàn)其它診斷功能:(1)初級(jí)端短路/開路;(2)次級(jí)端短路/火花能量低;(3)高壓開路.
四、本文總結(jié)
功率半導(dǎo)體是現(xiàn)今集成電子系統(tǒng)以期提高功能性、改善車輛性能以及提高可靠性的主要推動(dòng)力量。智能功率器件已經(jīng)成為配電系統(tǒng)中的核心構(gòu)建模塊。車輛中的獨(dú)立功率電路數(shù)量已經(jīng)從過(guò)去數(shù)十年間的數(shù)十個(gè)增加到現(xiàn)今復(fù)雜車輛中的50個(gè)以上。照明和便利性功能還將繼續(xù)發(fā)展,以滿足用戶的要求。許多使用基于極限控制的關(guān)鍵任務(wù)系統(tǒng)現(xiàn)在使用變量控制。智能功率特性的提升是必不可少的。更精確的負(fù)載反饋、診斷、故障安全功能、提高效率的精密控制、電磁兼容性以及用戶界面簡(jiǎn)化等均有著強(qiáng)大的市場(chǎng)需求。為了達(dá)到未來(lái)的性能目標(biāo),需要改進(jìn)控制芯片和獨(dú)特的IGBT/MOSFET功率器件,同時(shí)提升散熱優(yōu)化和環(huán)境穩(wěn)定性封裝技術(shù)。
隨著電子產(chǎn)品在汽車中的應(yīng)用持續(xù)增加,高壓和低壓應(yīng)用都面臨或多或少的挑戰(zhàn)。高壓產(chǎn)品面臨的挑戰(zhàn)包括:(1)隔離和增加熱壽命方面的封裝改進(jìn);(2)提高IGBT性能,降低損耗;(3)處理負(fù)載的更高相位電流的能力(大于30A),例如:壓縮機(jī)驅(qū)動(dòng);(4)增加自保護(hù)功能(散熱、峰值相位電流等);(5)改善電磁兼容性能。
低壓產(chǎn)品的挑戰(zhàn)有:(1)改善MOSFET技術(shù),降低硅器件成本;(2)集成耐用的柵極驅(qū)動(dòng)和智能電磁兼容控制;(3)集成電池反向保護(hù)功能;(4)降低散熱方面的材料成本。
但是不管怎么說(shuō),有挑戰(zhàn)就會(huì)有壓力,有壓力才會(huì)有動(dòng)力、有競(jìng)爭(zhēng),也只有在這種環(huán)境下,功率半導(dǎo)體在汽車電子中的應(yīng)用才會(huì)更上一層樓!
評(píng)論