將電芯通過焊接的方式串并聯起來成組,是電池模組生產的關鍵步驟,焊接技術在某種程度上已經成為制約模組產品品質、生產效率、成本的最關鍵因素之一。下面以幾家優秀的模組生產企業的專利技術為例,討論一下領域內對該技術的著眼點。
A企業
由于總輸出極承擔較大的載流量,所以一般會采用銅材質,而銅電極片直接與鋁極柱焊接強度低,穩定性不好。
A家最早的解決方案是先把銅電極片與一塊鋁片預制超聲焊接在一起,再對鋁片與極柱進行焊接。此方法存在三個問題:
1、對鋁連接片和鋁極柱焊接時,會影響已焊接好的銅鋁結合部穩定性;
2、銅鋁電極片焊接區域非對稱,影響焊接強度;
3、銅電極片連接插接件后會給銅鋁界面帶來剪切力,影響結合強度。
針對這三個問題,A家共進行了三項改進。
第一項改進是在銅電極片上開通孔,沿通孔一圈的圓環區域對銅鋁電極片進行超聲焊接,再在通孔區域對鋁片和鋁極柱進行激光焊接。該方法解決了多次焊接和焊接區域不對稱的問題,但是依然存在銅電極片上插接件造成的剪切力。
第二項改進是在上述分區焊接的基礎上,把銅電極片變成銅臺,銅臺上有帶有外螺紋的同心銅柱,或者帶有內螺紋的圓柱孔,與插接件進行螺紋連接。一方面降低剪切力帶來的影響;二來降低插接件的生產難度,實現自主生產。
第三項改進也是給予第一項分區焊接技術,開發了一種可伸縮鋁電極片,為多層鋁箔堆疊后經沖壓成型再分段熱壓焊接而成。拱形段為各層間未結合的多層分散的狀態,平面段為各層間經熱壓焊接結合在一起的單層的狀態,從而形成一種柔性鋁電極連接片,補償因電池膨脹形成的位移,降低在銅鋁結合部產生的應力。推測前兩項改進方式對界面結合力的提升并不能完全滿足要求,所以才采用這種柔性鋁連接片的方式,彌補銅鋁界面強度不足的問題。
B企業
B家是采用鎳片與極柱進行連接,可焊接性好,但是導電能力不足,且成本高。
針對此問題,研發了一種銅鎳復合電極片,分別開有對應的通孔,通孔處有鎳凸片用于與極柱進行焊接,從而兼具鎳的焊接性能與銅的導電性能。這種方式并未徹底解決導電能力不足的問題,如通過增加連接片厚度的方法來優化,則又影響焊接性能,增大了電池模組重量,提高了成本。
于是開發了一種由厚薄兩片鋁極片組成的復合連接片。在厚極片上設有通孔,薄極片上開有與通孔對應的圓槽,圓槽為薄極片與極柱的焊接區域。此時,厚極片可以增加到足夠大的厚度來保證導電性,薄極片降低到足夠薄來保證焊接性。而鋁材密度小價格低,也能保證整體質量和成本的要求。
C企業
C家為了實現很好的連接強度,在連接片上開通孔,電芯極柱穿過通孔與之配合,然后利用激光將通孔周圍金屬熔融進行焊接。問題是,如果所開通孔過大,焊接效果會受到影響。如果過小,又增加了裝配難度。
針對此問題,C家把通孔分成了大小孔兩段,采用過盈配合的模式降低對孔形狀和尺寸的要求。
為了提高連接片的導電性能,C家開發了一種多層疊加的連接片。兩層材料焊接在一起,其中一層或幾層開通孔,剩下一層與通孔對應的區域為連接片與極柱的焊接部,兼顧薄處焊接,厚處導電的功能。值得注意的是,兩項技術的基材均為多層箔材焊接而成,兩種連接片均為一次性沖壓成型。
總結一下各家企業的共同點:
1、連接片多采用多層材料復合+開設通孔的方法,其中一層材料為連接片與極柱的連接層,保證焊接性能。多層材料疊加用于保證連接片的導電性。
2、連接片基材采用多層箔材堆疊之后加工成型,可形成柔性區域,用于補償電芯膨脹造成的位移,減小對低強度界面的影響。
以上三家均為電池模組生產企業,解決問題的思路也基本類似,即想辦法繞開問題。當兩種材料焊接質量無法滿足要求時,嘗試采用不同的替代材料,再利用更加精細的結構或工藝彌補更換材料帶來的性能損失。因為焊接技術本身的優化空間,對于模組生產商來說是很小的。
-
焊接
+關注
關注
38文章
3401瀏覽量
61080 -
電池
+關注
關注
84文章
11017瀏覽量
134265
原文標題:【誠捷智能· 高工經緯】三家企業電池模組焊接方法對比分析
文章出處:【微信號:gh_a6b91417f850,微信公眾號:高工鋰電技術與應用】歡迎添加關注!文章轉載請注明出處。
發布評論請先 登錄
動力電池能量密度技術企業哪家強_七家企業對比分析
機器人焊接與人工焊接對比分析
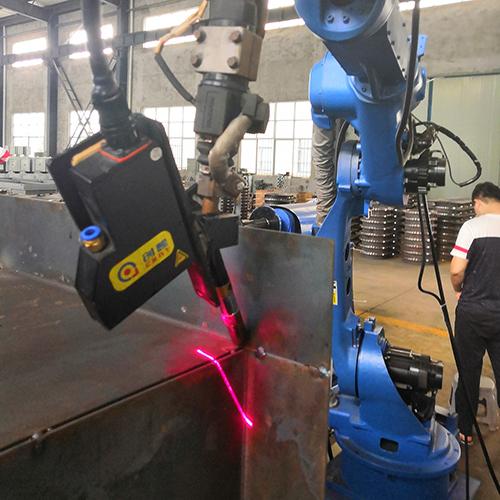
評論