在半導體制造領域,后道工藝(封裝與測試環節)對溫度控制的精度和穩定性要求高。冠亞恒溫半導體冷水機憑借其高精度溫控、多通道同步控制及定制化設計能力,成為保障后道工藝可靠性的核心設備。本文從技術原理、應用場景及核心優勢三方面展開分析。
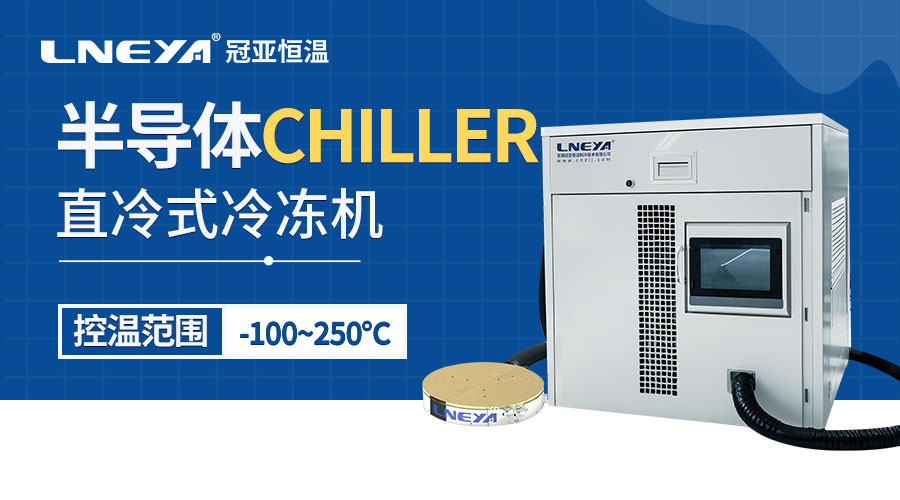
一、技術原理:高精度溫控與多通道同步控制
(一)快速升降溫與±0.5℃精度控制
冠亞恒溫半導體冷水機采用多通道獨立控溫技術,縮短升降溫時間。針對后道工藝中不同溫度需求區域(如塑封固化、鍵合焊接、測試環境艙),設備設置獨立溫控通道,每個通道配備單級或多級復疊壓縮機、微通道換熱器及電子膨脹閥,實現局部強化冷卻。
設備集成前饋控制與模糊邏輯優化算法,基于歷史數據建立溫度預測模型,在工藝負載變化前(如等離子體清洗、老化測試)預調整制冷功率。例如,在加速壽命試驗中,設備為多工位測試臺提供獨立溫控通道,支持-40℃至+125℃寬域循環,響應速度提升。
二、應用場景:覆蓋封裝測試全流程
(一)芯片封裝環節
塑封工藝熱管理
在環氧樹脂模塑過程中,設備通過全密閉循環系統維持模具溫度穩定(±1℃),避免因溫度波動導致樹脂收縮率異常。
鍵合焊接溫控
針對金線鍵合工藝,設備通過液氮冷熱沖擊技術實現鍵合頭溫度快速切換(如-10℃至+150℃),確保引線鍵合強度達標。
(二)測試環節
老化測試環境控制
在多工位加速壽命試驗中,設備為每個測試艙提供獨立溫控通道,支持動態負載調節。
終檢環節精度保障
在激光打標與電鍍工藝中,設備通過高精度控溫(±0.2℃)確保管腳成型質量。
三、核心優勢:定制化設計與可靠性保障
(一)硬件架構創新
全密閉循環系統
設備采用三通道獨立制冷循環架構,通道間通過管路隔離設計避免介質混合,確保溫度控制準確性。例如,在同時為晶圓測試平臺、封裝設備及環境艙供冷時,各通道溫差控制在±0.3℃以內。
高可靠性組件
壓縮機、膨脹閥等核心部件采用艾默生、丹佛斯等國際品牌,配合304不銹鋼管道與高壓靜電噴塑外殼,適應-40℃至+120℃寬溫工況。
(二)智能控制與安全機制
液晶控制器面板
支持本地+遠程雙模式控制,實時顯示溫度、壓力曲線,并可存儲歷史數據用于工藝分析。
自動故障保障系統
設備內置壓力傳感器與電磁三通閥,當檢測到管路壓力異常時,自動切換至內循環模式并輸出報警信號。
(三)定制化服務能力
冠亞恒溫提供從單通道(FLTZ變頻系列,-100℃至+90℃)到多通道(無壓縮機ETCU換熱單元,+5℃至+90℃)的全系列產品線,并可根據工藝需求添加輔助設備(如液氮補充裝置、防爆模塊)。例如,某企業定制的三通道直冷機在涂膠顯影工藝中實現溫度波動≤±0.8℃,良率提升。
四、典型案例:某企業半導體封裝產線升級
(一)問題診斷
某企業封裝產線在塑封與鍵合環節頻繁出現以下問題:
塑封模具溫度波動達±3℃,導致樹脂收縮率超標;
鍵合頭溫度不穩定,引發金線斷裂率上升;
老化測試艙溫差達±5℃,影響產品壽命評估準確性。
(二)解決方案
部署冠亞FLTZ變頻雙通道冷水機,分別為塑封機與鍵合機提供獨立溫控;
定制液氮冷熱沖擊模塊,實現鍵合頭溫度快速切換(響應時間≤5秒);
升級三通道直冷機,為老化測試艙提供±0.5℃精度控制。
(三)實施效果
塑封元件外觀缺陷率降低,降低返工成本;
鍵合斷裂率降低,單線產能提升;
老化測試數據重復性提高,客戶投訴減少。
冠亞恒溫半導體冷水機通過高精度溫控、多通道同步控制及定制化設計,有效解決了半導體后道工藝中的熱管理難題。其全密閉循環系統、智能安全機制及快速響應能力,為封裝測試環節提供了可靠的溫度保障。
-
半導體
+關注
關注
335文章
28854瀏覽量
236747 -
封裝測試
+關注
關注
9文章
156瀏覽量
24276 -
冷水機
+關注
關注
0文章
90瀏覽量
7985
發布評論請先 登錄
提供半導體二手及翻新設備(前道和后道)
半導體工藝講座
半導體的導電特性
半導體的導電特性
SPC在半導體在半導體晶圓廠的實際應用
《炬豐科技-半導體工藝》DI-O3水在晶圓表面制備中的應用
半導體制冷機chiller在半導體工藝制程中的高精度溫控應用解析
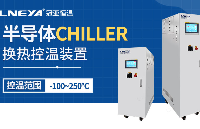
評論