文章來源:學習那些事
原文作者:趙先生
本文概述了集成電路制造中的劃片工藝,介紹了劃片工藝的種類、步驟和面臨的挑戰。
劃片工藝介紹
半導體制造的起點是對硅的加工。首先,要把純度高達 99.9999% 的硅晶柱切割成不同厚度的晶圓。一般而言,4 英寸晶圓的厚度約為 520 微米,6 英寸的是 670 微米,8 英寸的為 725 微米,12 英寸的則是 775 微米 。在晶圓上通過窗口刻蝕技術,一個個電路芯片被制作出來,它們整齊排列,在晶圓上形成小方格陣列,每一個小方格都代表著一個具有特定功能的電路芯片。
在半導體制造過程中,由于晶圓呈圓形,其邊緣一定區域內的芯片圖形工藝存在不完整的情況,主要有三種情形,如圖 1 所示。考慮到邊緣區域圖形不完整,在制作掩模版時會將這部分去除,從而保證每個圖形都是工藝完整、功能完備的晶粒,便于進行良率統計、晶粒分揀以及盲封操作。硅晶柱的尺寸越大,切割得到的晶圓面積就越大,能夠產出的功能完整的有效芯片晶粒數量也就越多。所以,芯片制造工藝越先進,晶圓尺寸越大,每只電路芯片的成本就越低,進而降低半導體的生產成本。
圖1 晶圓邊緣
半導體器件的發展方向是單個芯片尺寸越來越小,同時單個芯片集成的晶體管數量越來越多。硅晶圓的發展趨勢則是尺寸不斷增大,硅晶柱隨著工藝進步,從最初能生長為 1 英寸、2 英寸,到后來的 4 英寸、6 英寸(約 150 毫米)、8 英寸(約 200 毫米),近年來更是發展出 12 英寸,甚至還在研發更大規格,如 14 英寸、16 英寸,乃至 20 英寸以上。在一片晶圓上,重復刻蝕著幾只到幾十萬只電路芯片。在晶圓上,電路芯片單元之間通過特定區域相互隔離開,這些獨立的電路芯片被稱作芯片晶粒,而隔離區域則被稱為劃片槽,如圖 2、圖 3 所示。
圖2:晶圓切割晶粒示意圖
圖3:晶圓、芯片晶粒與劃片槽
在使用芯片晶粒之前,需要通過有效的方法將其分割并單獨取下,這就需要劃片這一工序。劃片工序將晶圓分割成一個個單獨的芯片晶粒,隨后對芯片晶粒進行鏡檢、焊接、鍵合、封蓋等一系列工序,最終封裝出能實現各種功能且不易受環境損傷的成品集成電路。
晶圓生產線制造完成的一整片晶圓,在經過探針臺電測試后,通過切割工藝分割成具有電氣性能、可用于制作集成電路的獨立芯片,這個過程被稱為晶圓切割或劃片。圖 4
展示了集成電路制造封裝流程及劃片工序的位置。晶圓劃片是電子封裝工藝流程的第一道工序,主要通過研磨、灼燒等方式來完成分割。在劃片過程中,還伴隨著對晶圓的固定、清洗等工藝步驟,以此保證芯片不被劃片過程中產生的污物污染,維持晶粒的潔凈度。同時,也要確保在劃片過程中芯片電路功能的完整性與可靠性。
圖4:集成電路制造封裝流程及劃片工序位置
劃片方式
在早期,晶圓切割采用的是物理切割方法,通過劃片刀進行橫向和縱向的切割運動,把晶圓分割成方形的芯片晶粒。直至今日,利用金剛石砂輪劃片刀(見圖 5)進行晶圓切割的方式依舊是主流。不過,機械劃片時,劃片力直接作用于晶圓表面,這會讓晶體內部產生應力損傷,容易引發芯片崩邊以及晶圓破損的問題。尤其是對厚度在 100 微米以下的晶圓進行劃片操作時,晶圓破碎的風險極高。機械劃片的速度通常為 8 - 10 毫米 / 秒,速度相對較慢,而且要求劃片槽寬度大于 30 微米,對于高可靠電路,劃片槽寬度需更大,甚至要達到 50 - 60 微米,以此保證芯片劃片后的完整性與可靠性。一般芯片的預留劃片槽寬度與切割用金剛石砂輪劃片刀厚度的推薦值,如表 1 所示。機械劃片原理示意圖如圖 6 所示。
圖6:機械劃片原理
表 1:一般芯片的預留劃片槽寬度與切制用金剛石砂輪劃片刀厚度的推薦值
激光切割屬于無接觸式劃片,不會給晶圓帶來機械應力,對晶圓造成的損傷較小,能夠有效避免芯片破碎、損壞等情況(見圖 7)。由于激光聚焦可以達到亞微米數量級,在對晶圓進行微處理時優勢顯著。同時,激光劃片速度能夠達到 150 毫米 / 秒,相比機械劃片速率有大幅提升,還能完成較薄晶圓的加工任務,也可用于切割一些形狀較為復雜的芯片,比如六邊形芯片。然而,設備成本高昂成為了阻礙激光劃片廣泛應用的因素之一。
圖7:機械劃片與激光劃片
劃片工藝步驟
在劃片工藝正式開始前,需要先做好必要的準備工作。隨后,把待切割的晶圓片粘貼到藍膜上,將藍膜框架放置到劃片機中,開啟劃片過程,并且在劃片過程中實時清除產生的硅渣和污物。最后,將分割好的芯片進行拾取和妥善保存,具體步驟如圖 8 所示。
圖8:劃片工藝步驟
1.準備工作
在進行劃片工藝前,需對相關設備與環境進行細致準備。首先,使用乙醇浸濕無塵布,對貼膜機進行全面擦拭,以去除表面的灰塵與雜質。隨后,利用氮氣槍對工作臺面及周邊區域進行吹掃,確保無殘留的微小顆粒。在必要情況下,開啟去離子風吹淋工作區域,有效消除靜電干擾,避免靜電對晶圓及后續工藝造成影響。完成設備與環境清理后,需對待劃片的晶圓(見圖 9)進行嚴格檢查。仔細核對晶圓的數量以及批次信息,同時全面查看晶圓表面,確保其完好無損,無任何破損跡象,為后續工藝的順利開展奠定基礎。
2.貼裝藍膜
貼裝藍膜后的晶圓如圖 10 所示。
1)藍膜:藍膜在劃片工藝中承擔著固定晶圓和束縛晶粒的關鍵作用。它將晶圓背面穩固地固定在金屬膜框上,確保在晶圓被切割成單個晶粒后,晶粒不會散落。晶圓通常依據直徑大小區分,常見的尺寸有 6 英寸、8 英寸、12 英寸,部分用于高可靠電路的穩定老品種還會使用 4 英寸晶圓。與之對應,藍膜也具備不同尺寸規格。藍膜的主要特征參數為厚度與黏附力,大多數用于硅晶圓劃片的藍膜厚度在 80 - 95 微米之間。藍膜的黏附力既要足夠大,以保證劃片過程中能將分離的每個晶粒緊緊固定在膜上,又要在劃片完成后,便于從膜上輕松取下晶粒。目前,最常用的藍膜類型為普通藍膜和紫外(UV)膜。普通藍膜成本約為 UV 膜的三分之一。UV 膜的粘接強度可通過紫外線照射改變,照射后,其粘接劑聚合固化,黏附力減小 90%,使得脫膜、揭膜更為容易,且不會留下殘留物。UV 膜具有極強的初始黏附力,能有效固定晶圓,即使是微小晶粒也不會出現位移或剝除問題;通過紫外線照射降低黏附力后,即便大晶粒也能輕松分揀,且應力極小,晶粒背面無殘留。
2)貼膜框:貼膜框又稱晶圓環、膜框、金屬框架等,采用金屬材質制成,具有一定剛性,不易變形,常與貼膜機配套使用。其主要作用是繃緊藍膜,穩固固定晶圓,方便后續的晶圓劃片以及晶粒分揀工序,避免晶圓切割后,因藍膜褶皺導致晶粒間相互碰撞擠壓而造成損傷。
3)裝配過程:圖 11 展示了晶圓、藍膜及貼膜框的裝配圖,圖 12 呈現了具體的裝配過程。首先,取出一片晶圓,使其正面朝下、背面朝上,放置在貼膜機工作盤上,打開真空開關,利用真空吸力牢牢吸住晶圓。接著,將貼膜框放置在貼膜機工作臺上,仔細調整位置,使其中心與晶圓中心精準對齊,然后將側邊定位框移動至貼膜框外側,對其進行左右限位。最后,拉出足夠長度的藍膜,將其拉緊后貼在貼膜機后部,確保藍膜覆蓋整個貼膜框區域,再用滾筒滾壓藍膜,使晶圓、藍膜及框架緊密裝配在一起。
3. 晶圓切割
此步驟旨在按照芯片大小,將晶圓分割成單一的晶粒,以便用于后續的芯片貼裝、引線鍵合等工序。盡管機械劃片存在諸多可靠性和成本方面的問題,如晶圓機械損傷嚴重、劃片線寬較大、劃片速度較慢、需要冷卻水輔助切割、刀具更換維護成本較高等,但目前機械切割仍是主要的劃片方式。為解決機械劃片中芯片崩邊、分層、硅渣污染等問題,人們通過調整劃片工藝參數、精心選擇最佳的刀具類型以及采用多次劃片等手段加以應對。劃片機切割晶圓的場景如圖 13 所示。
4. 清洗
在晶圓切割過程中,清洗環節至關重要,主要目的是去除劃片時產生的各種硅碎、粉塵,清潔晶粒,同時對劃片刀起到降溫冷卻作用。冷卻介質的選擇需依據劃切材料的質量要求,可采用去離子水、自來水或其他冷卻介質。冷卻流量一般通過流量計進行調節控制,正常范圍在 0.2 - 4 升 / 分鐘。流量大小需根據刀刃以及劃切材料的種類和厚度進行調整,流量過大可能會沖走劃切中粘接不牢固的芯片,對于特別薄的刀刃,過大的流量還可能影響刀刃剛性;而流量過小則會影響刀刃壽命和劃切質量。
5. 芯片拾取
使用 UV 光照射后,UV 膜的黏性會減退,這使得拾取分割好的晶粒變得更加便捷,如圖 14 所示。
圖14:從UV膜上拾取所需芯片
表 2 展示了劃片工序涉及的主要設備、部件及耗材和作用。
表 2:劃片工序涉及的主要設備、部件及耗材和作用
機遇與挑戰
使用晶圓劃片機,旨在實現將整個晶圓近乎無損地劃切成單個集成電路芯片,以便后續開展裝片和引線鍵合等工藝。鑒于劃片對象是成本高昂的晶圓,所以晶圓劃片機務必具備高精度與高可靠性。當前,在晶圓劃片機領域面臨著諸多主要挑戰:
晶圓規格與切割道變化:晶圓直徑從以往的 150 毫米、200 毫米逐步增大到如今的 300 毫米,并且其集成度持續攀升,芯片尺寸愈發小巧。與此同時,切割道寬度不斷縮窄,從曾經的 75 微米、65 微米、50 微米,縮減至目前的 30 微米,這已逼近機械式砂輪劃片的能力極限。這種變化對劃片機的精度和穩定性提出了更高要求,傳統的劃片方式在應對如此精細的切割任務時,顯得愈發吃力。
超薄晶圓的應力敏感性:隨著先進 3D 疊層封裝技術的發展,對晶圓及芯片的厚度要求越來越薄,甚至低于 50 微米。超薄晶圓對于機械應力和熱應力極為敏感,這就迫切要求劃片過程中應力殘留越低越好。而現有的機械劃片方式在切割超薄晶圓時,難以有效控制應力的產生,容易導致晶圓破裂或芯片性能受損,給劃片工藝帶來了巨大挑戰。
新型材料的劃切難題:低 K 介質層銅互聯材料呈現出多孔網狀結構,這種結構使其容易碎裂。此外,金屬材料對金剛石砂輪刀具具有極強的黏粘性,這使得傳統的劃切方法難以滿足需求,必須探尋全新的劃切手段。尋找既能避免材料碎裂,又能解決刀具黏粘問題的劃切技術,成為了亟待攻克的難題。
高硬度材料的應用挑戰:化合物半導體材料(如 GaAs、InP)和第三代半導體材料(如 SiC、GaN 和金剛石)的應用日益廣泛。這些材料具有高硬度的特性,其劃切無論是對設備的性能,還是對刀具的耐磨性和鋒利度,都提出了全新的要求。現有的劃片機和刀具在處理這些高硬度材料時,往往無法達到理想的劃切效果,限制了這些新型材料在集成電路制造中的大規模應用。
成本與可靠性的雙重壓力:電子封裝行業對成本控制有著嚴格要求,同時高可靠集成電路對可靠性有著根本需求。這就意味著劃片成品率應盡可能達到 100%,一旦劃片出現質量問題,極有可能導致整個晶圓甚至整個批次晶圓報廢,造成巨大的經濟損失。如何在保證劃片質量的前提下,降低成本,提高生產效率,是晶圓劃片機面臨的又一重大挑戰。
盡管砂輪劃片這種機械劃片方式至今尚未發生根本性變革,但上述這些挑戰促使設備商不得不積極探索新的劃切方法。在迎接挑戰的同時,這些難題也為相關技術的創新與發展帶來了機遇。一旦新的劃切方法得以突破,不僅能夠滿足當前集成電路制造的需求,還可能推動整個行業向更高水平邁進,開啟新的發展篇章。例如,激光劃片技術雖然目前存在設備成本高昂的問題,但隨著技術的不斷進步和成本的降低,有望在未來成為解決這些挑戰的關鍵技術之一。此外,一些新興的劃切技術,如等離子劃切、超聲劃切等,也在不斷研發和試驗中,為晶圓劃片機的發展注入了新的活力。
-
集成電路
+關注
關注
5420文章
11969瀏覽量
367335 -
晶圓
+關注
關注
52文章
5129瀏覽量
129223 -
工藝
+關注
關注
4文章
675瀏覽量
29281
原文標題:劃片工藝概述
文章出處:【微信號:bdtdsj,微信公眾號:中科院半導體所】歡迎添加關注!文章轉載請注明出處。
發布評論請先 登錄
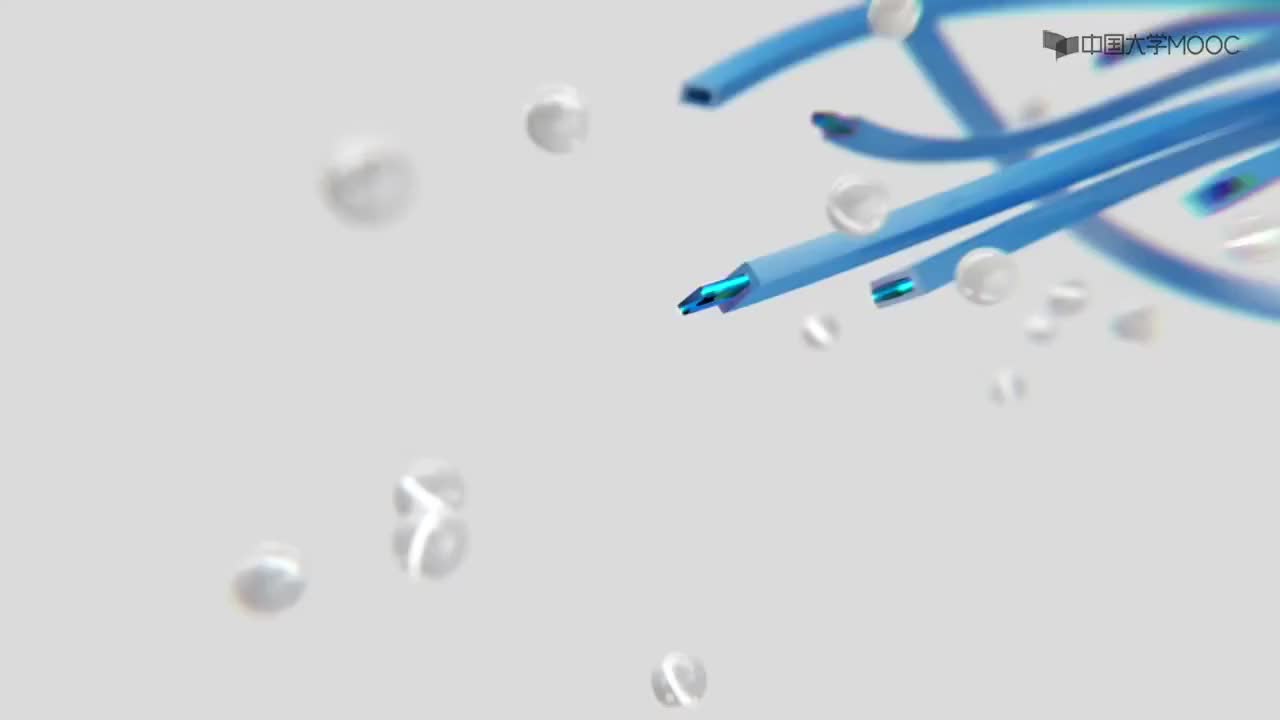
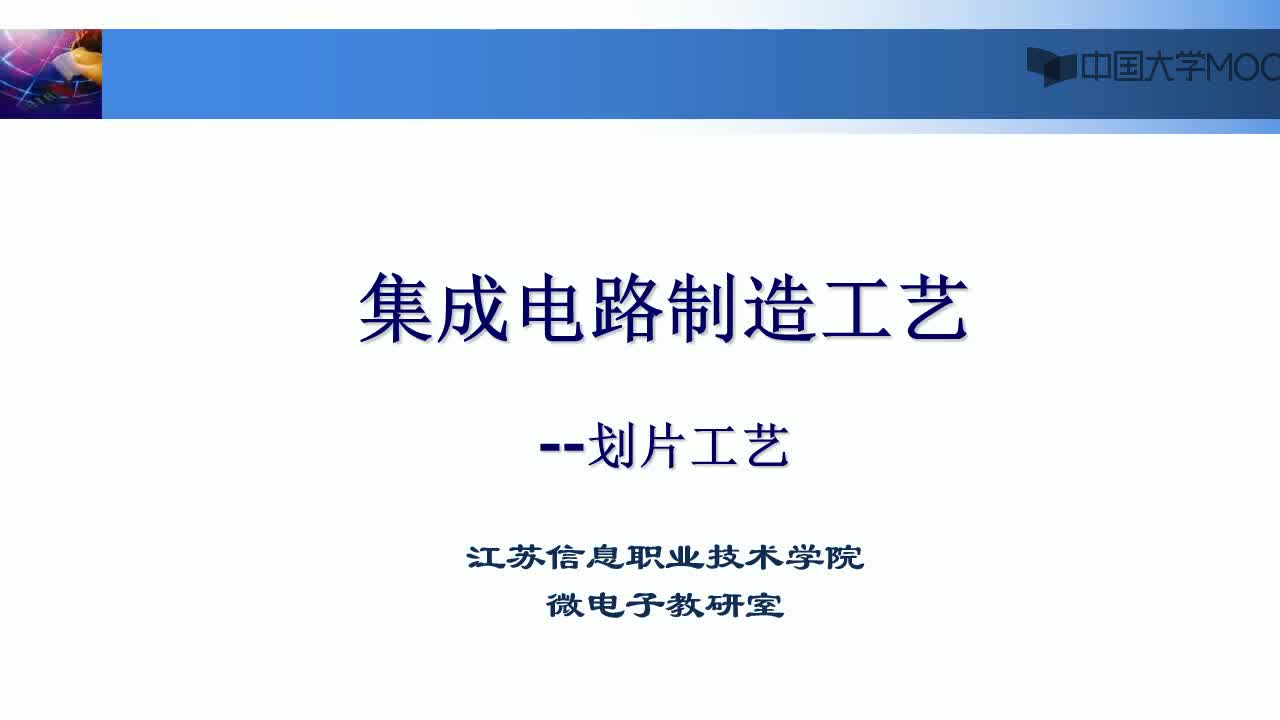
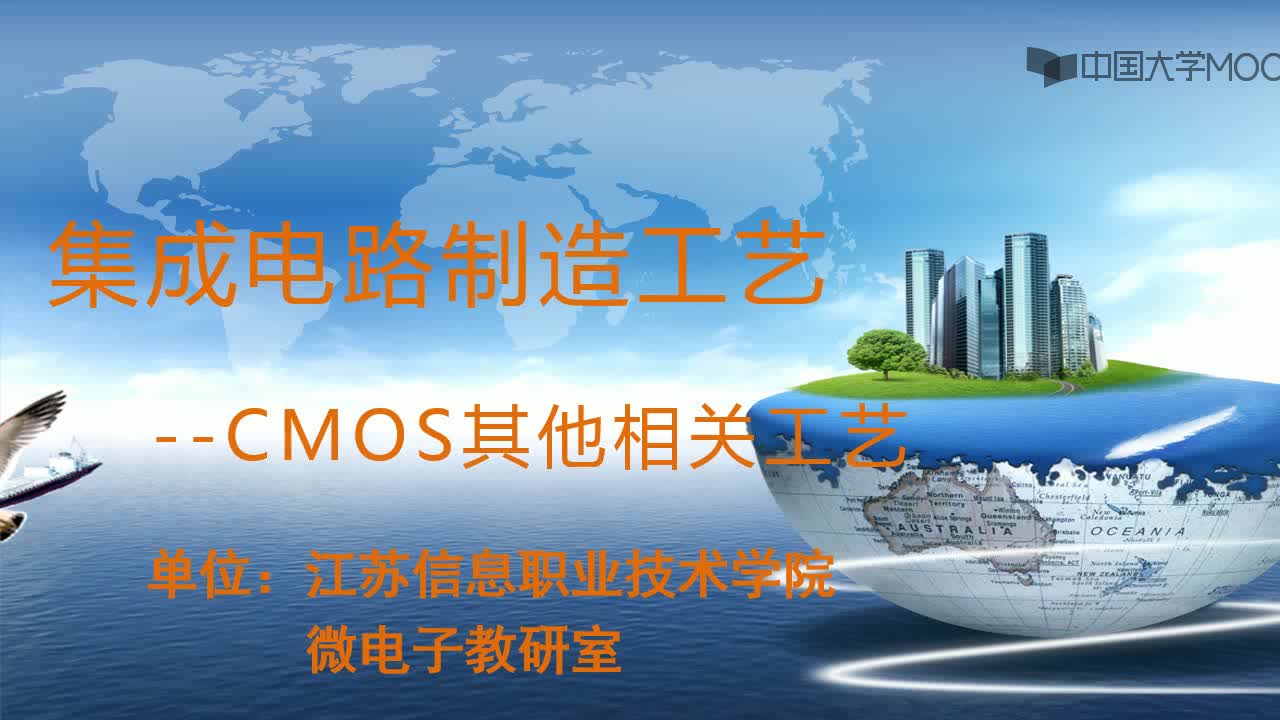
評論