There are basically two ways to go about making multi-material objects with photopolymer resin-based 3D printing processes. One is based on material science?and uses inkjet 3D printing technologies, such as Stratasys’ Polyjet and 3D Systems’ MJM, to release and instantly cure different materials in the same print job.? Another is mechanical, which is what 3D Systems’ presented around this time last year.
This latest approach is similar to the one implemented by Reinout Holtrop, a student from the University of Twente, for his Final Bachelor Assignment in Industrial Design, to design, develop and build the first DLP-based multi-material 3D printer, which he named XZEED. Ultimately, the basic concept behind the machine is relatively simple: using five alternating petri dishes in borosilicate glass with a PDMS layer, on a moving vat carrier.
This is the key component in the XZEED machine. It is made up of two shafts with bearings which support a movable array with the round vats. Light is projected with a beamer via a mirror on the bottom of the vat. The build platform is then moved vertically by the z-spindle, while the the x-spindle moves the array to change the vat.
Holtrop studied several 3D printers before developing his own design, including, of course, the industry leading Perfactory series by EnvisionTEC and CLIP technology by Carbon3D. He based his own project on a manual of how to design a normal DLP printer published by Tristram Budel in 2013, which is based on a Ramps 1.4 motherboard placed on top of an Arduino Mega 2560. This?simplified building and setting up the firmware.
The beamer that he used for this project is a Benq PB7230 DLP beamer. It works at the XGA resolution (1024×768) and was modified to be able to have a shorter throw. Perhaps the most amazing aspect is that almost all of the other components, which give the machine a highly professional and solid appearance, were manufactured with readily available in-house rapid prototyping tools. Using CNC mills, laser cutters and 3D printers, enabled Holtrop to work with PMMA plastics for the hood, as well as metal and MDF parts.
Apparently the project is still in its infancy, as Holtrop has stated several further areas of research, including experimenting with resin thickness, the light source (using LED’s instead of a projector), and improving the stability of the vats by building them using a more flexible material. For sure, this is a project that will draw quite a bit of attention from the industry and it will be very interesting to find out how and when it will grow into a commercial product.
自動翻譯僅供參考
特溫特大學(xué)的學(xué)生組建了多材料型3D打印機
基本上有兩種方式來制造基于光聚合物樹脂的3D打印過程的多材料對象。一是以材料科學(xué)為基礎(chǔ)的?使用噴墨3D打印技術(shù),如Stalasy' Pyj射流和3D系統(tǒng)的MJM,在同一打印作業(yè)中釋放和即時固化不同的材料。另一種是機械式的,這就是3D系統(tǒng)在去年這個時候提出的。
這個最新的方法類似于通過Reinout Holtrop,從特文特大學(xué),為他最后的學(xué)士學(xué)位分配在工業(yè)設(shè)計學(xué)生,實行設(shè)計,開發(fā)和建設(shè)的第一個基于DLP的多材料的3D打印機,這是他命名為一XZEED。最終,在機器后面的基本概念是相對簡單:使用五個交替在硼硅玻璃培養(yǎng)皿用PDMS層,一個活動大桶載體上。
這是在XZEED機的關(guān)鍵部件。它是由兩軸與支持一個可動陣列與輪大桶軸承。光被投射以經(jīng)由在缸的底部反射鏡一個投影儀。構(gòu)建平臺然后垂直移動由與z主軸,而在x-主軸移動陣列,以改變大桶。
Holtrop發(fā)展自己的設(shè)計,包括,當然,業(yè)界領(lǐng)先的Perfactory一系列EnvisionTEC和CLIP技術(shù),通過Carbon3D研究過不少3D打印機。他根據(jù)他自己的項目上如何設(shè)計由崔斯特瑞姆布德爾在2013年出版了一本普通的DLP打印機,它是基于一個斜坡1.4主板放置在一個Arduino兆2560這上面?簡化的建設(shè)和設(shè)立固件手工。
他用這個項目的投影儀是明基PB7230 DLP投影儀。它工作在XGA分辨率(1024×768),并進行了修改,能夠有一個更短的投射。也許最令人驚訝的方面是,幾乎所有的其他組件,從而使該機器高度專業(yè)和堅實的外觀,被制造使用現(xiàn)成的內(nèi)部快速原型開發(fā)工具。采用數(shù)控銑床,激光切割機和3D打印機,使Holtrop用PMMA塑料引擎蓋,以及金屬和中纖板的部分工作。
顯然,該項目仍處于起步階段,作為Holtrop曾表示研究一些其他領(lǐng)域,包括與樹脂厚度,光源實驗(采用LED的,而不是一臺投影儀),以及用更建立他們提高了大桶的穩(wěn)定性柔性材料。可以肯定,這是一個項目,該項目將吸引相當多的注意力從行業(yè),這將是非常有趣的,以了解如何以及何時會成長為一個商業(yè)產(chǎn)品。
-
3D打印
+關(guān)注
關(guān)注
27文章
3588瀏覽量
112066
發(fā)布評論請先 登錄
基于樹莓派的工業(yè)級 3D 打印機!
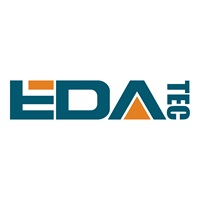
Molex莫仕與3D打印機制造商Prusa Research達成合作
高精度微型導(dǎo)軌在3D打印機中有多重要?
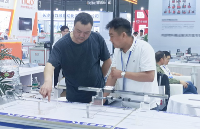
在樹莓派上安裝 Cura :輕松控制你的3D打印機!
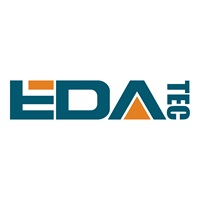
樹莓派“牽手”Formlabs:3D打印機界的“工業(yè)新寵”誕生記
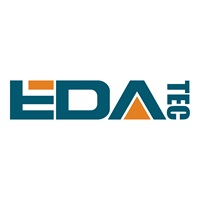
高效驅(qū)動:世平集團基于NXP RT1050的Klipper 3D打印機方案
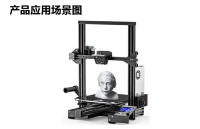
有源晶振在3D打印機應(yīng)用方案
工業(yè)一體機電腦在3D打印機設(shè)備中的應(yīng)用
3D打印機優(yōu)化:ARMxy嵌入式計算機的作用
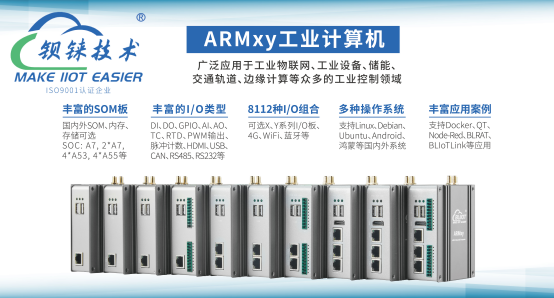
領(lǐng)麥微紅外測溫傳感器在小型光敏3D打印機中的創(chuàng)新應(yīng)用
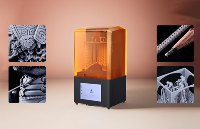
應(yīng)用在3D打印機的BD系列金屬連接器
Klipper固件的打印機可以插卡打印嗎?
2024年含直線電機3D打印機在內(nèi)共出口182.9萬臺
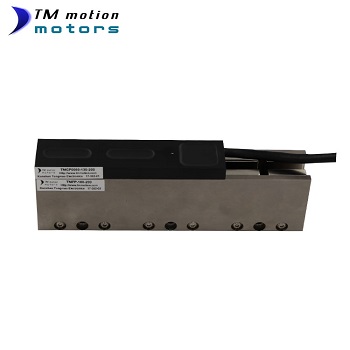
3D打印汽車零部件建模設(shè)計3D打印服務(wù)
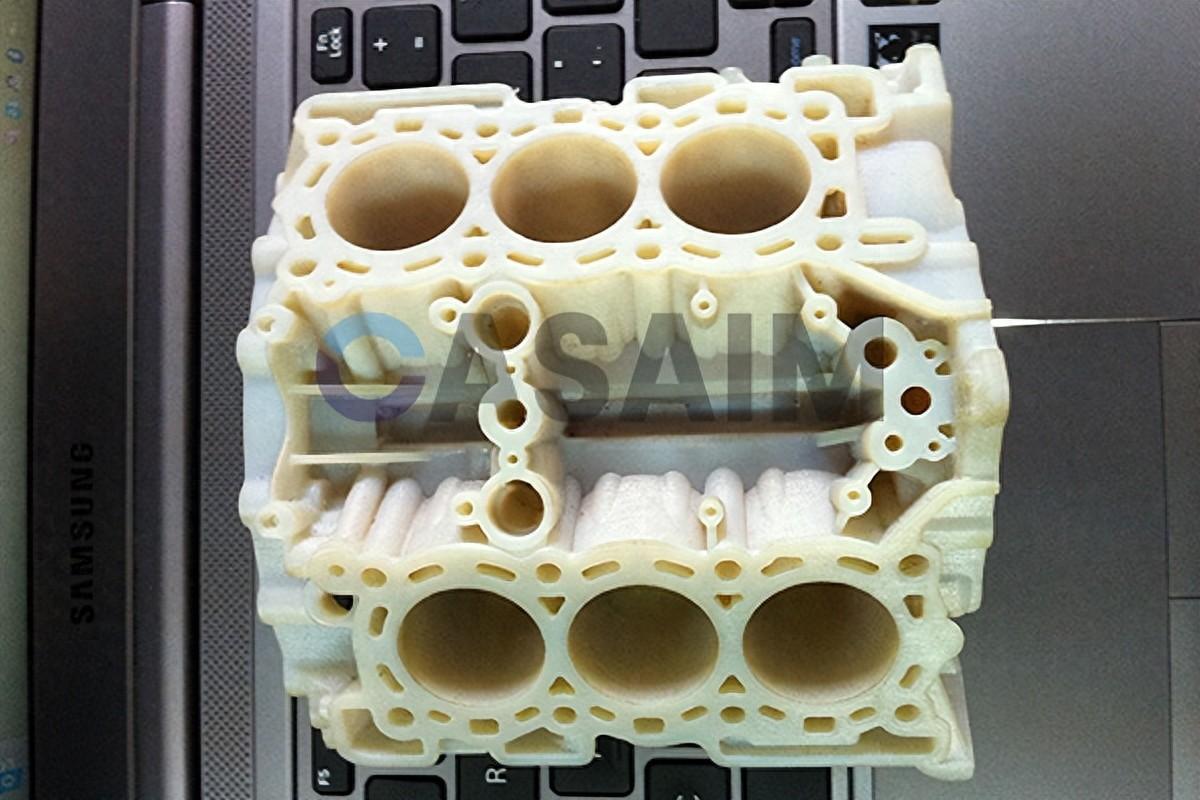
評論